X-선 검사를 통한 보이드 검출 확인
부피 변화에 따른 그레이스케일 밀도 차로 높이 측정도 가능
X-선 검사는 중앙 단자 아래의 보이드 수준을 쉽게 보여주고 측정하여 양호한 제조 공정을 빠르고 실질적으로 확인하거나 그렇지 않은지 확인할 수 있게 해 준다. 높이 변화를 직접 확인하지는 않지만, 디바이스 아래의 전도성 재료에 상당한 부피 변화가 있는 경우 X-선 이미지에서 불연속적인 밀도 차이로 표시된다. 과도한 보이드 수준도 명확하게 볼 수 있다. 이러한 관찰 결과를 함께 사용하면 패드 표면 위로 디바이스가 ‘부유’될 가능성과 사용 시 고장 가능성과 상관 관계를 알 수 있다. QFN에서 에지 단자의 밀도와 모양의 변화도 X-선 검사를 통해 빠르게 관찰할 수 있다.
요약
QFN(Quad Flat Pack No Leads) 스타일(LGA(Land Grid Array)라고도 함)의 무연 패키징은 저렴한 비용과 낮은 스탠드오프 높이, 우수한 열적 / 전기적 특성으로 인해 무선, 자동차, 통신 및 기타 여러 애플리케이션에서의 사용이 급속도로 늘어났다. 이 패키지 유형을 구현함에 있어서, 이들 패키지가 가져오는 문제를 파악해야 하는 공정 / 품질 엔지니어뿐만 아니라 사용에 따른 설계 및 프로세싱 관련 학습 곡선(learning curve)이 항상 존재한다. 본고에서는 제조 품질 관리의 일부로 광학 및 X-Ray 검사를 사용할 때 QFN/LGA에서 볼 수 있는 일반적인 공정 결함의 예를 알아본다. 4개의 PCB 마감재와 증기상 및 대류 리플로우를 사용하여 수행한 시험 결과에 대해 논의할 것이다. 광학 검사 외에도 고해상도, 고배율 X-선 검사를 사용하면 광학적으로 패키지의 숨겨진 측면에 대한 비파괴 검사를 수행하여 패키지 중앙 부분 아래에서 자주 볼 수 있는 오픈 조인트와 과도한 보이드를 표시할 수 있다. 이러한 과도한 보이드는 동작 중에 패키지의 열 성능에 영향을 미칠 뿐만 아니라 스탠드오프 높이를 수정할 수도 있다. 따라서 보이드 모니터링은 부적합한 스탠드오프 높이의 존재를 확인할 수 있는 유용한 방법이며, 이 경우에 생산 중 오픈 조인트의 성향을 파악할 수도 있다.
서문
리드 없는 패키지인 QFN(Quad Flat Pack No Lead) 타입은 PCBA에서 많은 용도로 사용되고 있다. 다른 패키지 타입에 비해 저렴한 비용, 낮은 스탠드오프 높이, 최종 제품의 경박이 가능하며 우수한 열 및 전기적 특성 때문이다. 일반적으로 QFN으로 알려져 있지만 패키지 유형은 다른 이름을 지니고 있다. 가장 일반적인 패키지는 LGA(Land Grid Array)이다. 그러나 동일한 용어를 설명하기 위해 사용할 수 있는 다른 용어로는 PQFN(Plastic Quad Flat No-Lead), MLFP(Micro Lead Frame Plastic), SON(Small Outline No-Lead), MLP(Micro Leadframe Package)가 있다. 이러한 모든 패키지에 대한 간단한 일반적인 설명은 패키지 하부에 있는 대부분의 조인트 단자와 가장자리 주변으로 평면적인 연결이 가능하다는 것이다. 종종 가장자리 단자는 몰딩된 외부의 수직 면을 따라 연결된다. 또한 디바이스 중앙 부분의 대부분 아래에 하나의 대형 종단/방열판이 더 있을 수 있다(그림 1 참조). 이후에 설명하겠지만 보드 어셈블리 중에 가장자리 연결의 품질뿐 아니라 중앙에 있는 중앙의 대형 패드(있는 경우) 내부의 보이드 수준을 고려해야 한다. 중앙 패드가 부품에서 열을 제거하는 데 사용되는 경우, 열 접촉 불량을 초래하는 보이드로 인해 발생하는 열 효율 감소는 디바이스 과열뿐만 아니라 고장을 유발할 수도 있다.
