FR-4 기판 / 솔더 마스크 표면의 청결도가 중요
적절한 어셈블리용 플럭스 선택, ‘크리프 부식 제거’
인쇄회로기판의 크리프 부식은 표면의 화학적 특성에 매우 민감하다. 깨끗한 FR-4도 깨끗한 솔더 마스크 표면도 크리프 부식을 지원하지 않는다. 일반적으로 로진계 웨이브 솔더링 플럭스와 로진계 플럭스를 포함하는 솔더 페이스트로 조립된 보드는 크리프 부식에 대한 내성도 있다. 한편, 유기산 플럭스에 의해 솔더 마스크 표면에 남은 잔류물은 ‘크리프 가능한’ 표면을 형성하고 구리 황화물의 크리프 부식을 지원하는 데 매우 활성적이다. 어셈블리 플럭스의 적절한 선택은 부식성이 높은 글로벌 환경에서 ImAg 도금 회로 기판과 관련된 크리프 부식으로 인한 제품 고장을 제거할 수 있다.
요약
전자 산업계가 무연 어셈블리 및 미세 피치 회로로 이동함에 따라 널리 사용되는 인쇄 배선 기판(PWB) 마감재인 SnPb HASL이 OSP, ImAg, ENIG 및 ImSn과 같은 무연 PWB 마감재로 대체되었다. SnPb HASL은 두꺼운 코팅과 고유한 내부식성으로 인해 기본 구리의 우수한 부식 방지 기능을 제공하는 반면, 무연 보드 마감은 매우 얇은 코팅으로 인해 기본 구리에 대한 부식 방지 기능을 감소시킨다. ImAg의 경우 코팅 재료 자체가 더 공격적인 환경에서도 부식될 수 있다. 이는 오염 물질이 포함된 황 함량이 높은 환경에 노출된 제품에 대한 문제이기도 하다. 이러한 부식성 환경에서 크리프 부식이 관찰되어 매우 짧은 서비스 수명(1~5년)에서 제품 고장으로 이어졌다. 제품 배포 후 1년 이내에 크리프 부식 실패도 보고되었다. 이러한 현상은 크리프 부식을 이해하기 위한 업계 전반의 노력을 촉발했다.
본고에서는 PWB의 크리프 부식이 표면에 매우 민감하다는 것을 보여줄 것이다. 깨끗한 FR-4나 깨끗한 솔더 마스크 표면은 크리프 부식을 지원하지 않는다. 일반적으로 로진계 웨이브 솔더링 플럭스와 로진계 플럭스를 포함하는 솔더페이스트로 조립된 기판도 크리프 부식에 강하다. 그러나 유기산 플럭스에 의해 솔더 마스크 표면에 남아 있는 잔류물은 활성도가 높아 구리 황화물의 크리프 부식을 지원한다. 적절한 어셈블리용 플럭스 선택은 부식성이 높은 글로벌 환경에서 ImAg 도금 회로 기판과 관련된 크리프 부식으로 인한 제품 고장을 제거할 수 있다. 또한, 혼합 유동 가스 테스트(MFG)는 응축 조건 없이 실험실에서 크리프 부식을 시뮬레이션하기 위한 현실적인 가속 테스트를 보여준다.
서문
무연 PWB 최종 마감재는 전자 회로 조립 중 부품 접합을 위해 납땜 가능하고 coplanar surface을 제공하는 주요 설계 목표로 개발되었다. 보드 마감재의 단기 내식성은 납땜성(최대 12개월)의 저장 수명을 유지하기 위해 중요하지만, 장기 내식성은 요구되거나 고려되지 않았다.[1],[2],[3]
디바이스의 수명 동안 현장에서 장기간의 내식성은 기존의 보드 마감인 HASL(hot air solder leveling)에서 문제가 되지 않았다. 두꺼운 코팅과 고유한 내식성으로 인해 기본 구리의 우수한 부식 방지 기능을 자원하기 때문이다. 무연 PWB 마감재에 대해 광범위한 테스트 및 신뢰성 평가가 수행되었다. 그러나 현장에 배치된 후 무연 PWB 마감재의 내식성에 대해서는 거의 관심을 기울이지 않았다. 최근, 무연 PWB 마감재의 내식성은 세계 여러 지역에서 관찰되는 조기 현장 고장으로 인해 상당한 관심을 불러일으켰다. 부식으로 인한 현장에서의 제품 고장 연구와 이를 실험실에서 시뮬레이션한 결과가 발표되었다.[4],[5],[6],[7]
‘▶ 크리프 부식, ▶ 부식 생성물의 박편(flaking)’이라는 두 가지 유형의 고장이 확인되었다.[6] 두 경우 모두 반도체-전도성 제품군의 전자기기에서 간헐적이거나 영구적인 단락을 유발하기도 한다.
