BMS는 전기자동차 배터리 셀 간을 정밀하게 균형을 잡아주며, 모든 셀이 완전 충전상태가 될 수 있도록 하여준다. 또한 배터리 팩에 저장된 전기 에너지를 완벽하게 활용할 수 있도록 해서 주행거리를 연장시켜준다. 안정적 연료 측정으로 운전자로 하여금 주행거리에 대한 불안감을 해소시켜준다. BMS의 우리나라 기술수준은 시작은 늦었지만 반도체 및 제어기술의 발달로 선진국 대비 크게 뒤지지 않는다. 집중적인 기술개발 노력이 지속된다면 전기자동차가 본격 출시되는 시기가 도래되면 BMS 분야에서 배터리 못지않게 경쟁 우위에 설 수 있을 것으로 전망하고 있다.
배터리 관리 시스템 기술
배터리 관리 시스템의 정의
EV 및 HEV의 심장부는 복잡한 배터리 관리 시스템(BMS: Battery Management System)이다. 구동 시스템에 필요한 전력을 공급하는 2차전지의 안전성과 신뢰성을 보증하여 주는 역할을 하기 때문이다. 그림 1은 미국 GM의 HEV 전기자동차 Chevrolet Volt의 BMS관련 시스템을 총망라한 것이다. 288개의 리튬이온 2차 전지 셀로 구성된 배터리 팩은 길이 1.8m, 무게 181kg의 크기이며 16kWh의 전력량을 축전할 수가 있다. 전지만을 사용할 경우 항속거리는 64km(약 40마일) 주행이 가능하다. 배터리의 용량이 하한에 가까우면 엔진을 구동시켜 전력을 생산한다. 이렇게 되면 EV이기 때문에 항속 주행거리가 600km 이상으로 늘어난다.
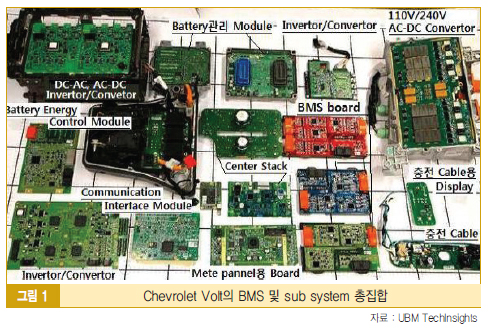
배터리의 수명을 연장하기 위해서는 배터리 충전상태(SOC: State Of Charge)를 일정하게 유지시켜주는 것이 중요하다. SOC가 너무 낮거나 높은 상태가 계속되면 SOC를 중간 수준으로 유지할 경우에 비해서 배터리의 열화가 빠르게 진행된다. 적절한 SOC의 범위는 일반적인 실험을 중복하여 봄으로써 알 수 있다. 배터리 셀을 과방전 시켜주면 구성부품이 열화되어 회복 불능상태가 된다. 충전 전압도 적정치를 넘어 충전하게 되면 배터리 셀이 과열되어 불가역적인 구조로 변화되고 만다.
BMS는 전기자동차의 배터리 제어의 최적화를 통하여 주행거리 향상 및 안전성을 확보하여주는 역할을 하여준다. BMS 기술은 크게 두 가지로 나눌 수 있다. 첫 번째로 열에 약한 배터리를 균등 냉각하여 동일한 성능 구현이 가능토록 하여주는 열관리 제어와 두 번째로는 배터리의 각 상태를 판단하여 최적 효율 점에서 작동토록 하여주는 배터리 충전상태(SOC)제어로 나눌 수 있다.
BMS는 시스템의 전압, 전류 및 온도를 모니터링하여 최적의 상태로 유지관리하여 주며, 시스템의 안전운영을 위한 경보 및 사전 안전예방 조치를 하여준다. 배터리의 충, 방전시 과충전 및 과방전을 막아주며 셀(cell)간의 전압을 균일하게 하여줌으로써 에너지 효율 및 배터리의 수명을 높여준다. 데이터의 보전 및 시스템을 진단하여 경보 관련 이력상태의 저장 및 외부 진단시스템 혹은 모니터링 PC를 통한 진단이 가능하다.
친환경 에너지에 대한 요구 증대와 고유가로 인한 고연비 이동 수단이 확대되면서 HEV, EV, E-Bike, E-Scooter 등이 인기를 더해 가면서 기존의 납축전지, Ni-Cd 전지는 환경오염 물질의 배출문제와 성능 부족이 문제가 되었다. Li-ion 배터리로 전환되면서 고성능, 고출력이며 중량도 가볍고 수명도 길어서 좋으나, 비정상적인 상황에서 발화 및 폭발의 위험성이 문제가 되고 있다. 이러한 안전성과 셀 밸런스를 위해서 필수적인 시스템으로 BMS가 등장하게 되었다.
Li-ion 배터리의 단일 셀의 정격전압은 3.6V, 충전전압은 4.2V이다. 이를 직렬로 접속하여 600V가 넘는 전압을 발생시켜준다. 여러 개의 셀을 직렬로 접속하는 경우 그 중 한 개의 셀이라도 고장이 나거나 열화 되면 배터리 팩 전체가 영향을 받는다. 그래서 최신의 HEV나 EV에 적용되는 BMS는 개개의 셀에 대한 과충전, 과방전, 과열을 막고 이들의 수명을 최적화시켜주는 기능을 하고 있다.
