연료전지자동차의 기술경쟁력은 사용하는 백금촉매/담지체 사용량과 내구성, 달러소 계, aroma계 그리고 프로톤 전도기구가 다른 전해질막 가운데에서 고온/저가습 운전이 가능하여 열 제거계통과 가습계통을 간소화할 수 있는 저가격 고체고분자전해질막을 채용하는 것이 압도적으로 유리해 진다. ANL 2012년 기술현황을 반영한 연료전지스택과 시스템을 준거하여 Strategic Analysis가 실시한 연료전지스택과 연료전지 BOP 및 자동차용 연료전지시스템의 비용을 분석하였다.
요소기술별 기술경쟁력 분석
Cost Analysis
가. 2012년 이전의 연료전지시스템과 개발과제
지난 10여년 간의 연료전지자동차기술개발 개황요약은 다음과 같다. 2005년~2006년경의 기술개발단계로부터 2012년까지의 기술개발을 요약하면 다음과 같은 것을 지적할 수 있다. 운전압력이 2~2.5bar의 연료전지스택의 출력은 비출력이 2.2kW/kg으로 출력밀도는 2.9kW/L로 거의 2배 증강되었다. 백금촉매량은 이 10년 동안에 0.3~0.35gr/kW로 1/3로 저감되었다. 10%의 출력저감이 나타날 때까지의 스택수명은 12년~15년이 되어 이 또한 2배가 길어졌다. 연료전지자동차 전체의 사이클 효율은 60%내외이다. 700기압 고압수소저장탱크용량으로 1회충전항속거리가 660㎞에 이르게 되어 내연기관자동차의 항속거리와 동등한 거리를 주행할 수 있게 되었다. 연료전지자동차를 개발하고 있는 완성차제조사 담당자는 이러한 기술개발성과로 2015년의 연료전지자동차 시장진입을 위한 기술적 요건은 모두 구비했고 앞으로의 과제로는 시장 개척을 위한 차량가격 저감과 수소충전소 인프라구축을 들었다.
ANL시스템에서 2011년 이전의 시스템으로부터 2012년에 변경된 것 가운데 중요한 것을 요약하면 다음과 같다. 전해질막과 가스확산층의 적층을 위하여 사용되던 고온프레스(hot-press) 공정은 NSTH 촉매층과의 적합성이 좋지 않아 저가의 crimping roller 공정을 도입했다. 공기공급 계통의 공기가습방식으로는 tubular 전해질막 가습기로부터 25㎛의 보다 얇은 전해질막으로 사용할 수 있는 Gore의 plat-frame 전해질가습기로 교체할 예정이다. 이로써 물 수송량이 증가하고 전해질 막의 필요량도 크게 저감시킬 수 있게 된다. 공기공급계통에 사용되던 Twin-lobe compressor를 centrifugal compressor와 expander로 교체했다. 물 분무식 가습기를 전해질막 가습기로 교체했다. precooler와 compressor 및 expander 구동 모터의 냉각을 위하여 저온냉각계통을 도입했다. 이것은 주행용 모터 구동 인버터 냉각용으로도 사용된다.
수소공급계통의 proportional 밸브와 pressure transducer를 제거하고 over-pressure cut-off 밸브와 check 밸브를 추가하고 순간적인 순도변화를 방지하기위한 inline-필터를 추가했다. expander에서의 결빙을 방지하기 위하여 셀 수소출구에 제습기를 설치하였다. 수소퍼지밸브를 수소가스퍼지와 물 수집 및 물 퍼지 기능을 겸할 수 있는 다기능 퍼지 밸브로 설치했다. 표 1은 ANL 2012 연료전지시스템의 제원이다.
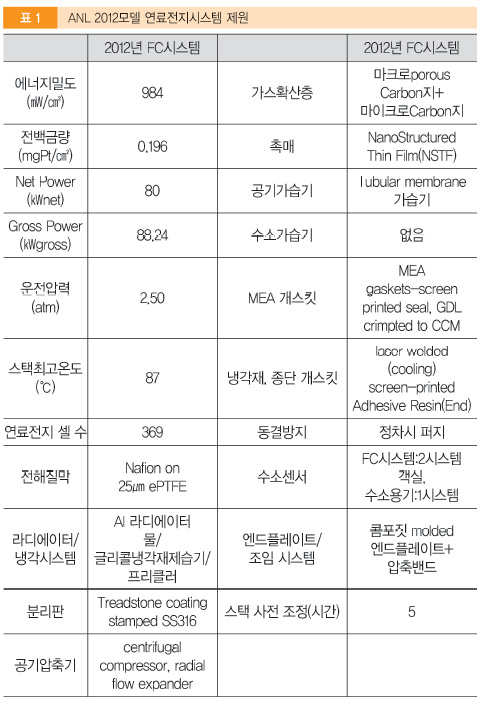
2012년 설계의 가격최적화를 위하여 선정된 설계조건들은 다음과 같다. 셀 전압 : 0.676V, 전류밀도 : 1.456㎃/㎠ , 출력밀도 : 984㎽/㎠, 스택 inlet 압력 : 2.5기압, 냉각재 출구온도 : 87℃, 전 백금촉매 loading : 0.196㎎/㎠ 등이다. 스택 운전 압력이 높을수록, 전 백금촉매 로딩이 0.196㎎/㎠일 때 시스템비용가 제일 낮다는 연구결과를 반영한 것이다.
