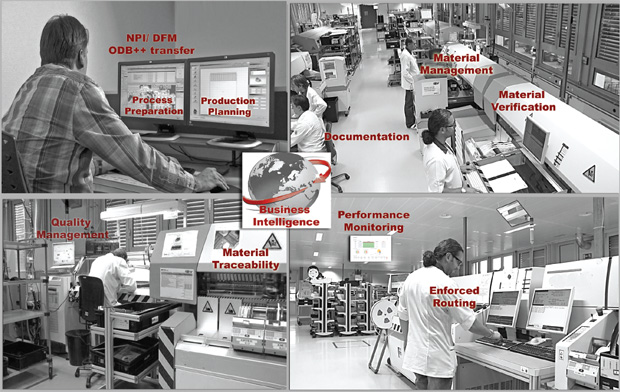
여러 제조업체의 SMT 머신이 한 라인에 혼재되어 운영되는 경우에는 머신 라이브러리 중복 관리가 매우 번거로운 일이 아닐 수 없다. 또한 이러한 중복 관리되는 머신 라이브러리를 이용하여 생산 모델마다 프로그램을 작성하고, 작성된 프로그램의 각 부품 정보가 올바른 형상과 정확한 중심점 및 각도를 갖고 있는지를 일일이 확인하고 디버깅하여야 한다.
- 연재순서
1. Mentor MSS Process Preparation - Global 표준 준비단계 통합 솔루션
2. Mentor MSS Asset Utilization - Global 표준 자원관리 통합 솔루션
3. Mentor MSS Material Verification - Global 표준 부품 실장 검증 통합 솔루션
4. Mentor MSS Material Traceability - Global 표준 부품 추적관리 통합 솔루션
5. Mentor MSS Material Management - Global 표준 부품 관리 통합 솔루션
6. Mentor MSS Quality Management - Global 표준 품질 관리 통합 솔루션
SMT 장비 프로그램 자동화 솔루션, Mentor MSS Process Preparation(MSS-PP)
제품개요
신제품 생산을 위한 SMT 머신 프로그램 출력 과정은 여러 단순 과정을 반복적으로 거치게 됨으로써 많은 개선과 시스템화가 요구되는 부분이다. 이 때문에 최근 많은 자동화 프로그램들이 이용되고 있으나 근본적으로 SMT 머신 라이브러리가 통합되지 않고서는 더 이상의 자동화를 기대하기는 어렵다.
현재의 공정에서는 프로그램을 만들기 위한 가장 기본적인 요소인 SMT 머신 라이브러리를 각 SMT 제조업체 별로 만들고 관리하여야 한다.
여러 제조업체의 SMT 머신이 한 라인에 혼재되어 운영되는 경우에는 머신 라이브러리 중복 관리가 매우 번거로운 일이 아닐 수 없다. 또한 이러한 중복 관리되는 머신 라이브러리를 이용하여 생산 모델마다 프로그램을 작성하고, 작성된 프로그램의 각 부품 정보가 올바른 형상과 정확한 중심점 및 각도를 갖고 있는지를 일일이 확인하고 디버깅하여야 한다.
MSS-PP 모듈은 SMT 머신 라이브러리 통합화를 바탕으로 생산 준비에 필요한 여러 과정을 시스템화하고 최적화된 프로그램을 자동 출력하여 줌으로써 신제품 생산을 위한 준비 과정을 대폭 단축시킬 수 있는 제품이다.
