본고에서는 무연 솔더 접합부 내의 크랙을 연구하기 위해 적용되는 많은 기술들의 적합성을 조사하여 설명하고, 그런 후에 이들을 이용하여 접합부의 수명을 추정해 본다. 크랙은 FR-4 서브스트레이트 위의 칩 레지스터의 솔더 접합부 내에서 나타나도록 하였고, 금속 Micro-sectioning, Dye penetration, 기계적 테스트 및 열 전도 기술들을 적용하여 연구하였다. Pb 기반 솔더 접합부를 연구하는 전통적인 이 기술들이 무연 솔더 접합부를 평가하는데도 손쉽게 적용될 수 있음을 본 연구에서 보여주고 있다.
서문
본고에서는 무연 솔더 접합부 내의 크랙을 연구하기 위해 적용되는 많은 기술들의 적합성을 조사하여 설명하고, 그런 후에 이들을 이용하여 접합부의 수명을 추정해 본다. 크랙은 FR-4 서브스트레이트 위의 칩 레지스터의 솔더 접합부 내에서 나타나도록 하였고, 금속 Micro-sectioning, Dye penetration, 기계적 테스트 및 열 전도 기술들을 적용하여 연구하였다. Pb 기반 솔더 접합부를 연구하는 전통적인 이 기술들이 무연 솔더 접합부를 평가하는데도 손쉽게 적용될 수 있음을 본 연구에서 보여주고 있다. 전통적인 Micro-sectioning 방법은 솔더 접합부 크랙을 찾아내고, 이미지화하는데 적합했는데 특히, SEM 내에서 섹션을 검사할 때 더욱 그러했다. 그러나 크랙의 정량분석(定量分析) 혹은 소형 표면실장형 레지스트 내의 자체 검출에 있어서는 매우 적합하지 않았다. Dye penetration 기술은 수평면 내에서 크랙의 더 좋은 특성 검출을 가능하게 하고, 크랙된 표면 부분의 정량적인 측정을 제공할 수 있다. Shear testing은 크랙 확대의 정도 및 솔더 접합부의 피해뿐만 아니라 접합부의 일반적인 강도까지 평가하는 증명된 파괴 방법이다. 다른 방법들(3/4점 굽힘 테스트, 인장 테스트 및 열 전송)은 엄격하게 제한되었고, 전자산업계 어셈블리의 솔더 접합부 내의 크랙을 연구하기에는 현재 부적합하다.
서론
전자산업계 어셈블리의 경우, 부품과 서브스트레이트가 솔더링 프로세스를 거쳐 기계적 및 전기적으로 상호접속한다. 솔더 접합부가 어셈블리 내에서 가장 취약한 지점으로, 어셈블리의 수명을 결정한다. 그래서 전자산업계의 어셈블리 수명 평가는 혹독한 노력 혹은 가혹한 조건 하에서 솔더 접합부의 열화(degradation)를 관찰함으로써 주로 실시되었다. 이러한 접합부의 수명 평가도 바람직하지만 우수한 프로세스 컨트롤을 유지하고 성취하기 위해 꼭 필요한 것은 아니다. 특히, 고신뢰성의 애플리케이션에서 그렇다. 전통적인 SnPb 솔더 접합부을 연구하기 위해 이용된 여러 가지 측정 기술들이 있으며, 이들을 이용하여 무연 솔더 접합부의 수명 관련 데이터를 제공하는데 잠재적으로 적합하다. 솔더 접합부의 기계적인 연구와 관련한 이전의 보고서에서는, 접합부의 기계적인 불량이 갑자기 파멸적인 형태로 대두되지 않고, 일반적인 크랙 형태의 점진적인 변화로 발생한다고 증명했었다. 2512-타입 칩 레지스터의 전형적인 솔더 접합부의 크랙은 그림 1에서 보여주고 있다.
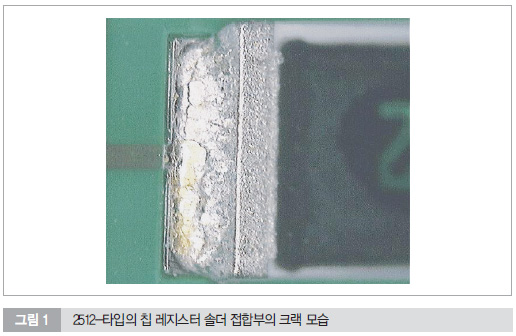
본고에서는 무연 솔더 접합부 내의 크랙을 연구하기 위한 다양한 기술들의 적합성을 조사하였고, 접합부의 수명을 평가하는데 있어서 이들을 이용하였다. Micro-sectioning, Dye penetration, 기계적 테스트 및 열 전도 등의 기술들을 포함하였다. 적합한 FEA 분석은 다양한 테스트 평가에 도움을 준다고 단언한다.
테스트 시편
어셈블리에서 FR-4 laminate에 납땜된 경성 세라믹 몸체의 커다란 부품이 포함될 때, 솔더 접합부의 강도는 특히 영향을 받았다. 결과적으로, 이 ‘최악의 경우’ 시나리오를 실험하기 위해서 2512-타입 칩 레지스터와 ENIG(immersion gold over electroless nickel) 마감처리된 FR-4 서브스트레이트를 이 연구에 이용하였다. 일반적으로 널리 사용되고 있는 무연 솔더페이스트를 이용하였다. 그림 2에서 보이는 바와 같이, 이용한 PCB 어셈블리는 35㎛의 copper 두께 및 ENIG 마감재가 처리된 단면 FR-4 보드(1.6㎜ 두께)로 제작되었다.
