PCB 제작에 몇 가지 뚜렷한 이점 가져
생산속도 & 프린팅 강도 개선 방법 연구 활발
3D 프린팅은 단순히 빠른 프로토타입 도구, 소형 플라스틱 장난감을 프린팅하는 그 이상으로 진화하기 시작했다. 기업들은 전통적인 제조 기술을 이용하여 수행할 수 없는 복잡한 부품을 제조하기 위해 3D 프린팅을 채택하기도 한다. 전기 기능의 대상물은 PCB와 경쟁할 수 있는 이점을 지니고 있다. 인쇄 회로 구조는 전자 패키징에 대한 새로운 접근 방식이 될 것이다. 많은 기업들이 비용 절감 차원에서 어셈블리 공정 단축, 전자 제품 사이즈 축소를 바라고 있다. 이는 어려운 일이지만 인쇄 회로 구조와 전자 장치를 하나의 모놀리식 유닛으로 프린팅하는 구조는 많은 잠재력을 가지고 있다.
인쇄 전자기기는 기술이 성숙해짐에 따라 더 많은 의미를 부여하는 익숙한 용어가 되었다. 플렉시블한 전자기기는 때때로 이 기술의 하부 개념으로 언급되고 있으며, 롤투롤(roll to roll) 프로세스가 가용한 인쇄 방식 중 하나가 되었다. 인쇄 전자기기는 성능이 향상되고 있으며, PCB와 직접 경쟁하는 많은 애플리케이션을 가지고 있다. 롤투롤의 장점은 생산 속도, 대형 영역 가능 그리고 비용 절감이다. 이 기술이 성숙해짐에 따라 높은 프로파일의 3D 프린팅과도 통합되어 가고 있다. 3D 프린팅은 단순히 빠른 프로토타입 도구, 소형 플라스틱 장난감을 프린팅하는 그 이상으로 진화하기 시작했다. 기업들은 전통적인 제조 기술을 이용하여 수행할 수 없는 복잡한 부품을 제조하기 위해 3D 프린팅을 채택하기도 한다. 3D 프린팅과 인쇄 전자기기의 결합은 새로운 제품을 만들 가능성이 높으며, 특히 대상물을 전기적인 기능을 부여할 수도 있다.
전기 기능의 대상물은 PCB와 경쟁할 수 있는 이점을 지니고 있다. 인쇄 회로 구조는 전자 패키징에 대한 새로운 접근 방식이 될 것이다. 많은 기업들이 비용 절감 차원에서 어셈블리 공정 단축, 전자 제품 사이즈 축소를 바라고 있다. 이는 어려운 일이지만 인쇄 회로 구조와 전자 장치를 하나의 모놀리식 유닛으로 프린팅하는 구조는 많은 잠재력을 가지고 있다. 어셈블리에서 인간의 접촉을 줄일 것이다. 전자 장치와 대상물이 인쇄되기 때문이다. 모놀리식 디바이스이기 때문에 제품의 내구성이 향상될 것이다. 와이어, 솔더 그리고 커넥터를 없앨 수 있고, 디바이스를 더욱 작게 만들 수 있다. 이것은 PCB와 마이크로일렉트로닉 패키징의 미래가 될 잠재성을 가지고 있다. 본고에서는 인쇄 회로 구조의 작동 시연, 장애물 및 3D 인쇄 전자기기의 잠재적인 미래를 보여줄 것이다.