H2S, SO2, NO2 및 Cl2를 포함하는 혼합 유동 가스(MFG)는 현장 환경 조건을 시뮬레이션하고 전자 디바이스에 대한 가속 테스트를 수행하는데 널리 사용되고 있다. 부식 생성물의 박편은 MFG 테스트에서 쉽게 재현될 수 있지만, 크리프 부식은 일관되게 재현되지 않았다. 예를 들어, 깨끗한 IPC-B25 comb pattern을 사용하여 준비한 샘플은 부식 제품의 심각한 박편이 관찰되었음에도 불구하고 국제적인 조건[6] 하에서 MFG에 장기간 노출 후 크리프 부식이 경미하거나 전혀 나타나지 않았다. 그림 1은 국제적인 조건 하에서 MFG에 40일 노출된 후 Cu 트레이스만 있는 샘플(오른쪽)과 ImAg 도금된 Cu 트레이스(왼쪽)가 있는 샘플을 보여준다.[6] 두꺼운 부식 생성물(주로 황화구리)과 부식 생성물의 박편이 두 경우 모두에서 관찰되었지만 두 경우 모두 트레이스 사이의 FR-4 표면을 가로질러 크리프 부식의 징후가 보이지 않았다. 그러나 표면에 특정 유형의 오염이 있는 경우 MFG 테스트에서 크리프 부식이 쉽게 발생했다.
그림 2에서는 MFG 노출 2일 후의 ImAg 도금처리된 IPC-B25 comb 쿠폰을 보여주고 있다. 대부분 영역에서 크리프 부식이 관찰되지 않았지만 ImAg 도금 트레이스에서 심각한 국부적인 부식이 관찰되었다. 흥미롭게도 쿠폰 중간에 물방울 모양의 영역 내에서 크리프 부식이 관찰되었으며 1.3㏀의 쇼트가 측정되었다. 이 결과는 크리프 부식이 높은 표면 특성이고, 표면 화학적 특성에 민감하다는 것을 나타낸다. 깨끗한 FR-4 표면은 크리프 부식을 지원하지 않는 반면, 오염된 FR-4 표면은 크리프 부식을 지원한다. 외관상으로는, 부식 생성물이 이러한 표면에 서서히 나타나기 위해서는 특정 표면 특성이 필요하다.
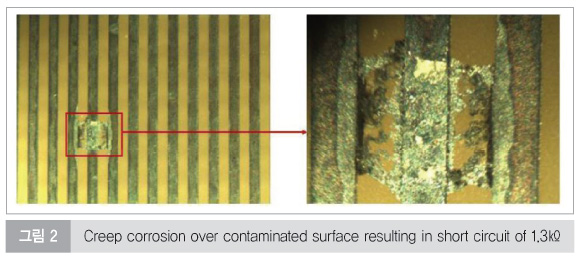
PWB 조립에서 플럭스 잔류물은 일반적인 표면 오염 물질로 여겨진다. ‘플럭스 잔류물이 크리프 부식을 촉진합니까(특정 유형의 표면 오염의 경우에서와 같이)?’라는 의문이 들 수밖에 없다. 이게 사실이라면 현장에서 조립된 회로 기판에서 관찰된 크리프 부식과 어셈블리 플럭스에서 경험하지 못했던 LAB실 샘플의 크리프 부식에 대한 일관성 없는 현상 사이의 차이를 설명할 수 있다. 크리프 부식에 관한 플럭스 잔류물이 미치는 영향을 조사하기 위해 소비자 전자 제품에 사용되는 ImAg 도금처리된 PWB를 구입하였고, 셀렉티브 웨이브 솔더링을 적용하여 어셈블리하였다. 보드는 실험실에서 MFG에 노출시켰다. 그림 3은 국제 조건 하에서의 MFG 노출 5일 후의 결과를 보여주고 있다. 뚜렷하게 다른 세 영역이 관찰되었다. (1) 오른쪽 상단 모서리 영역, via가 셀렉티브 솔더링되었는데, 솔더에 의해 완전히 덮어졌다. 이 영역에서는 부식이 관찰되지 않았다. (2) 왼쪽 하단 모서리 영역, 납땜되지 않았고 via에 Ag 마감재가 완전하게 노출되었다. 이 영역에서 심각한 부식이 관찰됐지만, 크리프 부식은 보이지 않았다. (3) 솔더링되지 않은 영역과 웨이브 솔더링된 영역 사이의 경계 영역, 이 경계 영역에서 심한 크리프 부식이 나타났으며 크리프 부식으로 인한 쇼트도 관찰되었다. 솔더링된 부분의 부식 없음, 경계 부분의 크리프 부식, 솔더링되지 않은 부분의 크리프 없는 부식 패턴이 회로 기판 전체에 걸쳐 반복적으로 관찰되었다.
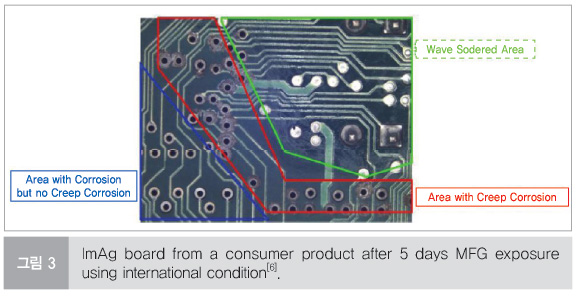
플럭스는 셀렉티브 웨이브 솔더링 동안 솔더링된 영역에서 인접한 경계 영역으로 이동하고 경계 영역에 잔류물을 남겼다. 노출된 Ag와 경계 영역의 플럭스 잔류물의 조합은 Ag를 부식시킨 후에 부식 생성물이 플럭스 잔류물로 덮인 솔더 마스크 표면에서 마이그레이션할 수 있는 운송 매체를 제공한다. 솔더링 영역에서 멀리 떨어진 영역의 Ag 도금된 via는 부식되었지만 깨끗한 솔더 마스크 표면이 부식 제품의 크리프를 지원하지 않기 때문에 크리프 부식의 징후를 보이지 않았다. 이 결과는, 크리프 부식이 매우 표면적이며 특정 유형의 표면만이 크리프 부식을 지원할 수 있음을 보여준다. 솔더 마스크, 플럭스 및 프로세스 조건의 ‘잘못된’ 조합은 ImAg 도금처리된 회로 기판에 대해 ‘크리프 가능한’ 표면을 생성할 수 있다. 크리프 부식 방지 ImAg 또는 기타 PWB 최종 마감재를 찾는 작업은 솔더 마스크와 플럭스가 있는 어셈블리된 기판에서 수행되어야 한다. MFG 테스트는 크리프 부식에 대한 실행 가능하고 현실적인 가속 노화 테스트를 제공한다.