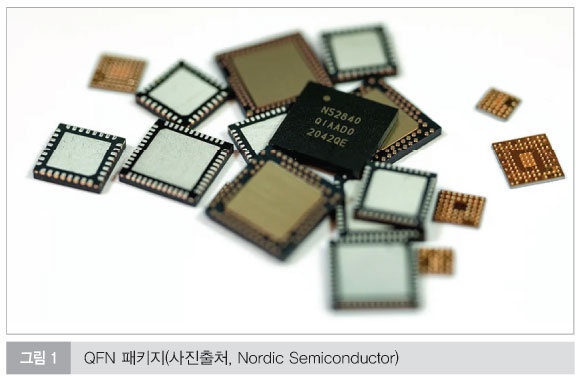
패키지 단자가 모두 디바이스 아래에 위치해 있고, 에지 조인트의 주요 벌크와 중앙 조인트 전부가 가려져 있기 때문에 기존의 자동 광학 검사(AOI)가 불가능하지는 않더라도 매우 어렵다. 또한 리플로우 도중에 패키지의 측면 단자가 젖어 들지 않으면 이들 패키지에 대한 AOI 효율성은 더욱 떨어진다. 나중에 볼 수 있듯이 수동 광학 현미경의 사용은 이들 패키지 에지 조인트의 품질에 대해 좋은 정보를 얻을 수 있지만, 중앙 조인트를 분석 및 평가할 수 없다. 이와 대조적으로, 생산 환경 내에서 X-Ray 검사를 사용하면 비파괴적인 방법으로 중앙 패드 아래의 보이드를 포함하여 모든 패키지 단자를 조사할 수 있다.
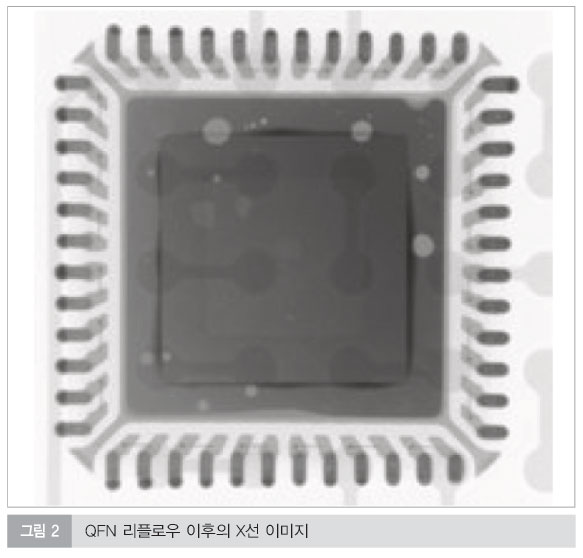
QFN 패키지를 조사하기 위한 최근 기술 개발이 이뤄진 2D X-Ray 검사 장비[1],[2],[3]를 사용하였다. 특히 오블릭 앵글 뷰(oblique angle views)에서 검사할 때 해상도 배율과 그레이스케일 감도가 향상되었다. 또한 새로운 X-Ray 시스템에는 기본으로 그레이스케일 범위가 개선된 디지털 X-선 이미징 디텍터가 포함되어 있으며, 이를 통해 유사한 밀도 특징[3]에서도 훨씬 더 나은 시각적 분리가 가능하여 최상의 효과적인 식별 및 분석할 수 있었다(그림 2 참조).
이러한 X-Ray 개발을 통해 비교적 경험이 없는 운영자는 생산 환경 내에서 분석을 신속하게 평가하고 정량화할 수 있다. 우수한 배율, 해상도 및 컨트라스트 감도가 부족한 X-Ray 검사 장비에서는 분석의 명확성을 달성하기가 더 어려울 수 있다.
실험 세부 사항
무연[4] 표면 마감의 보드에 대류 및 증기상 리플로우를 사용하여 실험을 수행했다. 보드의 두께는 1.6mm였으며 다양한 SMD 부품과 쓰루홀 커넥터 타입의 소자가 포함되어 있었다. 6×6mm 40-핀 QFN 패키지 2개가 디자인에 포함되었다.
다른 유형의 측면 단자를 갖도록 패키지 구성이 다른 두 개의 보드를 사용하였다. 경성 보드와 마찬가지로 유사한 설계 규칙과 공정 매개변수를 사용하여 연성 회로보드의 QFN에 대한 실험도 병행하였다.
두 가지 유형의 경성 보드 적층의 구조는 다음과 같다:
· ISOLA 410 소재
- 1.08mm 코어 35/35um + 2 × 7628 프리프레그
· ISOLA 104 (표준 FR4) 소재
- 1.00mm 코어 + 2 × 7628HR 프리프레그
연성 회로보드의 구성은 다음과 같다:
· 0.05mm 동박 18/18um ESPANEX
· 액상 솔더 마스크 - MPR80 Amber
4개의 배치 구조로 연성 보드와 경성 보드를 구분하였다. 전형적인 무연 공정에 적합한 4개의 주요 OSP 중 하나가 각 배치에 적용하였다. 이는 동일한 보드에 OSP 처리만 유일하게 차이를 두기 위해서 였다.
사용된 OSP는 다음과 같다.
