로진 및 안티-크랙 조성 제품
테스트 결과 산업계의 다양한 조건 충족
솔더 합금의 경우, 많은 발전이 이뤄져 왔으며 현재도 개발이 진행 중에 있다. 솔더페이스트 플럭스의 경우, 자동차 및 다른 높은 신뢰성 애플리케이션용 플럭스는 고온 및 고습의 분위기에서도 신뢰할 수 있는 절연 저항을 가지고 있어야 한다. 이러한 요구 사항을 충족시키기 위해 자동차 및 다른 높은 신뢰성 제품군 제조업체에서의 엄격한 표면 절연 저항 및 전자-마이그레이션 기준을 설정하였고, 신뢰성을 더욱 끌어올리도록 극한 환경에서도 크랙을 억제시킬 수 있는 ‘크랙-프리’ 타입의 플럭스 페이스트가 개발되어 왔다. 크랙-프리 플럭스 잔사는 플럭스 잔사 크랙을 통해 유입된 습기로 인한 전기 화학적 마이그레이션을 예방하는데 도움을 준다. 또한, 크랙-프리 잔사는 컨포멀 코팅 공정 사용 없이 어셈블리가 필요한 특정 애플리케이션에서 하나의 컨포멀 코팅 타입으로 역할을 수행할 수도 있다.
추상
최근 몇 년 동안 점점 더 많은 수의 전자 디바이스가 자동차 및 다른 높은 신뢰성의 최종 제품군에 통합되면서 이들 디바이스의 신뢰성을 높이는 것이 과제가 되었다. 디바이스의 패키지 사이즈는 컨수머 산업계에 의해 크게 좌우된다. 자체 사이즈 소형화는 어셈블리를 더욱 어렵게 만들고 있다. 자동차 및 높은 신뢰성의 전자 제품군의 경우, 사람의 생명과 안전에 직접적으로 연관되어 있기 때문에 높은 신뢰성을 확보하는 것이 최우선 과제이다. 이러한 과제에는 적당한 솔더 합금을 선택하는 것과 솔더페이스트 플럭스의 우수한 신뢰성을 가지는 것이 포함되어 있다.
솔더 합금의 경우, 많은 발전이 이뤄져 왔으며 현재도 개발이 진행 중에 있다. 솔더페이스트 플럭스의 경우, 자동차 및 다른 높은 신뢰성 애플리케이션용 플럭스는 고온 및 고습의 분위기에서도 신뢰할 수 있는 절연 저항을 가지고 있어야 한다. 이러한 요구 사항을 충족시키기 위해 자동차 및 다른 높은 신뢰성 제품군 제조업체에서의 엄격한 표면 절연 저항 및 전자-마이그레이션 기준을 충족하고, 신뢰성을 더욱 끌어올리도록 극한 환경에서도 크랙을 억제시킬 수 있는 ‘크랙-프리’ 타입의 플럭스 페이스트가 개발되어 왔다. 크랙-프리 플럭스 잔사는 플럭스 잔사 크랙을 통해 유입된 습기로 인한 전기 화학적 마이그레이션을 예방하는데 도움을 준다. 또한, 크랙-프리 잔사는 컨포멀 코팅 공정 사용 없이 어셈블리되어야 하는 특정 애플리케이션에서 하나의 컨포멀 코팅 타입으로 역할을 수행할 수도 있다.
IPC 및 JIS(Japan Industrial Standard) 규격에 부합한 테스트 보드를 사용하여 다양한 산업계의 전기 화학적 마이그레이션 및 이슬 테스트(dew tests) 표준규격에 근거를 두고 플럭스의 신뢰성을 테스트하기 위한 실험을 진행하였다. 플럭스 잔사는 1,000 사이클 동안 -30℃에서부터 80℃까지의 예비-조건 이후 열사이클링을 가속하였음에도 크랙의 조짐이 없음을 나타냈고, 이어서 테스트 보드에 사용된 다양한 보드 라인폭과 간격에서 전기 화학적 마이그레이션의 증거가 없었다. 개발된 솔더페이스트가 대량 생산구조에 적합하다는 결과를 보고하기 위해 프린팅, 젖음, 보이드 및 리플로우 테스트를 실시하였다.
