진공 처리 후 특성 수명 및 Weibull 기울기, 명확하게 개선
열 피로 신뢰성도 높여
2개의 서로 다른 무연 에어리어 어레이 패키지 보드의 솔더 조인트 보이드 및 열 피로 신뢰성에 대한 진공 리플로우 처리의 효율성을 평가하기 위한 프로그램을 수행하였다. 표면 실장 어셈블리에서는 기존의 리플로우 공정과 솔더 조인트에 상당한 보이드를 생성하는 솔더 페이스트를 사용하였다. 테스트 보드의 절반은 진공 리플로우를 사용하여 재처리하였다. 열 사이클링은 0/100℃ 및 -55/125℃ 프로파일을 적용하였다. 열 사이클링 테스트 및 후속 실패 분석의 주요 결과를 밝인다.
요약
솔더 조인트 보이드에 대한 진공 리플로우 프로세스의 효율성과 후속 열 사이클링 퍼포먼스를 평가하기 위해 테스트 프로그램을 개발하였다. 에어리어 어레이 패키지가 장착된 테스트 보드는 솔더 조인트에 상당한 보이드를 생성하는 솔더 페이스트와 기존의 리플로우 프로세스를 적용하여 어셈블리되었다. 그런 다음 진공 리플로우를 사용하여 재처리(리플로우)되었다. X-선 검사에서는 진공 처리 후 솔더 보이드의 현저한 감소를 확인하였다. 기존 및 진공 리플로우 테스트 보드의 솔더 어테치 신뢰성을 특성화하고 2개의 다른 가속 열 사이클링 프로파일을 사용하여 비교했다. 열 사이클링 결과에서는 솔더 열 피로 신뢰성에 있어서 보이드의 일반적인 영향, 공개 문헌의 결과 그리고 솔더 보이드에 관한 진화하고 있는 산업계 표준의 관점을 논의한다. 다른 보이드 감소 방법 및 추가 신뢰성 연구를 기반으로 추가 작업에 대한 권장 사항을 제공한다.
서문
에어리어 어레이 솔더 조인트의 보이드와 신뢰성 간의 관계는 수년 동안 연구와 논쟁의 주제였다. 솔더 조인트 내 보이드의 근본적인 원인이 이해되고 있으며 주제에 대한 수 많은 보고서가 문서화되어 있다.[1],[2],[3] 보이드 특성화에 대한 업계 지침이 있지만[4],[5], 에어리어 어레이를 본질적으로 검사하는 것이 어렵고 보이드 함량을 정량화하는 것도 역시 힘들 수 있다.
Aspandiar의 솔더 조인트 보이드를 주제로 한 논의를 벤치마크했다.[3] 그림 1에 요약된 그의 분석에서는 여러 유형의 보이드와 여러 보이드 형성 메커니즘이 있음을 보여준다. 보이드는 어떻게 형성되었고, 솔더 조인트 내의 어느 위치에 존재하며, 솔더 조인트의 신뢰성에 어떻게 영향을 미치느냐에 따라 구분할 수 있다. Aspandiar는 열 사이클링 또는 기계적 충격 및 벤딩과 같은 다양한 유형의 스트레스 테스트 도중 크랙이 솔더 조인트의 기하학적 중심에 근접한 것보다 인접한 계면 영역을 통해 시작되고 전파되는 경향이 더 높다고 주장했다. 이러한 가설은 그림 2와 그림 3에서 보여주고 있다.
에어리어 어레이 솔더 조인트 보이드와 솔더 조인트의 장기적인 열 피로 신뢰성 사이에 상관관계가 있는지 이해하는 것이 중요하다. 열 피로 저항의 요구사항은 대부분의 고신뢰성 제품군에서 먼저 나오고 있다.[6] 솔더 조인트는 동작 중에 노후화되고 열화되며 열 활성 솔더 피로(크리프 피로)[7]의 마모 메커니즘에 의해 결국 파손된다. 이는 전자 산업계 어셈블리의 SMT 부품의 주요 마모 고장 모드이자 주요 고장 원인이기도 하다.[8]
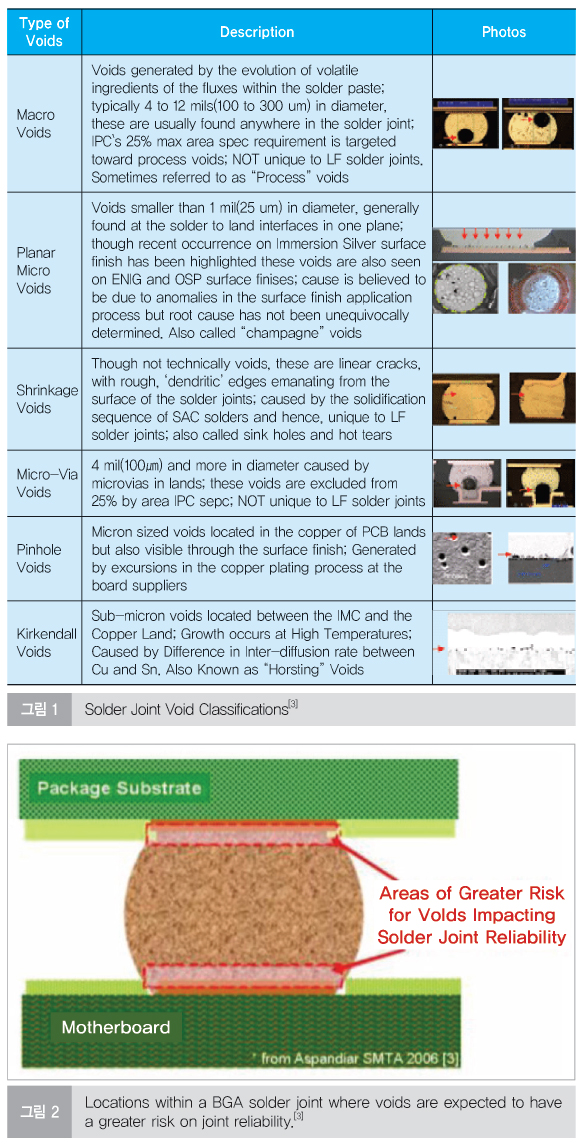
‘플래너 마이크로보이드(planar microvoid)’라고 불리는 특정 유형의 보이드는 어테치 영역을 실질적으로 줄이거나 전파 성향이 강한 크랙이 존재한 솔더 조인트 영역에서 솔더를 약화시킴으로써 신뢰성을 낮추는 것으로 나타났다.[9] 이 같은 영향은 그림 4의 Weibull 플롯에서 설명하고 있다. 여기에서 플래너 마이크로보이드는 특성 수명 에타(열 피로 신뢰도)를 23% 감소시킨다. 불량 모드 열 사이클링 샘플의 직교 단면에서 촬영한 현미경 사진에서는 마이크로 보이드와 크랙 전파에 대한 영향이 항상 분명하지 않거나 표준 파손 분석 기술을 사용하여 감지하기 쉬운 것은 아님을 보여주고 있다. 플래너 보이드로 인한 유사한 현상은 Mukadam et al[10]에 의해 수행된 기계적 신뢰성 테스트에서도 보고되었다. 그러나 플래너 마이크로보이드는 표면 마감 문제 또는 표면 오염과 가장 자주 관련된 보이드의 특수한 경우이다.