▶ Immersion Nickel/Gold - Aurotech(Atotech)
▶ Immersion Tin -
▶ Immersion Silver -
▶ OSP - Glicoat SMD P2(Shikoku)
그런 다음에 경성 및 연성 보드 모두 다음의 공정 단계로 어셈블리하였다;
▶ Electroform 니켈 도금 스텐실
▶ 고속 마운터
▶ 컨벡션 & 증기 위상 리플로우
▶ IR & 컨벡션 리웍
더 자세한 내용과 사용된 프로세스 파라미터는 무연 경험 보고서[4]에서 확인할 수 있다. ‘경험 보고서 4’ 실험의 경우, 샘플 보드를 -55℃~+125℃에서 초기 2,000사이클, 이후에는 900 사이클의 주기로 열 순환하였다. 사이클 지속 시간은 48분이었다. 온도 사이클링은 영국 국립 물리 ​​연구소(NPL)에서 수행되었다. 각각의 실험 보드를 육안으로 검사하고 선택된 샘플을 미세하게 절단했다. 이 부문은 주로 마이크로 비아홀 신뢰성 테스트와 연관되어 있으며 별도의 논문에서 논의된다.[5]
QFN 조인트 품질에 대한 X-ray 검사는 납땜 공정 후와 900회의 열 사이클 후에 수행되었다. 이 분석에 디지털 X-Ray 검사 시스템이 사용되었다. X-ray 시스템에는 2.0메가픽셀의 X-선 이미지 크기, 16비트 그레이스케일 감도의 서브미크론 해상도를 갖춘 ‘밀폐 투과형’ 타입의 X-ray 튜브가 장착되어 있다. X-선 이미지는 초당 30프레임으로 획득되었다. 시스템은 사용 가능한 배율 손상 없이 테스트 보드의 모든 위치 주변 360°의 모든 지점에서 최대 70°의 오블릭 앵글(경사각도)를 구현할 수 있었다. 보드를 기울이는 대신 X-선 디텍터를 기울이는 구조이다.
분석 - 광학 검사
테스트 보드 내의 QFN 조인트에 대한 광학 검사 결과, 대류 또는 증기상 리플로우를 사용했는지 여부에 관계없이 대부분의 조인트 품질이 양호하게 나타났다. 그러나 발생한 몇 가지 결함에서는 QFN 에지 단자의 ‘양호’, ‘양호한 불량’과 관련하여 다양하게 나타났다.
그림 3은 QFN 부품의 에지 단자 솔더 조인트의 광학 이미지이다. 부품 공급업체는 단자에서 최적의 도금 마감을 실시하여 리플로우 중에 ‘고전적으로 완벽한’ 필렛이 형성되도록 했으며, 여기에는 측면 단자의 커버리지도 포함된다. 그림 4에서는 에지 단자에 만족스러운 솔더 필렛이 있지만, 측면 단자에는 ​​실질적인 젖음이 없었다. 이러한 유형의 이미지는 실제 제조 중에 훨씬 더 일반적으로 발견된다.

그림 5는 에지 단자에서 볼 수 있는 일반적인 패드 버링(pad burring) 현상을 보여주는 QFN 하단의 광학 이미지이다. 이는 디바이스 제조 중 리드프레임의 빈약한 부품 싱귤레이션에 기인한다. 그림 6은 리플로우 후 QFN 에지의 광학 이미지이다. 그림 6 우측 대부분의 접합부는 성공적으로 만들어지지 않았으며, 다른 접합부와 비교해야 할 필요가 있다. 이는 중앙 QFN 패드에 페이스트가 과도하게 도포되었거나 부적절한 리플로우 프로파일 동안 중앙 패드에서 과도하게 보이드가 발생하여 발생했다. 이러한 조건으로 인해 리플로우 중에 QFN이 중앙 패드에서 ‘부유’하여 패키지가 정상보다 보드 위로 더 많이 올라가 리플로우 공정의 모세관 현상(capillary action)을 방해한다. 이러한 문제로 인해 측면 필렛의 솔더 품질이 변했다. QFN 중앙 패드의 문제는 시각 검사기로 볼 수 없으며 다른 요인으로 인해 에지 단자가 불량할 수도 있다. X-ray 검사를 통해 중앙 QFN 패드를 비파괴적으로 볼 수 있다.
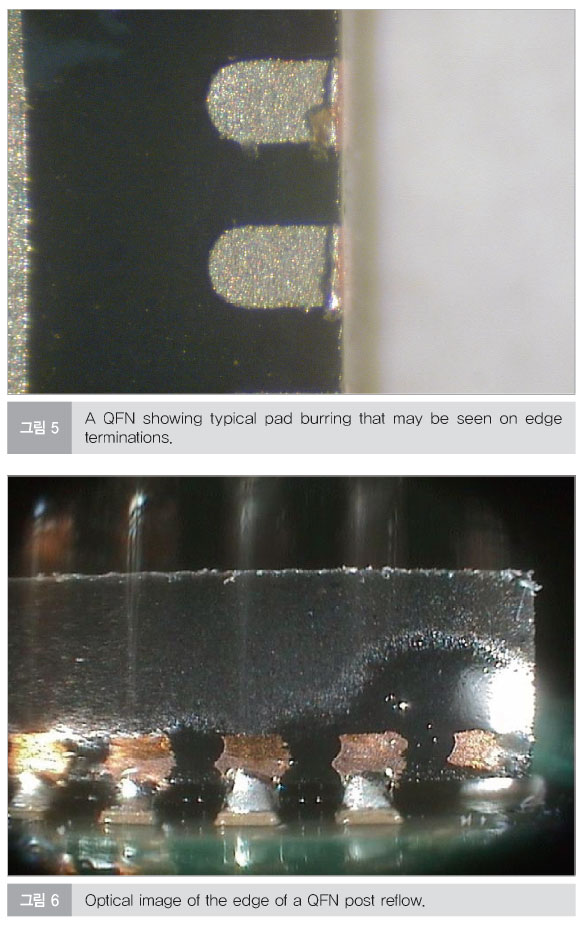
그림 7은 FPCB 상의 QFN 마이크로섹션(Microsection) 이미지이다. 중앙 패드에 페이스트가 과도하게 도포되거나 혹은 중앙 패드에 과도한 보이드가 발생하여 QFN이 ‘부유’되었다. 이로 인해 오픈 조인트가 발생했다. 이러한 불량은 부품 도금의 납땜성 또는 버링 문제로 인해 악화되었을 수 있다.