2013년 시점에서도 연료전지 MEA, 스택 및 시스템의 보다 단순화되고 대량생산품으로의 교체 등이 활발하게 진행되고 있음을 알 수 있다. 고온 저가습 전해질막 및 3원 합금 촉매 등의 본격적인 실용화는 이루어지고 있지 않아 비약적인 가격저감이 달성될 가능성은 크다고 볼 수 있다.
나. 연료전지시스템 비용 분석
연료전지자동차의 기술경쟁력은, 사용하는 백금촉매/담지체 사용량과 내구성, 달러소 계, aroma계 그리고 프로톤 전도기구가 다른 전해질막 가운데에서 고온/저가습 운전이 가능하여 열 제거계통과 가습계통을 간소화할 수 있는 저가격 고체고분자전해질막을 채용하는 것이 압도적으로 유리해 진다.
ANL 2012 기술현황을 반영한 연료전지스택과 시스템을 준거하여 Strategic Analysis가 실시한 연료전지스택과 연료전지 BOP 및 자동차용 연료전지시스템의 비용분석표가 표 2, 표 3 및 표 4이다.
미국 DOE에서 개발지원하고 있는 연료전지스택에는 25㎛ 두께의 ePTFE막에 Nafion을 코팅한 전해질막과 PtNi dealloy 촉매를 사용하는 NSTF를 적층한 MEA에 다시 마이크로 poros 탄소 부직포와 마크로poros 탄소부직포로 구성된 가스 확산층을 적층한 5층 구조를 채용하고 있다. 분리판으로는 TreadStone이 코팅된 스테인리스 316 스템핀 판이 사용되고 있다.
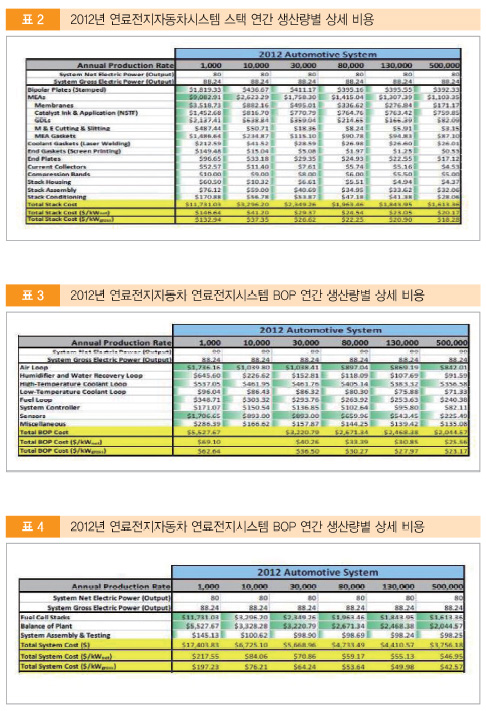
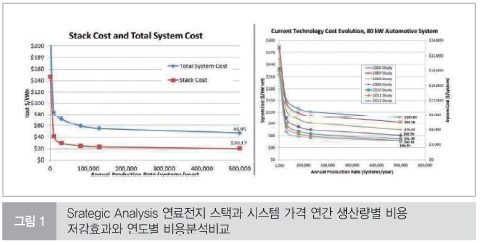
그림 2는 DOE의 Hydrogen and Fuel Cell program에서 2017년의 목표 가격을 달성하기 위하여 연료전지시스템의 요소부품별 저감노력 목표량을 제시하고 있다. 50만대 양산체제 가격을 기준으로 2010년의 49$에서 2017년의 30$를 달성하기 위하여 크게 개선해야 할 것으로 MEA부분, 특히 촉매와 전해질막 부분이 자치하는 비율이 크다. 공기공급계통의 압축기와 가습기가 적지 않은 비율을 차지하고 있다.
2011년 McKinsey가 기술개발과 양산효과를 반영하여 2015년과 2020년의 연료전지자동차용 연료저지시스템의 비용을 분석한 것을 표 5에 나타내고 있다.
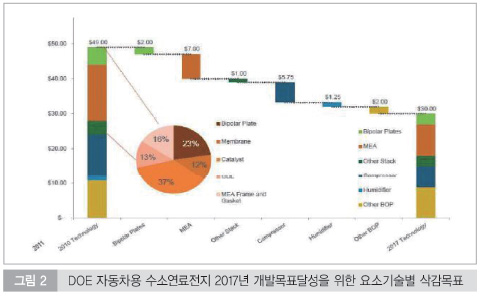
다. 연료전지자동차 비용 분석
Toyota가 보는 연료전지자동차 요소기술별 비용분석과 기술개발효과가 비용에 미치는 영향을 분석한 것이 그림 3이다.