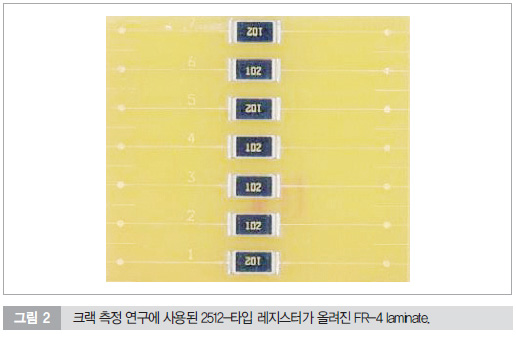
150㎛ 두께의 스테인리스-강 스텐실을 적용하여 솔더 페이스트를 서브스트레이트에 스텐실 프린트하였다. 부품들은 전자동 실장기로 서브스트레이트 위에 놓았고, 무연 솔더 페이스트는 비세척 95.5Sn3.8Ag0.7Cu 및 96.5Sn3.5Ag 조성의 제품이 이용하였다. 이러한 프로세스들은 접합부에 일관성 있는 솔더 체적을 보장했다. 솔더 페이스트의 리플로우는 대류 리플로우 오븐을 이용하였고, 리플로우 온도 프로파일은 권장사항을 준수하였다.
열 사이클링
크랙은 특정 솔더 합금의 궁극적인 전단 응력(shear stress)을 초과하는 응력(應力)에 의해 기인하는데, 솔더 접합부 내에서 발생하는 크랙을 촉진하는 전통적인 촉진 방법은 그 기간의 열 사이클링 유형에 어셈블리를 적용하는 것이다. 국부적인 응력은 재질의 미스-배치에 의해서나 혹은 온도 변화에 노출된 2개 접합물질의 CTE(coefficients of thermal expansion)의 불일치에 의해서 기계적으로 발생할 수 있다. 본고에 사용된 전자기기 어셈블리의 경우, 부품 몸체(알루미나 6.5ppm/℃), 솔더(21~25ppm/℃), 동박 터미네이션 패드(17.6ppm/℃)와 FR-4 적층판(CTExy = 12~18ppm/℃, CTEz = 50ppm/℃) 사이에서 CTE가 불일치되었다. 게다가 모든 이들 계수는 온도에 의해 변했다. 가장 긴 절대치수의 가장 큰 불일치는 부품 몸체와 FR-4 적층판 사이이다. 본고에서 측정에 사용된 열 사이클링 영역의 파라미터는 표 1에서 보여주고 있으며, 그림 3에서는 열 사이클의 그래픽을 나타내고 있다.
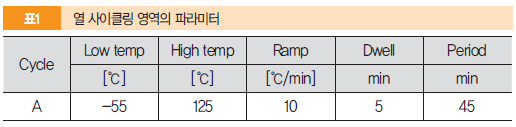
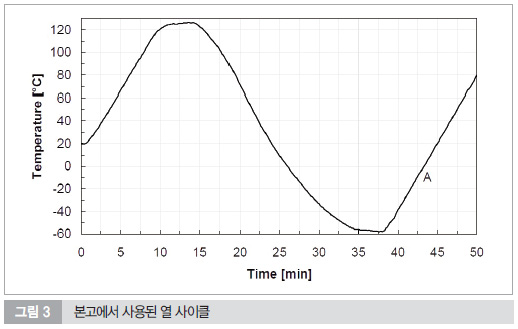
이 열 사이클링 테스트 영역은 넓은 온도 범위의 사이클로 여겨지는 군수용품 테스트에 폭 넓게 적용되고 있다. 10℃/min의 상승 비율은 전통적으로 30℃/min 이상인 열 충격 영역보다 느린 적당한 상승 비율이다. 상대적으로 짧은 5분의 상주 시간(dwell time)은 사이클 영역을 최소화할 것이고, 테스트 영역을 단축할 것이다.
Micro-sectioning
접합부 미세구조와 발생된 특정한 모든 크랙을 연구하기 위해 접합부의 microsection 조사가 필수적이다.
결과적으로, 부품 및 서브스트레이트의 어셈블리는 추가적인 특정한 응력원인을 회피하기 위해서 저속 시편절단기를 이용해 예비-절단되었다. 그리고 이들 예비-절단 시편은 솔더 접합을 보호하고, 캡슐화하기 위해 냉연용 경화 에폭시 수지 금형(cold curing epoxy resin mould)으로 마운트했다. 시편은 실리콘 카바이드 페이퍼(grades of silicon carbide papers, 120~4,000 석질)를 이용하여 연마되었다. 그 다음 직경 내에서 15~0.25㎛의 일련의 파티클 사이즈를 지닌 다이아몬드 페이스트/스프레이를 이용하여 폴리싱되었다. 솔더, 동박 패드, 특정 층간 존재, 부품의 가장자리들의 경도가 다르기 때문에 폴리싱 동안 약한 압력만 적용하는 것을 보장하도록 주의를 기울였다. 폴리싱 천의 다이아몬드 함유는 최적의 절단 비율을 보장하기 위해 최대로 유지하였다. 시편의 최종 폴리싱은 랩핑액(OP-S) 내에 떠 있는 감마 알루미나이드 파우더를 이용하여 수작업으로 실행되었다.