그림 8은 디바이스 하단부에 솔더 조인트가 형성되었음을 보여주는 QFN의 광학 이미지이다. 그러나 측면 단자가 젖지 않으면 조인트의 시각적 모양이 달라져 AOI 검사가 매우 어려울 수 있다. 랜드 패턴은 여전히 ​​부품 풋프린트 밖으로 확장되어야 하며 부품 아래에 설계된 패드의 길이는 금속화 끝까지 확장되어야 한다. 측면 단자의 양호한 젖음은 좋은 QFN 엣지 조인트를 만드는 데 필요하지 않지만, 존재한다면 실제 제조 환경에서 품질을 검사하는 데 큰 도움이 된다.
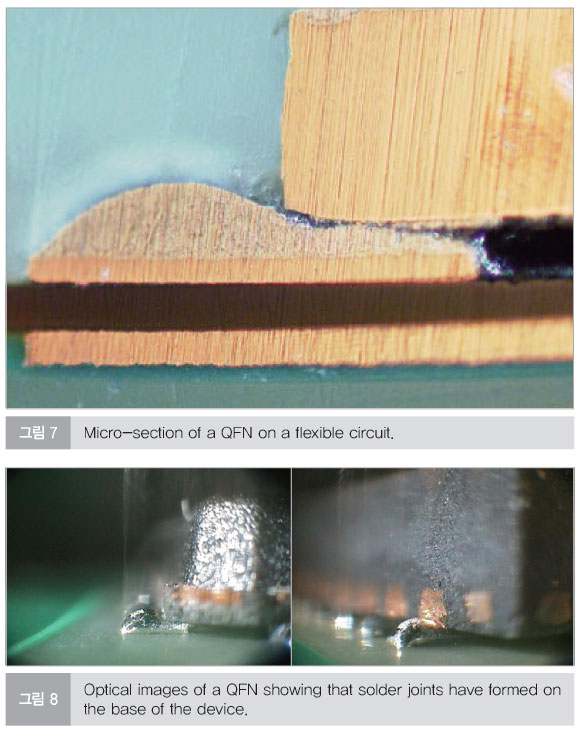
분석 - X-선 검사
광학 검사 이미지와 마찬가지로 테스트 보드는 양호한 QFN 접합부와 불량 QFN 접합부의 차이를 보여주었다(그림 9, 그림 10 참조). 결함은 대류 또는 기상 리플로우에서 QFN 패키지를 사용하는 데 따른 문제보다는 임시적인 어셈블리 라인에서 보드를 생산하려는 서두름으로 인해 발생했을 가능성이 더 크다. 양호한 접합부는 열 사이클링 후에도 양호한 상태를 유지했다. 그러나 X-ray 검사에서 명확하게 볼 수 있는 것은 모든 테스트 보드에서 보이드 형성 수준이 극적으로 다른 중앙 패드가 있었던 점이다. 이는 보드에서 사용된 리플로우 방법과 무관했으며 이러한 변화는 특히 FPCB 상의 QFN에서 두드러졌다(그림 9, 그림 10 참조).
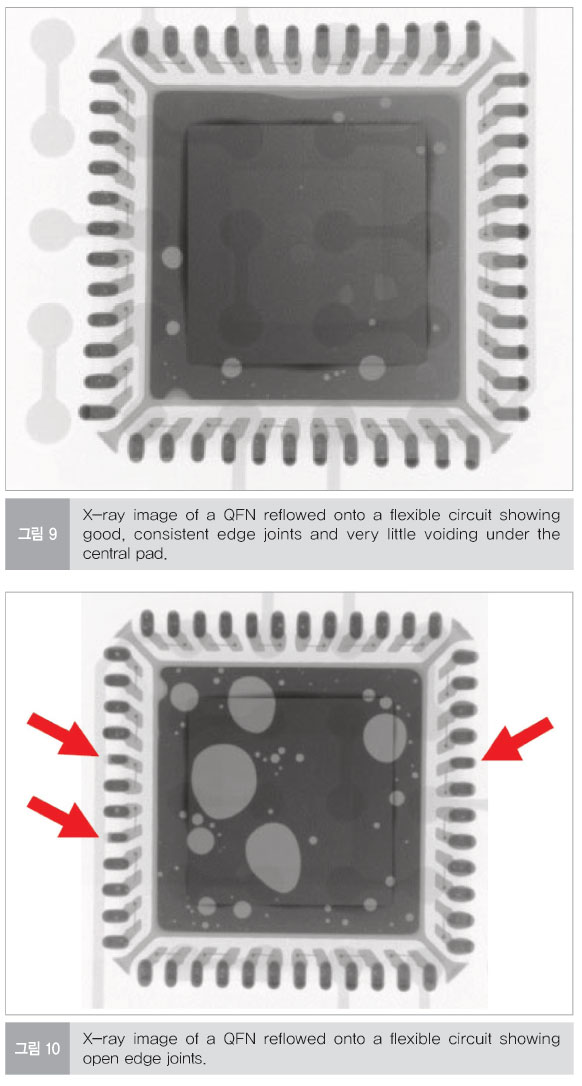
그림 6에서 보는 바와 같이, 이러한 보이드 변화의 가장 큰 원인은 ‘작업자의 경험’에 기반을 둔 프린팅 공정 설정이고, 이로 인한 솔더 페이스트 증착 변동성 때문이다. 과도한 솔더 페이스트로 인해 QFN이 패드 위로 ‘부유’해서 결과적으로 열 발산 및/또는 패키지 동작 효율성에 영향을 미칠 수 있다. 과도한 보이드 수준은 증기상에 비해 대류 리플로우 보드에서 약간 더 두드러졌다는 점에 유의해야 한다. 그러나 차이는 적었고 보이드가 거의 없거나 전혀 없는 대류 리플로우 보드가 많았다. 데이터의 불일치는 대신 PCB 솔더 마감의 습윤 효율 및/또는 스텐실 설계로 인해 발생했을 수 있다.