SLA(Stereo Lithography Apparatus) 방식의 3D 프린팅은 1980년대 초반부터 진행되어 왔지만 많은 형태로 발전해 왔다. 본고에서는 용융수지압축조형(fused deposition modeling, FDM)이라고도 하는 FFD(fused filament deposition) 방식에 초점을 두고 있다. 최근에는 전자 인쇄에 FDM 인쇄를 결합하여 3D 프린팅 전자기기를 만들었다. 이러한 3D 프린팅의 진화로 PCS(Printed Circuit Structures)는 PCB에 비해 뚜렷한 장점을 가질 수 있다. PCB에 있는 많은 부품들을 PCS에 통합할 수 있다. PCS는 안테나[1], [2], 집중정수 소자(lumped component)[3] 그리고 심지어 커넥터[4] 등과 같은 전체 매립형 소자를 포함할 수 있는 것으로 여겨지고 있다. 대상물에 부착할 PCB를 생성하는 대신 회로를 대상물의 일부로 통합하여 인쇄할 수 있다. 이 인쇄 방법은 마이크로-디스펜싱 펌프, 가열 압출 헤드, 픽-앤-플레이스 헤드 그리고 마이크로-밀링, 드릴링 및 연마 헤드 등을 포함한 다양한 공구 툴 헤드의 사용을 결합한 DDM(Direct Digital Manufacturing) 기계를 활용할 수 있다.
PCB는 많은 설비의 활용이 필요하고, 마스킹이 요구되지만, PCS는 단일 기계 내에서 전체 제작이 이뤄지기 때문에 완전 자동화를 할 수 있다.[5], [6] PCS가 장점을 지니고 있지만, 아직 극복해야 할 몇 가지 장애물, 즉 제작 속도와 최종 부품 강도가 남아 있다.
FDM 방식의 3D 프린팅은 느린 것으로 유명하다. 이는 기존 데스크톱 3D 프린터의 낮은 체적 압출 속도 때문이다. 압출 비율을 결정하는 요소가 많이 존재한다. 이들 중 일부에는 노즐 직경, 노즐 온도, 베드 온도(bed temperature), X-Y 이동 속도, 재료 및 압출 모터까지 포함시킬 수 있다. 이들 모두가 압출된 총 필라멘트에 영향을 미치지만, 노즐 직경이 압출 속도의 주요 결정 요인이다. 레이어 높이, 압출 폭 및 인쇄 속도는 모두 노즐 직경을 기준이다. 그래서 개선을 통해서 가장 많은 이점을 얻을 수 있는 인쇄 공정의 측면이다.
표준 프린팅 노즐은 내부 직경이 0.4mm이다. 이는 설비와 원하는 인쇄 품질에 따라 최대 80~100mm/s의 인쇄 속도를 얻을 수 있다. 전체 인쇄 시간을 단축을 위해 노즐 크기를 늘릴 수 있지만 품질 저하를 벗어나기 어렵다. 이러한 품질 저하는 거친 표면 마감, 둥근 모서리 그리고 부정확한 치수 등과 같은 사항일 수 있다. 대구경 노즐은 작은 대상물을 프린팅 할 때 작은 지형이 문제가 될 수 있기 때문에 또한 사용이 제한적이다.
대구경 노즐 선택의 품질 관련 단점이 매력적이지 않지만 사용이 가능할 수 있다. ‘스파게티(Spaghetti)’ 인쇄라고 불리는 인쇄 방법은 압출 속도를 크게 높이고 인쇄 시간을 단축하기 위해 개발되었다. 이 공정은 특수 설계된 1.75mm 노즐로 필라멘트를 인쇄한 다음 필요에 따라 밀링 헤드를 사용하여 고품질의 표면 처리를 가하고, 인쇄를 치수에 맞춘다. 속도 실험은 0.4mm 노즐을 사용한 ASTM D638 타입 V 인장시편 인쇄의 인쇄 속도와 ‘스파게티’ 방식을 비교해 설정하였다. 두 종류의 인장시편을 인쇄하였다; 하나는 0°의 인필(infill) 비율이고, 다른 하나는 수평에서 90°의 인필(infill)이다. 이 샘플들은 인장 시험을 하지 않기 때문에 테두리 없이 인쇄하였다. 이 샘플 유형은 모두 두께 1.0mm이며 노즐 온도 235℃ 및 베드 온도(bed temperature) 50℃로 인쇄하였다. 그림 1과 그림 2에서 보이는 테두리는 치수를 나타내는데 사용하였다.