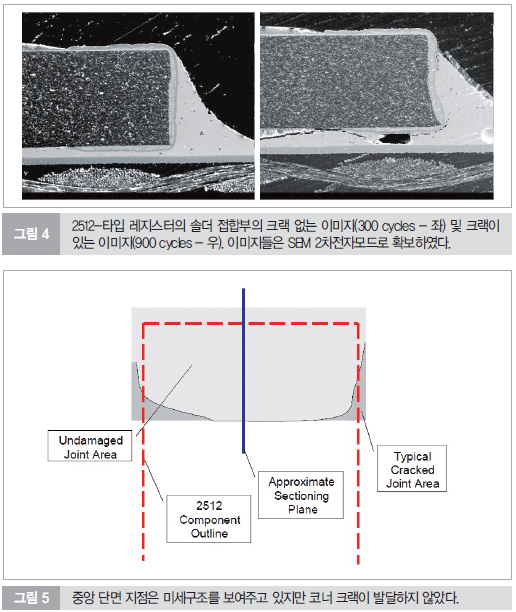
샘플의 에칭이 요구될 때, 다음의 과정으로 진행되었다;
납 기반 솔더 : polishing medium으로써 0.25㎛ 다이아몬드 페이스트가 함유된 polish-etch technique 내에 2㎖ 질산 및 98㎖ IMS(industrial methylated spirits)가 포함된 솔루션.
무연 솔더 : polishing medium으로써 0.25㎛ 다이아몬드 페이스트가 함유된 polish-etch technique 내에 2㎖ 질산, 2㎖ 염산 및 96㎖ 증류수. 매우 짧은 polish cycle(2sec)로 만족스러운 결과를 위해 증류수에 즉시 시편을 세척한 다음에 적용하였다.
접합부 미세구조의 만족할만한 이미지들은 광학 현미경을 이용하여 얻었다. 반면, 솔더 접합부의 크랙은 SEM의 2차전자 모드(secondary electron mode)를 이용하여 일반적으로 더 좋게 위치시켰다. 그러나 SEM 기술에는 전체 시편에 걸친 전도성 코팅(AuPd 혹은 카본)을 요구한다. 폴리싱의 레벨은 질량 혹은 질량분석에 매우 적합한 SEM의 후방산란반사 모드(SEM back-scattered electron mode) 내에서 시편을 평가함으로써 최소화되었다. ‘digimap’이라고 불리는 이 기술은 코팅 및 박판이 적용되는 애플리케이션을 이용할 때 또한 도움을 준다.
마이크로-섹셔닝 기술이 불량 모드의 평가에 적합하지만, 솔더 접합부 내 크랙 성장의 정량 분석에 대한 오해의 소지가 있다는 것을 주의해야만 한다. 이를 그림 5에 도식화했다. 전자부품의 가장자리 사이의 중앙 평면을 참조하여 크랙이 발생한 접합 부분의 위치를 보여주고 있다. 종단면에 나중에 나타난다면, 크랙이 발생한 부분은 마이크로섹션에서도 볼 수 없을 것이다. 따라서 종단면 크랙 검출을 보장하기 위해서 부품의 아웃라인과 근접해야만 한다. 불행히도 0805-타입 레지스터와 같은 작은 부품 사이즈는 원하는 데이터를 얻기가 어려울 것이다.
Dye Penetration
Dye Penetration은 크랙 너비와 위치를 연구하는데 사용되는 또 다른 파괴 기법이다. 본 고에서 Dye penetration 테스트는 열 사이클링 이후 2512-타입 레지스터로 실행되었다. 어셈블리는 물 50%, 이소프로필알코올(iso-propyl alcohol) 50% 용액의 초음파 통에서 어셈블리가 세척되었다. 콤프레셔 에어를 이용해 어셈블리를 건조한 후, 진공 벨에 넣고 Rocol Layout Ink Fluid(red 혹은 blue) 염료에 적셨다. 부분 진공에 15분을 적용했다. 염료는 50℃의 컨벡션 오븐에서 10분 동안 구워지는 어셈블리에서 경화되었다. 그런 후에 전자부품은 집게로 비틀어 제거되었고, 광학 현미경을 이용하여 접합의 dye penetration을 검사하였다. 전형적인 이미지는 그림 6에서 보여주고 있으며, 흰색선이 크랙이 나타난 부분이다.
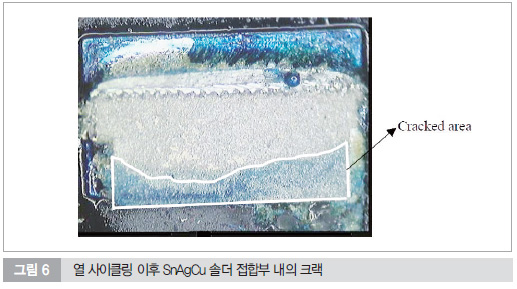
여러 번의 사이클 동안 크랙이 발생한 부분의 성장은 이미지의 해당부분에 픽셀의 수를 측정함으로써 평가하였고, 그 결과를 그림 7에 나타냈다. 이 방법은 마이크로-섹션닝 방법보다 더 나은 정량적 분석 결과를 제공하기 때문에 크랙이 없는 부분 평가 즉, 솔더 접합부의 응력을 연구하고 전체 크랙 부분을 분석하기 위해 이용될 수 있다. 마이크로-섹셔닝의 경우와 같이 종단면의 포지셔닝에 의존하지 않는다.