BMS는 모든 셀을 항상 균등한 충전상태로 유지시켜주는 셀 밸런스에 의해 이를 실현하고 있다. 더욱이 BMS는 각종 변화 요소들을 종합 분석하여 남은 주행 가능 거리를 예측하고 그 정보를 상위의 차량 ECU에 제공한다. 차량 내 통신으로는 일반적으로 CAN(Controller Area Network의 약자로 차량 내 ECU들 간의 데이터 공유를 위해 Bosch에 의해 개발된 통신 시스템)을 활용하고 있다.
BMS의 역할은 배터리 전류, 전압, 온도 등의 상태를 실시간으로 모니터링 하여 최적의 조건으로 사용할 수 있도록 제어하여 준다. 배터리의 잔존 용량 및 교체시기를 예측하여 차량제어에 활용 및 배터리의 성능 균등제어를 통한 시스템 수명을 확보하여 준다. 배터리 보호와 자가진단을 통한 시스템 신뢰성과 안전성을 확보하여 유지비용을 절감하는 데 기여하고 있다.
배터리 관리 시스템의 구성 및 기능
BMS는 BMS ECU 본체와 셀 모듈(CM: Cell Module) 등 2개의 부분으로 구성되어 있다. 이는 절연형 CAN을 통해서 서로 접속되어 있다. 각 CM은 셀 스택(Cell Stack; 모든 단일 배터리 셀의 서브 스택)에 접속되어 있다. CM은 개개의 단위 셀의 전압을 계측해서 필요에 따라 방전을 개시한다. 그림 2는 EV용 리튬 배터리 시스템의 구성부품과 BMS의 구조 예를 보여주고 있다.
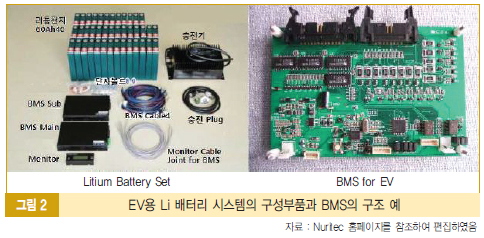
KIA의 Forte HEV에는 180V의 고전압 배터리를 적용하여 엔진과 변속기 사이에 있는 고출력 모터에 에너지를 공급함으로써 엔진에 출력을 도와주는 역할을 하고 있다. 또한 고전압을 12V로 낮추어 보조 배터리를 충전하는 방식을 적용함으로써 엔진에 장착되는 발전기를 삭제하여 구동에 필요한 엔진 토크 손실을 저감하여준다.
HEV는 하이브리드 제어기(HCU: Hybrid Control Unit), 모터 제어기(MCU: Motor Control Unit) 등의 차량 내 다른 시스템과의 통신을 통하여 배터리 충전 상태(SOC: State Of Charge), 파워 제한, 셀 밸런싱, 냉각 제어를 수행한다. HCU는 고전압 배터리의 배터리 충전상태(SOC)를 지속적으로 모니터링하고, SOC에 따라 각 주행모드에서 충전 및 방전을 제어한다. SOC 게이지는 계기판에 설치된 두 가지의 하이브리드 전용 게이지로 하나는 고전압 배터리의 충전 상태를 표시해 주는 SOC 게이지이고 나머지 하나는 모터의 충, 방전 동작 상태를 보여주는 모터 게이지 이다.
BMS의 하드웨어적인 구성에는 VITM(Voltage, Current, Temperature Measure) 모듈 셀 밸런싱(Cell Balancing)모듈, 마이크로프로세서(Micro Processor) 등으로 구성되어 있다. 그림 3은 EV용 BMS의 구성 및 작용 흐름 과정을 보여주고 있다.
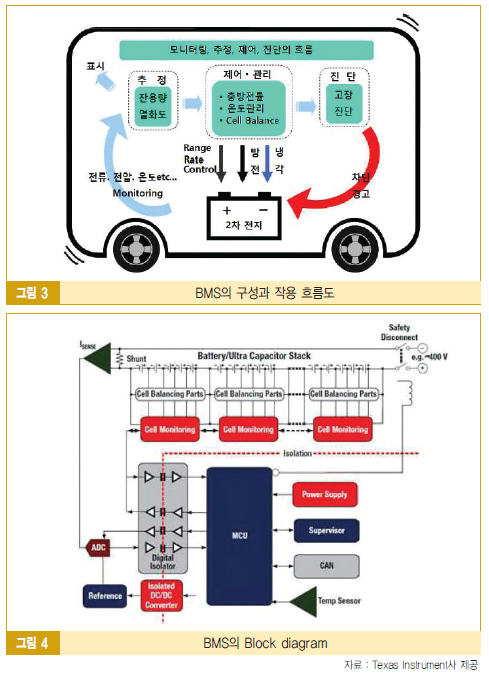
BMS의 기능을 지원하여주는 소프트웨어에는 전압, 전류, 온도 등의 계측(Measuring algorithm for voltage, current and temperature)알고리즘, 충전량 계산(SOC : State of Charge calculation), 수명 예측(SOH : State of Health estimation), 셀 밸런싱 알고리즘(Cell balancing algorithm), 온도 관리(Thermal Management), 진단 알고리즘(Diagnostic algorithm), 방호 알고리즘(Protection algorithm), 차량 내 통신(Communication with vehicle) 등이 있다. 그림 4는 BMS의 블록 다이어그램을 보여주고 있다.