프로세스 매크로 보이드와 신뢰성 감소 사이에서는 이러한 명확한 상관관계가 확립되지 않았다. Aspandiar는 매크로 보이드가 솔더 조인트 신뢰성에 영향을 미치지 않는다는 현재 산업계의 입장을 지적했다.[3] 이러한 주장은 매크로 보이드가 보드 레벨 신뢰성을 감소시키지 않는다는 여러 연구의 결과에 의해 뒷받침되었다.[11],[12],[13]
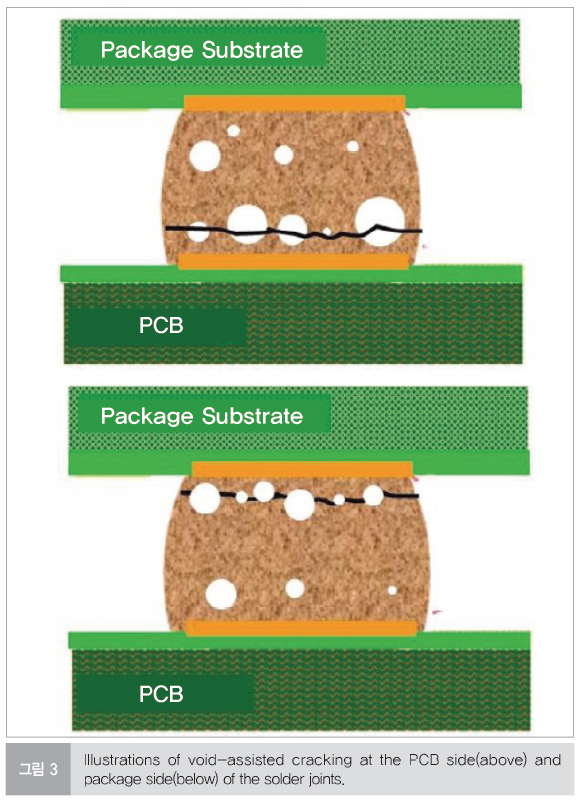
Sethuraman[14], Coyle[15], Hillman[16]에 의한 독립적인 조사에서는 솔더 조인트 신뢰성 악화에서 보이드의 유무가 반드시 충분한 근거가 되지 않는다는 점을 발견했다. 오히려, 솔더 조인트 파손 크랙 경로와 관계있는 보이드의 위치가 단독으로 존재한 것보다 훨씬 더 큰 영향을 미친다고 지적했다.
완성된 전자 어셈블리가 매크로 또는 프로세스 보이드 결함[4],[5]에 있어서 IPC 지침에 따라 거부될 수 있으므로 보이드를 제거하거나 보이드 밀도를 실질적으로 줄이는 것이 바람직하다. 리플로우 프로파일 수정, 질소 분위기 리플로우, 특수 솔더 페이스트 및 스텐실 설계 구현 등을 포함한 보이드를 줄이기 위해 다양한 프로세스 기술이 사용되었다.[17] 공정을 최적화하고 보이드를 최소화하려는 시도에도 불구하고 일반적인 표면 실장 어셈블리에서 일정량의 솔더 조인트 보이드는 불가피한 것으로 간주되고 있다.
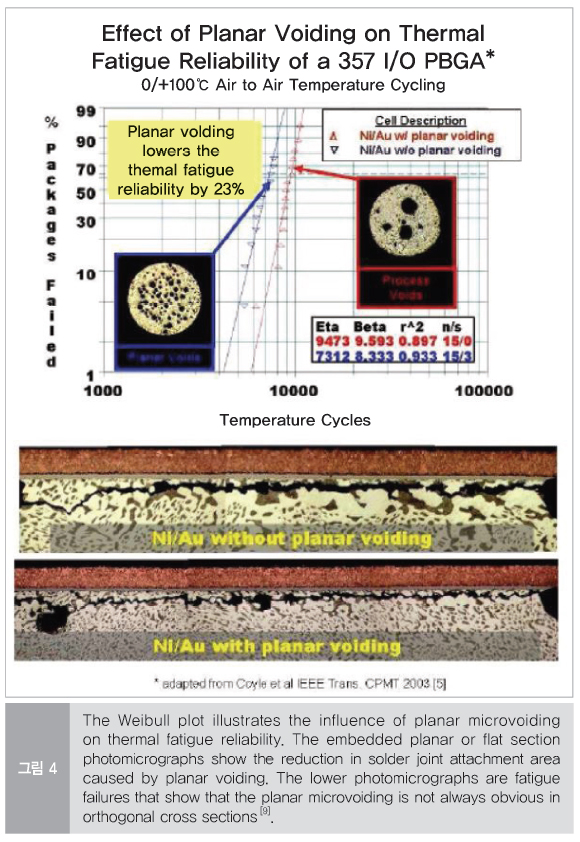
진공 리플로우는 솔더 조인트의 보이드 밀도를 줄이는 인정받은 프로세스 옵션이다. 그러나 Sweatman et al은 진공 리플로우 자체가 보이드가 없는 솔더 조인트를 보장하지 않는다는 점을 보여주었다.[18] 따라서 진공 리플로우를 사용하더라도 솔더 조인트 신뢰성에 대한 보이드의 영향에 대한 논쟁이 남아 있다. 본고에서는 솔더 조인트 보이드의 진공 리플로우 처리의 효율성과 열 사이클링에 의해 측정된 솔더 조인트의 열 피로 신뢰성을 평가하기 위해 설계된 테스트 프로그램의 결과를 보고한다. 열 사이클링 결과는 솔더 열 피로 신뢰성에 대한 보이드의 일반적인 영향, 공개 문헌의 결과, 솔더 보이드에 대한 진화하는 산업 표준의 관점에서 논의된다.