QFN의 광학 검사 기준
QFN에 대한 광학 검사 기준은 IPC-A-610D 문서[6]를 참조했다. 특히, Class 2 및 Class 3 제품의 경우 패드에 대한 단자의 최대 측면 오버행이 패드 너비의 최대 25%여야 한다고 규정하였다. 또한 Class 2 및 Class 3 제품의 경우, 최소 엔드 조인트 너비가 전체 패드 너비의 최소 75%여야 한다고 정의하였다(그림 11 참조).
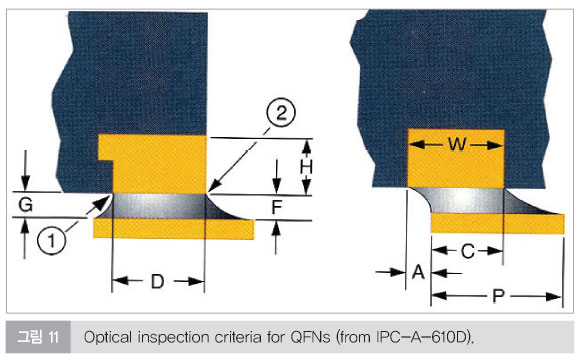
제조 시 허용 가능한 QFN 조인트와 허용 불가능한 QFN 조인트의 시각적 모양을 보다 쉽게 ​​이해할 수 있도록 작업장 검사 포스터를 활용했다.[7] 그림 12와 그림 13은 허용 가능한 QFN 에지 단자의 광학 이미지이고, 그림 14는 허용 불가능한 QFN의 이미지이다. 그림 12에서 보는 바와 같이 솔더 필렛은 설계 단계에서 패키지 너비를 넘어 확장된 패드가 통합되어야 한다. 그림 13과 같이 솔더 필렛은 단자 너비의 최소 75%까지 보여야 한다. 그림 14는 허용 불가능한 QFN 모습으로, 솔더 올라섬이 제한적으로 오픈 조인트 현상이 보이고, 패키지 또한 표면 위로 ‘부유’되어 있다.
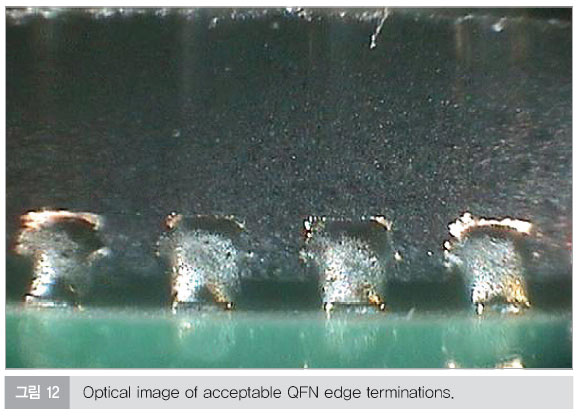
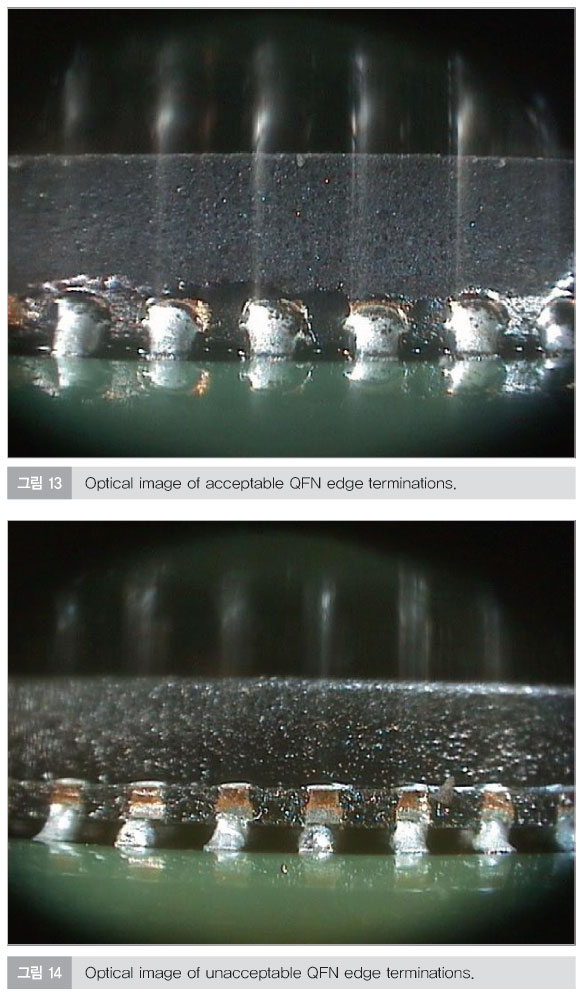
QFN의 X-선 검사 기준