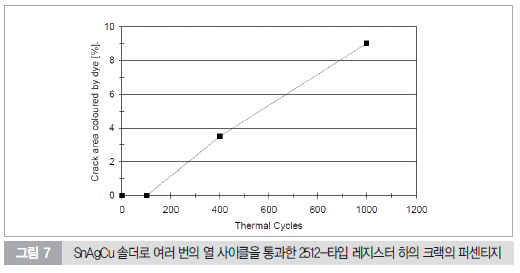
Mechanical Tests
Mechanical test는 외부 적층에 노출될 때 솔더의 시간에 따른 변형을 조사하기 위해 이용하였다. 테스트는 FR-4 기판에 솔더된 표면실장형 레지스터에서 실행되었고, 측정은 0, 300, 600, 900 및 1200 사이클 이후에 실시되었다. 사용된 테스트 시료 및 재료의 구성은 그림 8에서 개략적으로 보여주고 있다.
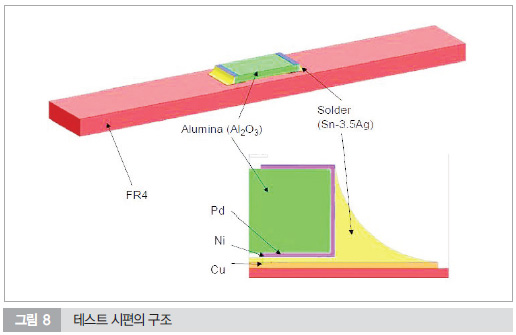
Shear Test
Shear 테스트는 크랙 확대의 정도와 솔더 접합의 피해뿐만 아니라 일반적인 접합부의 강도를 평가하는 설정된 파괴 방법이다. 방법은 솔더 접합부 내 크랙의 존재, 사이즈 및 확대의 너비가 접합의 강도에 영향을 미칠 것이라는 추측에 기반하였다. 따라서 상호작용이 솔더 접합부의 강도와 접합 실패 사이에서 정해질 수 있다. 전형적인 shear test 셋업은 그림 9에 나타냈다. 본고 내에서 테스트는 모듈러 다기능 본드-테스트로 시작하였다.
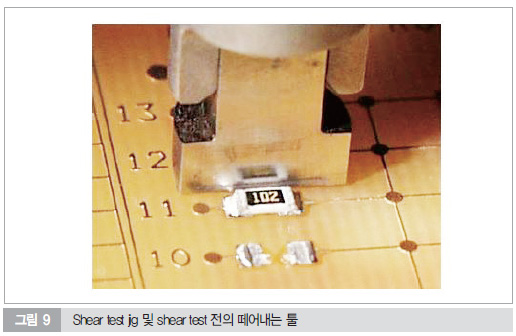
다음의 단계를 거쳐 실행되었다:
▶ 보드에 최소한의 스트레스를 주면서 깨끗한 가장자리를 만드는 수냉, 저속 다이아몬드 전기톱을 이용한 shear tester 보유 지그에 적합한 부분으로 기판이 절단되었다.
▶ 섹션은 절단 단계에서의 특정 오염 잔사를 제거하기 위해 세척되었고(이소프로필알코올을 이용하여), 컴프레셔된 공기로 건조시켰다.
▶ 스탠드-오프 높이는 절단 툴의 바닥면과 보드 표면 사이가 h/2(일반적으로 80㎛)로 설정되었다(h는 전자부품 및 보드 표면 사이의 스탠드-오프 높이다). 이것이 가장 중요한 테스트 조건이다.
▶ 각 테스트, 절단 툴이 테스트용 전자부품에 정의된 속도(200㎛/s)로 앞으로 이동하는 동안 접촉면이 깨질 때까지 적용하는 힘을 가했다.
본 테스트에서 얻은 데이터는 솔더 접합부 단절에서 요구되는 궁극적인 절단력의 항목이 분석되었다. 그런 후에 어셈블리를 실시했던 많은 열 사이클의 기능으로써 구분되었다. 평균값은 26개 개별적인 항목에서 추출하였고, 그림 10에서 나타내는 박스-휘스커 다이어그램의 1/4 및 3/4에 함께 꾸몄다.
특정한 수의 사이클에 도달한 이후 측정된 궁극적인 절단력의 분배를 박스-휘스커 다이어그램이 보여주고 있다. 테스트가 규정된 사이클 수 이후에 실행되었더라도 다이어그램에 표시된 박스의 위치는 데이터의 오버레이를 위해 계획된 사이클 수 언저리에서 측면 방향으로 이동되었다. 박스의 상면과 바닥면은 개체군 샘플의 Q1, Q3 값을 표시하고 있다. 박스에 그려진 선은 Q2의 표시이다. 이들 박스에서 수직 선(휘스커)은 제한 범위 내에서 최종 데이터 포인트로 확대되었다. 최상 및 최하 수치는 다음의 관계에 따라 측정되었다.