크리프 부식을 돕는 플럭스 잔류물은 ImAg 도금 회로 기판에만 국한되지 않는다. 유사한 결과가 OSP 마감재에서도 관찰되었다.[8] 그림 4에서는 국제 조건 하에서[6] MFG 노출 5일 경과된 2개 PWB를 비교하여 보여주고 있다.
2개의 PWB 모두 OSP로 최종 마감 처리가 되어 있지만 서로 다른 유형의 솔더 페이스트로 어셈블리되었다. 왼쪽 기판은 유기산 플럭스를 함유한 솔더 페이스트로 어셈블리한 반면, 오른쪽 기판은 로진계 플럭스를 함유한 솔더 페이스트를 사용하였다. MFG 노출 5일 경과 후, 유기산 플럭스를 함유한 페이스트를 사용하여 어셈블리된 기판에서 심각한 크리프 부식이 관찰되었다. 반면에 로진계 플럭스를 포함하는 페이스트를 사용한 보드에서는 심각한 크리프 부식 없이 노출된 OSP 영역에서만 국부적인 부식이 나타났다. 또한 크리프 부식의 정도는 어셈블리 후 클리닝 작업에 따라 다르며 보드의 청결도와 관련이 있다. 서로 다른 유형의 플럭스로 어셈블리된 보드 간의 이러한 급격한 차이는 플럭스 잔류물이 크리프 부식에 미치는 중요한 역할을 보여주었다. 크리프 부식에 대한 다양한 어셈블리 플럭스의 영향을 자세히 설명하기 위해 8개의 서로 다른 웨이브 솔더링 플럭스와 6개의 서로 다른 솔더 페이스트를 포함하는 체계적인 연구가 수행되었으며 그 결과가 이 문서에 보고하였다.
실험조건
테스트 보드
그림 5에서는 본 작업에 사용된 테스트 보드의 상단과 하단 이미지를 보여주고 있다. 다양한 라인 너비와 간격을 가진 9개의 트레이스 빗살(comb) 패턴(상단에 7개, 하단에 2개)이 포함되어 있다. 9개의 트레이스 패턴 중 5개는 크리프 부식에 맞게 ImAg 및 솔더 마스크 인터페이스의 최대 영역을 생성하기 위해 트레이스 전체에 솔더 마스크 스트라이프(solder mask stripes)가 있다. 4개의 빗살(comb) 패턴의 쓰루홀이 있는데, 각 측면에 2개의 SMD(solder mask defined) via와 2개의 NSMD(non-solder mask defined) via가 적용되었다. QFP 부품용 패턴도 상단에 포함되어 있다. 바닥면의 중간 영역은 셀렉티브 웨이브 솔더링을 위해 표시되었다(그림 5의 오른쪽 이미지 참조).
테스트 조건
문헌과 Alcatel-Lucent 내의 현장 및 실험실[9],[10],[11],[12],[13],[14],[15],[16]의 광범위한 내부 테스트를 기반으로 혼합 유동 가스(MFG) 테스트 파라미터를 선택하여 현재 상황에서 발생할 수 있는 최악의 필드 조건을 시뮬레이션했다. Battelle 및 Telcordia MFG 테스트 조건은 주로 북미 환경을 시뮬레이션하기 위해 설계되었으므로 훨씬 더 높은 H2S 농도는 보다 공격적인 환경에서 빠른 부식 속도(현장에서 부식 제품의 주요 구성 요소인 황화구리)를 시뮬레이션하는 데 사용해야만 했다. 부식성 가스의 농도는 표 1에 요약되어 있다. 온도는 40℃이고 습도는 70~75% RH 사이였다. 챔버의 부식 속도는 Cu 쿠폰 중량 증가를 사용하여 모니터링했으며 ~500nm/day(동등한 황화구리 두께)로 결정되었다. 유사한 두께의 부식 생성물이 전 세계 일부 현장[15],[16]에 1년 동안 배치된 Cu 쿠폰에서 관찰되었다. 따라서 해당 위치의 설비 1년 현장 배치는 MFG 챔버에서 1일 노출로 시뮬레이션할 수 있다. 비교를 위해 북미 지역의 일반적인 부식률은 실내에서 60~90nm/년, 실외 환경에서 180~270nm/년임을 고려했다.[13]
테스트 보드
테스트 보드는 다양한 유형의 ImAg 및 솔더 마스크를 사용하여 6개의 다른 보드 업체에서 제작되었다. 그런 다음 보드는 8개의 서로 다른 웨이브 솔더링 플럭스(4개의 ORL0, 3개의 ROL0 및 1개의 ROM1 플럭스)와 6개의 서로 다른 솔더 페이스트(4개의 ROL0 플럭스 포함 및 2개의 ROL1 플럭스 포함)를 사용하여 4개의 서로 다른 EMS 업체에서 어셈블리되었다. 그런 후 샘플은 표 1에 설명된 조건을 사용하여 MFG 테스트를 거쳤다. 서로 다른 유형의 플럭스 간에 크리프 부식의 주요 차이점이 관찰되었다. 다른 보드 업체(다른 ImAg 및 솔더 마스크 조합)에서 제조된 보드 간에는 약간의 차이만 관찰되었다.