서문
자동차 및 기타 높은 신뢰성이 요구되는 애플리케이션의 경우, 납땜된 솔더페이스트 내의 플럭스는 고온 및 고습의 분위기에서도 신뢰할 수 있는 절연 저항을 가져야 한다. 열 사이클링과 같은 극한의 환경에서, 납땜된 솔더페이스트 플럭스 잔사에 크랙이 생길 수 있으며, 이는 고습도 환경에서 물이 침투하여 그림 1과 같은 전기 화학적 마이그레이션 신뢰성과 같은 문제가 발생할 수 있다.
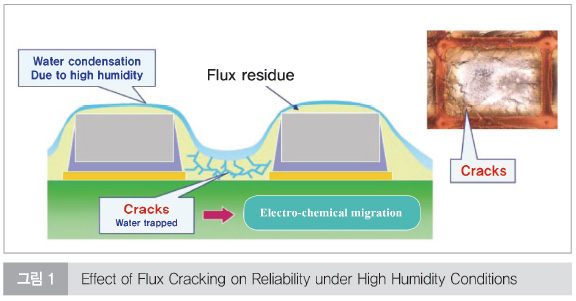
열사이클 동안 납땜된 솔더페이스트의 크랙을 예방하기 위해 플럭스에 첨가제를 추가하는 것은 습한 환경에서 수분의 침입을 감소시킬 것이다. 또한 산업계의 엄격한 표면 절연저항과 전기 화학적 마이그레이션 테스트 기준을 충족시키는데 도움을 주기에 더욱 신뢰할 수 있는 ‘크랙-프리’ 플럭스 타입을 제작하는데 일조한다. 크랙-프리 플럭스 잔사는 플럭스 잔사 틈을 통해 유입되는 습기로 인해 유발되는 전기 화학적 마이그레이션을 예방하는데 도움을 줄 수 있다. 크랙-프리 플럭스 잔사는 또한 컨포멀 코팅 역할을 수행할 수도 있다. 컨포멀 코팅 공정 없이 어셈블리해야 하는 특정 애플리케이션에서 하나의 옵션사항이 될 수 있다. 하부 섹션에서는 개발된 크랙-프리 잔사 솔더페이스트를 테스트할 때 수행된 작업들을 설명한다.
실험
열사이클 후 리플로우 플럭스 잔사의 신뢰성
첫 번째 평가는 개발된 솔더페이스트가 열사이클 조건 이후에 크랙이 발생하지 않았음을 확인하는 것이었다. 개발된 크랙-프리 Type 4 파우더 크기의 Sn3Ag0.5Cu 무세척 Paste A와 ROL0 플럭스 타입 제품을 리플로우하였고, 플럭스 잔사는 -30℃~+80℃의 범위에서 60분 주기로 1,000 사이클 동안 열 사이클링 테스트를 실시했다.
OSP 표면처리된 FR4 재질의 보드를 이번 테스트에 사용하였다. 페이스트의 프린팅 동안 스텐실의 두께는 0.15mm이었고, 레이저절단 방식으로 스텐실 개구가 제작된 제품을 이용하였다. 스텐실 개구는 보드 패드에 100%의 개구부를 가지도록 제작하였다. 보드 상에 리플로우된 부품은 0.5mm 피치의 QFP이었고, 리플로우된 보드 패드 치수는 1.0mm 폭 패드, 패드 간의 간격은 0.15mm이었다.
페이스트의 리플로우는 대기 분위기의 열풍 대류 오븐에서 실행하였다. 237℃의 피크온도에 100초 동안 130℃에서 180℃까지 예열하는 리플로우 프로파일을 적용하였다(그림 2 참조).
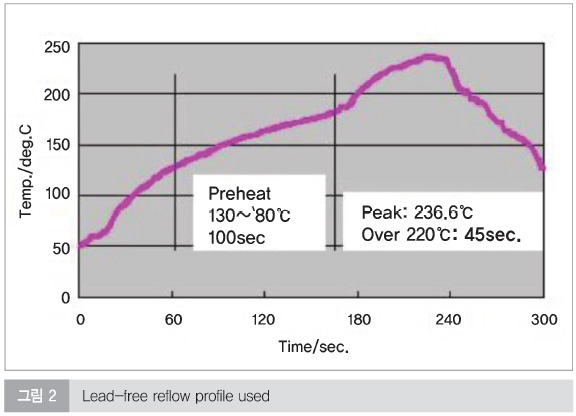
리플로우된 페이스트의 듀(Dew) 테스트 방법 (A)
크랙-프리 솔더 Sn3Ag0.5Cu Paste A와 기존 솔더 Sn3Ag0.5Cu Paste B는 그림 3과 같은 IPC-B-25(E pattern)을 이용해 산업계의 dew 테스트 방법 (A)이 수행되었다. 라인의 폭과 간격은 모두 0.318mm로 하였다.