Lower Limit: Q1 - 1.5 (Q3 - Q1),
Upper Limit: Q3 + 1.5 (Q3 - Q1)
원은 개체군을 의미하고, 별 모양(*)은 아웃라이어(outlier)이다.
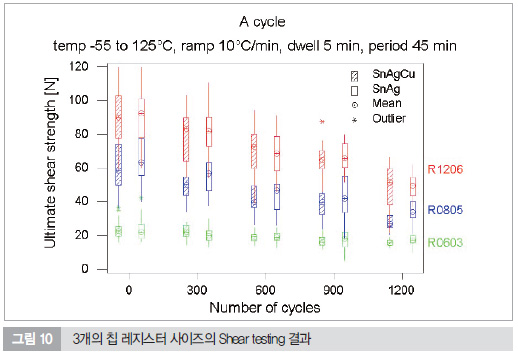
Pull Test
100N의 지속적인 임의의 인장 테스트(그림 11 참조)는 3.3N/sec 비율에서 20초 이상 적용하였고, 60초(그림 14) 동안 잡았다. 변형은 레지스터의 상위 부분에 실장된 스트레인 게이지(그림 12 참조)를 이용하여 측정했다. 그림 13은 FEA 소프트웨어 툴 PHYSICA를 이용하여 측정한 레지스터-기판 시스템의 초기 변형 모드를 도식화하였다.
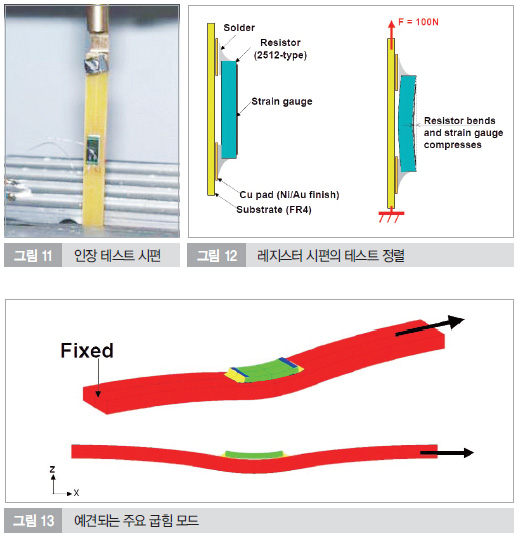
분석에서는 솔더 접합부 무결성이 열화 위상을 통해 진행되는 것을 나타내고 있다. 그리고 레지스터의 상부는 수 많은 사이클 이후 더 작은 압축 응력을 받게 된다.
그림 14에서 보여주듯이 시간에 따른 응력의 의존도는 언로드(0 사이클)에서부터 완전한 로드(1200 사이클)까지 예상했던 지속적인 진행을 보이지 않았다. 이는 사이클 수의 함수로써 응력의 비-직선성을 보인 그림 15에서 확인되었다. 즉, 1000사이클 이후 SAC와 SnPb의 솔더 접합부 양쪽에서 응력이 증가하였다. 이 현상은 시편의 정렬, 스트레인 게이지의 본딩 및 소형 레지스터 접합 부분과 연관이 있을 수도 있다. 그러나 중요하게도 이 방법은 솔더 접합부 무결성 평가에 현재 권장되지 않고 있다. 스트레인 게이지 부착과 관련해서 복잡하기 때문이다. 더 나은 결과는 모아레 기술을 이용한 필드 스트레인 모니터링을 적용하여 얻었다.
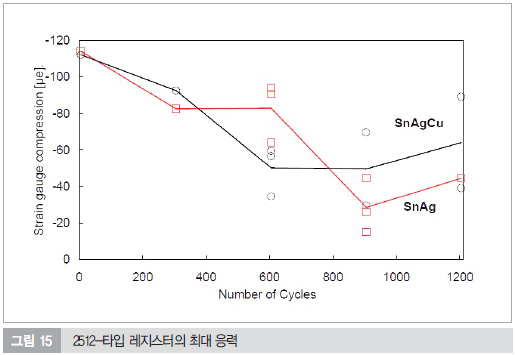
3-point Bend Test
3-점 굽힘 테스트의 경우, force는 레지스터 반대측의 서브스트레이트에 적용했고(그림 16 및 그림 17 참조), 서브스트레이트 변형은 레지스터 몸체의 상부에서 관찰되었고, 측정되었다. 변형의 정도는 솔더 접합부를 통해 레지스터에 가해지는 force에 따라 달라진다.