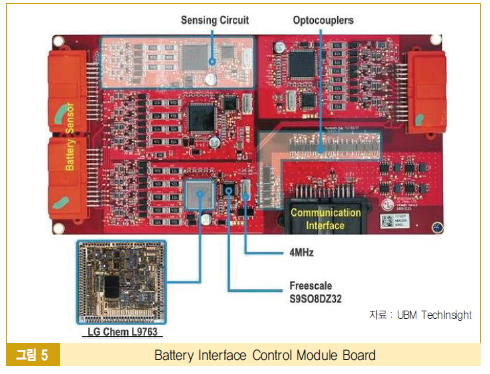
그림 5는 Chevrolet Volt에서 채용하고 있는 BMS의 배터리 인터페이스 제어 모듈 기판이며 상세 구조는 다음과 같다. 이 모듈은 4층 기판으로 되어 있으며 표면층의 모든 부품은 실장 되어 있다. 양단의 배터리와 연결되는 커넥터와 우측 하단에는 데이터 통신 커넥터가 있다. 아래층 면과 연결하기 위한 구멍(via)을 여러 개 갖추고 있는 그라운드 플레인(ground plain)과 신호배선도 있다.
제2층에는 전원용과 접지용의 평탄면이 기판의 고전압 영역 하에 펼쳐있다. 제3층에는 신호배선이 역시 고전압 영역 하에 깔려 있다. 제4층에는 그라운드 플레인과 신호배선에 사용되는 것과 몇 개의 부가적인 부품이 실장 되어 있다. 4층으로 된 각 기판 위에는 4개의 측정회로부가 절연용 광 커플러(opto couplers)를 경유해서 우측 하단의 CAN 통신 회로부에 연결되어 있다. 광 커플러는 통신 서브시스템의 단부에 위치해서 L자형으로 배치되어 있다.
우측 하단의 커넥터에는 5V 레퍼런스(reference) 외에 저전압 레퍼런스, 신호 그라운드, CAN Bus의 시리얼 데이터(H와 L), 고전압 고장신호 등을 연결시켜준다. 양단에 있는 배터리 센서 커넥터 등은 배터리 모듈로부터 온도신호와 저전압 레퍼런스, 각 배터리 셀 집단으로부터 전압 검출 신호를 통과시켜준다.
측정 서브시스템(Measuring subsystem)은 배터리 인터페이스 제어 시스템 가운데 핵심적이고도 정교한 서브시스템이다. 이 시스템은 완전한 임베디드(Embedded) 회로 시스템으로 되어 있으며 각 배터리 셀 군의 전압 출력 외에 배터리 팩의 온도도 감시한다. 셀 전압은 배터리 커넥터를 거쳐서 ASIC 「L9763」으로 전달된다.
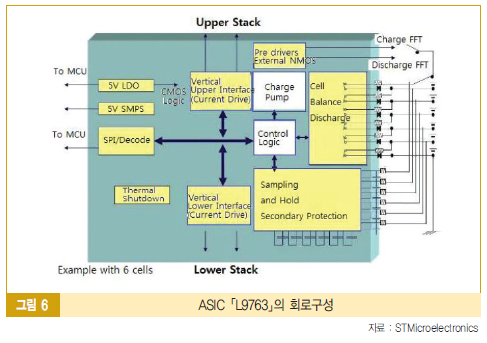
측정 서브시스템 ASIC 「L9763」은 한국의 LG화학과 미국의 STMicroelectronics이 공동으로 개발한 것이다. 그림 6은 「L9763」의 회로 구성을 보여주고 있다. 「L9763」은 최대 10개의 리튬이온 배터리 셀 군을 개별적으로 감시 가능하다. 각 셀의 부하 전류를 감시하기 위한 온 칩(On chip) 전류 검출 증폭기를 비롯하여 셀 전압을 감시하는 온 칩 아날로그 멀티플렉서(Analog multiplexer)와 샘플 홀드 회로를 내장하고 있다.
「L9763」은 차동입력을 채용하고 있기 때문에 보상전압(offset voltage)이 높은데다가 그 수준이 배터리 팩 내에서도 배터리 셀 위치에 따라서 달라지는 환경 아래서도 mV 정도의 미세한 전압 측정이 가능하다. 기판을 설계한 사람은 이러한 엄격한 동작환경에서도 양호한 신호 완전성(signal integrity)을 실현할 수 있도록 신호 배선의 배치법이나 절연수법, 그라운드 플레인을 연구해서 각각의 수법을 적절히 조합하였다.
배터리 셀 간의 전압 차이에 대한 제어 방법은 다음과 같다.