IPC-A-610D에는 QFN에 대한 허용 가능한 X-선 검사 기준에 대한 명확한 권장 사항이 없으므로 다음을 지침으로 제안하였다. 생산에 사용되는 다양한 일반적인 부품에 대한 X-선 검사 지침의 자세한 내용은 참조 8에서 확인할 수 있다. 양호한 QFN과 불량 QFN의 X-선 이미지 비교는 그림 9, 그림 10 그리고 그림 15에 나와 있다. 그림 15에서는 리플로우 이후 이상적인 QFN X-선 이미지(좌)와 만족스럽지 못한 예(우)를 보여주고 있다. 만족스럽지 못한 이미지는 낮은 배율에서도 명확하게 볼 수 있었으며, 더 높은 배율이나 오블릭 앵글 구조의 X-선 시스템으로 촬영할 필요가 없었다.
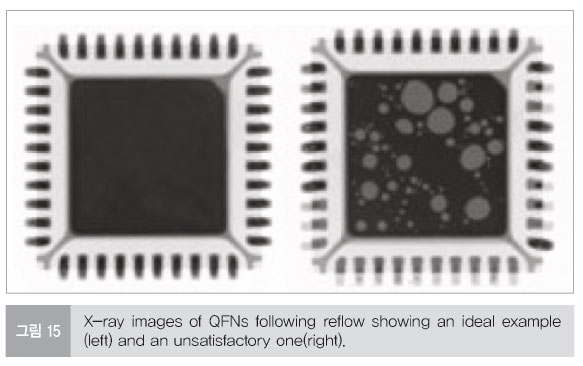
X-선 검사는 부품의 한 모서리에서 시작해야 하며, 네 면 모두에서 수행할 수 있다. 확장 랜드에 필렛이 있는지 주의해야 한다.
패드 중앙을 포함한 모든 단자의 최대 보이드 비율은 조인트 전체 면적의 20% 미만이어야 한다. 여러 개의 보이드가 존재하는 경우, 최대치가 20% 미만이어야 한다. 패드 중앙 영역의 블라인드 비아 또는 보드의 맞은 편에 솔더 마스크 캡핑이 있는 관통 비아도 보이드 형성에 기여할 가능성이 있음을 유의해야 한다. 다음의 그림에서는 QFN의 세 가지 X-선 이미지를 보여주고 있다. 그림 16. 조인트 내에 적당한 수준의 공극이 나타나는 QFN 에지 조인트의 목표 조건은 허용 가능하다. 모든 조인트가 리플로우되었다. 그림 17의 이미지는 조인트 내에 보이드가 늘어났지만, 모든 조치 수준 내에 있는 허용 가능한 조건이었다. 그림 18은 조인트에 솔더가 부족하거나 보이드가 단일 조인트의 조인트 면적의 20%를 초과하는 QFN 에지 조인트의 결함 상태를 보여주었다.