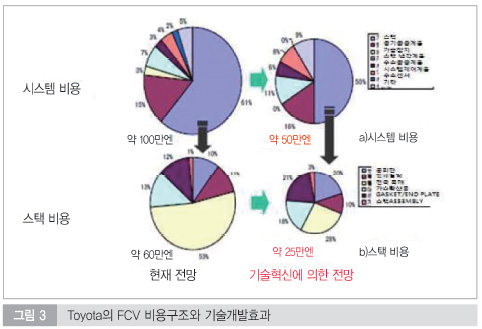
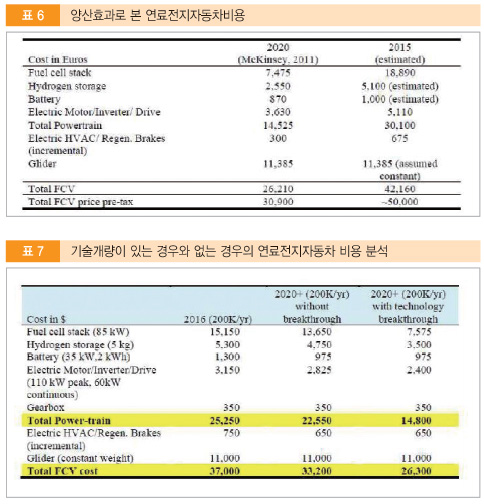
표 6은 McKinsey가 EU의 위탁을 받아 수행한 연료전지 자동차 비용분석이다. 양산체제를 갖추면 2015년에는 프리미엄급 내연기관자동차와 경합할 수 있는 기술수준에 도달 할 것임을 밝히고 있다.
표 7은 2020년의 연간생산량 20만대일 때 연료전지자동차 시스템요소별로 기술혁신이 가져다 줄 비용 변동을 요약한 것이다. 표 8은 2012년 시점에서 시판되고 있는 자동차용 연료전지의 제원과 상품명 및 제조사를 정리한 것이다.
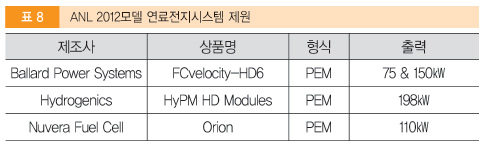
촉매(백금 촉매량 저감 기술 vs 대체촉매)
가. 개황
연료극에서의 촉매반응에 비하여 산소극에서의 촉매반응은 매우 늦기 때문에 연료극보다는 많은 백금촉매가 필요하게 된다. 표준적인 연료극에서는 카본담지체표면 백금나노입자를 고분산 시킨 Pt/C 촉매가 널리 사용되고 있다. 운전 사이클 과정에서 연료/산소공급의 달러 연속인 공급과 중단 등으로 커다란 전위변화를 겪게 된다. 이 과정에서 일어나는 카본부식에 위한 백금탈리와 백금촉매자신의 용해 재 설출 등으로 반응표면적이 감소하여 산소환원반응이 저하한다. 연료전지의 본격적인 보급을 위해서는 백금 사용량의 저감과 고내구성을 동시에 양립시키는 산소극 촉매개발이 필수적이 된다. 고내구성의 카본 담지체 또는 카본 담지체에 대체되는 담지체 개발은 활발하게 연구되고 있으나 백금사용량 저감과 내고구성 촉매의 개발은 아직 달러 충분하다.
개량 촉매 개발방향은 크게 두 가지로 나누어진다. 나노백금입자의 담지체 고분산형에서 고내구성의 담지체개발과 2006년 이후 활발하게 연구 개발되고 있는 3M의 NSTF(Nano Structured Thin Film)촉매와 ANL의 MSTF(Meso Structured Thin Film)촉매 및 Toshiba의 Sputtering 촉매로 대표되는 벌크특성유사 백금/합금계 촉매의 두 가지이다.
나. 백금/담지체 전극촉매
고분자연료전지의 촉매로는 귀금속계인 Pt와 비귀금속계인 Ni-Fe 합금 및 산화물계 등이 개발되고 있으나 2020년대까지는 Pt 촉매가 주류를 이룰 것으로 전망된다. 따라서 Pt 촉매량 저감과 장수명화가 기술개발의 중심이 된다. 수 ㎚크기의 Pt 입자의 응집과 용출을 방지하기 위한 최근의 기술개발로는 Pt 촉매입자의 담지체 개발과 Pt 산화막 형성억제 기술 등이 주로 논의되고 있다. 그간 널리 사용되던 카본 컴포짓 담지체의 부식이 Pt 촉매기능의 저하와 미치는 영향이 큼이 확인되어 도전성 세라믹 담지체 연구가 활발하게 전개되고 있다. Yamanashi대학의 M. Watabe그룹은 Sn0.96Sb0.04O2-d를 합성하고 나노캡슬법으로 Pt를 고분산 시킨 새로운 촉매시스템을 개발하여 n-Pt/GC의 약 80배, 시판의 Pt/CB의 약 1,600배의 내구성을 확인했다. 그림 4는 전위 사이클 수명시험 결과이다.
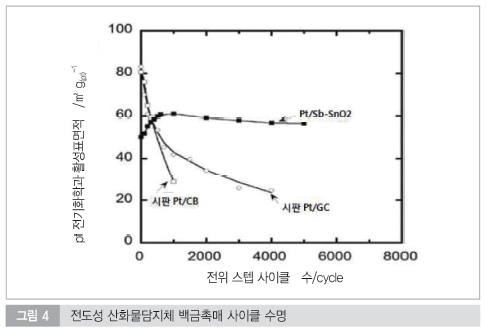
세라믹 담지체인 Sb를 고용치환한 SnO2는 금속유기착체 등의 용액을 고온 반응장의 1400℃화염속에 분무하여 작제할 수 있다. 비결정상이 없는 평균 입자경은 8.0±2.4㎚이다. 비표면적 100㎡/g의 구상의 경정립자로 1차 입자가 서로 융착한 응집체구조를 갖는다. Sb-SnO2 담지체위에 평균 입자경은 1.7±0.3㎚, 담지량 16.4wt%의 백금 나노입자를 고분산시킨 것이다.