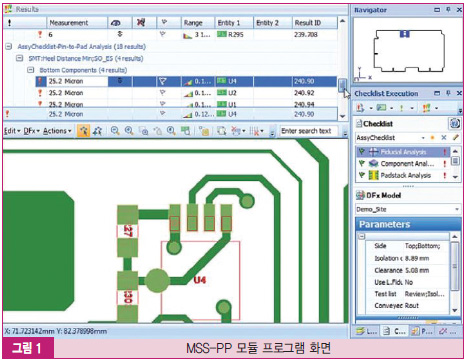
주요기능 및 이점
▶ 한 번의 시도로 신제품 생산 준비
▶ 머신프로그램(NC 프로그램), 전장검사항목, 일반검사항목
준비시간 최소화
▶ 전장검사기 비용 절감
▶ 생산성 향상
▶ 효율적인 생산환경 (라인 밸런스, 전체라인밸런스)
▶ 장비 활용률 증대 - 유휴 장비 및 시간 감소
▶ 내·외부 고객간의 소통 증대
▶ 준비시간 단축
▶ 재고 활용률 증대
▶ 추가로 머신 라이브러리 생성 필요 없음
머신 라이브러리 통합에 의한 NC 프로그램 자동출력
Global 생산기지 보유기업 및 협력사를 통한 생산을 하는 회사들이 그 생산기지 또는 협력사의 기술력 차이에 따라 제품의 품질의 차이가 좌우 되지 않도록 시스템에 의한 안정화를 위해 많은 노력을 해 왔으며 현재도 적절한 솔루션을 찾고 있다. 특히 전장품 제조社의 경우 동일한 사업장이라 하더라도 공정에 여러 제조 회사의 SMT 장비가 동일 라인에 혼재되어 운영 되는 등 머신 라이브러리의 중복 관리로 인해 어려움을 겪고 있다.
Mentor Graphics의 MSS-PP 모듈은 SMT 머신 라이브러리를 통합하여 SMT준비시간 최소화, 최적화 할 수 있는 솔루션이다.
설계 데이터 입력
현재 대부분의 생산에서는 NC 프로그램을 만들기 위한 도면 데이터는 PCB CAD 작업을 마친 후에 출력되는 Gerber 데이터를 받아서 생산 모델을 정의하고 있다. 즉, Gerber 데이터와 이와 관련된 부품의 X, Y 좌표 정보를 이용하여 PCB층 정의, 원점(Origin) 좌표 설정, PCB 외곽 라인 정의, 각 부품의 X, Y 좌표 설정 및 각도 정렬 등의 작업을 하게 된다. 이러한 작업은 이미 CAD 설계 시에 모두 진행된 작업으로서 CAD 파일에 모두 포함 되어 있는 데이터들이다. 이것을 생산에서 중복하여 만들고 있는 것이다. 그 이유는 그 동안 효과적으로 CAD 정보를 이용할 수 있는 프로그램이 없었기 때문이다.
이미 생산에서 효과적으로 사용할 수 있는 ODB++ 포맷이 10여 년 전부터 Valor社에 의해 출시되었고 세계적인 표준 협회인 IPC에서 공인되었다. 그러나 많은 PCB 제조업체에서 이미 널리 이용되고 있었음에도 불구하고 PBA 생산에서는 아직도 Gerber data를 이용하여 중복 작업을 반복적으로 계속하고 있다.
본 제품은 현재와 같이 Gerber 데이터를 이용할 수도 있지만 ODB++와 같은 효율적인 데이터를 이용할 수 있으므로 이를 권장하여 불필요한 중복 작업을 없애도록 권장하고 있다. 하지만 아직도 많은 업체에서는 Gerber 데이터를 이용하고 있으므로 이에 대한 효과를 최대한 높이기 위하여 ‘Gerber Re-engineering’ 기능을 이용하여 Gerber 데이터와 부품 좌표 정보를 일치 정렬시킨 후 부품 패드 정보를 역으로 추출할 수 있도록 하였다. 이와 같이 본 제품에서는 Gerber 데이터나 CAD 데이터, 또는 ODB++ 데이터 등 어떠한 형태의 데이터라도 읽어 들여 시스템화할 수 있다.