실험
부품 및 테스트 보드 설명
그림 5에 표시된 PCB 테스트 보드 및 부품은 원래 iNEMI Alloy Alternatives 연구[19]를 위해 개발되었다.
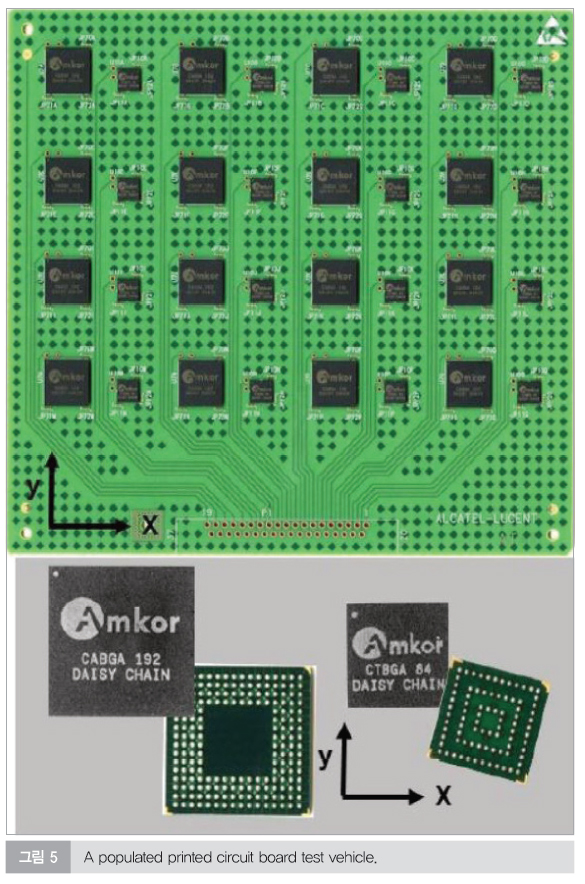
테스트 보드는 무연 솔더 구형으로 제작된 192CABGA 및 84CTBGA 패키지가 데이지체인 유형으로 채워졌다. PCB 테스트 보드의 두께는 6-레이어 구조의 2.36mm(93mils)이며, 16개 사이트에 각각 192CABGA 및 84CTBGA 패키지가 들어갔다. 테스트 보드는 고온 PCB 라미네이트와 OSP로 최종 마감처리되었다. 부품 및 PCB 속성은 표 1에서 나타내고 있다.
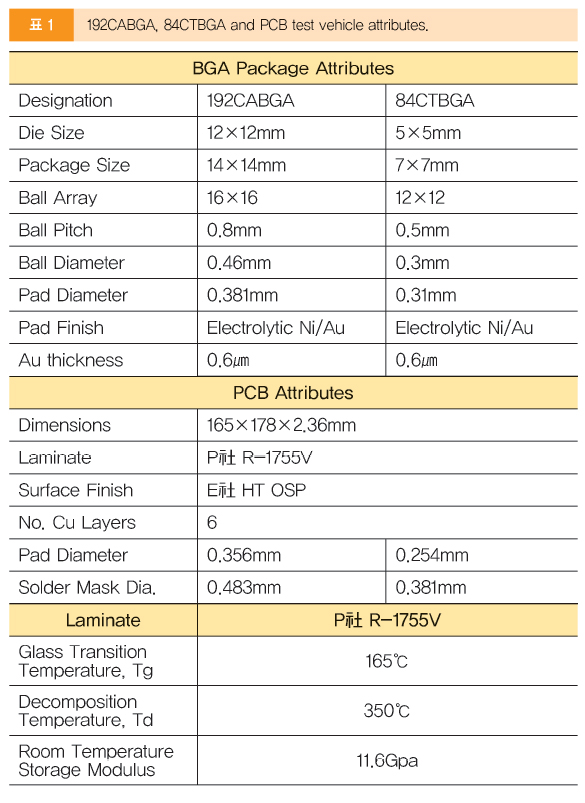
테스트 보드 표면 실장 어셈블리
테스트 보드는 250℃의 피크 리플로우 온도와 60초의 액상선 상의 측정 시간을 가진 기존의 리플로우 프로세스를 사용하여 조립되었다. 어셈블리에 사용된 무연 솔더 페이스트는 솔더 조인트에 상당한 보이드를 생성했다. 그 후, 테스트 보드의 밀집된 부문의 보이드를 줄이기 위해 진공 리플로우를 적용하여 재처리되었다.
진공 리플로우 프로세스는 3개의 컨벡션 쿨링 존이 있는 15-존 대류 리플로우 오븐에서 수행되었다. 진공 오븐은 히팅 15-존과 냉각 1-존 사이에 있다. 피크 온도는 238℃이고 액상선(217℃) 위의 시간과 재조립 리플로우를 위한 소크 시간은 각각 80초와 65초였다. 이 재조립 리플로우 프로세스에 대한 대류 영역 설정점이 표 2에 나와 있다. 이 공정을 위해 진공 리플로우 챔버 IR 패널 히터를 300℃로 설정했다.