그림 4로부터 기동정지 모의내구성시험결과로부터 탄소담지체의 부식열화과제를 극복하였음을 확인했다.
다. 3M-NSTF, ANL-MSTF 촉매
2006년 이후 3M의 M. K. Debe 등에 의하여 개발된 나노박막구조의 백금합금 촉매가 전통적인 카본 담지체 나노백금분산 촉매보다 산소환원활성도가 매우 높고 내구성, 가격 및 생산성에서 크게 향상됨이 밝혀졌다. 그림 5는 카본 담지체 나노백금입자 분산 촉매, 백금 벌크 촉매 및 나노박막 합금촉매(Nano Structured Thin Film)와 백금단결정 표면 노출 Pt3Ni합금촉매(Meso Structured Thin Film) 등의 ORR활성도 향상을 비교한 것이다.
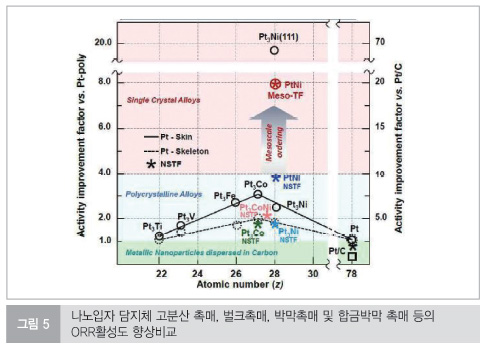
ANL에 실시한 2013년 자동차용 연료전지시스템의 대량 생산시 비용분석에서 백금 로딩량 0.196㎎/㎠를 실현하여 2012년에 48$/㎾h를 달성하는데 크게 공헌한 바 있다.
그림 6은 이들 촉매들의 ORR촉매활성도를 표면활성동도와의 관계를 정리한 그래프이다. 그림 6의 (a)는 RDE로, 그림 6의 (b)는 MEA를 만들어 900㎷, 80℃ 150kPa 포화 O2조건에서 측정한 값이다.

10배 이상의 백금 비면적 활성과 1/1000이하의 F이온 방출로 전해질막의 열화를 저감시켰다. 카본을 담지체로 사용하지 않아 카본 부식이 없다. 백금의 용출이 저감되었다.
그림 7과 그림 8은 75℃에서 Pt/C와 Pt NSTF 촉매의 0.6~1.2V ; 20㎷/s의 cyclic voltammetry 사이클 시험에서 전기화학적 활성비면적 변화결과이다.
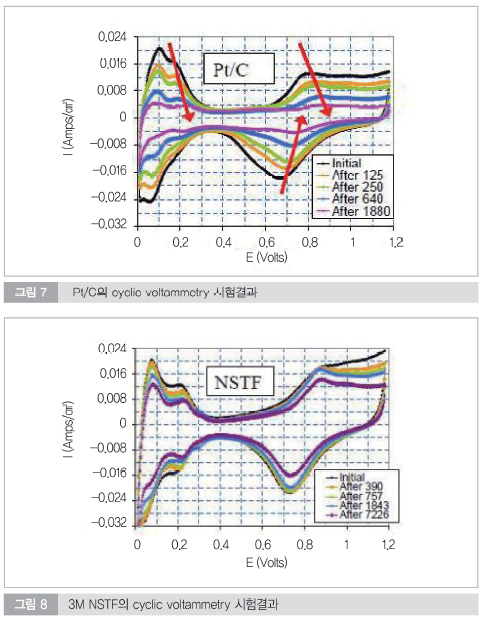
Pt/C에서는 2,000사이클 미만에서 90% 가까이가 저감된 것과 대조적으로 5,000~9,000사이클에서 여러 온도영역에서 67% 이상 안정화되어있음을 보이고 있다. 운전정지로 양극에의 수소공급이 퍼지 되었을 경우를 상정한 공기-공기 기동에서는 4,000번 이상 가혹시험, 1일 4회 단거리 운전을 가정한 경우와 -25℃ 기동 70회, -5℃ 기동 1000회 이상의 내구성에 견디는 것으로 보고하고 있다.
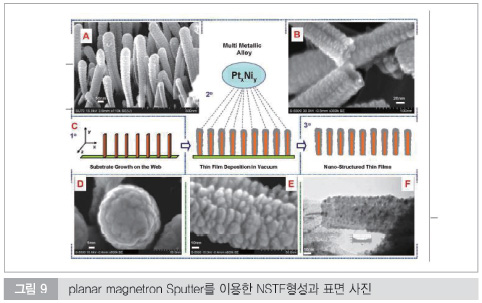
3M의 NSTF는 단층구조를 갖고 방향이 정렬된 길이 1㎛이하, 단면적이 30㎚×50㎚의 perylene red 결정질 유기위스커 표면에 planer magnetron sputter로 백금 등의 촉매금속을 증착시킨 것이다. 3M의 NSTF 촉매형성과정과 표면 현상을 나타낸 것이 그림 9이다.