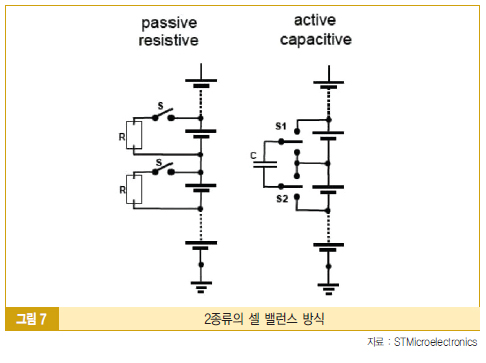
특정 셀 군의 전압이 높은 것을 검출하게 되면 ASIC의 온 칩 회로가 작동해서 특정 셀 군을 외부저항 회로망에 접속한다. 선택된 셀 군이 어느 정도 방전하게 되면 전압 차가 줄어들게 된다. 그림 7은 셀 밸런스 방식의 2가지 종류의 회로도를 보여주고 있다. 상기의 간략한 수동 셀 밸런스(Passive cell balance)방식은 신뢰성이 높고 비용이 적게 드는 방법이지만, 방전 저항 내에서 에너지가 열로 손실되기 때문에 효율이 떨어진다. 반면에 능동 셀 밸런스(Active cell balance)방식은 전압이 가장 높은 셀로부터의 전하를 받아 축적해서 전압이 가장 낮은 셀로 재분배를 하여준다. 전하의 축적과 재분배에는 콘덴서, 인덕터, 트랜스를 사용해서 셀을 순차적으로 바꿔가면서 상황에 따라 전하를 축적하고 방전 또는 재분배하여 준다. 이 방식은 수동 셀 밸런스 방식에 비해서 에너지 보존(효율)이라는 점에서 우수하지만, 시스템의 비용이 증가하고 복잡하다는 점이 있다.
리튬이온 배터리 팩의 충전과 방전에는 정전류법과 정전압법이 있다. 이 방식에서 충전 시스템에 있는 한 쌍의 MOSFET를 사용해 소요의 충전 전압에 도달하게 되면 충전 전류를 감소시켜주고, 이와 반대로 방전 동작을 할 때에는 전류를 증가 시켜준다. L9763에는 파워 MOSFET를 구동시켜주기 위한 차지 펌프(Charge pump)가 있다.
측정 서브시스템 ASIC 「L9763」의 우측에 있는 Freescale의 S9S08DZ32는 온 칩의 정교한 CAN 컨트롤러를 내장하고 있다. CAN 컨츠롤러는 사용하지 않을 때에는 선택적으로 전원이 끊긴다. 슬립 모드(sleep mode)로 설정할 수도 있다. 온 칩의 컨트롤러는 FIFO 구성의 버퍼를 5개, 송출 메시지의 우선선택을 가능하게 하는 송신 버퍼를 3개를 갖추고 있어 실시간으로 동작의 예측 및 제어 가능성을 확보하고 있다. 송신 메시지의 순위 설정도 가능하다. 그림 8의 구성도를 참조하면 된다.
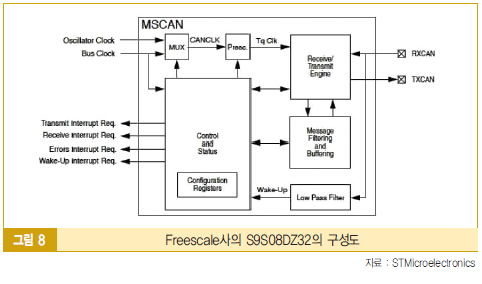
EV의 BMS에서 또 하나의 중요한 것은 통신과 제어이다. 개개의 리튬이온 배터리 셀은 복잡한 알고리즘에 의해서 관리되고 있다. 배터리 팩은 배터리 인터페이스 제어 모듈 내의 각 측정 서브시스템이 감시하고 있다. 그렇지만 결국 배터리 전체에 걸쳐서 꼭 필요한 데이터는 CAN Bus 신호와 고전압 고장 신호에 포함되어 있다.
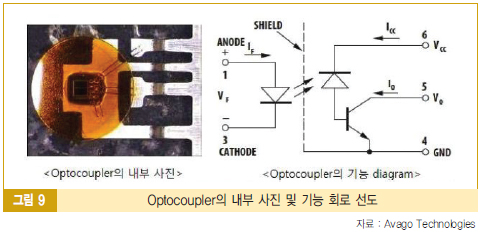
시스템의 안전성과 신뢰성은 CAN Bus 네트워크를 어떻게 하면 고전압 측정회로로부터 확실하게 절연하느냐에 달려 있다. 절연에는 여러 가지 방법이 있지만, 과혹한 환경과 복수의 안전규제를 고려했을 때 광 커플러가 가장 적합하다. 그림 9는 광 커플러의 내부 사진 및 기능 회로 선도를 나타낸 것이다.
광 커플러는 일반적인 노이즈에 대한 내성이 강하다. 자동차와 같은 전기적인 노이즈가 많은 환경에서도 기본적인 EMC나 EMI의 문제가 생기지 않는다. 다층구조의 절연을 하였기 때문에 배터리 팩으로부터의 직류 전압 스트레스에 오랜 시간 노출되어도 문제가 없다. 각종시험이나 충전기의 탈착, DC-DC변환에 따른 고속, 고전압의 과도한 전압 변동에도 잘 견딘다.
EV 및 HEV가 자동차 시장에서 성공을 거두기 위해서는 배터리와 배터리 관리 시스템에 달려있다. 미국의 McKinsey의 최근 시장조사에 의하면 리튬이온 배터리의 기술의 발전으로 2025년까지 용량이 80~100% 증가하고 가격도 떨어질 것으로 예측하고 있다. EV의 총 소유원가(TCO)가 가솔린 자동차와 비교해서 작아지고, 배터리의 고전압화 및 대용량화, 데이터 처리의 고속화 등의 발전을 기대하고 있다.