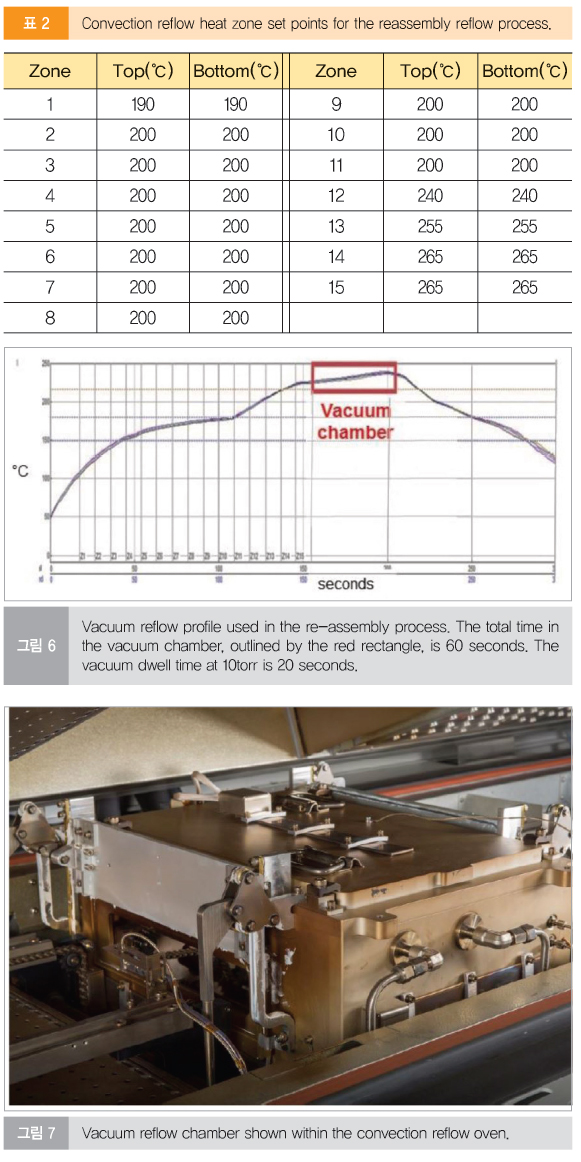
재조립 프로세스에서의 진공 리플로우 프로파일은 그림 6에 보여주고 있다. 빨간색 직사각형은 기판이 진공 챔버에 있었던 총 시간을 나타내며 약 60초이다. 총 시간에는 펌프 다운, 재충진 및 체류 시간뿐만 아니라 진공 챔버 안팎으로 테스트 보드의 운송시간도 포함되었다. 펌프 다운 시간은 8초, 10torr 진공에서의 체류 시간은 20초, 재충진 시간은 약 5초이다. 리플로우 프로파일의 피크 온도는 기판이 IR 패널 가열 상태에서 진공 챔버에 있는 동안 달성된다.
대류 리플로우 오븐 내에 위치한 진공 챔버는 기판을 수용할 준비가 되어야 한다. 그림 7에서는 진공 도어가 열린 상태를 보여주고 있다.
CTE 측정
솔더 조인트 접합 신뢰성은 패키지와 PCB 사이의 열팽창 계수(CTE) 불일치에 따라 달라진다.[20],[21] PCB의 CTE는 열역학적 분석기(TMA)를 사용하여 측정되었고, 192CABGA 및 84CTBGA 패키지의 복합 열팽창 계수는 미세한 모아레 간섭계를 사용하여 측정되었다. PCB 및 2개의 BGA 부품에 대한 CTE 데이터는 표 3과 표 4에 나와 있다.
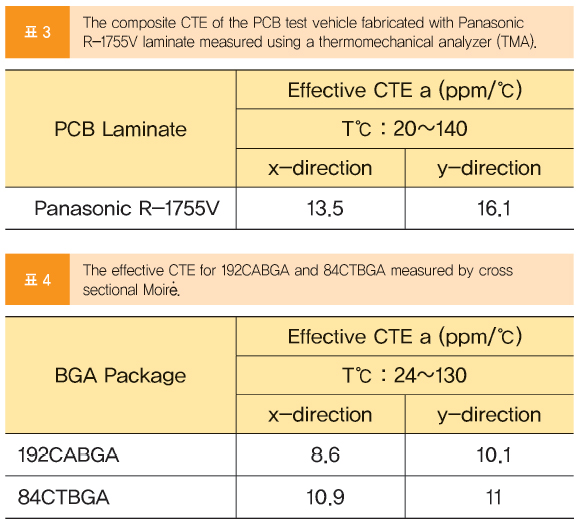
ATC(Accelerated Temperature Cycling) 테스트
데이지체인 유형의 부품과 테스트 회로 기판은 표면 실장 조립 후 전기적 연속성 테스트가 가능하고, 열 사이클링 동안 현장에서 지속적으로 모니터링할 수 있다. 열 사이클링 테스트는 IPC-9701A 지침[22]에 따라 수행되었다. 솔더 조인트는 1000Ω의 저항 한계로 설정된 이벤트 감지기를 사용하여 모니터링되었다.
고장 데이터는 2개의 파라미터를 적용한 Weibull 분석에서 특성 수명 η(63.2%의 고장비율에 도달하기 위한 사이클의 수)과 슬로프 β로 보고하였다.
2개의 ATC 프로파일은 표 5에 나와 있다. 해당 프로파일은 0/100℃(TC1)의 통신 업계의 신뢰성 요구사항과 –55/125℃(TC4)의 군사/방위 업계에서 가장 자주 언급되고 있다.[22]
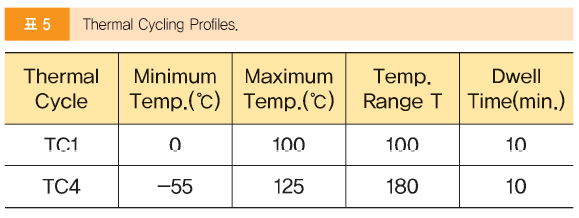
실험 테스트 구성
실험에 사용한 부품 및 열 사이클링 프로파일은 표 6에서 보여주고 있다. 각 테스트 셀에는 각 32개의 192CABGA와 84CTBGA 부품을 제공하기 위해 완전히 밀집된 복제 테스트 보드가 포함되어 있다. 기준 품질 및 미세 구조 특성화를 위해 추가 샘플을 조립했다.
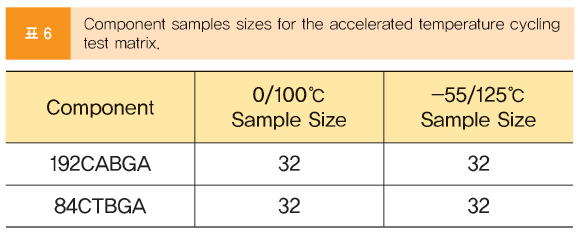
솔더 조인트 보이드 특성화 및 고장 분석
X-선 검사 및 금속 단면 분석을 사용하여 대표적인 보드 레벨 어셈블리의 솔더 조인트 보이드 및 타임-제로 미세 구조를 특성화했다. 고장 분석을 위해 온도 사이클링 챔버에서 제거된 샘플과 비교할 수 있도록 타임-제로 시간을 문서화했다. 솔더 접합 품질과 미세 구조는 광학 및 SEM(scanning electron microscopy)을 사용하여 관찰했다. SEM은 Pb-free 미세구조에서 상을 구별하기 위해 후방산란 전자 이미징(BEI) 모드에서 작동하였다.
결과
솔더 조인트 보이드 특성화
일반 혹은 표준 SMT 리플로우 어셈블리 공정을 거친 제품의 X-선 검사에서는 두 부품의 BGA 솔더 조인트에서 상당한 보이드 함량을 보여주었다. 그림 8의 a(192CABGA)와 그림 9의 a(84CTBGA)의 X-선 이미지는 일반적인 솔더 보이드의 범위와 크기이다. 보이드가 크면 응고된 솔더 구체의 직경이 눈에 띄게 증가했다.