유기담지체 나노위스커는 전기전도체가 아니기 때문에 부식 전류가 흐르지 않으며 체심입방체구조를 갖어 촉매박막코팅에 영향을 미친다. 코팅된 백금촉매 등은 2차원적인 표면을 가지며 전기전도도 담당한다. ORR촉매작용으로 생성된 물이 프로톤과 산소의 통로를 형성시키기 때문에 카본 담지체 나노백금분산 촉매에서의 이오노머를 필요로 하지 않는다. NSTF의 증명된 성능들로서는 표면활용률, 안정성, 배금 로딩량의 혁신적인 저감, 담지체 부식내구성, 대량 생산성 그리고 촉매반응과정에서 부차적으로 생성된 H2O2가 전해질막을 열화시키는 것을 NSTF에서 발생되는 F-이온이 억제시키는 효과가 있다는 것들을 들 수 있다.
담지체의 두께가 엷어 담지체가 차지하는 체적이 작아 카본 담지 백금촉매와 비교하여 10~20배 촉매두께가 얇다. 내구성은 DOE의 개발목표인 5,000시간을 초과하고 있고 촉매활성화면적은 Pt/C에서 2500사이클에서 약 90%가 상실되는 것과 대조적으로 NSTF는 4225사이클에서 ~20%정도이다.
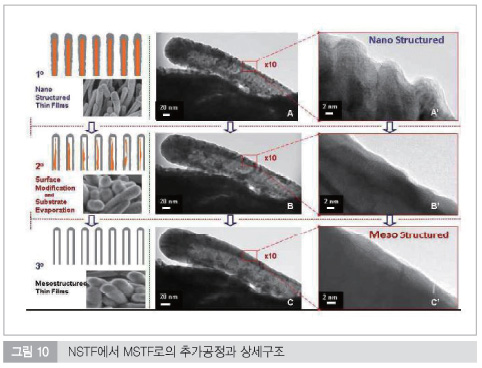
ANL의 MSTF는 3M의 Pt3Ni NSTF막을 백금단결정 표면이 노출되도록 400℃에서 2시간 동안 열처리하여 제작한 것이다. 이 과정을 나타낸 것이 그림 10이다. 표면 초구조(Surface super-structure)가 형성된 것이다.
열처리(annealing)로 나노백금입자와는 달리 2차원 격자구조로 자유에너지가 가장 작은 {111}결정면이 표면에 나타나는 확률이 커져 벌크 백금 층과 유사한 전자상태를 띠게 된다. 나노입자의 약 10배 이상의 산소환원촉매비활성을 띠게 되며 프로톤 통로확보를 위한 이오노모를 필요로 하지 않는 특성을 활용하는 것이다. 이 과정에서 유기결정질의 위스커는 증발하고 금속박막만이 남는다.
그림 11은 PtNi(111)이 표면에 나타나면 약 100배의 Pt/C 산소환원반응비활성을 보인다. 이때의 표면층과 그 밑 3개 층의 Pt와 Ni의 조성비를 도식화한 것이다.
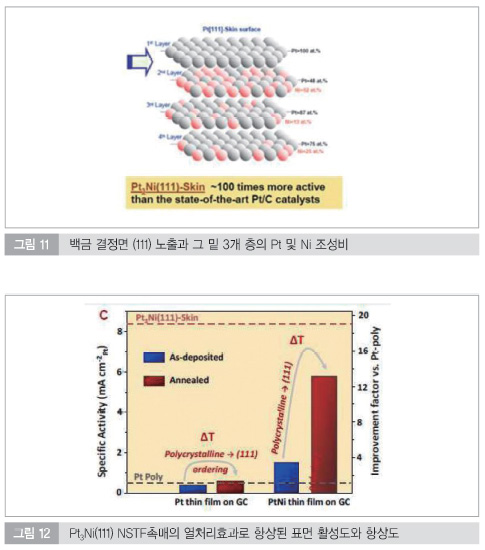
그림 12는 Pt3Ni NSTF의 열처리효과로 백금단결정면(111)이 표면에 나타 나 향상된 표면활성도와 다결정 백금 NSTF촉매의 표면 비활성도 비교를 나타 낸 것이다. Pt NSTF에 비하여 PtNi NSTF에서 4배 향상되었고 MSTF에서는 8배로 향상되었음을 보인다.
그림 13은 3M의 NSTF공정의 개념도이다. 마이크로구조를 갖는 기판위에 PR149 위스커를 증착하고 열처리한 뒤 planer sputter로 촉매합금을 증착한다. 모든 공정의 one-step으로 이루어진다. 5단계 공정을 갖는 Pt/C보다는 단순한 공정을 보인다.