실험결과
모든 샘플은 초기 5일 동안 MFG에 노출되었다. 심각한 크리프 부식이 관찰되면 MFG 테스트를 종료했다. MFG 노출 5일 후 크리프 부식이 거의 없거나 전혀 없는 샘플의 경우 MFG 테스트를 10일, 15일 및 20일로 연장하였다.
어셈블리된 테스트 기판 외에도 6개 업체 모두에서 베어 기판을 수집했다. 11개의 베어 보드가 어셈블리된 테스트 보드와 함께 MFG 테스트하였다.
20일 동안 MFG에 노출된 후에도 모든 베어 보드에서 크리프 부식이 없거나 매우 미미했다. 어셈블리된 보드의 크리프 부식은 주로 쓰루홀 패턴 영역에서 발생했다. 그림 6은 바닥면(웨이브 솔더링면)에 있는 두 개의 쓰루홀 패턴에서 촬영한 이미지를 보여주고 있다. 그림 6의 왼쪽 이미지는 수령한 샘플에서 가져온 것이고 오른쪽 이미지는 20일 MFG 테스트 후 샘플에서 가져온 것이다. 이미지에서 명확하게 볼 수 있듯이 노출된 Ag 표면은 완전히 부식되었지만 인접한 유전체 표면(솔더 마스크 또는 FR-4 표면)에 대한 크리프 부식은 관찰되지 않았다. 이 결과는 깨끗한 솔더 마스크와 FR-4 표면이 크리프 부식을 지원하지 않는다는 이전 연구와 일치했다.
웨이브 솔더링 플럭스가 크리프 부식에 미치는 영향
8개의 다른 웨이브 솔더링 플럭스를 평가하였다. 8개의 플럭스 중 4개는 IPC J-STD-004 표준에 따라 ORL0으로 분류되며 주요 활성제로 유기산을 포함하고 있다. 4개의 ORL0 플럭스 중 3개는 수용성 플럭스이고 4번째 플럭스는 솔벤트계이다. 8개의 플럭스 중 나머지 4개는 로진 유형의 플럭스(RO)이다. 4개의 로진 플럭스 중 3개는 활성이 낮고 할로겐화물을 포함하지 않으며(ROL0) 네 번째는 중간 활성도를 가지며 0.5~2% 할로겐화물(ROM1)을 포함하고 있다. 어셈블리에 사용된 플럭스 유형에 따라 크리프 부식의 강한 의존성이 관찰되었다. 논의를 용이하게 하기 위해 우리는 관찰된 크리프 부식의 정도에 따라 샘플을 세 그룹으로 나누었습니다. 1) 나쁨(보통의 크리프 부식에서 심각한 크리프 부식까지), 2) 경계(플럭스 잔류물로 인한 작은 고립된 영역의 크리프 부식), 3) 양호(플럭스 잔류물 이외의 명백한 오염으로 인한 크리프 부식이 없거나 경미하거나 국부적인 크리프 부식).
성능이 좋지 않은 샘플
유기산 웨이브 솔더링 플럭스(유형 ORL0)로 어셈블리된 샘플에서 최악의 크리프 부식이 관찰되었다. 그림 7은 솔벤트 기반 ORL0 플럭스로 어셈블리된 테스트 보드의 결과를 보여주고 있다. 두 이미지 모두 테스트 보드의 바닥면(웨이브 솔더링면)에서 촬영되었으며, 왼쪽 사진은 MFG 노출 전에 찍은 것이고 오른쪽 사진은 MFG 노출 5일 후에 찍은 것이다. 두 그림 모두에서 두 개의 쓰루홀 패턴이 포함되었으며, 두 패턴의 아래쪽 절반은 셀렉티브 웨이브 솔더링되었다. 프로세스 변동으로 인해 왼쪽 패턴은 솔더에 의한 부분적인 젖음만 보여주는 반면에, 오른쪽 패턴의 쓰루홀은 솔더로 완전히 덮였다. MFG 노출 5일 후 노출된 모든 ImAg(솔더로 덮이지 않음)는 완전히 부식되었다. 노출된 ImAg 표면에서 국부적인 부식이 관찰되었음에도 불구하고 두 패턴의 상단 절반은 크리프 부식을 나타내지 않았다. 반대로 솔더로 완전히 덮힌 부분을 제외한 셀렉티브 솔더링 부분에서는 심한 크리프 부식이 관찰되었다. 또한 솔더링 영역과 솔더링되지 않은 영역의 경계 영역에서도 크리프 부식이 관찰되었다. 이것은 그림 8에 표시된 이미지에서 더 명확하게 볼 수 있으며 두 개의 쓰루홀 패턴을 자세히 보여주고 있다.