0.4mm 노즐로 인쇄했을 때 각 인장시편은 4분과 24초에 인쇄가 완료되었다. 스파게티 방식을 사용했을 때, 각 인장시편은 총 1분과 58초 시간이 평균이었다. 실제 3D 프린팅 부문이 32초 밖에 걸리지 않았다. 이 실험은 25번 반복했다. ‘스파게티’ 방식이 대상물을 완성하는데 2배 이상 빨라졌을 뿐만 아니라 밀링의 최종 표면처리도 기존 인쇄 시편의 그것보다 더 훨씬 뛰어났다.
전자기기 일부분을 인쇄할 때 전도성 물질이 도포되기 위한 매끄러운 표면이 필요하기 때문에 이는 PCS에 큰 이점이 된다. 일반적으로 전도성 물질의 인쇄가 성공하려면 FDM 기판 레이어는 100미크론 정도의 작은 노즐로 인쇄되어야 할 필요가 있다. 전도성 물질을 정확하게 인쇄하기 위해서는 표면이 매끄러워야 한다. 이를 위해 정확한 설계가 필요하다. 윤곽 인쇄를 할 수 있는 표면 매핑이 가능하지만 매끄러운 표면이 선호된다. 여러 개의 열가소성 플라스틱을 서로 인쇄했을 때, 이상적인 표면을 제공하기도 한다.
매끄러운 표면은 픽-앤-플레이스(pick-and-place)를 활용한 USB 칩의 레벨 배치를 가능하게 한다. 그런 다음 전도성 페이스트를 도포하여 칩에서 USB의 패드를 연장시켰다. 다음으로, 폴리카보네이트 쉘(polycarbonate shell)은 도포될 에폭시용 컵 모양으로 원형 부분의 둘레 주위에 인쇄된다. 일단 경화되면 에폭시는 부드럽게 으깨진다. 이는 다중 재료, 다중 프로세스 현장 PCS 제조의 작은 데모이다.
인쇄 가능한 융합 필라멘트 범주는 ABS(acrylonitrile butadiene styrene)와 같은 내구성 있는 재질에서부터 유연한 TPE(thermoplastic elastomers) 및 FST 등급의 ULTEM까지 다양하다. 이들 재료에는 일장일단이 있다. ABS의 높은 충격 강도 혹은 ULTEM의 화학적 및 온도 안정성과 상관없이 특정 애플리케이션에 적합한 재료를 선택하면 성공 여부를 판단할 수 있다. 그러나 FDM 인쇄 부품은 사출 성형과 같은 다른 제조 방법보다 강도가 훨씬 떨어진다.[7] 이는 3D 인쇄 부품의 강도가 레이어-투-레이어 표면 접착, 사이드-바이-사이드 프린트 라인의 접착 그리고 인쇄 방향뿐만 아니라 재료 자체의 기계적 특성에 의존하기 때문이다. 벌크 재료 특성에 비해 인쇄된 부품의 전반적인 강도를 감소시키는 3D 인쇄의 또 다른 측면은 인쇄 공정 중에 부품에 유입되는 보이드(void)의 존재이다.
그림 7과 그림 8에서 보는 바와 같이, 사이드-바이-사이드 라인의 중첩이 있는 곳에서 보이드를 볼 수 있었다. 이는 인쇄된 라인의 모서리가 원형이기 때문이다. 보이드를 없애기 위해 객체의 인쇄 경로 생성에 중첩 요인을 입력한다. 이렇게 하면 라인을 근접하게 그릴 수 있어서 어느 정도 보이드를 최소화할 수 있다. 높은 중첩 요인이 지정될 때 함께 쥐어짜지는 재질은 어딘가로 가야함으로 위쪽으로 옮겨진다. 이것은 최상 레이어에 있는 경우 거친 표면 처리를 생성할 것이고, 전체 인쇄물에 콤파운드가 허용되면, 총 높이 치수를 벗어날 수 있다. 0.4mm 노즐로 인쇄할 때, 비록 작아도 많은 보이드들이 대상체에 유입된다. 스파게티 인쇄 레이어에 존재하는 일부 보이드가 크지만 0.4mm 노즐로 인쇄된 부품의 전체 보이드 면적이 더 넓다. 이러한 보이드는 인쇄된 시편의 ~10%의 인장 강도 차이의 원인이 된다(그림 9 참조).