페이스트 프린팅을 위한 스텐실 두께는 0.1mm로 하였다. Dew 테스트 방법 (A)는 30%RH~95%RH의 습도, 10℃~80℃의 온도 환경을 적용하였다. 30회의 사이클링을 실시하였다. 테스트 동안의 인가 전압은 50V이었고, 측정 전압은 100V이었다. Dew 테스트 방법 (A)의 온도 및 습도 프로파일은 그림 4에 보여주고 있다. 생산 현장에서의 에이징(aging) 영향을 확인하기 위해 dew 테스트 이전에 1,000 사이클 동안 -30℃~+80℃의 온도 사이클 시험을 실시하였다. 온도 사이클 테스트를 수행함으로써 잔사물에서의 크랙이 더욱 촉진되기 때문에 더 엄격한 테스트 조건으로 설정하였다.
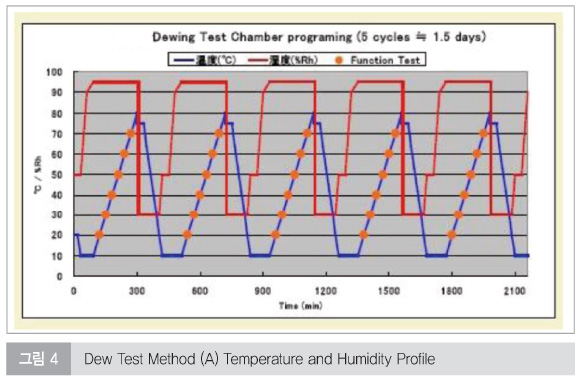
리플로우된 페이스트의 듀(Dew) 테스트 방법 (B)
크랙-프리 솔더 Sn3Ag0.5Cu Paste A도 그림 3과 같은 IPC-B-25(E pattern) 테스트 보드를 사용하여 dew 테스트 방법 (B)을 실시했다. 페이스트를 인쇄하기 위한 스텐실 두께는 0.1mm로 하였다. Dew 테스트 방법 (B)는 온도 25℃~55℃, 습도 25%RH~93%RH 환경의 IEC 60068-2-30 테스트 방법을 준수했고, 온도 사이클링을 6회 실시했다.
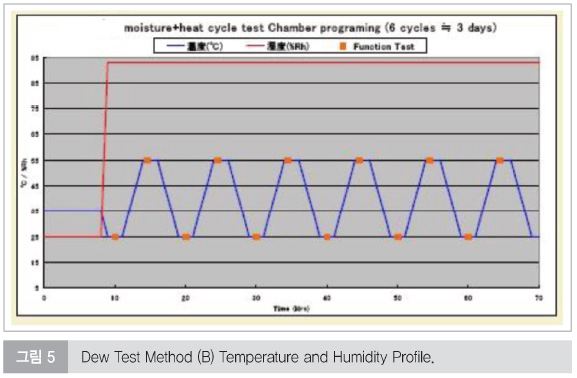
시험 중 인가 전압은 100V의 측정 전압을 지닌 50V로 설정하였다. Dew 테스트 방법 (B)의 온도 및 습도 프로파일은 그림 5에 나와 있다.
리플로우된 페이스트의 전형적인 고온/습도 SIR 테스트
크랙-프리 Sn3Ag0.5Cu Paste A를 그림 6에 표시된 0.318mm 너비 라인과 0.318mm 공간 라인을 가진 JIS comb pattern 테스트 보드에 적용하여 전형적인 고온/습도 SIR 테스트를 실시하였다. 0.25mm, 0.2mm 및 0.175mm를 포함하는 폭과 간격에서도 크랙-프리 Paste A의 특성을 평가하였다.