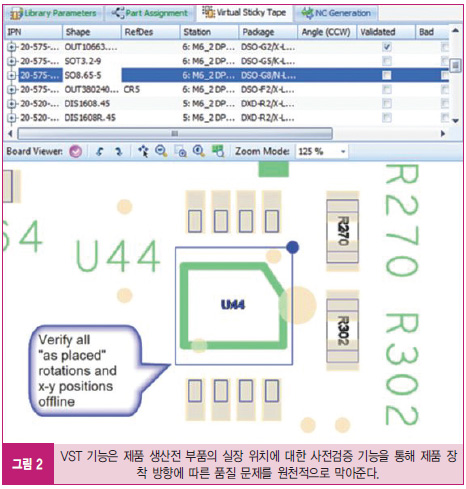
BOM 데이터 입력
본 제품은 사용자의 BOM(Bill of Material)에 있는 여러 정보 중에서 생산에서 필요한 정보 만을 자동 정리하도록 초기에 한번 설정함으로써 이후에는 사용자의 BOM을 읽어 필요한 정보만을 자동 정리하여 활용하게 된다. 또한 BOM에서 나타나는 문제점을 자동으로 표시해 줌으로써 쉽게 BOM 오류를 확인하고 수정할 수 있다. 즉 중복 부품, 누락 부품, CAD에는 있으나 BOM에는 없는 부품, CAD에는 없으나 BOM에 있는 부품, BOM이 개정되면서 발생하는 차이 등을 한눈에 표시하여 줌으로써 BOM 작업 시에 작업자의 실수에 의해 발생한 오류를 바로 확인하고 수정할 수 있다.
VPL 입력 및 DFM
부품 형상 라이브러리인 VPL(Valor Part Library)을 BOM에 있는 부품 제조사명과 부품번호를 기준으로 Valor사에 의해 구축된 VPL 서버에서 찾아내어 불러오고 이미 전 단계에서 읽어 들인 설계 데이터의 각 부품 X, Y 좌표를 통해 정확한 위치에 부품 형상 라이브러리를 올려놓는다.
VPL 기능은 세계적으로 이용되는 4000만개 이상의 부품 라이브러리가 등록되어 있으며, 이러한 부품 형상 라이브러리가 설계 도면의 부품 패드 위에 올려짐으로써 설계에서 그려진 부품 라이브러리의 패드가 실제 부품 핀에 적합하게 설계 되었는지 또는 부품 패드 위의 부품 핀이 생산 규격에 맞게 솔더링 되는지, 실제 여러 타입의 부품과 부품간의 간격이 생산 규격에 위배되지 않는지 등의 여러 가지 생산성 검증을 사전에 할 수 있다.
여기서 문제가 발견되면 그 부분에 대한 그래픽과 함께 HTML 리포트로 정리하여 설계 담당자에게 이 메일로 보내어 설계를 수정하도록 한다. 이와 같이 사전 제조 검증을 DFM(Design for Manufacture)이라고 하며 생산 불량 요인을 사전에 방지하여 불필요한 개정을 사전에 막을 수 있도록 한다. 이러한 DFM 솔루션은 R&D 에서 설계 후에 주로 적용하였으나 최근에는 더욱 철저한 사전 검증을 위해 제조현장에 적용을 하고 있는 추세이다. 이러한 과정을 통해 제조에 문제가 없는 가상 PBA를 완성하여 DB화한다.
완성된 PBA는 실제 라인에 투입될 수 있는 어레이 보드(Array Board)로 만들 수 있으며 이를 프로젝트화 한다. 본 제품에서는 생산 모델을 PCB(부품 실장 전의 보드), PBA(부품이 실장된 단일 보드), 어레이 보드(부품이 실장된 연배열 보드)로 DB 화하여 향후 부품 일부 변경에 의한 ECO에서는 기존의 PCB에 서 새로운 PBA를 만들고, 어레이 변경에 의한 ECO에서는 기존의 PBA를 다시 어레이하여 새로운 프로젝트를 만들어 냄으로써 ECO에 신속히 대응할 수 있다.
가상생산라인 구성
사용자의 라인과 동일한 가상 SMT 라인을 시스템 상에 구축한다. 이러한 가상 라인은 실제의 SMT 머신 모델과 동일하게 구성하고 각 SMT 머신이 갖고 있는 동일한 환경을 설정하게 된다. 이러한 가상 라인은 공장의 모든 라인을 구성할 수 있을 뿐 아니라 해외의 모든 생산 라인까지도 구축하여 놓음으로써 한번 출력된 생산 모델에 대한 최적화된 NC 프로그램을 세계 어느 라인에서도 프로그램을 자동 변환하여 바로 이용할 수 있다. 즉, 본 제품에 의해 프로젝트화된 생산 모델을 원하는 라인에 적용하여 원하는 최종 NC 프로그램을 자동 출력하거나 이미 사용 중인 프로그램을 새로운 라인의 프로그램으로 자동 변환하여 즉시 이용할 수 있도록 한다.