국내외 동향
해외 동향
유럽
독일의 LTC/Gaia은 리튬이온 전지 제조회사로서, 자동차용 이외에 정치형 전지, 재생가능 에너지, 군사, 우주항공 용을 공급하고 있다. 2002년에 미국의 Lithium Technology Co.에 합병되었다. NCA계, 인산철 리튬이온(LiFePO4) 전지 셀, 배터리 팩, BMS를 장비한 배터리 팩 등이 주요 생산품이다. 2011년 9월 27일 미국의 배터리 메이커 EnerSys사와 대형 리튬이온 전지 셀을 생산하는 합병회사 EAS Germany를 설립하였다. 출자 비율은 EnerSys가 60%, LTC/Gaia가 40% 이다.
dSPACE는 자동차산업 및 항공산업에서 필요로 하는 전자 제어기기 등을 제조하는 회사로서 독일에 본사가 있고 일본에 자회사가 있다. BMS의 HIL(Hardware-In-the-Loop) 테스트에서는 셀 수준에서 고전압 배터리를 시뮬레이션 할 필요가 있다. 이를 가능하게 하기위하여 dSPACE는 실시간으로 계측할 수 있는 셀 모델과 셀 단자 전압을 출력할 수 있는 고정밀도의 에뮬레이션 유닛(Emulation unit)을 개발하였다. ECU 단체 및 ECU 네트워크 통합 테스트가 가능하다.
독일의 Continental사는 세계 유수의 자동차 회사에 섀시, 파워트레인, 타이어 등 자동차 부품을 공급하고 있는 글로벌 메이저 종합 자동차 부품회사이다. 특히 전기자동차용 배터리 분야에서는 배터리 팩 시스템 기술과 BMS기술에 세계적인 강점을 가지고 있다. 2012년 7월 한국의 SK이노베이션과 합작회사 설립을 위한 계약을 체결하였다. SK의 배터리 셀 기술과 Continental의 배터리 팩 시스템 및 BMS 기술 노하우가 접목되면 엄청난 시너지 효과가 기대 된다.
미국
FEV에서는 리튬이온 배터리의 관리 및 감독을 위해서 FEV LiionMan이라고 하는 특별한 BMS 장치를 개발 SAE 2009 World Congress에서 발표하였다. 그 밖에 이번 전시회에서는 리튬이온 배터리 전기자동차 개발기술을 적용한 차량을 선보였다.
EnerDel은 Ener1의 자회사로 Ener1이 국내 Enertech International의 83%지분을 갖고 리튬이온 폴리머 배터리 셀 및 팩 제조를 통해 BMS 및 차량을 개발하는 업체이다. Indiana주에 위치해 있으며 이너테크인터내셔널(주)는 한국 군자역 및 충주에서 배터리 셀과 팩을 제조하고 있다. EnerDel은 차량용 BMS와 배터리 팩을 최근 개발한 업체이다. 원래 이너테크인터내셔널은 휴대전화 등 모바일 기기에 사용되는 배터리 셀 전문업체로 시작하였다.
EnerDel은 EV, HEV, PHEV용 리튬이온 배터리 기술개발을 위해 USABC 및 Ford, GM, Chrysler 등 자동차 조립업체와 협력하고 있다. 그동안 ANL과 Delphi 등과의 협력을 통해서 배터리 산업의 기술 노하우를 부지런히 축적해 왔다. SAE 2009 World Congress에서 배터리 팩과 BMS를 전시하였다.
Delphi社는 전기자동차와 관련해서는 배터리 제어기 및 Connector 개발 공급업체이다. 이번에 320VDC Battery Pack System이라고 하는 BMS를 개발하여 SAE 2009 World Congress에서 선보였다. LGCPI(LG Chem. Power Inc.)는 LG화학의 미국 자회사로 북미 HEV, PHEV, EV용 리튬이온 폴리머 배터리를 GM에 공급하는 업체이다. 이번에 BMS를 개발하여 SAE 2009 World Congress에서 선보였다.
Maxim Integrated는 기존 자동차시장의 전통적인 강자들인 Freescale, Infineon, Analog Devices 등을 제치고 향후 부각될 HEV, PHEV, EV의 배터리 시장을 선점하기 위해 새로운 BMS 관련 기술을 공개하였다. 배터리 모니터링 IC MAX11068은 통신 버스를 탑재하고 있어 값비싼 절연부품을 사용하지 않아도 여러 개의 MAX11068을 데이지 체인 방식으로 연결할 수 있다. 이는 비용을 80%까지 줄여주고 설계를 간소화 하면서 셀 밸런싱을 정밀하게 할 수 있다.
일본
Toyota의 자회사인 Panasonic EV Energy는 Prius, Camry, Lexus 등에 적용된 니켈수소전지 및 BMS를 적용한 경험을 보유하고 10년 이상 차량시스템 평가 및 필드 테스트를 통해 BMS의 최적화를 달성하였다.