두 경우 모두 납땜되지 않은 부분(각 이미지의 왼쪽)에서는 국부적인 부식만 관찰되었으며, 셀렉티브 솔더링 된 부분과 솔더링 된 영역과 솔더링 되지 않은 영역 사이의 경계 영역에서는 심한 크리프 부식이 관찰되었다. 또한 NSMD(non-solder mask defined) via에 솔더 마스크로 덮인 영역보다 크리프 부식이 먼저 발생한다는 점에 주목할 가치가 있다. 이 결과는 플럭스와 솔더 마스크의 조합이 크리프 부식이 발생할 수 있는 표면을 제공한다는 것을 의미한다. 테스트 보드의 윗면에서도 유사한 결과가 관찰되었다.
그림 9에서는 MFG 노출 5일 후 동일한 샘플의 윗면에서 촬영한 이미지를 보여주고 있다. 이미지 좌측의 쓰루홀은 국부적인 부식만 보였고, 우측의 솔더링 부위 그리고 솔더링 부분과 미납 부분의 경계 부위에서는 심한 크리프 부식이 관찰되었다. 웨이브 솔더링 플럭스는 웨이브 솔더링 동안 쓰루홀을 통해 흘렀고 솔더 마스크와 결합하여 크리프 부식이 발생할 수 있는 표면을 제공하는 윗면의 표면에 잔류물이 존재했다.
플럭스의 3개 수용성 ORL0 중 2개의 어셈블리된 보드에서도 심각한 크리프 부식이 관찰되었으며, 세 번째 수용성 ORL0으로 어셈블리된 보드는 약간의 크리프 부식을 나타내었지만 다른 두 개보다 훨씬 적었다. 그림 10은 MFG 테스트 전(왼쪽)과 5일 후(오른쪽) 한 샘플의 상단을 보여주고 있다. 흥미롭게도 솔더링 된 쓰루홀과 솔더링 되지 않은 쓰루홀 모두에서 심각한 크리프 부식이 관찰되었다.
분명히 웨이브 솔더링 플럭스는 솔더링된 부위의 쓰루홀을 통해 상부에 도달한 다음 웨이브 솔더링 중에 솔더링된 영역에서 솔더링되지 않은 영역으로 이동했다.
이러한 결론은 바닥면의 솔더링되지 않은 영역(웨이브 솔더링 동안 마스크로 보호됨)이 어떠한 크리프 부식도 나타내지 않았다는 사실에 의해 뒷받침된다. 그림 11은 MFG 테스트 5일 후 샘플의 SMD(solder mask defined)과 NSMD(non-solder mask defined) 쓰루홀의 클로즈업 모습을 보여주고 있다. 두 영역 모두에서 심각한 크리프 부식이 관찰되었다. 다시 말하지만, NSMD 쓰루홀용 오염된 플럭스의 FR-4 표면보다 오염된 플럭스의 솔더 마스크 표면에서 발생하는 크리프 부식이 명확하게 나타났다.
경계 샘플
앞서 언급한 바와 같이 세 가지 수용성 플럭스 중 하나로 어셈블리된 테스트 보드는 크리프 부식이 이 경우에도 관찰되었지만 크리프 부식 발생 비중이 현저히 적었다. 그림 12는 MFG 테스트 5일 전후의 보드를 상부에서 찍은 사진이다. 그림 10에 표시된 이미지와 비교할 때 이 샘플에서 크리프 부식이 훨씬 적게 관찰되었다. 크리프 부식은 선택한 영역에서만 발생했다. 그러나 그림 13의 확대도에서 볼 수 있듯이 크리프 부식이 관찰된 영역에서는 인접한 쓰루홀 사이에 단락이 발생했다.
좋은 샘플
유기산 플럭스(OR)와 달리 로진계 플럭스(RO)는 일반적으로 크리프 부식을 촉진하지 않는다. 이는 ROL0 플럭스로 어셈블리된 보드의 이미지가 표시된 그림 14에서 설명되어 있다. 두 이미지 모두 테스트 보드의 하단에 있는 두 개의 쓰루홀 패턴을 보여주고 있다. 왼쪽 이미지는 받은 그대로의 샘플에서 가져온 것이고 오른쪽 샘플은 MFG 테스트 5일 후 샘플에서 가져온 것이다. 이 샘플의 모든 영역에서 크리프 부식이 관찰되지 않았다. 그림 15는 SMD 쓰루홀 패턴 중 하나의 확대도를 보여주고 있다. 이 이미지에서 명확하게 볼 수 있듯이, 노출된 Ag 표면이 솔더링 및 비-솔더링된 영역 모두에서 심하게 부식되었음에도 불구하고 크리프 부식이 보이지 않았다.
적당한 활성도의 0.5~2% 할로겐화물(ROM1)을 함유하는 로진계 플럭스에서도 유사한 결과가 관찰되었다. 이는 그림 16과 그림 17의 이미지에서 보여주고 있다. 노출된 Ag 표면에서 심각한 부식이 관찰되었으나 어떠한 크리프 부식도 관찰되지 않았다. MFG 테스트는 또한 RO 플럭스와 어셈블리 샘플을 20일 연장되었으며 여전히 플럭스 잔류물로 인한 크리프 부식이 관찰되지 않았다.