머신 라이브러리 자동 생성
생산 모델에 대한 라인의 모든 SMT 머신 NC 프로그램을 다른 라인의 모든 SMT 머신 NC 프로그램으로 자동 변환시키기 위해서는 SMT 머신 간 NC 프로그램 자동 변환이 가능하여야 한다. 또한 SMT 머신 간 NC 프로그램 변환이 가능하기 위해서는 각 SMT 장비에 대한 머신 라이브러리가 자동 지원되어야 한다.
세계 유명 SMT 장비 업체들과의 파트너 계약을 통하여 많은 SMT 장비 모델들을 지원하고 있다. 이로 인해 부품 형상 정보를 해당 SMT 머신이 인식할 수 있는 포맷으로 자동 변환하게 된다. 더욱 상세한 사용자 머신 사양에 맞추기 위해 각 머신 별로 상세 사양을 정의할 수 있는 머신 라이브러리 자동 생성 테이블을 제공하며 여기에 사용자가 개별적으로 운용하는 사양을 사용자 임의로 정의하여 실제 생산 라인의 환경과 정확히 일치하는 환경을 구축할 수 있게 한다.
많은 조건 설정 항목이 있겠으나 하나의 예로써 특정 부품의 노즐 픽업 위치를 정의하는 높이 값(t)을 사용자 임의로 정의토록 하여 기본 설정 값 이외의 조건으로 노즐의 픽업 위치를 조절할 수 있도록 한다. 이와 더불어 각 부품 라이브러리 정보에 부품이 공급되는 형태 정보를 함께 정의하여 올바른 피더(Feeder)가 자동 선택되도록 한다. 즉, 부품 공급 형태가 트레이(Tray) 방식인지 릴(Reel) 방식인지를 구분하고 릴 방식의 경우 몇 mm 릴에 공급되는지를 함께 정의한다.
이와 같은 머신 라이브러리 정보는 기존에 사용하고 있는 머신 라이브러리를 그대로 이용할 수 있고 Mentor社에서 제공하는 VPL 서비스를 받아서 이용할 수도 있으며 제품에서 제공하는 VLM을 이용하여 쉽게 만들어 사용할 수도 있다. 중요한 것은 기 확보된 머신 라이브러리는 앞으로 여러 머신에서 각각 별도로 구축할 필요 없이 통합적으로 이용할 수 있으므로 번거로운 중복 작업을 피할 수 있다는 것이다. 이로 인해 이종 장비간의 NC 프로그램 자동 변환과 더 나아가 라인과 라인간의 프로그램 자동 변환까지 가능하게 된다. 따라서 글로벌 환경에 맞게 세계 어느 공장의 어느 라인에서도 하나의 NC 프로그램으로 생산이 가능하다. 물론 이를 위해서는 사용 중인 SMT 장비와 제품 간의 호완성이 필요 하지만 주요 회사들의 장비는 모두 지원이 가능하다.
제품운영을 통해 확보된 머신 라이브러리는 앞으로 여러 장비 에서 각각 별도로 구축할 필요 없이 통합적으로 이용할 수 있으므로 번거로운 중복 작업을 피할 수 있다. 이로 인해 장비와 장비간의 NC 프로그램 자동 변환과 더 나아가 라인과 라인간의 프로그램 자동 변환 까지 가능하게 된다. 따라서 글로벌환 경에 맞게 세계 어느 공장의 어느 라인에서도 하나의 NC 프로그램으로 생산이 가능하다.
생산 공정 정의
생산 공정에는 SMT 공정과 자삽 공정, 매뉴얼 공정 등과 같이 부품의 종류에 따른 공정 분류가 필요하다. 신규 부품에 대해 부품 타입 별 공정 분류를 하여 저장함으로써 향후 해당 부품들은 공정에 따라 자동 분류가 되게 된다. 또한 이에 따른 작업 지도서가 자동 출력될 수 있도록 초기에 사용자가 이용하는 작업 지도서 형태를 구성할 수 있게 한다. 필요에 따라서는 각 부품 타입에 따른 스텐실 규격을 부품마다 등록하여 놓음으로써 스텐실을 자동 출력하고 편집할 수 있다.