Keihin社는 Honda에서 생산 판매중인 New Civic HEV용 니켈수소 2차 전지를 위한 BMS를 개발 생산하고 있으며 리튬계 배터리용 BMS에 대한 연구개발도 진행 중이다. Hitachi Vehicle Energy는 배터리 제어 시스템 개발을 위해 4채널의 셀 제어용 전용 칩을 개발하였다. 이 전용 칩의 적용으로 인해 BMS의 크기는 1/10로, 제조비용은 1/8로 크게 줄였다고 2005년 Hawaii에서 개최된 AABC Conference에서 발표하였다.
(주)ZMP는 2001년 1월 설립된 회사로 2005년에 세계 최초로 가정용 2족 로봇 Nuvo를 발매한 회사이다. 최근 전기자동차가 주목을 받게 되면서 리튬이온 배터리 수요가 늘고, 이에 대한 운용 방법 및 학습을 위한 기술자 연수 및 대학 교재 용의 실험 키트 ‘e-nuvo BMS’를 개발 발매하고 있다. 총전압 25.9V(3.7V, 16Ah×7 cell), 출력전압 100V이다.
중국
리센 배터리(Lishen Battery)는 한국의 Nexcon Technology와 공동으로 대용량 전력저장장치(ESS), EV, HEV용 BMS에 대한 전략적인 파트너 쉽을 구축하기 위한 양해각서를 체결하였다. Lishen Battery는 중국 해양 석유총공사가 투자한 2차 전지를 생산하는 국영기업으로 현재 중국내에서 개발 중인 전기자동차용 배터리를 개발 시험양산하고 있다.
비야디(BYD: Build Your Dream)는 중국 자동차의 제4위 메이커로 폭발적인 중국시장과 미국의 투자가 Warren Buffet의 한화 2,700억 원 규모의 투자를 배경으로 세계의 이목을 끈 기업이다. 그러나 지금 전기자동차 개발에 총력을 기울이고 있지만, 인프라 및 원가 등으로 고전을 면치 못하고 있다. 리튬이온 배터리 및 BMS에 대한 연구개발도 아직까지는 미숙하고 불투명한 상태이다.
국내 동향
우리나라의 전기차용 배터리는 세계적인 수준으로 평가 받고 있다. LG화학, SB리모티브, SK이노베이션 등이 시장을 선도하고 있으며, LG화학은 세계1위 전기차 배터리 생산업체로 미국 전기차 배터리개발 컨소시엄으로부터 고성능 전기차 배터리 개발 프로젝트를 수주, GM, 포드 등 총 10개 기업의 전기차 배터리 공급업체로 선정되었으며 배터리 생산능력은 현재 1,600MWh에서 2013년 5.6GWh로 확대 증설할 예정이다.
삼성SDI와 독일 Bosch가 50대 50으로 합작 설립한 SB리모티브는 BMW, Chrysler와 공급계약을 체결하였고, SK이노베이션은 현대, 기아차, Mercedes AMG, Mitsubishi Fuso에 납품하고 있다. SB리모티브는 생산규모를 현재 135MWh에서 2015년까지 4GWh로, SK이노베이션은 현재 100MWh에서 2012년말 600MWh로 확대 증설할 예정이다.
삼성SDI는 SB리모티브에 전기자동차 시장이 빠르게 성장할 것으로 보고 막대한 투자를 하였지만, 활성화가 늦어지고 있는 상황에서 2011년도에 1,755억의 손실을 보았다. 결국 삼성SDI는 2012년 9월 Bosch의 지분을 전량 인수 100% 자회사로 새 출발한다고 발표하였다. 삼성SDI는 이미 확보된 자동차산업에 대한 노하우를 바탕으로 독자경영을 시행하는 동시에 자체 팩 기술을 확보하여 전기자동차 배터리 사업부문에 대한 경쟁력을 강화해 나갈 계획이다.
BMS 분야에서는 케피코(Kefico), 파워로직스(PowerLogics), 넷스콘텍(Nexcon Technology), 이렌텍(Elentec) 등이 생산 및 개발에 참여하고 있다. PowerLogics는 전기자전거용을 시작으로 전기자동차용 BMS를 연간 60만개를 생산하고 있다. PowerLogics는 그간 삼성 SDI에, Nexcon Tech.는 LG화학에 제품을 공급해 왔다.
레오모터스(Leo Motors)는 리튬폴리머 배터리와 BMS에서 월등한 기술력을 바탕으로 전기차 사업을 주도하고 있는 업체다. 레오모터스는 일본 자동차부품상사 글로벌커머스와 함께 중고 버스를 전기차로 바꾸는 개조 키트를 일본 시장에 수출하기로 되어 있다. 레오는 현대자동차의 24인승 버스를 고속 전기차로 개조해 시속 110km로 도로주행시험에 성공한 바가 있다.
레오모터스의 배터리는 배터리 셀의 수량을 1/10로 줄여 중량과 부피를 줄인 것도 포인트다. 100A짜리 80개의 셀만을 사용한다. 여기에서 테슬라(Tesla) 등에서 사용하는 배터리 셀과의 기술력 차이가 크게 난다. 코캄(Kokam)으로부터 공급받은 이 셀 기술을 바탕으로 완성된 배터리 팩은 또 레오모터스가 개발한 그 BMS에 이해 제어된다.
파워로직스가 개발한 BMS는 국내 2차 전지 업체 및 상용차 업체와 테스트를 이미 거쳤고 배터리 잔량 정확도 , 신뢰성, 전압, 온도, 전류 제어의 정확성에서 우수한 평가를 받고 있다.