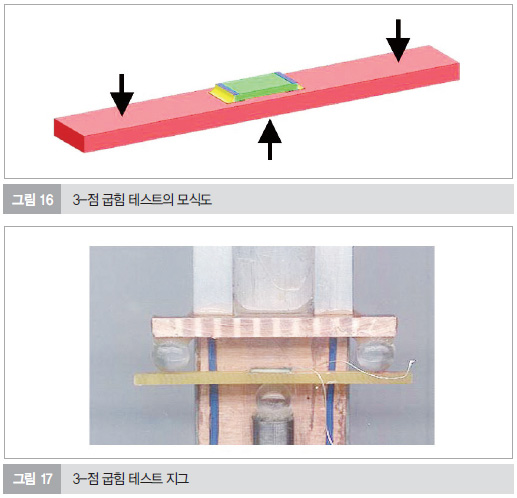
그림 18 내에서는 변화된 스트레인 게이지 분석이 레지스터의 납땜 접합 사이의 중앙 지점에 미스-실장된 어셈블리의 기능으로 표시되었다. 테스트 시편은 SnAgCu 합금을 이용하여 납땜되었고, 특정 열 사이클에 대상이 되지 않았다. 이 실험은 각각 10초의 드웰 타임(dwell time)을 지닌 20㎛ 미스-실장 공정 이후의 시간에 따른 변형의 추이를 조사하기 위해 실시되었다. 개별적인 미스-실장은 수평축 사이에서 나타났고 반면, 수직 공정은 각각의 미스-실장 공정 이후 시간에 따른 변형의 양에서 나타났다. 단지 60㎛의 미스-실장이후 곡선은 변형 내의 흐름을 지적하는 즉, 10초의 휴지 기간 동안 시간에 따른 행태의 모양과 같은 단계를 보인 것이 분명하다.
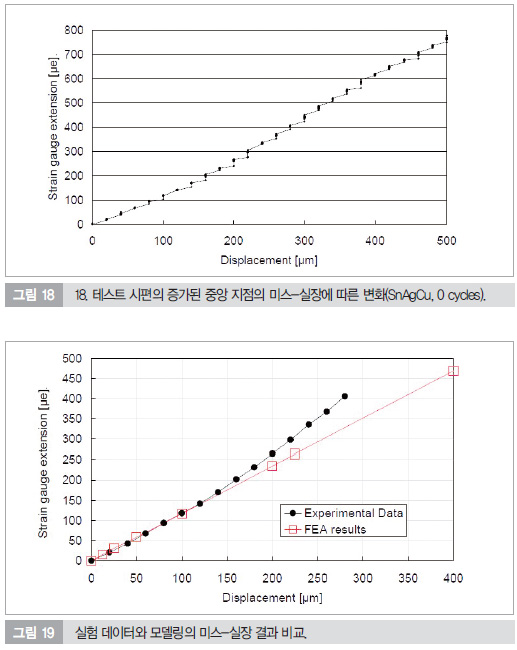
열 사이클링 상황에 관계없이 사용된 것은 다음과 같다. 솔더는 다루기 쉽게 되었고, 불가역적인 플라스틱 변형(크리프)는 테스트의 휴지 시간 동안 접합부 내에서 발생했다. 결과적으로, 굽어진 보드의 뒤틀림은 레지스터의 밴딩되지 않은 낮은 면과 보드 자체 간의 갭이 근접하게 되었고, 이로 인해 접촉이 발생할 수도 있다.
스트레인 게이지 어테치와 관련된 이 문제는 이 실험 방법이 크랙 혹은 솔더 접합부의 수명을 측정하는데 권장되지 않음을 의미한다.
그림 19는 변화된 스트레인 게이지 측정과 탄성변형에 완전히 기반하여 FEA 모델을 사용한 표면에 축적된 스트레인 간의 비교하여 보여주고 있다. 150㎛ 미만에서의 미스-실장의 경우 두 개의 곡선이 동시에 발생했다. 미스-실장의 더 높은 레벨의 경우 두 개의 곡선이 분기하였고, 이는 모델의 간결함 탓이다. 비슷한 결과로, 열 사이클 범위에 시편을 적용한 또 다른 테스트에서도 비슷한 비교분석 결과가 만들어졌다.
4-Point Bent Test
4-점 굽힘 테스트는 솔더 접합부가 3-점 시험에서 사용된 것과 반대 방향으로 스트레스가 가해짐으로써 3-점 굽힘 테스트를 대체한다. 그림 20에서는 어셈블리에서 가해지는 힘의 방향을 도식화하여 보여주고 있다. FEA 모델 계산은 레지스터의 상부 면에 이론상 압축 스트레인의 크랙 너비에 영향을 미치는 명확한 관계를 보여주고 있다(그림 21 참조). 그러나 이 테스트 방법은 실제 테스트가 향후 크랙의 확대와 나머지 솔더 접합부의 필연적인 박리 원인이 될 수 있다는 핵심 시뮬레이션으로 거부되었다. 그림 22에 도식화하였다.
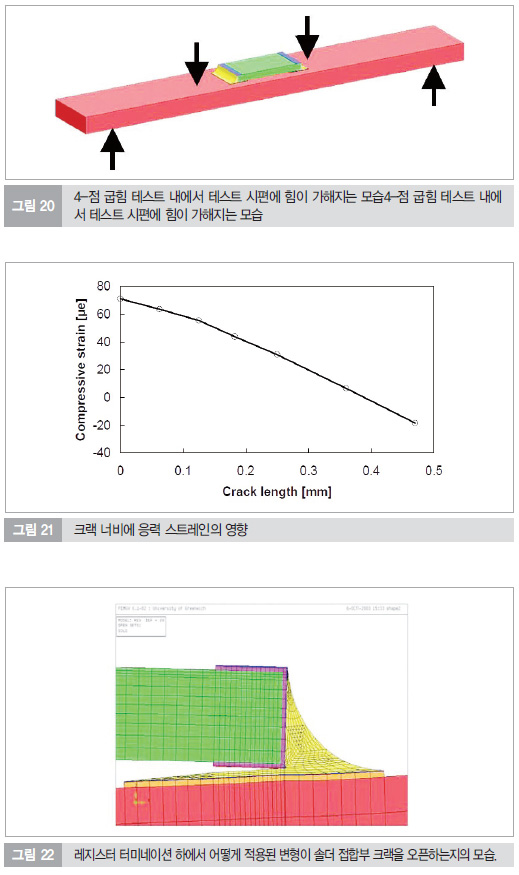
열 전도
솔더 접합부 내부의 크랙이 자체 열 전도율(동적 온도변화)에 영향을 끼칠 수 있다고 제안하고 있다. 크랙이 증가함에 따라 재질 내의 직접적인 전도성 통로가 좁아지게 되기 때문에, 결과적으로 열 전송의 비율이 감소한다. 이 제안된 칩 레지스터 어셈블리가 다양한 열 사이클 구간에 적용(그림 23 참조)하기 위해서, 가열된 플레이트에 놓았고, 온도-시간별 데이터를 기록했다.