보이드 테스트 보드의 절반은 보이드를 줄이기 위해 진공 리플로우 처리를 사용하여 2차 조립을 받았다. 그림 8의 b(192CABGA)와 그림 9의 b(84CTBGA)의 X-선 이미지는 진공 리플로우 후 결과적인 솔더 접합 품질을 보여주고 있다. X-선 이미지(STD SMT + VAC SMT로 식별됨)에서 진공 리플로우 처리 후 2개의 부품에서 솔더 보이드 표시가 없었다.
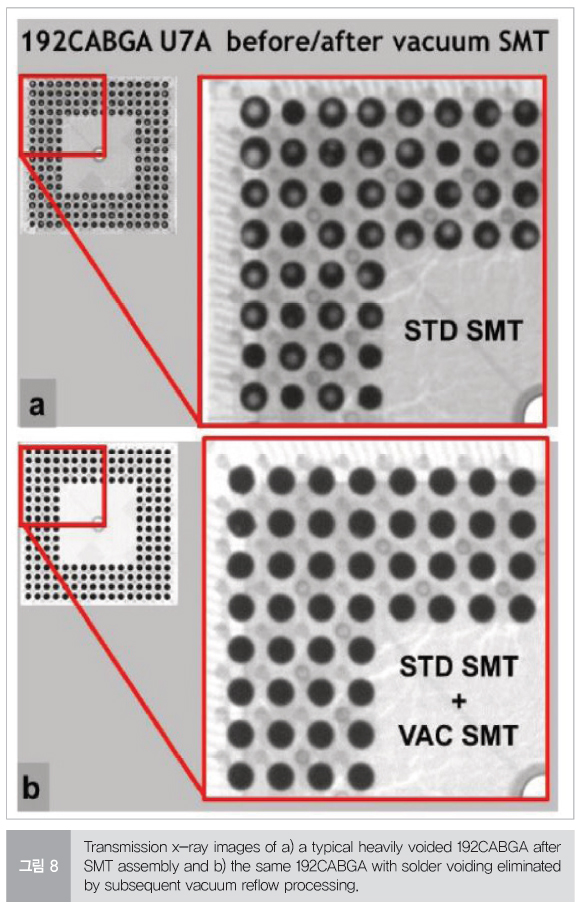
보이드의 단면도는 그림 10의 광학 현미경 사진에 나와 있다. 단면 분석에서 관찰된 많은 보이드가 X-선 이미지 영역의 30%인 IPC-JSTD-001 BGA 최대 보이드 기준을 초과했다.[23] 그림 8의 X-선 이미지에서 볼 수 있는 응고된 솔더 구체의 직경이 눈에 띄게 커짐으로써 질적으로 많았음을 관찰할 수 있었다.
그림 8과 그림 9의 플래너 X-선 이미지와 비교하여 그림 10의 횡단면 이미지는 피로 균열이 전파될 것으로 예상되는 납땜 인터페이스에 있어서 보이드의 위치를 보여주고 있다(그림 2 참조). 보이드가 항상 솔더 구체나 패드의 중앙에 있는 것은 아니기 때문에(X-선 이미지 참조), 단면 이미지는 보이드의 크기를 정확하게 나타내지 않을 수 있다. 최악의 경우 단면 영상에서 오프셋 보이드가 전혀 나타나지 않을 수 있다. 그러나 그림 10의 일부 이미지는 납땜 인터페이스에서 보이드 위치의 위험을 보여주고 있다. 그래서 열 사이클링에서 조기 실패의 위험이 늘어난다. 고장 분석의 경우 단면 이미지를 사용하여 X-선 이미지를 보완할 수 있지만 열 사이클링에 놓이기 전에 샘플을 특성화하는 데 파괴적인 단면을 사용할 수는 없다.
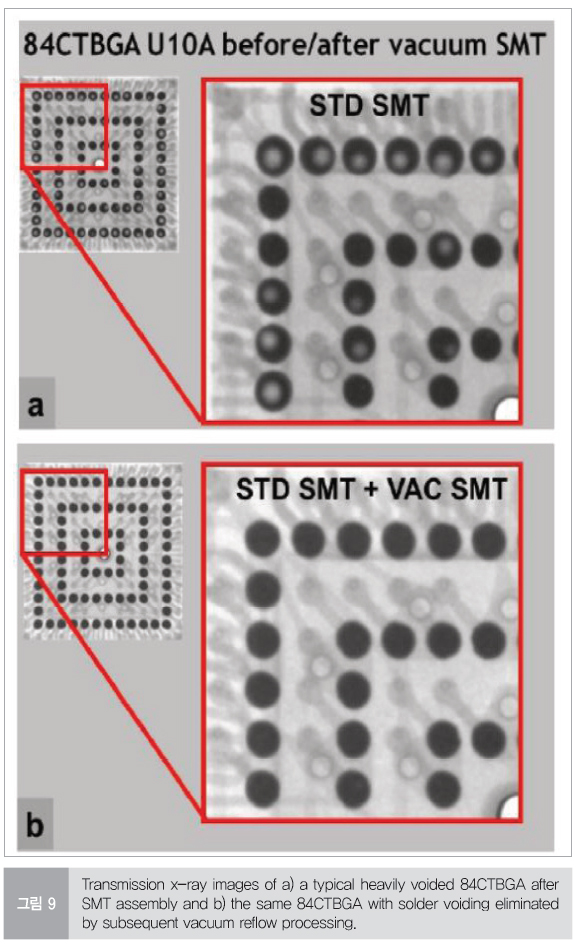
열 사이클링
그림 11과 그림 12는 각각 0/100℃ 및 -55/125℃의 열 사이클링 테스트에서 얻은 Weibull 분포 플롯이다. 표 7은 두 테스트에 대한 Weibull 통계 요약을 보여주고 있다.