일본 Daimler 그룹 산하의 Mitsubishi Fuso에 2차 전지 공급계약을 체결한 SK이노베이션이 파워로직스의 친환경 BMS를 결합한 배터리 팩을 공급함으로써 파워로직스는 2012년부터 공급을 시작해 2017년까지 연평균 2,800대의 트럭용 BMS를 공급하기로 하였다.
SK C&C는 BMS 부품 개발을 위해 SK이노베이션과 별도로 60억원을 투입해 연구개발을 하고 있다. 따라서 향후 SK이노베이션이 리튬이온 배터리를 공급하게 될 Mercedes Benz의 첫 전기 Supercar에 SK C&C의 BMS 부품이 공급될 것으로 예상된다. 관련업계에서는 향후 전기차 시장이 활성화되면 BMS 시장규모는 2015년도 5조원, 2020년에는 35조원 규모에 이를 것으로 추산하고 있다.
SK이노베이션은 독일의 Continental 사와 51대 49의 비율로 배터리 공동개발을 위한 합작법인을 2012년 말까지 설립할 계획이라고 2012년 7월 23일 독일 Frankfurt에서 설립 계약을 체결하였다. 이 합작법인은 SK이노베이션에서 배터리 셀을 공급받고, Continental사에서 BMS를 공급받아 세계 최고 수준의 배터리 팩 시스템의 개발 및 생산에 들어갈 예정이다. 양사는 향후 5년간 약 4,000억원을 투자할 예정이며 합작법인은 독일 Berlin에 본사를 두기로 하였다.
현재 전기자동차 생산업체인 현대, 기아는 자회사인 케피코를 통해 BMS를 생산하고 있으며 2차 전지 생산업체인 LG화학은 LG이노텍을 통해, 삼성SDI는 SB리모티브를 통해 BMS 개발을 진행하고 있다. 외국계 기업들 중에서는 리니어테크놀러지(Linear Technology)가 2008년 BMS 제품을 가장 먼저 선보였으며 최근 기능을 향상시킨 후속 제품을 출시하였다. 지난 2년간 글로벌 자동차 회사에 제품을 공급해온 경험을 바탕으로 국내 자동차 조립업체 등 관련 기업을 공략하고 있다. 그 밖에 Linear Technology, TI, Maxim, Analog Device 등 굵직한 글로벌 대기업들도 한국의 신규 시장 공략을 추진하고 있다. 이들 기업은 기존에 노트북, 휴대전화 등 중소형 모바일 기기 위주로 관련 제품을 공급해 왔으며 전기자동차 및 대용량 저장 장치 등 신규시장 진출 및 입지 확대를 준비하고 있다.
BMS의 우리나라 기술수준은 제어기술의 발달로 제품의 설계 및 생산기술면에서 선진국 대비 크게 뒤지고 있지 않으나 부품과 최종품질에서 경쟁력이 다소 떨어지는 것으로 분석되고 있다. 선진국 대비 90%으로 다소 기술격차는 존재하지만 그 기술력 차는 크지 않은 수준이다.
집중적인 기술개발 노력만 지속 된다면 전기자동차의 본격적인 시기가 왔을 때 BMS 분야에서 선진국과 경쟁이 가능할 수 있는 동등 수준에 접근할 수 있을 것으로 전망된다.
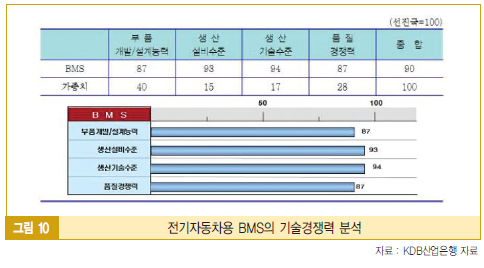
그림 10은 선진국 대비 우리나라의 전기자동차용 BMS의 기술경쟁력을 분석하여 보여주고 있다.
BMS의 우리나라 기술수준은 제어기술의 발달로 제품의 설계 및 생산기술면에서 선진국 대비 크게 뒤지고 있지 않으나 부품과 최종품질에서 경쟁력이 다소 떨어지는 것으로 분석되고 있다. 선진국 대비 90%정도로 보고 있다.
향후 기술개발 동향은 가격경쟁이 심화될 것으로 보이며, 이에 따라 원가절감을 위한 방향으로 진행될 것으로 본다. 배터리 셀의 안정성 확보를 위해 배터리의 전기화학적 반응을 억제하
는 방향으로 BMS의 기술이 개발된 반면, 기술동향은 활용범위를 적극적으로 확대하고 잔존 용량 및 수명 예측을 보다 정확히 하는 방향으로 기술개발이 전개되고 있다.
국내 BMS업체 가운데 제품을 생산하여 전기자동차에 적용해 본 업체는 케피코, P&E Solution, Nexcon technology, PowerLogics, 등이다. 국내 고속 전기자동차에 적용해본 제품은 Kefico 제품 밖에 없으며, 그 밖에 업체들은 시속 40km 이하의 저속 전기자동차를 비롯한 전기자전거, 전기스쿠터, 골프카 등에만 적용 되었다.