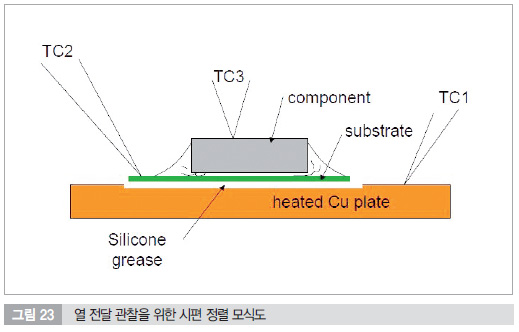
Copper 플레이트는 130℃로 가열되었고, 어셈블리(싱글 레지스터 칩을 지닌 PCB 서브스트레이트를 각각 대조하여)는 열 접촉 향상을 위해 실리콘 그리스로 처리된 플레이트 위에 놓였다. 써머커플 TC1은 플레이트의 온도를 모니터하기 위해 이용되었고, 서브스트레이트의 온도를 위해 TC2 그리고 납땜된 레지스터의 상부면의 온도를 관찰하기 위해 TC3가 이용되었다. TC2와 TC3의 시간에 따른 온도의 변화를 그림 24에서 보여주고 있다. 그들은 레지스터 온도(TC3)가 STD(short time delay)를 지닌 서브스트레이트 온도(TC2)를 뒤따라가고 있음을 확실하게 보여주고 있다. 그러나 크랙의 다양한 등급을 내재한 시편의 시간 지연에 두드러진 차이가 없었다. 즉, 300 혹은 1200 사이클의 열 사이클 범위에 넣었다.
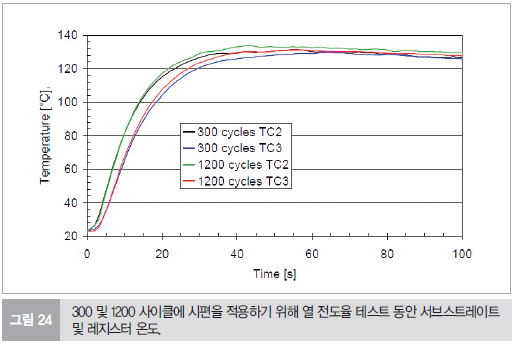
실험은 FEA 접근법을 이용하여 모델화되었다(그림 26 참조). 이 어셈블리의 경우 열 소스(100℃의 고정된 온도)에 ‘노출’되었고, 레지스터 상부면의 온도는 시간과 함께 기록되었다.
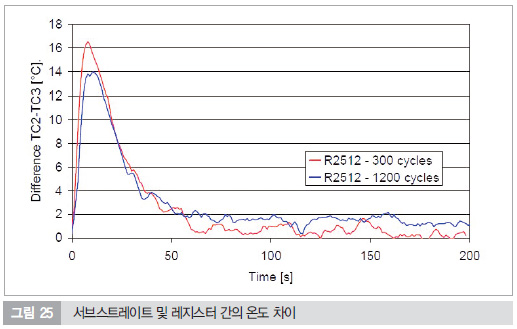
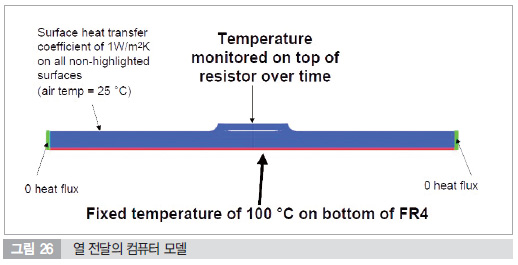
FEA 분석에 의한 결과는 그림 27의 A~E에서 보여주고 있다. 그림에서는 열 노출에 따른 솔더 접합부의 크랙 범위를 보여주고 있다. 각 크랙의 너비는 퍼센티지로 기록되었다. 0% 크랙은 사이클되지 않고, 크랙되지 않은 상태를 나타내고 있으며, 반면, 100% 크랙은 레지스터 테미네이션의 너비와 동일하다. 온도는 컬러에 의해 나타냈다. 그리고 시뮬레이션 (A~E)는 열 노출 12초 후에 멈췄다. 시뮬레이션 A에서 C까지는 가열 구간 전체에 온도 분배에 있어서 심각한 차이가 없었다. 그러므로 크랙의 사이즈는 솔더 접합부의 열 전도성에 영향이 없음으로 결론지어 진다.