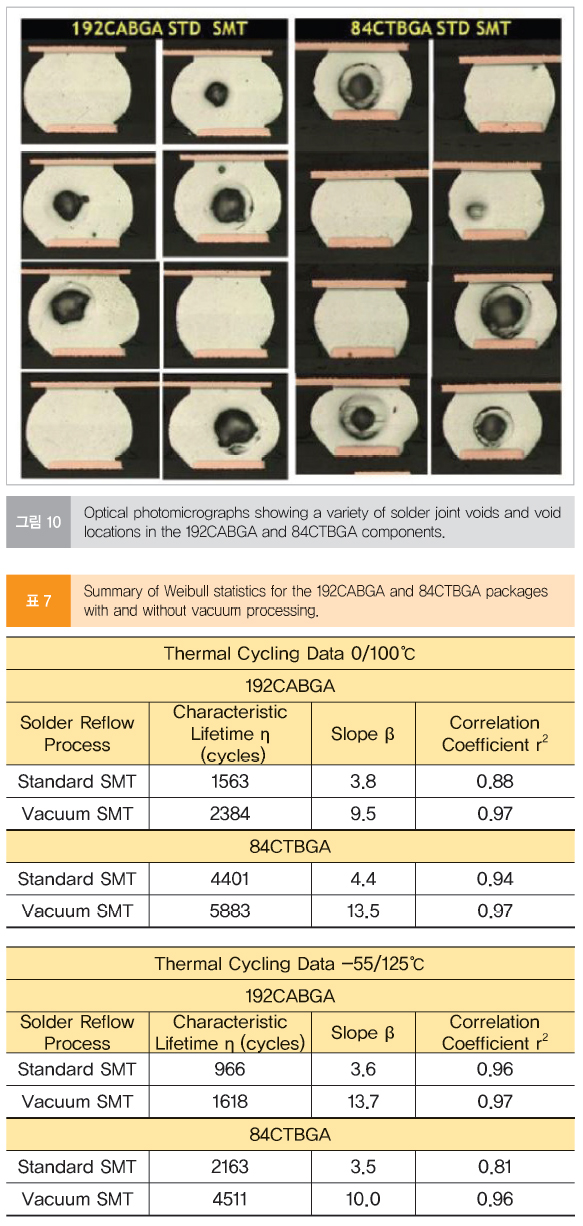
열 사이클링 테스트 결과에서는 진공 처리를 통한 특성 수명(신뢰성)과 Weibull 슬로프(데이터 품질)의 명확한 개선을 보여주었다. BGA 솔더 조인트 보이드가 어테치 신뢰성 위험을 나타내지 않는 경우가 많지만[14],[15],[16], 현재 샘플에서 보이드의 크기와 위치가 열 사이클링 동안 실패 프로세스에 영향을 미친다. 또한 개별 샘플 내에서 그리고 샘플 세트 전반에 걸쳐 보이드 변동이 더 낮은 Weibull 슬로프를 설명한다고 가정하는 것이 합리적이다.
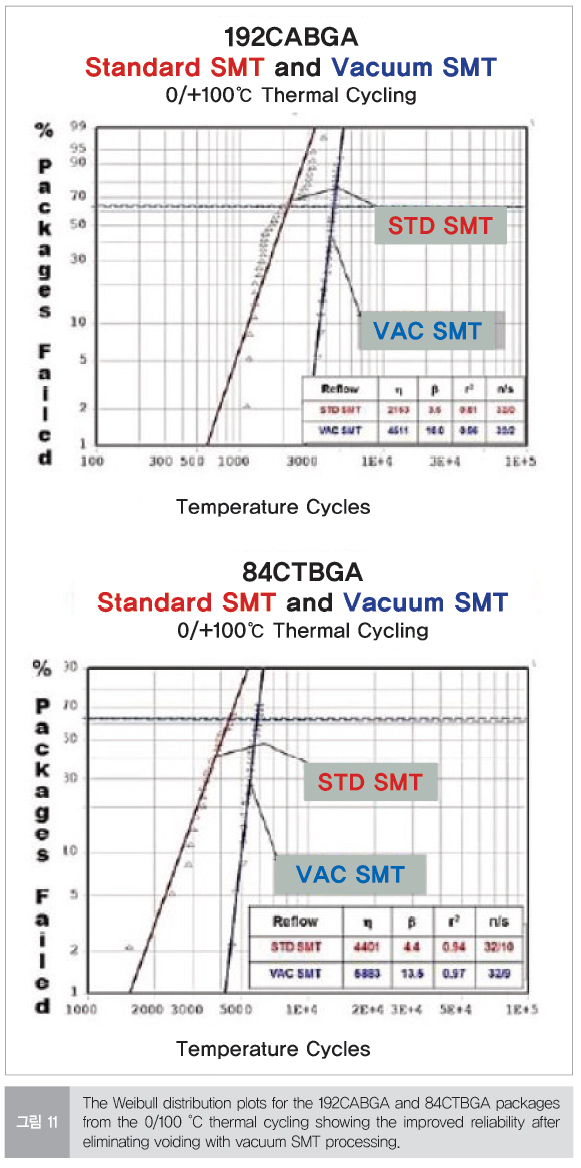
고장 분석
-55/125℃ 열 사이클링 테스트는 0/100℃ 테스트 후에 실질적으로 시작되었으며, 0/100℃ 사이클의 샘플만 고장 분석에 사용할 수 있었다.
TC1의 0/100℃ 열 사이클링 테스트에서 보이드 솔더 접합 불량의 예는 그림 13의 광학 현미경 사진에 나와 있다. 대형 솔더 보이드는 크랙이 전파됨에 따라 실질적인 어테치 영역을 줄인다. 그래서 고장에 이르는 사이클링 수가 적다.