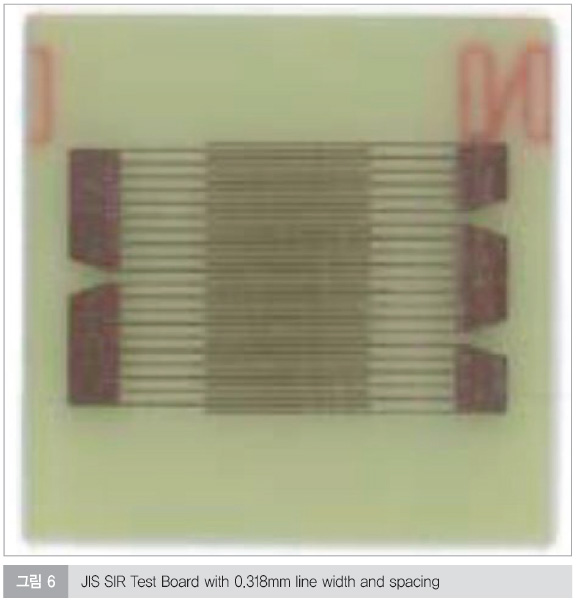
페이스트 인쇄용 스텐실 두께는 0.1mm로 하였다. 기존의 고습/고온 SIR 테스트는 습도 85%RH에서 100시간 동안 85℃의 온도 환경에서 진행하였다. 시험 중 인가 전압은 50V이고, 측정 전압은 100V로 설정하였다.
연속적인 프린트성 페이스트 테스트
크랙-프리 Paste A는 레이저 컷 스텐실 개구(fine cut stencil apertures)를 사용하여 0.15mm의 스텐실 두께를 가진 제품을 활용해 프린팅 테스트를 수행하였다. 생산용 프린터는 60°의 각도의 금속 스퀴지를 사용하여 페이스트를 인쇄했다. 프린팅 속도는 0.4mm 피치 QFP 패드와 0.35mm 직경 패턴을 평가하는 테스트 보드에서 40mm/sec로 하였다. 페이스트 측정은 SPI 장비를 통해 수행하였다.
페이스트의 점도 변화 인쇄 테스트
크랙-프리 Paste A는 24시간 동안 밀봉된 스텐실 챔버의 솔더 페이스트를 프린팅(반죽)함으로써 점도 테스트를 실시하였다. 시간의 경과에 따른 특정 점도 변화를 측정하기 위해 이러한 조건을 설정하였다. 사용된 금속 스퀴지 블레이드는 300mm의 프린팅 스트로크, 30mm/sec의 스퀴지 속도로 하였고, 각도를 60°로 하였다.
솔더 파인 패턴 젖음/리플로우 테스트
크랙-프리 Paste A는 또한 그림 7에서 보여준 테스트 보드를 사용하여 젖음 리플로우 테스트를 진행하였다.
FR-4 재질의 테스트 보드는 OSP 보드 표면 마감처리가 되었다. 페이스트 프린팅용 스텐실 두께는 0.15mm이었으며, 보드 패드에 100% 개구부가 매칭되는 레이저 컷 스텐실 개구로 제작되었다. 평가된 보드 패드 크기는 0.35mm 직경이었고, 테스트된 부품은 100% 주석 코팅을 가진 1005R 칩 부품을 사용하였다. 그림 2에서 보는 바와 같이 리플로우는 대기 분위기의 열풍 대류 오븐에 100초 동안 130℃~180℃ 예열, 237℃ 피크 온도, 45초의 220℃ 타임 오버의 리플로우 프로파일을 적용하였다.
보이드 / 리플로우 테스트
그림 8에서 보여준 테스트 보드와 부품들을 이용하여 크랙-프리 Paste A의 보이드/리플로우 테스트도 실시하였다.
FR-4 재질의 테스트 보드는 OSP 보드 표면 마감처리가 되었다. 페이스트는 보드 패드에 대한 100%의 스텐실 개구부를 지닌 0.15mm 두께의 레이저 컷 스텐실로 제작된 스텐실을 통해 프린팅시켰다. 납땜 부품은 파워 트랜지스터, 100% 주석 코팅된 2012R 칩, 100% 주석 코팅된 6330R 칩 및 Sn3Ag0.5Cu 구형 조성을 가진 한 종류의 BGA 부품이었다. 대기 분위기 열풍 대류 방식의 리플로우 오븐에서 수행하였다. 그림 2에서 보는 바와 같이 리플로우는 대기 분위기의 열풍 대류 오븐에 100초 동안 130℃~180℃ 예열, 237℃ 피크 온도, 45초의 220℃ 타임 오버의 리플로우 프로파일을 적용하였다.