웨이브 솔더링 플럭스 요약
앞서 논의한 바와 같이, 크리프 부식은 어셈블리에 사용되는 웨이브 솔더링 플럭스의 유형에 따라 달라진다. 표 2는 MFG 5일 후의 결과를 요약한 것이다. 11개 보드 모두에서 크리프 부식이 나타나지 않았다. 이는 깨끗한 FR-4 및 솔더 마스크 표면이 크리프 부식을 지원하지 않는다는 이전 연구 결과와 일치하다.
로진계 플럭스로 어셈블리된 18개의 테스트 보드 중 16개에는 약간의 크리프 부식이 나타나지 않았다. 로진계 플럭스로 조립된 18개의 테스트 보드 중 2개만이 국부적인 영역에서 크리프 부식을 보였고 ‘경계’ 성능 샘플로 분류되었다. 이 두 샘플 모두 동일한 플럭스와 솔더 마스크로 조립되었다. 이 두 샘플에서 관찰된 크리프 부식이 특정한 로진계 플럭스의 플럭스 조성 변화 때문인지 플럭스 잔류물 이외의 오염 때문인지는 분명하지 않았다. 이 시점에서 로진계 플럭스 잔류물이 크리프 부식을 촉진하지 않는다는 결론을 내리는 것이 타당하다. 대조적으로, 유기산 플럭스는 솔더 마스크 표면에 잔류물을 남겨 크리프 부식이 발생할 수 있는 표면을 제공한다. 유기산 플럭스로 어셈블리된 41개의 테스트 보드 중 25개는 심각한 크리프 부식이 나타났고, 그 중 9개는 일부 영역에서 크리프 부식을 보였다. 이 결과를 통해 유기산 플럭스 잔류물이 크리프 부식을 촉진하는 경향이 크다는 것을 유추할 수 있었다. 유기산 플럭스로 어셈블리된 7개의 테스트 보드에서 경미한 크리프 부식도 나타내지 않았다는 점은 흥미로웠다. 7개 샘플 중 4개는 ‘경계’ 정도의 상태로 유기산 플럭스로 조립된 13개 샘플에서 나온 반면, 나머지 3개는 성능이 낮은 유기산으로 어셈블리되었다. 이 예외적인 현상에 대한 한 가지 추론은 노출된 ImAg가 있는 영역에 활성 잔류물이 남아 있지 않다는 것이다. 이 성능 변화를 이해하기 위한 추가적인 작업이 필요하다.
솔더 페이스트가 크리프 부식에 미치는 영향
6개의 서로 다른 솔더 페이스트를 이번 연구에 포함하였다. 6개의 모든 솔더 페이스트는 활성도가 낮은 로진계 플럭스로 제조되었다. 6개 플럭스 중 4개는 할로겐화물이 없고(IPC 분류에 따른 ROL0) 나머지 두 개는 0.5% 미만의 할로겐화물을 포함하고 있다(IPC 분류에 따른 ROL1). MFG 테스트 5일 후 플럭스 잔류물에 의한 크리프 부식이 모든 샘플에서 관찰되지 않았다. 선택 샘플을 20일 연장하였으며, 여전히 플럭스 잔류물에 의한 크리프 부식이 관찰되지 않았다. 그러나 때때로 섬유-보조 크리프 부식이 관찰되었다. 그림 18은 MFG 테스트 5일 후 ROL1 플럭스를 포함하는 솔더 페이스트로 조립된 샘플을 보여주고 있다. 왼쪽 이미지는 노출된 ImAg 도금 트레이스의 심각한 국부 부식을 보여주고, 오른쪽 이미지는 인접한 트레이스를 가로지르는 광섬유이다. 광섬유는 황화구리로 덮여 있으며 인접한 트레이스 사이에서 132㏀의 단락을 발생시킨다. 크리프 부식이 표면에 매우 민감하다는 것을 다시 한번 입증하였다. 섬유 표면이 크리프 부식을 지원하기 위해 활성화되는 동안 깨끗한 솔더 마스크나 로진계 플럭스 잔여물은 ‘크리프 가능한’ 표면을 제공하지 않는다.
논의사항
크리프 부식은 고체 부식 생성물(일반적으로 황화물 및 염화물)이 전기장의 영향 없이 표면에서 마이그레이션하는 대량 이송 프로세스이다. 전기화학적 이동과 달리 크리프 부식은 양극과 음극 사이에 전기적 바이어스와 低-저항 전해 경로가 필요치 않다. 습기가 모재의 부식과 크리프 부식 가능성을 가속화하지만, 크리프 부식에는 흡착/응축수 층의 존재가 필요하지 않다. 크리프 부식은 ‘건조한’ 표면에서도 발생할 수 있다. 전기 바이어스 하에서 흡착/응축수 레이어가 있는 모든 표면에서 발생할 수 있는 전기화학적 마이그레이션과 달리 크리프 부식은 표면에 따라 다르며 주어진 부식 생성물은 특정 유형의 표면에서만 마이그레이션할 수 있다. 예를 들어, Ag2S는 금 표면에서 쉽게 크리핑디지만 로듐 및 팔라듐 표면에서는 크리핑되지 않는다.[17]
크리프 부식은 금속 표면에만 국한되지 않는다. IC 패키지용 플라스틱 몰딩 컴파운드에서도 관찰되었다. 이 경우 먼저 노출된 리드 프레임에서 부식이 발생하고 부식 생성물이 부품에 인접한 캡슐화 표면으로 이동하여 인접한 리드 사이의 전기적 단락을 유발하고 사용 중 제품 고장을 유발한다. Zhao[18]는 도금 이전의 금속 리드 프레임을 가지고 있는 플라스틱 갭슐화된 소형 회로에서 크리프 부식에 대해 체계적으로 검토한 결과, Telcordia Outdoor MFG 테스트가 플라스틱 몰딩 컴파운드에서의 크리프 부식을 발생시키는 데 효과적이라는 것을 알게 되었다. 5일간 진행된 Telcordia outdoor MFG 테스트를 통해 몰드 컴파운드에서 크리프 부식이 유발할 수 있었다.