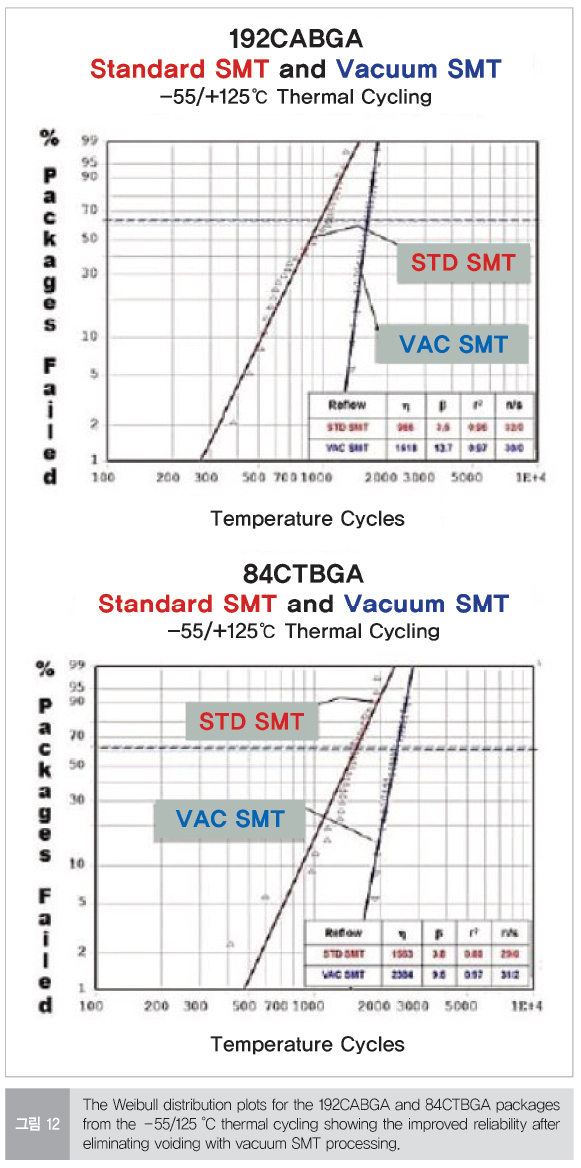
불량 모드는 솔더 피로가 남아 있으며, 피로 수명의 감소는 크랙 경로를 줄이는 기하학적 효과에 기인한다. 이 샘플은 0/100℃ 열 사이클링 테스트에서 가장 초기에 실패한 두 가지이며, 초기 실패가 보이드의 엄청난 크기와 관련이 있다고 가정하는 것이 확실히 합리적이다.
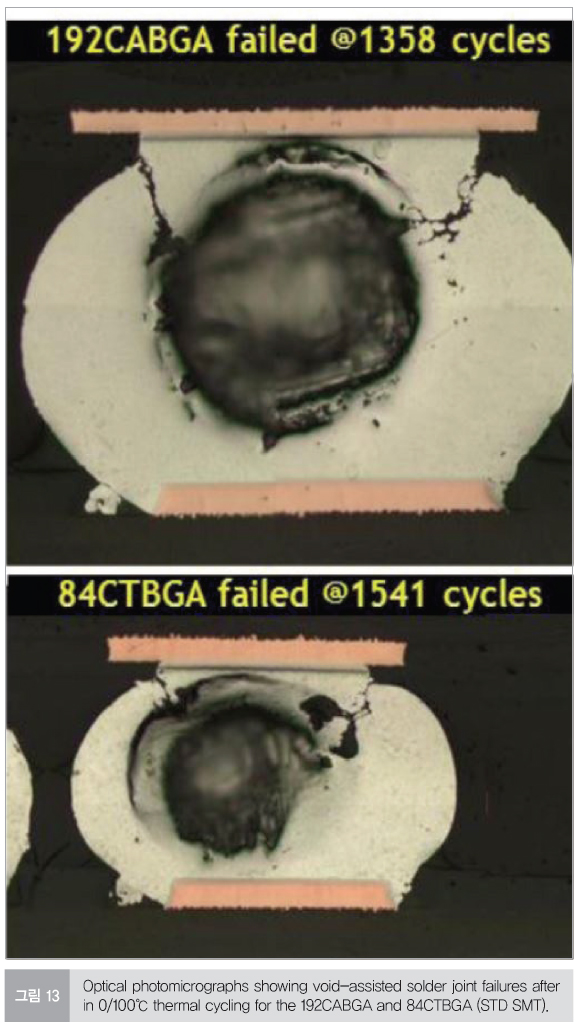
그림 14의 광학 현미경 사진은 진공 처리된 샘플에서 솔더 접합 실패(0/100℃ 열 사이클링)의 예를 보여주고 있다. 이 이미지는 SAC 합금에서 열 피로의 벌크 솔더 크랙 특성을 보여준다. 192CABGA 패키지에서 결함은 대부분 솔더 조인트의 PCB 측에서 발생하며 패키지 측면에서 약간의 피로 균열 시작이 발견되었다. BGA 열 사이클링 실험에서 패키지 측면 솔더 접합 실패가 일반적이지만, 이 192CABGA 패키지에서 PCB 측 결함이 발생하는 것으로 알려져 있다.[24] 84CTBGA 패키지의 피로 파손은 BGA 피로 크랙의 일반적인 위치보다 패키지 측면 위치의 벌크 솔더에서 발견되었다.
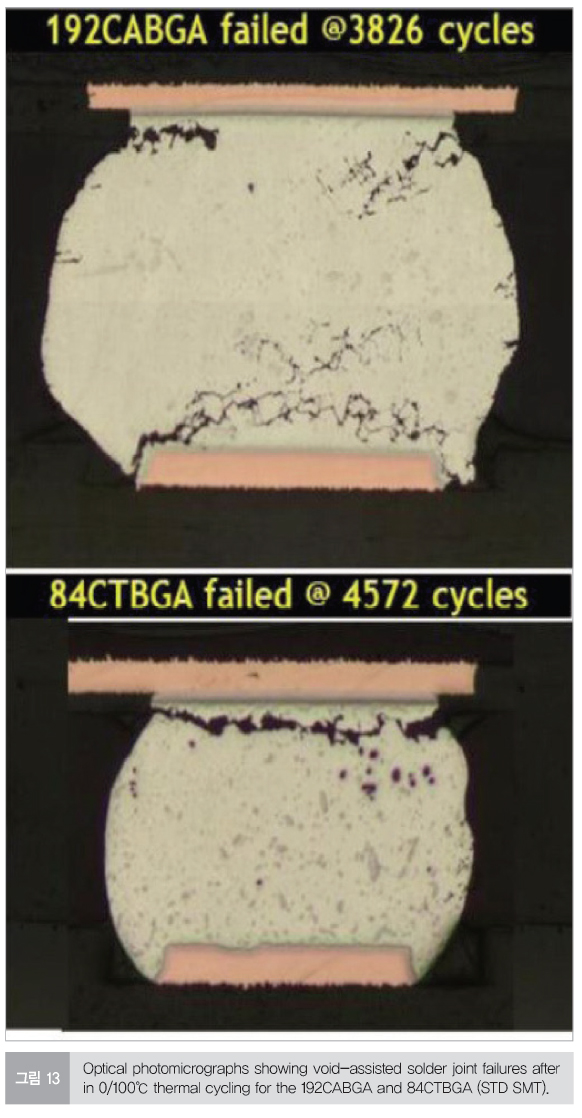
열 사이클링 동안 불량난 부품의 금속 조직 이미지는 표 6에 요약된 Weibull 분석의 결과를 확인하고 IPC-JSTD-001 최대 보이드 기준과 일치했다. 진공 리플로우가 솔더 프로세스 보이드를 수정했고 마찬가지로 솔더의 열 피로 신뢰성을 수정했음이 분명했다. 보이드가 극도로 크고 잠재적인 피로 균열 경로의 위치에 있을 때 솔더 조인트의 부차적인 보이드 파괴로 인한 특성 수명의 감소는 25%~50% 사이였다. 솔더 조인트 수명, 보이드 및 보이드 부재 사이의 이러한 관계는 2개의 다른 부품과 2개의 다른 열 사이클링 프로파일을 사용하여 입증되었다.