결과 및 논의
열 사이클링 후의 리플로우 플럭스 잔사물의 신뢰성
리플로우된 크랙-프리 Paste A 플럭스 잔사물은 60분 주기로 1,000 사이클 동안 -30℃에서 +80℃까지 열 사이클을 가했다. 0.5mm 피치 QFP 부품과 패드 사이에 0.15mm 간격을 갖는 1.0mm 폭의 보드 패드의 경우, 그림 9에서 나타내는 바와 같이 플럭스 잔사물의 크랙 현상 증거가 없었다.
리플로우된 페이스트 Dew 테스트 방법 (A)
크랙-프리 Sn3Ag0.5Cu 솔더 Paste A와 기존 Sn3Ag0.5Cu 솔더 Paste B는 IPC-B-25(E pattern) 테스트 보드를 이용하여 Dew 테스트 방법 (A)가 실시되었다. 50시간 이후 기존 솔더 Paste B는 그림 10에서 나타내는 것과 같이, 테스트 기간 동안 어떠한 이슈도 없었던 크랙-프리 Paste A와 달리 회로 쇼트 징후를 보였다. 그림 11에서와 같이 기존 Paste B에서 수상돌기가 관찰된 반면, 그림 12에서 볼 수 있듯이 크랙-프리 Paste A의 경우 어떠한 수상돌기 혹은 전기 화학적 마이그레이션이 나타나지 않았다.
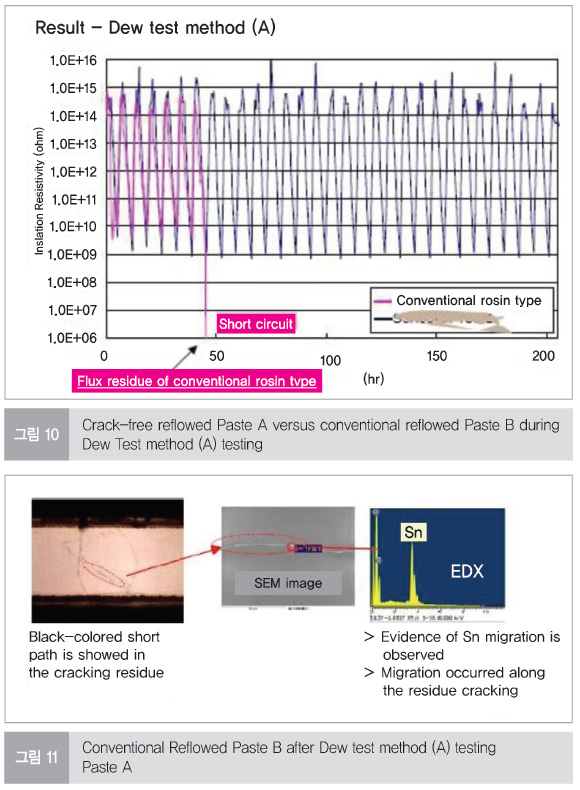
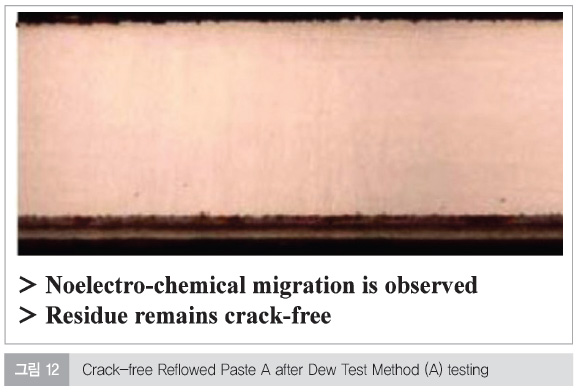
리플로우된 페이스트 Dew 테스트 방법 (B)
크랙-프리 Sn3Ag0.5Cu 솔더 Paste A는 또한 IEC 60068-2-30 테스트 방법론에 따라 동일한 IPC-B-25(E pattern) 테스트 보드를 사용하여 Dew 테스트 방법 (B)을 거쳤다. 그림 13에서 관찰할 수 있듯이 절연 저항 또는 전기 화학적 마이그레이션이 크게 감소했다는 증거가 없었다.