인쇄 방향은 인쇄 부품의 강도에 중요한 역할을 한다.[7], [8] 구조적인 부분을 인쇄할 때 최종 부품이 겪게 될 힘의 방향으로 레이어가 인쇄되는 것이 일반적이다. 힘의 방향으로 인쇄하는 것이 중요한 이유를 예시하기 위해 인장 시험편을 힘 방향 (0° 시편) 및 힘 방향 (90° 시편)에 수직으로 인쇄했다. 0° 시편은 평균 47.028MPa UTS에서 파단한 반면 90° 시편은 13.572MPa의 훨씬 낮은 힘에서 파단되었으며 강도는 ~ 72% 감소했다. 관찰된 UTS의 차이는 극단적이고 인쇄 방향이 강도에 미치는 영향을 보여주었다. 이 차이는 힘의 방향이 90° 시편의 인쇄 방향에 수직이기 때문에 라인들 간의 접착력이 재료 자체보다는 저항력을 제공하는 유일한 것임을 다시금 알 수 있었다.
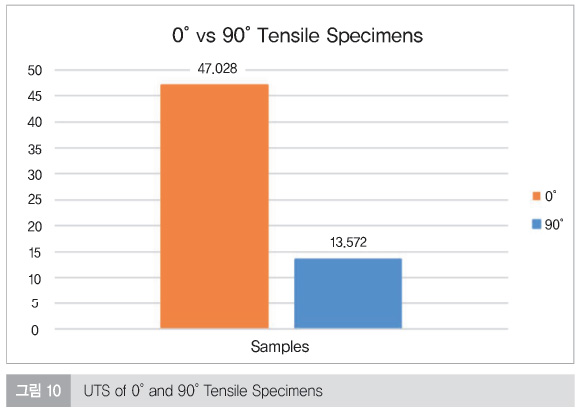
가장 이상적인 것은, 특정 애플리케이션에서 여러 방향의 힘이 존재할 수 있기 때문에 모든 방향에 강도가 있을 것이다. 3D 인쇄에서는 일반적으로 0° 또는 90° 채우기 프린트가 아니라 여러 방향으로 힘을 제공하기 때문에 45°로 프린트한다.[7], [8] 그러나 이는 오로지 힘의 방향으로만 인쇄하는 것과 비교할 때 전반적인 인장 강도를 감소시키기 때문에 절충안이라고 할 수 있다. 게다가, 힘의 방향은 Z-방향인 경우에 동일한 문제를 발생한다. 레이어 접착이 부품 파손 전에 얼마만큼의 힘을 받을 수 있는지를 결정하는데 중요한 요인이기 때문이다. 레이어 및 사이드-바이-사이드 라인 접착은 3D 인쇄 측면이기 때문에 유지할 수 있는 힘을 증가시키는 방법이 필요하다. 이렇게 하기 위해 ‘리플로우’ 실험을 수행하였다. 방법은 온도 제어 레이저를 사용하여 이미 인쇄된 플라스틱을 가열하여 ‘리플로우’하였다. 30W 레이저가 기계에 장착되어 90° 인장 부분 바로 위에 놓았다. 레이저가 시편 표면을 가로 질러 이동하는 동안, 비접촉 온도계를 사용하여 플라스틱 부품의 온도가 상승되어 120℃로 유지하였다. 레이저는 부품 중간 부분을 3번 통과하여 플라스틱을 리플로우하고 층간 접착을 증가 시켰다.
이러한 ‘리플로우’된 샘플의 인장 테스트는 처리되지 않은 샘플의 평균 13.572MPa UTS, 58% 증가에 비해 평균 21.574 MPa UTS를 산출되었다.