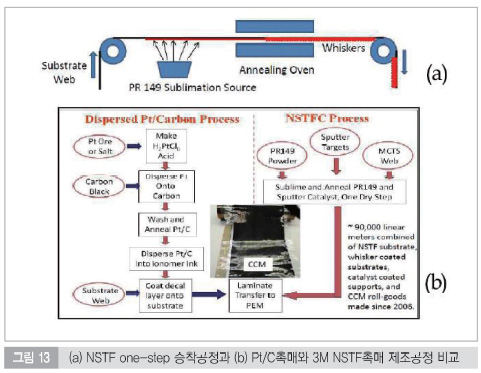
전해질막(달러소계 전해질 막 vs 고온 저가습 전해질막 vs 탄화수소계 전해질막)
ANL 2012 연료전지 스택에는 25㎛두께의 고 다공질ePTFE(expanded polytetrafluoroethylene) 기판에 Nafion 이어 노모를 코팅하고 공격을 채운 달러소계 전해질막을 널리 채용되고 있는 전해질막으로 사용하고 있다. Nafion은 perfluorinated 측쇄에 sulfonic acid group을 첨가한 것이다. 충분히 가습된 30℃에서 프로톤 전도가 0.1S/㎝인 화학적 안정성과 열적 안정성이 우수한 전해질막이다.
perfluorosulfonic acid(PFSA) 전해질막은 상대습도가 낮아지면 급격하게 프로전도도가 저하되어 면밀한 습도관리와 80℃근방의 온도관리를 필요로 한다. 이것이 내연기관대비 큰 라디에이터와 가습시스템을 필요로 한다. 120℃정도의 운전온도와 저 가습 운전이 가능한 전해질막을 개발을 DOE와 US Drive의 목표로 정하고 있다.
가. 고온 저가습 전해질 막 개발
고온 연료전지시스템의 열관리시스템과 가습시스템을 간소화, 더 나아가서는 삭제를 실현하여 커다란 비용저감을 실현할 수 있어 DOE와 NEDO등이 적극적으로 개발하고 있는 연료전지용 전해질 막이다. 현재로서는 DOE 2020년 성능목표를 충족시키는 것은 3M의 multi-acid side chain을 갖는 PFIA(Per Fluoro Imide Acid)전해질막이고 이를 실현할 것으로 전망되는 것으로 FuelCell Energy가 개발하고 있는 multi-component composite membrane(mC2) 등이 있다.
널리 사용되고 있는 PFSA(PerFluoro Sulfonic Acid)는 EW(equivalent weight)가 낮은 것이 고온저가습에서 이온전도도가 높은 특성을 보인다. 그러나 EW가 낮을수록 팽윤율이 증가하는 등의 기계적 강도의 저하가 크다. 3M은 그림 14와 같이 이온전도성을 향상시킬 프로톤 도너역할의 multi-acid chain을 첨가한 625 EW PFIA를 개발하고 추가적으로 화학적 활성이 없는 나노섬유를 참가하여 비등수속에서의 팽윤 저항성을 증대하여 기계적 특성을 16배 향상시켰다.

-30, 20, 80 및 120℃에서 ASR(area specific resistance)의 DOE 목표를 충족시키고 있다. 20,000번의 상대습도 변경시험과 600시간의 OCV(open circuit voltage)반복시험에서도 내구성을 입증했다.
FuelCell Energy는 기계적 강도를 보강하는 지지층에 수분 유지층과 프로톤 도너 층을 적층하는 그림 15과 같은 mC2 전해질막을 개발하였다. 체적증가 없이 수분흡수량을 증대시키기 위하여 zeolite 나노입자를 첨가하였다.
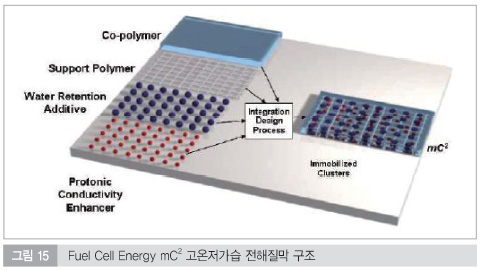
그림 16은 mC2의 30, 80 및 120℃에서의 상대습도에 따르는 이온전도도를 나타낸 것이다. 120℃ 50%의 상대습도에서 0.113S/㎝의 평균값을 보이고 있다. 상대습도 40%에서는 DOE 목표를 약간 못 미치는 것을 볼 수 있다.
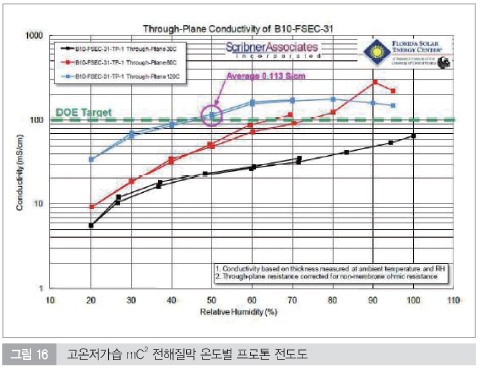
나. 탄화수소계 전해질 막
2008년 Honda가 세계 최초로 리스판매를 개시한 Honda FCV ‘Clarity’에는 JSR의 아로마틱 전해질막을 사용한 V-flow 연료 전지스택이 탑재되었다.
Yamanashi 대학의 M. Watabe그룹은 신규탄화수소계 전해질막의 sulfonic acid를 포함하는 친수성부분을 프로톤의 이동경로가 충분하게 확보될 수 있도록 block 공중합법으로 친수성 부분만을 고밀도로 모은 전해질막을 Kaneka와 공동연구로 개발하였다. Kaneka는 새롭게 개발한 전해질막의 roll-sheet 생산기술을 개발했다.