이전 결과와 마찬가지로, 인쇄회로기판의 크리프 부식은 표면 특성이 매우 높고 표면 화학적 특성에 민감하다는 사실도 발견했다. 국제적인 조건에서 20일 동안 MFG에 노출된 샘플의 경우에도 깨끗한 FR-4나 솔더 마스크 표면 모두에서 크리프 부식의 징후를 보이지 않았다. 그러나 특정 유형의 오염된 표면이 존재한 FR-4 또는 솔더 마스크의 경우에는 Cu2S의 광범위한 크리프 부식이 관찰되었다. 솔더 마스크의 유기산 웨이브 솔더링 플럭스에 의해 남겨진 잔류물은 크리프 부식이 발생하는 표면을 제공한다. FR-4 표면과 유기산 플럭스 잔류물의 조합은 크리프 부식에 대해 훨씬 덜 활동적이다. 분명히 솔더 마스크 표면은 플럭스 잔류물을 흡수하는 경향이 높으며 크리프 부식이 발생할 수 있는 매우 활동적인 표면을 제공한다.
유기산 플럭스 잔류물과 달리 로진계 플럭스 잔류물은 일반적으로 크리프 부식을 촉진하지 않는다. 카르복실산 기능족(機能族)(carboxylic acid function group)이 두 유형의 플럭스에서 활성 성분임에도 불구하고 유기산 플럭스와 로진 플럭스 사이에 왜 그러한 급격한 차이가 관찰되었는지는 이 시점에서 명확하지 않다. 한 가지 가능한 설명은 유기산 플럭스와 어셈블리된 후 표면에 노출된 카르복실산 기능족의 농도가 더 높고 표면의 유리 카르복실산 기능족이 크리프 부식의 활성 사이트를 제공한다는 것이다. 로진계 플럭스의 경우 카복실산 기능족은 대부분 로진 매트릭스에 매립되어 있으며 극소량만 표면에 노출되어 크리프 부식을 지지할 수 있다. 또한, 로진의 카르복실산 그룹은 일반적으로 무거운 유기 분자에 결합되는 반면, 작고 이동성인 유기산 분자는 종종 유기산 플럭스에 존재한다. 이 차이점을 이해하기 위한 추가 작업이 진행 중이다.
크리프 부식의 메커니즘은 잘 알려져 있지 않다. 금속 표면의 크리프 부식에 관해 Conrad[19]가 갈바닉 부식 이론(galvanic corrosion theory)을 처음 제안했으며, 서로 다른 금속 간의 갈바닉 전위 차이가 크리프 부식의 원동력을 제공한다는 것이다. 이는 솔더 마스크 표면과 같은 유전체 재료의 크리프 부식에는 분명히 적용할 수 없다. 현상학적으로 말하자면, ‘크리프 가능한’ 표면을 부식 생성물 표면으로 교체하는 사이의 에너지 차이(두 표면의 표면 에너지 차이)는 부식 생성물과 ‘크리프 가능한’ 표면(계면 에너지) 사이의 상호작용 때문에 방출되는 에너지에 의해 보상되어야 한다. 미세한 의미에서 PWB에서 크리프 부식의 추진력은 아마도 구리 황화물과 플럭스 잔류물에 존재하는 카복실산 기능족 간의 상호작용 때문에 제공될 것이다.
깨끗한 FR-4 또는 솔더 마스크 표면의 경우, FR4/솔더 마스크 표면과 크리핑 황화구리 사이의 상호작용은 황화구리와 FR-4/솔더 마스크 사이의 표면 에너지 차이를 보상할 만큼 충분히 강하지 않은 것이 분명하다. 솔더 마스크에 플럭스 잔류물이 존재하면 유기산 플럭스의 카르복실산 활성 성분으로 인해 깨끗한 솔더 마스크 표면의 표면 에너지가 증가할 가능성이 크다. 또한 카르복실산은 크리핑 종(creeping species, 황화구리)과 더 강하게 상호작용하고 크리핑 부식 생성물과 ‘크리프 가능한’ 표면 사이에 상당히 높은 계면 에너지를 생성한다. 플럭스로 덮인 솔더 마스크 표면의 늘어난 표면 에너지와 크리핑 부식 생성물과 ‘크리핑 가능한’ 표면 사이의 인터페이스의 계면 에너지는 모두 자발적인 크리프 부식에 대한 열역학적 구동력을 제공할 수 있다. 크리핑 종과 ‘크리핑 가능한’ 표면 사이의 상호작용이 너무 강할 수 없다는 점을 지적하는 것도 중요하다. 그렇지 않으면 운동 효과로 인한 이 강한 상호작용 때문에 크리프 부식이 ‘제동’이 걸린다.