강도 증가가 훨씬 향상되었지만, 힘의 방향으로 인쇄된 충전물 부품의 UTS 아래에 여전히 있다. 이는 여러 방향으로 힘을 발휘하는 강력한 부품을 인쇄할 수 있기 때문에 중요하다. 본질적으로 사이드-바이-사이드 라인 접착력을 증가시키기 위해 수행되었지만, 레이어 접착에도 적용될 수 있다. 레이저를 인쇄 헤드 앞에 놓음으로써, 이전에 증착된 재료의 레이어가 재가열되는 동시에 위에 인쇄되어 더욱 견고한 부품이 만들어진다. 이렇게 하면 보이드가 제거를 통한 레이어 접착력이 증가하여 전반적인 부품이 강력해진다.
오늘날 PCB는 최적화되고 유비쿼터스화되어 있다. 대량 생산이 가능하고 비교적 신속하게 생산되며 검증되고 신뢰할 수 있는 제품이 되었다. 하지만 한계가 있다. 공정 집약적이며 경제적인 일회용 제품이 없어서 많은 낭비를 초래하여 특성에 따라 제조비용 추가가 필요하다. 인쇄 회로 구조는 PCB 및 3D 인쇄 산업계의 진화이다. 그들은 PCB에 비해 몇 가지 뚜렷한 이점을 가지고 있다. 즉, DDM 프로세스로 인해 공정 단계를 단축하고, 일회용 및 커스터마이징화가 쉽고, 주로 추가적인 작업이기에 낭비가 거의 없다. 그러나 아직 몇 가지 장애물이 존재한다. 오늘날 PCS는 작업 속도가 빠르지 않아서 아직 대량 생산에서는 어려움을 겪고 있다. 가공 부품의 강도는 PCS의 또 다른 장애물이다. 3D 인쇄 부품은 벌크 특성만큼 강하지 않으므로 PCS 설계를 고려해야 한다. 본고에서 설명된 방법을 통해 두 가지 문제를 해결하고 개선하고자 하였다. ‘스파게티 (Spaghetti)’ 방식의 인쇄를 사용하여 2배 이상의 속도가 향상되었고 더 강하고 매끄러운 부품을 얻을 수 있었다. 강도를 높이는 또 다른 방법은 레이저를 사용하여 이미 인쇄된 플라스틱을 리플로우하여 사이드-바이-사이드와 레이어 접착력을 향상시키는 것이다. 이러한 방법을 결합하면 보다 강력하고 내구성이 뛰어난 인쇄 회로 구조를 훨씬 더 빠르게 제작할 수 있다.
REFERENCES
[1] Deffenbaugh, Paul, et al. “Fully 3D Printed 2.4 GHz Bluetooth/Wi-Fi Antenna.” International Symposium on Microelectronics. Vol. 2013. No. 1. International Microelectronics Assembly and Packaging Society, 2013.
[2] Nassar, Ibrahim T., et al. “A high efficiency, electrically-small, 3-D machined-substrate antenna fabricated with fused deposition modeling and 3-D printing.” 2014 IEEE Radio and Wireless Symposium (RWS). IEEE, 2014.
[3] Church, Kenneth H., et al. “Advanced printing for microelectronic packaging.” submitted for publication in IPC APEX Expo (2014).
[4] Arnal, Nicholas, et al. “3D multi-layer additive manufacturing of a 2.45 GHz RF front end.” 2015 IEEE MTT-S International Microwave Symposium. IEEE, 2015.
[5] Church, Kenneth H., et al. “Printed circuit structures, the evolution of printed circuit boards.” IPC APEX EXPO Conference Proceedings, San Diego, CA, Feb. 2013.
[6] Deffenbaugh, Paul. 3D printed electromagnetic transmission and electronic structures fabricated on a single platform using advanced process integration techniques. Ph. D. dissertation, Elect. & Comput. Eng., UTEP, El Paso, TX, 2014.
[7] Ahn, Sung-Hoon, et al. “Anisotropic material properties of fused deposition modeling ABS.” Rapid Prototyping Journal 8.4 (2002): 248-257.
[8] Torrado, Angel R., and David A. Roberson. “Failure analysis and anisotropy evaluation of 3D-printed tensile test specimens of different geometries and print raster patterns.” Journal of Failure Analysis and Prevention 16.1 (2016): 154-164.