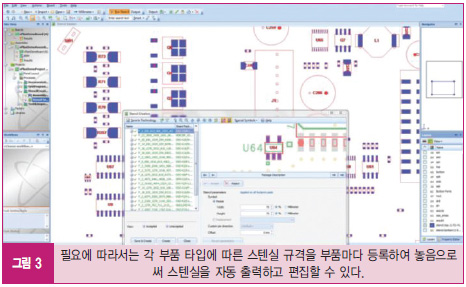
최적화된 NC 프로그램 자동출력
SMT 공정으로 분류된 부품들에 대해서는 해당 라인의 생산 흐름에 병목 현상이 발생하지 않도록 각 SMT 머신 간 라인 밸런싱(Line Balancing)을 자동 처리한다. 이때 사용자가 갖고 있는 특정 조건이 있는 경우, 이에 대한 사용자 조건을 특별히 설정할 수 있으므로 이를 우선 반영하여 라인 밸런싱을 하도록 한다. 경우에 따라 여러 모델을 생산하여야 하는 사용자를 위하여 유사 모델끼리 그룹화하여 동시 생산함으로써 모델 변경에 소요되는 시간을 최소화할 수도 있다. 이것을 그룹핑(Grouping)이라고 한다.
가장 기본적으로는 각 SMT 장비에 대한 피더 배열 및 부품 실장 순서를 효과적으로 하여 부품 실장 시간을 단축시키는 최적화 기능을 이용하게 된다. 이를 통해 생산 시간을 단축하여 라인 가동률을 증가시키고 라인 투자 효과를 극대화시킬 수 있다. 또한 최적화된 NC 프로그램의 결과에 대한 SMT 머신 별 피더 세팅 테이블이 자동 출력되기 때문에 사용자는 각 SMT 머신 별로 출력된 피더 세팅 테이블에 따라 피더를 세팅하고 최적화된 NC 프로그램을 SMT 장비에 입력한 후 바로 생산을 시작할 수 있다.
오프라인에 의한 NC 프로그램 검증
현재 신제품을 생산하기 위해서는 생산 모델의 각 부품의 정확한 형상이 올바른 위치와 각도로 위치해 있는지를 육안으로 하나씩 확인하여야 하기 때문에 매우 세심한 주의가 필요할 뿐 아니라 이에 대한 최종 검증을 위해서 실제 라인에서 디버깅을 하여야 한다. 이것은 생산에 이용되어야 할 실제 라인의 가동률을 저해시키는 요인이 된다. 이에 대한 검증을 시스템적으로 간단히 확인하여 잘못된 부품 형태 및 각도와 부정확한 위치에 놓인 부품에 대한 수정을 손쉽게 처리하게 한다.
과거 이러한 작업은 양면 테이프로 부품을 도면에 일일이 붙여서 확인하였기 때문에 유럽 및 미국에서는 일반적으로 스티키 테이프(Sticky Tape) 작업이라고 하는데 본 제품에서는 이와 같은 부품의 형상, 각도, 위치 검증 기능을 자동 시스템화하였다. 이를 VST(Virtual Sticky Tape : 가상 스티키 테이프)라고 칭한다. 설명한 바와 같이 VST 작업에 따라 생산에 부적절한 부품을 올바르게 수정하여 업데이트하면 해당 부품은 다음부터 항상 수정된 형태로 이용되게 되므로 다음 신규 모델 생산 에서는 추가된 신규 부품만 이러한 검증 확인이 필요하게 된다. 이와 같이 부품에 대한 검증 및 디버깅은 실제 라인이 아닌 가상 모델과 가상 라인에서 모두 이루어지기 때문에 실제 라인을 이용한 디버깅이 필요 없게 되고 실제 라인에서는 생산에 주력할 수 있으므로 라인 가동률을 더욱 높일 수 있다.