기술의 기본 원리에서는 고속 전기자동차에 적용된 기술과 저속 전기자동차의 기술에서는 큰 차이가 없어 관련 업계의 기본 기술력의 차이는 별로 없다고 봐도 된다. 다만, 고속 전기자동차의 실제 양산을 위한 필드 테스트에 대한 경험 유무가 업체의 기술력 차이를 결정한다고 볼 수 있다.
결 론
HEV, PHEV, EV 등의 전기자동차들은 부품 수가 내연기관차 대비 60% 수준에 불과하며 그 구조도 매우 단순하기 때문에 배터리 가격을 제외할 경우, 가솔린차보다 저렴할 것으로 예상된다. 에너지 효율도 53%로 내연기관 자동차 보다 월등히 우수하다. 다만, 배터리 기술로 인해 실용화가 지연되어 왔으나 이제 배터리관련 기술도 해결되어 실용적인 교통수단으로 등장할 날이 눈앞에 다가 왔다.
배터리의 기술도 중요하지만, 더 중요한 것은 배터리 관리 시스템이다. BMS는 배터리 시스템의 전압, 전류 및 온도를 모니터링하여 최적의 상태로 유지관리 하여준다. 시스템의 안전운영을 위한 경보 및 사전 안전예방 조치도 하여준다. 배터리의 충, 방전시 과충전 및 과방전을 막아주며 셀 간의 전압을 균일하게 하여줌으로써 에너지 효율 및 배터리의 수명을 높여준다.
전기자동차의 실용화가 확대되면 BMS 역할의 중요함이 더욱 강조되고 있다. 기술개발에 더욱 박차를 가해야 되리라고 본다.
BMS사업자가 배터리 생산업체에 높은 의존도를 지니는 산업적 환경에서는 배터리 생산자와 그것을 제어하는 IT기업인 BMS사업자간의 협력 관계가 자동차용 2차 전지와 BMS 양쪽에 모두 시장 경쟁력의 원천이 된다. 그리고 자동차용 2차 전지에 탑재되는 BMS는 자동차의 진동, 온도, 습도 등 가혹한 환경에서 작동 되어야 하기 때문에 시스템의 안전성 측면에서 까다로운 품질이 요구 된다. BMS는 최초 설계 단계부터 엄격한 품질관리 체계가 필요하며, 차별화 경쟁력을 가지기 위해서는 자동차들의 특성이 반영되어 다양한 특성을 가지고 있는 BMS의 개발과 인증/정산/통신 등 부가 기능에 대한 것도 연구되어 있어야 한다.
향후, 차량용 2차 전지에 탑재되는 BMS의 시장규모를 국내에서 양산 계획을 가지고 있는 HMC의 Avante급을 기준으로 가정해보면, Avante를 EV화 한 모델에서만 약 7조 6천억 원의 매출이 예상된다. 녹색성장시대를 맞아 전세계에 걸쳐 기하급수적으로 성장할 시장을 고려하면 이러한 시장이 새로운 사업 기회인지 아닌지를 굳이 강조할 필요는 없을 것 같다.
BMS의 시장은 배터리 메이커이며 배터리는 전기자동차 조립업체가 되는 밸류 체인을 형성하고 있다. 그러나 최종 조립단계에 있는 전기자동차 보급실적이 2011년 목표대비 10%에 지나지 않는 80대 밖에 되지 못하고 있음은 자동차 수출 주력국가인 우리나라로서는 심히 우려되는 바가 크다. 자동차 산업의 패러다임 변화로 전기자동차 시장은 빠른 성장이 예상된다. 현재 전기자동차 시장은 미국, 중국, 일본이 주도하고 있으며 한국은 아직 걸음마 단계라고 볼 수 있다.
한국의 전기자동차 관련 R&D 투자비는 미국의 1.2%, 중국의 8% 수준으로 미약하기 짝이 없다. 그런 가운데 전기자동차의 핵심 부품인 배터리 기술과 BMS는 수준급에 이르러 해외 수출 비중이 급증하고 있는 상황이다. 전기자동차의 국내 생산이 미진하여 부품의 해외 수출이 앞서가고 있다. 전기자동차의 국내 출시 지연으로 배터리와 배터리 관련 부품과 불균형적으로 발전하고 있으며 바람직한 산업구조 형성에 문제가 되고 있다.
전기자동차의 내수시장 활성화를 통해 배터리와 BMS가 수출에 앞서 국내 전기자동차에서 충분한 실용성을 거쳐 자동차와 더불어 수출전략 상품이 되어야 바람직한 구조가 되는 것이다. 이를 위해서는 미국, 일본과 같이 수요자에 대한 파격적인 자금 지원 정책 등과 같은 보급 활성화 대책이 반드시 수립되어야 할 것으로 판단되는 바이다.
전기자동차 시장은 가장 핵심적인 배터리 관련 기술이 어느 정도 수준에 올라와 경쟁력을 갖추고 있기 때문에 정책적 지원만 있으면 기술혁신을 통한 원가하락 및 지속적인 성장이 예상되므로 국내 기업들의 적극적인 참여가 필요하다. 이미 보유하고 있는 가솔린 자동차에 대한 수출 경쟁력과 앞서가고 있는 배터리 경쟁력을 기반으로 국내 완성차 업체는 단시간에 전기자동차 시장에서도 두각을 나타낼 것으로 예상된다.