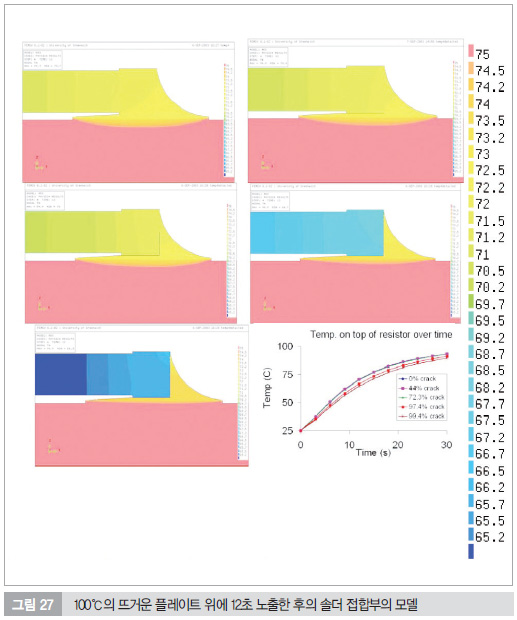
그림 27의 F에서는 각 크랙에 대한 시간별 온도 증가가 어떻게 이뤄지는지를 보여주고 있다. 열 전송의 역학에서 중요한 변화는 크랙의 너비가 테미네이션 너비의 72%와 97% 사이 일 때 발생했다. 그러나 이 스케일의 크랙을 지닌 솔더 접합부가 이미 기계적으로 불량이 되었을 것으로 예상된다. 이러한 결과로써 크랙 측정에 있어서 이 실험 방법의 부적합을 확신할 수 있었다.
결론
다수의 측정 기술들이 무연 솔더 접합부 내의 크랙을 연구하기 위하여 그들의 적합성이 평가되어 왔다. 전통적인 SnPb 솔더 접합부를 실험할 때 산업계에서 일반적으로 사용되는 기술들을 선택하였다. 비록, 검증 절차의 약간의 일부 수정이 필요하지만(즉, 무연 마이크로섹션에 서로 다른 에치), 이들 기술들이 SnPb 솔더 접합부 측정에 적합한 이들 기술들은 새로운 무연 솔더를 이용해 생성된 접합부 실험 측정에도 적합하다고 증명되었다.
다른 두드러진 사항은 다음과 같다;
▶ 마이크로-섹셔닝 방법은 크랙의 위치를 증명하고, 열 사이클링 이후 미세구조의 변화를 연구하는데 가장 적합한 방법임을 보여주고 있다. 이 방법인 소형 부품의 솔더 접합부 내에 존재한 크랙의 문제를 확대할 수도 있지만, 이 단점은 광학 마이크로스코프에 비해 SEM 내에서 마이크로섹션을 실험함으로써 상쇄될 수 있다. 마이크로-섹셔닝 방법은 자체 수명 내내 솔더 접합부의 정성분석(定性分析)에 적합하다.
▶ Dye penetration 기술은 솔더 접합부 크랙의 정량분석(定量分析)에 강점을 가지고 있음 보여주고 있으며, 전체 크랙 지점을 분석하는데 사용될 수 있다. 마이크로섹션닝의 경우와 같이 단면 종단면의 위치에 의존하지 않는다.
▶ 절단 테스트는 크랙 확대의 정도와 솔더 접합부의 피해뿐만 아니라 접합부의 강도도 측정하기 위해 설정된 방법이다.
▶ 대조적으로, 다른 기계적인 테스트(인장 테스트, 3점 및 4점 굽힘 테스트)는 고도의 기술력에 의존(작업자의 노련함에 강하게 의존하는 결과)하거나 혹은 테스트 동안 향후 피해를 자체적으로 유발시킨다. 결과적으로, 테스트는 일관적이지 않고, 잘못된 결과를 보인다. 이들 기술들은 미숙함으로 간주되고 넓게 사용되기 전에 기술향상이 요구된다.
▶ 열 전달 결과 테스트에서는 크랙이 터미네이션 너비의 ~70%보다 커지기 전까지 크랙의 사이즈가 솔더 접합부의 열 전도성에 어떠한 영향이 없음을 보였다. 이러한 스케일의 크랙을 지닌 솔더 접합부는 이미 기계적으로 불량으로 판명났다. 그래서 이 방법은 크랙 확대 연구에 부적합하고, 이는 크랙 및 크랙되지 않은 솔더 접합부를 통하여 열 전달의 역학에 심각한 변화가 없음을 보여주는 FEA 모델링에서 확인했다.
▶ 본 연구에 적용되지 않았지만 현재 진일보하고 있는 다른 기술들(즉, 실시간 X-Ray, 유도 혹은 초음파 이미징)은 공간해상도 부문의 제약을 극복할 때 향후 분명 가치가 있을 것이다. 노이즈 및 표면 거칠기에 기반을 두는 다른 기술들은 여전히 연구실용 분석으로 존재하고 있다.
▶ 이 작업은 연구에 필요한 분석 기술의 적합성을 측정하는데 도움을 주기 위해 FEA 분석의 가치를 증명하였다. 특히, 잠재적인 중요한 요소가 핵심이었고, 실제 테스트의 결과를 설명하는데 도움을 주었다.