결론
2개의 서로 다른 무연 에어리어 어레이 패키지 보드의 솔더 조인트 보이드 및 열 피로 신뢰성에 대한 진공 리플로우 처리의 효율성을 평가하기 위한 프로그램을 수행하였다. 표면 실장 어셈블리에서는 기존의 리플로우 공정과 솔더 조인트에 상당한 보이드를 생성하는 솔더 페이스트를 사용하였다. 테스트 보드의 절반은 진공 리플로우를 사용하여 재처리하였다. 열 사이클링은 0/100℃ 및 -55/125℃ 프로파일을 적용하였다. 열 사이클링 테스트 및 후속 실패 분석의 주요 결과는 다음과 같다.
▶ X-선 및 금속 조직 검사 결과, 솔더 페이스트는 양쪽의 부품의 많은 볼 위치에서 현저한 보이드를 생성하는 데 영향을 미쳤다. 관찰된 보이드의 상당수가 IPC-JSTD-001 최대 보이드 크기 기준을 초과했다.
▶ X-선 및 금속 조직 검사 결과, 후속 진공 리플로우 처리로 양쪽 부품의 보이드가 거의 모두 제거된 것으로 나타났다.
▶ 열 사이클링 결과에서는 진공 처리로 특성 수명(신뢰성)과 Weibull 기울기(데이터 품질)의 명확한 개선을 보여주었다. 진공 처리 후 특성 수명이 25~50% 향상되었다.
▶ 금속 조직학적 단면 분석에서는 표준 표면 실장 조립 공정으로 제작된 샘플에서 보이드 보조 고장 모드를 보여주었다. 매우 크고 전략적으로 위치한 보이드는 피로 크랙 확산에 유효 경로 영역을 줄이는 단순한 기하학적 영향으로 인해 신뢰성을 감소시킨다. 진공 처리된 샘플의 비교 가능한 금속 조직 분석에서는 벌크 솔더에서 예상되는 열 피로 모드를 보여주었다.
▶ BGA 솔더 조인트 보이드는 일반적으로 접착 신뢰성 위험을 나타내지 않지만[14-16], 샘플의 큰 크기와 보이드 위치는 열 사이클링 동안 실패 사이클 수와 실패 프로세스에 상당한 영향을 미쳤다.
REFERENCES
[1] Ning-Cheng Lee, Reflow Soldering Processes and Troubleshooting SMT, BGA, CSP and Flip Chip Technologies, “SMT problems During Reflow, Section 6.1, Voiding,” Butterworth-Heinemann, Reed Elsevier Group, 2002.
[2] R. J. Klein Wassink, Soldering in Electronics, A Comprehensive Treatise on Soldering Technology for Surface Mounting and Through-Hole Techniques, 2nd Edition, Electrochemical Publications, Great Britain, 310-311, 1984.
[3] Raiyo F. Aspandiar, “Voids in Solder Joints,” Proceedings of SMTAI 2006, 406-415, Chicago, IL, September 2006.
[4] IPC-A-610D, “Acceptability of Electronics Assemblies,” Section 8.2.12.4, 8-83, IPC, February 2005.
[5] IPC-7095B, “Design and Assembly Process Implementation for BGAs,” Section 7.5.1, 76-83., IPC, October 2004.
[6] Gregory Henshall, Keith Sweatman, Keith Howell, Joe Smetana and Richard Coyle, Richard Parker, Stephen Tisdale, Fay Hua, Weiping Liu, Robert Healey, Ranjit S. Pandher, Derek Daily, Mark Currie, Jennifer Nguyen, “iNEMI Lead-Free Alloy Alternatives Project Report: Thermal Fatigue Experiments and Alloy Test Requirements,” Proceedings of SMTAI, 317-324, San Diego CA, 2009.
[7] Joe Smetana, Richard Coyle, Peter Read, Richard Popowich, Debra Fleming, and Thilo Sack, “Variations in Thermal Cycling Response of Pb-free Solder Due to Isothermal Preconditioning,” Proceedings of SMTAI 2011, 641-654, Fort Worth, TX, October 2011.
[8] Werner Engelmaier, “Surface Mount Solder Joint Long-Term Reliability: Design, Testing, Prediction,” Soldering and Surface Mount Technology, vol. 1, no. 1, 14-22,
February, 1989.
[9] Richard J. Coyle, Diane E. Hodges Popps, Andrew Mawer, Donald P. Cullen, George M. Wenger, and Patrick P. Solan, “The Effect of Modifications to the Nickel/Gold Surface Finish on Assembly Quality and Attachment Reliability of a Plastic Ball Grid Array,” “The Effect of Modifications to the Nickel/Gold Surface Finish on Assembly Quality and Attachment Reliability of a Plastic Ball Grid Array,” IEEE Transactions on Components and Packaging Technologies, vol. 26, no. 4, 724-732, December 2003.
[10] Muffadal Mukadam, Norman Armendariz, Raiyo Aspandiar, Mike Witkowski, Victor Alvarez, Andrew Tong, Betty Phillips, and Gary Long, “Planar Microvoiding in Lead-Free Second-Level Interconnect Solder Joints,” Proceedings of SMTAI 2006, 393-405, Chicago, IL, September 2006.
[11] Donghyun Kim, Ken Hubbard, Bala Nandagopal, Mason Hu, Sue Teng, Ali Nouri, “Effect of Voiding on Solder Joint Shock and Thermal Reliability,” Proceedings of IPC APEX 2006, S31-03-01 to S31-03-10.
[12] D. R. Banks, T. E. Burnette, Y. Cho, W. T. DeMarco, and A. J. Mawer, “Effect of Solder Joint Voiding on Plastic Ball Grid Array Reliability,” Proceedings of Surface Mount International 1996, 121-126, Chicago, IL, September 1996.
[13] M.Wickham, M. Dusek, L. Zou, and C. Hunt, “Effect of Voiding on Lead-Free Reliability,” NPL Report DEPC MPR 033, April 2005.
|