리플로우 페이스트의 전형적인 고온/습도 SIR 테스트
크랙-프리 Sn3Ag0.5Cu 솔더 Paste A는 또한 0.318mm 너비의 라인과 0.318mm 너비의 공간을 지닌 JIS comb 패턴 형태의 테스트 보드와 0.25mm, 0.2mm 및 0.175mm를 포함한 더 작은 선폭과 간격을 갖는 다른 테스트 보드를 사용하여 전형적인 고온/습도 SIR 테스트를 진행하였다. 그 결과는 그림 14에서 보여주고 있으며, 이용된 상이한 선폭 및 간격에 관계없이 테스트 동안 절연체의 현저한 저하 또는 전기 화학적 마이그레이션의 증거가 나타나지 않았다.
페이스트의 연속적인 인쇄성 테스트
크랙-프리 Paste A가 전자 제품 생산에 사용될 수 있는지를 확인하기 위해 연속적인 인쇄 성능 테스트를 포함한 일련의 테스트를 수행하였다. 페이스트 프린트 결과는 그림 15와 같이 직경 0.35mm의 보드 패드 패턴과 0.4mm 피치 QFP 부품 패드에서 양호했다.
또한 그림 16에서와 같이 연속 프린팅 이후 높은 페이스트 전사 효율을 나타내는 해당 위치에서 SPI 설비를 이용하여 페이스트 측정을 수행했다.
페이스트 점도 변화 인쇄 테스트
크랙-프리 Paste A는 밀봉된 스텐실 챔버 내에 24시간 동안 놓아둔 솔더페이스트를 프린팅해서 점도 변화를 관찰하였다. 그림 17에 도시된 바와 같이, 개발된 솔더페이스트의 안정된 인쇄 성능을 의미하는 24시간 스트로크 평가에서 점도의 현저한 하락을 볼 수 있었다.
솔더 미세 패턴 젖음/리플로우 테스트
0.35mm 직경의 보드 패드가 설계된 테스트 보드에 크랙-프리 Paste A를 프린팅하고, 이 보드를 대기 분위기에서 1005R 칩 부품을 리플로우하는 방식으로 젖음/리플로우 테스트를 실시하였다. 그림 18의 결과에서는 0.35mm 직경의 보드 패드와 납땜된 1005R 칩 부품에서 양호한 젖음성을 나타내고 있었다.
보이드/리플로우 테스트
크랙-프리 Paste A는 테스트 보드에 파워 트랜지스터, 2012R 칩, 6330R 칩과 특정 타입의 BGA 부품으로 이뤄진 부품들을 납땜함으로써 추가적인 보이드/리플로우 테스트를 거쳤다. 그 결과, 그림 19와 같이 양호한 젖음 및 보이드 발생률이 나왔다.
산업계의 일반적인 크랙-프리 솔더페이스트 애플리케이션
앞서 평가 결과를 바탕으로 개발된 페이스트 A가 평가되었고, 산업계에서 사용되고 있다. 하나의 영역인 자동차 애플리케이션에 사용되었으며, 표 1에서는 자동차 산업의 일반적인 애플리케이션을 보여주고 있다. 이들 애플리케이션 중 일부에서 컨포멀 코팅(conformal coating) 공정을 뺄 수가 있어서 추가비용 절감과 생산/처리 시간 단축이라는 이점을 제공할 수도 있다.
결론
무연 솔더페이스트는 열 사이클 동안의 크랙에 대한 내성에 집중해 개발되고 있다. 크랙에 대한 내성은 플럭스 잔사 크랙을 통해 유입된 수분으로 인한 전기 화학적 이동을 방지하는데 도움이 되는 다양한 산업계 시험 방법이 활용된 고온 및 고습 조건 하에서도 신뢰할 만한 절연 저항을 제공하는 것으로 나타났다. 크랙-프리 잔사는 컨포멀 코팅와 비슷한 동작을 하기 때문에 특정 애플리케이션에서는 컨포멀 코팅 공정 적용 없이도 어셈블리할 수 있다.
개발된 페이스트를 적용한 부품의 프린팅, 젖음, 보이드 및 리플로우 테스트가 생산 현장에서와 동일한 조건 하에서 진행한 결과 양호한 결과를 얻었다. 이를 통해 대량의 전자제조에서도 사용될 수 있음을 입증하였다.