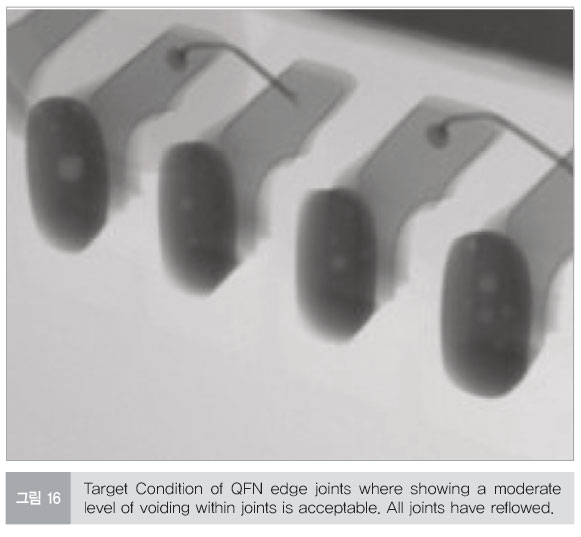
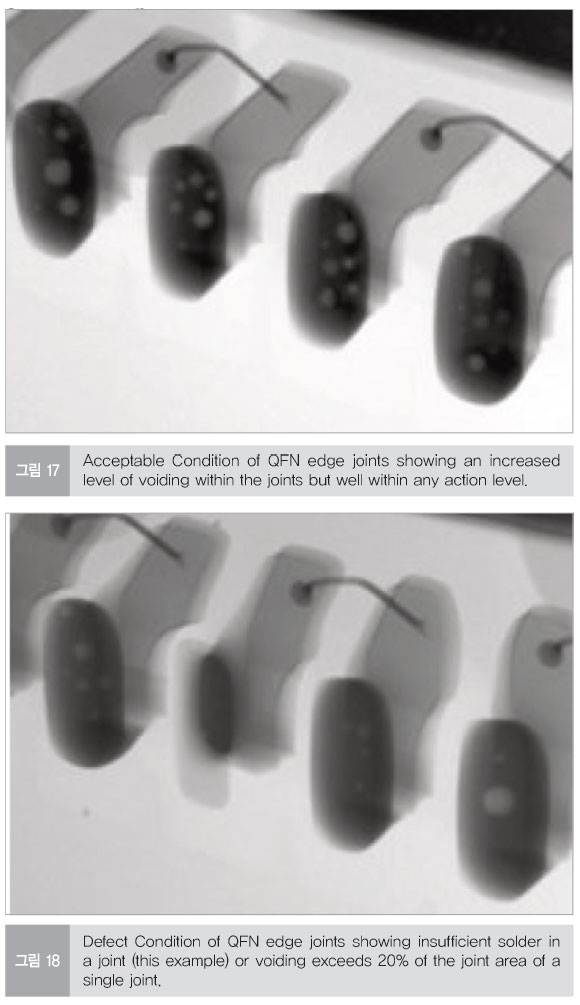
각각은 가장자리 및 중앙 단자에 대해 서로 다른 수준의 조인트 조건 허용 가능성을 나타낸다. 이는 다음과 같다;
1. 목표 조건 -X-선으로 검사했을 때 이상적인 솔더 조인트의 이미지.
2. 허용 가능한 조건 - 목표 조건으로 설정된 최대 허용 편차 수준에 있는 X-선 이미지. 이러한 조인트는 재작업이 필요하지 않지만, 목표 조건에 대한 조인트 품질을 개선하기 위해 프로세스 검토를 고려해야 함을 시사한다. 이 수준은 생산 프로세스의 최소 조건이다.
3. 결함 조건 - 허용할 수 없는 조인트를 나타내는 X-선 이미지. 이 상태의 원인을 조사하고 적용된 프로세스에 필요한 시정 조치를 취해야 한다. 이러한 조인트 상태의 가능한 재작업은 프로세스가 수정될 때까지 기다려야 한다.
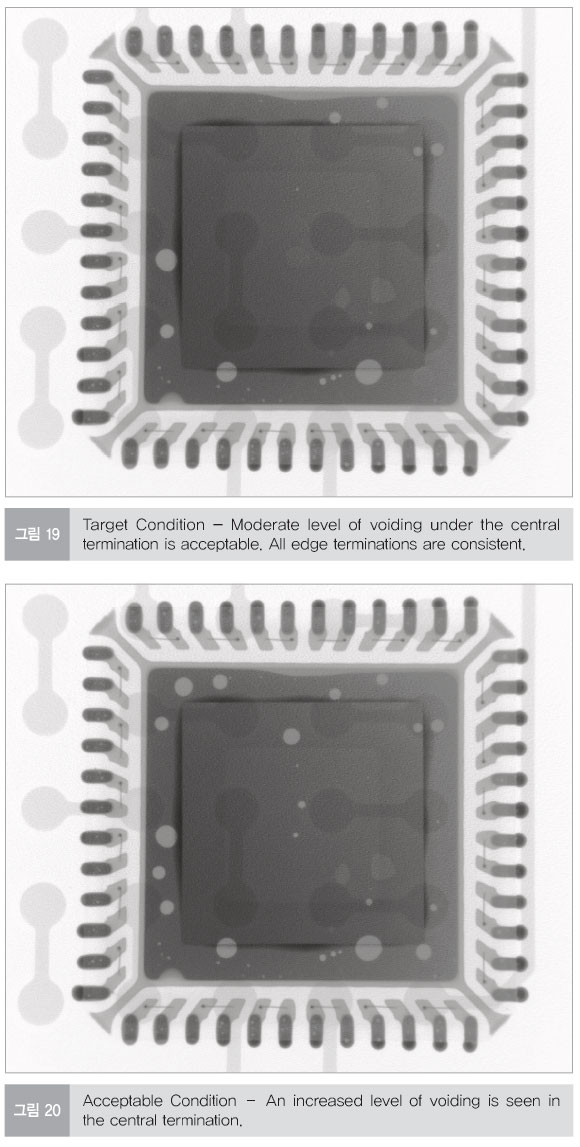
그림 19는 ‘목표 조건’으로, 중앙 단자 아래에 적당한 수준의 보이드가 나타났으나 허용 가능한 비율이였고, 모든 에지 단자는 일관된 모습을 보였다. 그림 20은 ‘허용 가능한 조건’이며, 중앙 단자에서 보이드 수준이 늘어난 것을 확인할 수 있었다. 그림 21은 ‘결함 조건’으로, 전체 수량과 개별 보이드 모두에서 과도한 수준의 보이드가 보였다. 에지 단자에서도 오픈 조인트도 나타났다.