그림 17은 종래형의 랜덤 중합을 블록공중합으로 개선하여 수소이온통로를 확보하게 되어 전도성이 향상되는 메커니즘을 개념화한 것이다.
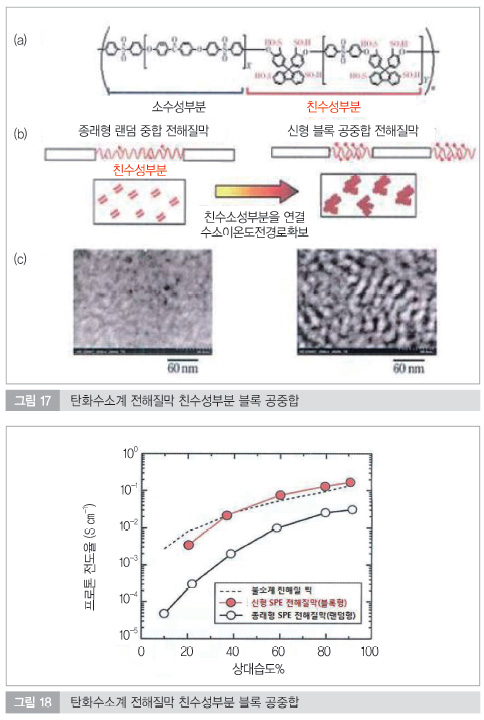
그림 18은 이들이 개발한 블록형 SPE전해질막의 프로톤 전도율 특성곡선이다. 달러소계전해질막에 손색이 없는 특성을 보이고 있다. 탄화수소계 전해질막으로서는 가장 우수한 성능을 보이고 있다. 공동연구기업인 Kaneka는 이 탄화수소계 전해질막의 롤-시트 제조공정을 성공적으로 개발하여 실용화시험 중에 있다.
금속분리판(bipolar plate, separator)
분리판의 선택은 스택의 소형화, 경량화 및 경쟁력확보에 중요한 인자가 된다. 탄소 컴포짓과 금속 분리판으로 크게 나누어진다. 금속 분리판 채용이 증가하고 있다. 금속 분리판도 부동태막 형성방법 등 차별화를 기하고 있다.
금속분리판은 공업적으로 널리 사용되고 있는 스테인리스 금속판을 사용하여 대량생산이 가능하고 얇기 때문에 출력밀도가 높고 전기전도가 우수하다 는 등의 장점이 있는 반면, 스템핀 형성량에 한계가 있고 부식에 취약하다는 단점이 있다. 자동차용으로는 출력밀도의 증대로 소형 경량화가 가능한 금속분리판 사용 연료전지 스택을 모든 완성차기업이 사용하고 있다.
DOE ANL 연료전지시스템에서 채용하고 있는 것은 TreadStone이 개발한 Au-dot 금속분리판이다.
TreadStone팀은 그림 19에서 보듯이 TiO2 등이 내부식성 산화물을 코팅한 뒤 직경 5㎛ 정도의 금 전기통로를 spray-gun을 사용하여 20~70㎛ 간격으로 넓적한 형태로 분무하여 < 1~2%의 전기통로를 형성시켰다. 단위 inch당 500,000개의 통로를 확보함으로써 가스 확산층과의 전기통로를 확보함과 동시에 금과 스테인리스판과의 접착성도 향상시켰다.
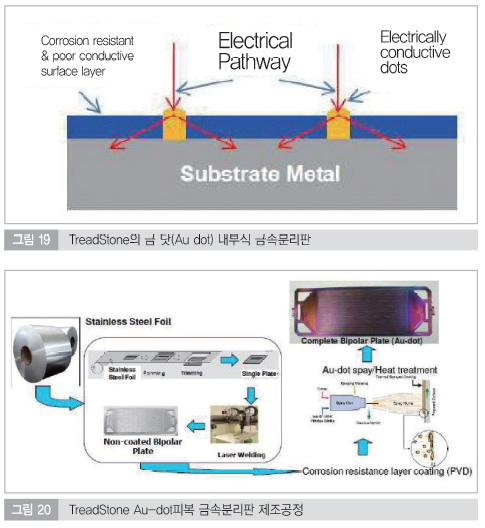
그림 20은 TreadsStone 금속분리판 제작공정이다. 스테인리스 박판에 부식재를 코팅한 뒤 금을 스프레이건으로 분무한 뒤 열처리하여 사용한다. DOE가 요구하는 성능내구성시험에 통과하여 자동차용 연료전지에 탑재가 가능한 것으로 평가되고 있다.
Sumitomo Metal은 SS 316강중에 다수분산하는 미세한 CrB를 주체로 하는 도전성 금속석출물을 염화제2철수용액의 스프레이 부식(splay etching)처리하여 시킴으로써 표면의 도전성을 개선했다. 연료전지 환경속에서의 우수한 내식성은 SUS 316상당의 재료설계로 조성함으로써 확보하고 있다. 금 등의 코팅을 하지 않아 박리나 균열에 의한 특성열화가 없는 보고하고 있다. 금 등의 코팅을 하지 않아 박리나 균열 등에 의한 성능열화가 없다. 모든 성능시험에서 적합성이 실증되었다. 20만회이상의 프레스성형가공이 가능한 기술과 양산체제도 갖추었다.