실험실에서의 크리프 부식 시뮬레이션은 크리프 부식의 표면에 매우 민감한 특성을 고려해야 한다. MFG 테스트는 국제적인 환경 조건 하에서 시뮬레이션할 수 있으며 이전에 전기 접점(금속 표면) 및 IC 부품(유전체 표면)에서 크리프 부식을 생성하는 데 성공적으로 사용되었다. 본 연구에서는 MFG 테스트를 통해 인쇄회로기판에서 크리프 부식을 성공적으로 재현했다. 이전의 부정합적인 PWB의 크리프 부식 생성은 크리프 부식의 표면에 매우 민감한 특성을 인식하지 못하는 데 있었다. 어셈블리 프로세스를 거치지 않고 표면 마감재와 솔더 마스크만 포함된 테스트 보드는 크리프 부식을 이해하기 위한 적절한 샘플이 아니다. 크리프 부식 방지 ImAg 또는 기타 PWB 최종 마감재를 찾는 작업은 솔더 마스크와 플럭스가 있는 어셈블리된 기판에서 수행되어야 한다. MFG 테스트는 크리프 부식에 대한 실행 가능하고 현실적인 가속 노화 테스트를 제공한다.
결론
인쇄회로기판의 크리프 부식은 표면의 화학적 특성에 매우 민감하다. 깨끗한 FR-4도 깨끗한 솔더 마스크 표면도 크리프 부식을 지원하지 않는다. 일반적으로 로진계 웨이브 솔더링 플럭스와 로진계 플럭스를 포함하는 솔더 페이스트로 조립된 보드는 크리프 부식에 대한 내성도 있다. 한편, 유기산 플럭스에 의해 솔더 마스크 표면에 남은 잔류물은 ‘크리프 가능한’ 표면을 형성하고 구리 황화물의 크리프 부식을 지원하는 데 매우 활성적이다. 어셈블리 플럭스의 적절한 선택은 부식성이 높은 글로벌 환경에서 ImAg 도금 회로 기판과 관련된 크리프 부식으로 인한 제품 고장을 제거할 수 있다. MFG를 활용한 부식 테스트는 글로벌 환경에 배치될 장비에 대한 현실적인 가속 테스트를 제공한다. 실험실에서 크리프 부식으로 인한 제품 고장을 시뮬레이션하기 위해 응축 조건이 필요없다.
REFERENCES
1. IPC, “Specification for Immersion Silver Plating for Printed Circuit Boards” IPC-4553, September 29, 2005
2. IPC, “Specification for Electroless Nickel/Immersion Gold (ENIG) Plating for Printed Circuit Boards” IPC-4552, October 2002
3. IPC, “Time, Temperature and Humidity Stress of Final Board Finish Solderability”, IPC-TR-585, May, 2006
4. R. Veale, “Reliability of PCB Alternate Surface Finishes In A Harsh Industrial Environment”, SMTA 2005
5. P. Mazurkiewicz, “Accelerated Corrosion of Printed Circuit Boards due to High Levels of Reduced Sulfur Gasses in Industrial Environments”, Proceedings of the 32nd International Symposium for Testing and Failure Analysis, November 12-16, 2006, Renaissance Austin Hotel, Austin, Texas, USA
6. C. Xu, D. Flemming, K. Demerkin, G. Derkits, J. Franey, W.Reents, “Corrosion Resistance of PWB Surface Finishes”, Alcatel-Lucent, APEX, 2007.
7. R.Schueller, “Creep Corrosion On Lead-Free Printed Circuit Boards In High Sulfur Environments” SMTA 2007
8. C. Xu, J. Yaemsiri and W. Reents, to be published
9. W. Abbott, “The Development and Performance Characteristics of Mixed Flowing Gas Environment,” IEEE Trans. Components, Hybrids, Manufacturing Technol., Vol. CHMT-11:1 (1988) 22-35.
10. ASTM International, “Standard Guide for Mixed Flowing Gas (MFG) Tests for Electrical Contacts,” ASTM B 845-97, June 10, 2003.
11. ISA-S71.04-1985, “Environmental Conditions for Process Measurement and Control Systems: Airborne Contaminants”, Instrument Society of America, 1985
12. D. Williams, “The Effect of Test Environment on the Creep of Base Metal Surface Films over Precious Metal Inlays,” IEEE Trans. Components, Hybrids, Manufacturing, Vol. CHMT-11:1 (1988)36-42.
13. Telcordia GR-63-CORE Issue 2, Section 5.5, “Airborne Contaminants Test Methods”, Nov. 2000.
14. Corrosion, Vol. 55, No. 1, page 66. –1999
15. Lucent Technologies corrosion taskforce: Coupons deployed at beginning of 1999
16. G.E. Derkits, J.P. Franey and W.D. Reents, “Biased Mixed Flowing Gas Testing for World Class reliability”, Bell Labs Technical Journal, 11(3), 105-120, 2006.
17. T. F. Egan and A. Mendizza, “Creeping Silver Sulfide”, Journal Of The Electrochemical Society, Vol 107 (4), 353, (1960)
18. P. Zhao “ Creep Corrosion Over Plastic Encapsulated Microcircuit Packages With Noble Metal Pre-Plated Leadframes”, Ph.D. Dissertation, 2005, University of Maryland
19. Conrad, L.R., Pike-Biegunski, M.J., Freed, R.L, “Creep Corrosion over Gold, Palladium, and Tin-l