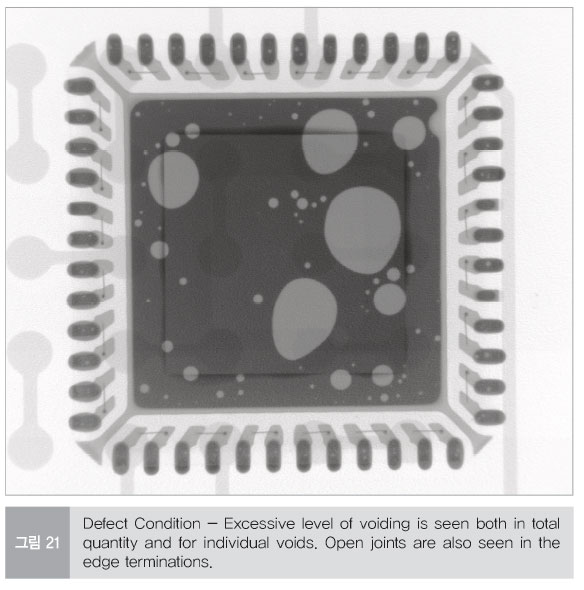
결론
설계 엔지니어가 패키지의 풋프린트 외부로 돌출형 랜드를 포함하는 경우 QFN(LGA) 또는 이와 유사한 패키지에 대한 수동 광학 검사가 가능하다. 이를 통해 눈에 보이는 솔더 필렛이 형성될 수 있다. 그러나 이러한 조인트를 수동 광학 검사하는 것은 실용적이지 않다. 따라서 적절한 공정 제어와 우수한 공정 엔지니어링 관행을 구현하는 것이 처음부터 우수한 조인트를 얻는 가장 좋은 솔루션이다.
자동 광학 검사 시스템은 설계 엔지니어가 적합한 풋프린트를 사용하는 경우 QFN 디바이스 주변에 형성된 조인트를 검사할 수 있다. 그러나 QFN의 자동 테스트를 위한 최상의 기준을 정의하는 것은 패키지 에지에 나타날 수 있는 다양한 변화로 인해 어려울 수 있다. 이러한 변화는 측면 단자의 한정된 습윤 ​​및/또는 제조 중 부품의 싱귤레이션 후 생성된 버링으로 인해 발생할 수 있다.
광학 검사 방식으로는 패드 위의 패키지 높이 변화를 확인할 수 없다. 이는 디바이스가 중앙 단자부 아래에 과도한 솔더 페이스트가 증착되거나 과도한 보이드가 발생하여 ‘부유’ 현상이 발생할 수 있다.
X-선 검사는 중앙 단자 아래의 보이드 수준을 쉽게 보여주고 측정하여 양호한 제조 공정을 빠르고 실질적으로 확인하거나 그렇지 않은지 확인할 수 있게 해 준다. 높이 변화를 직접 확인하지는 않지만, 디바이스 아래의 전도성 재료에 상당한 부피 변화가 있는 경우 X-선 이미지에서 불연속적인 밀도 차이로 표시된다. 과도한 보이드 수준도 명확하게 볼 수 있다. 이러한 관찰 결과를 함께 사용하면 패드 표면 위로 디바이스가 ‘부유’될 가능성과 사용 시 고장 가능성과 상관 관계를 알 수 있다. QFN에서 에지 단자의 밀도와 모양의 변화도 X-선 검사를 통해 빠르게 관찰할 수 있다.
REFERENCES
[1] Bernard D., “X-ray tube selection criteria for BGA / CSP X-ray inspection”, Proceedings of SMTA International, Chicago, September 2002
[2] Bernard D., “Selection Criteria for X-ray Inspection Systems for BGA and CSP Solder Joint Analysis”, Proceedings of Nepcon Shanghai, 2003
[3] Bernard, D. and Ainsworth, S., “Comparing Digital and Analogue X-ray Inspection for BGA, Flip Chip and CSP Analysis”, Proceedings of APEX, Anaheim, CA, 2004.
[4] Results from Hands-on Lead-free Experience held at Nepcon UK, Birmingham, England May 2006. See www.smartgroup.org/experience/experiencereport2006.pdf
[5] Bernard D. and Willis B., “Quality and Reliability Investigation of Printed Circuit Board Micro-Vias by X-Ray Inspection”. Published in the Proceedings of SMTA International Conference, Florida, October 2007.
[6] “Acceptability of Electronic Assemblies”, IPC document IPC-A-610D, February 2005. Available from www.ipc.org.
[7] Shop floor posters, providing examples of acceptable and unacceptable optical inspections for a range of common packages, are available from the SMTA Book Store.
[8] Bernard D. and Willis B., “A Practical Guide to X-ray Inspection Criteria & Common Defect Analysis”, Dage Publications 2006. Available through the SMTA bookshop. Originally published in the Proceedings of the SMTA International Conference, Orlando, Florida, 2007 |