Honda는 양산을 전제로 한 연료전지 스택에 세계 최초로 부동태막 형성 스테인리스 금속판을 분리만으로 채택했다. 그림 21은 Honda V-Flow FC 스택에 탑재된 분리판이다.
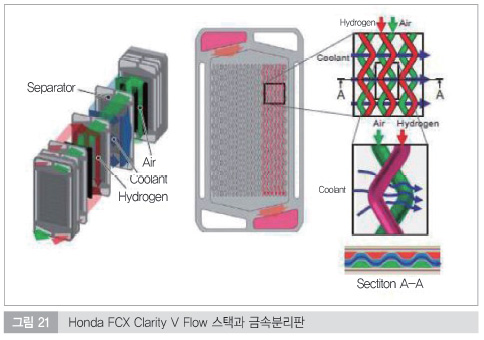
그림 22는 종래의 유로패턴과 Honda가 채택한 파형 유로패턴의 차이와 2개 MEA층에 걸치게 되는 금속분리판의 냉각유로 확보개념을 도식화 한 것이다.
GDL(가스확산층)
SA는 2012년부터 가스확산층으로 Balllard의 탄소섬유부직포에 2층의 teflonated 마이크로 porous layer를 적층한 것을 채용하고 있다. 50만 대 연료전지자동차 소요량인 10×10+6㎡/year에 4.45$/㎡, 5,000대용(80,000㎡/year)의 생산량에는 56$/㎡가 된다고 보고하고 있다.
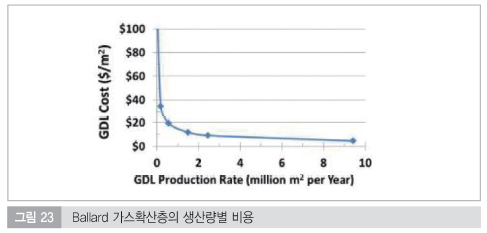
MEA 형성기술
그림 24는 3M 특허에 표시한 MEA 형성을 위한 gasket 적용공정이다. 이것으로 콤팩트한 스택형성에 크게 기여했다. 그림 25는 3M의 NSTF 촉매막과의 sub-gasket 형성과정을 도식화한 것이다. 3M MES 성형공정이 고진공황경에서 수행되는 것과 대조적으로 Gore는 생산성을 향상시킨 그림 26과 같은 공정을 개발하여 단순화시켰다.
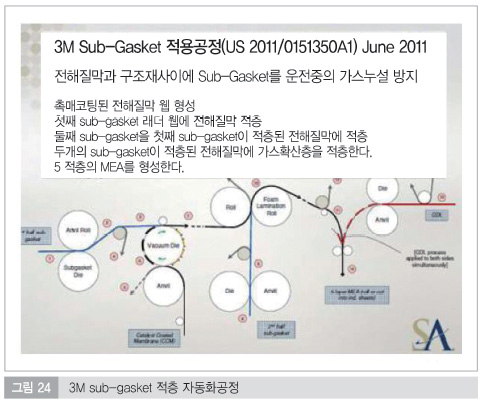
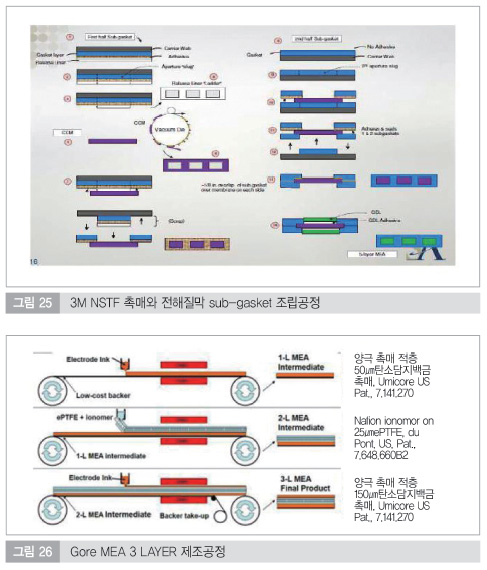
2012년도 규정 연료전지 시스템 비용분석에 사용하고 있는 3M NSTF촉매/Nafion공전해질막 적층공정과 2013에 반영할 Gore MEA 형성공정 비용를 비교한 것이 그림 27이다.
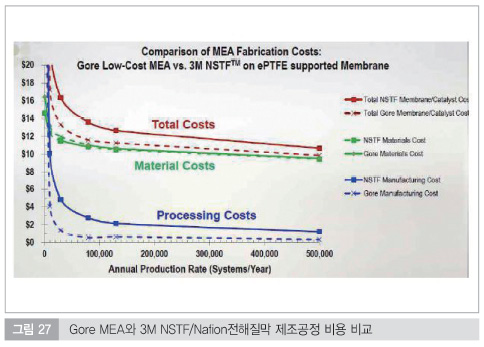
백금이 차지하는 비용가 크기 때문에 소재 비에서는 거의 차이가 나타나지 않는다. 진공공정을 필요로 하는 3M 공정에 비하여 이의 필요가 없는 Gore 공정이 공정속도도 빠르고 비용도 저력해질 것으로 보인다. 출력특성이 공정선택의 기준이 된다.