기존 기술 기반 제작품과 비교
다양한 크기 부품 혼재에 필요성 커질 전망
본고의 목적은 3개의 스텝 스텐실 테크놀로지를 평가하는 것이고, 프린팅 공정 동안 동일한 보드에서 서로 다른 체적의 페이스트를 적용할 때의 효율성을 측정하는 것이다. 평가된 스텝 테크놀로지는 화학 에칭, 레이저 용접과 마이크로-머시닝 기술들이다. 각 테크놀로지의 스텝 다운 영역은 정확도를 물리적으로 측정하였다. 주어진 스퀴지 속도와 압력에 따라, 스텝 엣지에서 근거리 개구까지의 거리를 다르게 하였다. 또한 각 테크놀로지의 스텝 다운 영역 내의 솔더 페이스트 체적도 측정하였다. 마지막으로 Fluoro Polymer Nano(이하 FPN)-코팅을 스텐실의 접촉면과 개구부 벽에 실시하였고, 솔더 페이스트 체적을 측정하였으며, 코팅되지 않은 스텝 테크놀로지와 비교하였다.
SMT 생산에서 솔더 프린팅 공정이 가장 중요한 부분 중 하나라는 것은 일반적인 사실이다. 오늘날의 많은 어셈블리 업체들은 커다란 커넥터와 같은 대형 부품뿐만 아니라 0201, 마이크로-BGA, LGA 그리고 QFN와 같은 소형 부품을 동일한 생산라인에서 처리하고 있다. 이러한 어셈블리 라인에서 솔더 페이스트를 적합한 체적으로 프린팅하는 일은 싱글 레벨 스텐실의 개구 조정으로만 가능하지 않다. 결과적으로, 제조업체들은 월등한 첫 번째 pass 수율을 가지고 동일한 어셈블리 라인에서 서로 다른 부품에 정확한 양의 페이스트 적용을 가능하게 하는 ‘Step Stencil’를 모색하고 있다.
본고의 목적은 3개의 스텝 스텐실 테크놀로지를 평가하는 것이고, 프린팅 공정 동안 동일한 보드에서 서로 다른 체적의 페이스트를 적용할 때의 효율성을 측정하는 것이다. 평가된 스텝 테크놀로지는 화학 에칭, 레이저 용접과 마이크로-머시닝 기술들이다. 각 테크놀로지의 스텝 다운 영역은 정확도를 물리적으로 측정하였다. 주어진 스퀴지 속도와 압력에 따라, 스텝 엣지에서 근거리 개구까지의 거리를 다르게 하였다. 또한 각 테크놀로지의 스텝 다운 영역 내의 솔더 페이스트 체적도 측정하였다. 마지막으로 Fluoro Polymer Nano(이하 FPN)-코팅을 스텐실의 접촉면과 개구부 벽에 실시하였고, 솔더 페이스트 체적을 측정하였으며, 코팅되지 않은 스텝 테크놀로지와 비교하였다.
본고에서는 테스트된 변수에 대하여 연구의 결과들을 요약하였다. 스텐실 디자인 권장사항은 스텝 스텐실 테크놀로지를 통해서 페이스트의 서로 다른 체적을 적용하고자 할 때 솔더 페이스트 프린팅 프로세스 내의 결점을 제거하려는 의도로 만들어질 것이다. 부품 소형화가 지속되고 커다란 부품은 여전히 남아있음에 따라, 스텐실 제조업체에 의한 스텝 테크놀로지는 지속적으로 발전되고 있다.
QFN, LGA, 마이크로 BGA, 0201 및 심지어 01005와 같은 부품들은 보드 위에 정확한 페이스트 양을 적용할 수 있도록 더 얇은 스텐실 호일 활용을 임가공 업체들에게 지속적으로 강요하고 있다. 그러나 엣지 커넥터와 같은 대형 부품들은 여전히 많은 양의 페이스트가 필요하다. 스텝 스텐실은 수년 동안 이러한 요구를 충족시키는 목적에서 사용되어 왔다. 역사적으로 볼 때, 이들 스텝 스텐실을 생산하기 위한 초창기 방법은 광화학 에칭(photochemical etching) 프로세스를 사용하는 것이었으며, 최근에는 레이저 용접과 마이크로-머시닝 모두를 포함한 새로운 스텝 스텐실 제조방법이 등장했다.
광화학 에칭은 이미 정립된 프로세스로, 수십년에 걸쳐 행해져 왔다. 이는 덜어 내는 프로세스로, PWB 에칭에 활용되는 프로세스와 매우 비슷하다. 스텐리스 스틸 스텐실 호일은 광-레지스트로 코팅되고, 포토그래픽 프로세스를 이용하여 형상화되며, 두께가 줄어들지 않거나 혹은 에칭되지 않은 특정 영역을 보호하기 위해 레지스트를 남기도록 발전되었다. 에칭 설비에 스텐실 호일을 올리고, 스텐실 상에 화학 에칭제를 분사하여 정확한 두께를 얻을 때까지 스텐리스 스틸 호일을 용해한다. 원하는 스텐실 두께에 도달했다면, 광-레지스트는 제거된다. 에칭의 깊이 혹은 이 프로세스를 활용하는 스텝 영역은 스텐실이 에칭 화학재에 노출된 시간에 좌우된다. 화학 에칭 프로세스는 그림 1에서 보여주고 있다.
레이저 용접 프로세스는 서로 다른 두께의 스텐실 호일을 가져와 그들을 함께 용접하는 공정이다. 어떠한 화학 에칭 프로세스도 포함되지 않고, 단지 레이저 절단 및 레이저 용접 공정만이 존재한다. 스텝 opening은 첫 번째 스텐실에서 절단된다. 해당 스텝 영역은 두 번째 스텐실 호일에서 원하는 두께만큼 절단된다. 스텝 조각들은 첫 번째 스텐실의 opening에 놓은 다음에 레이저를 이용해 이들 조각들을 용접한다. 스텝 영역의 두께는 사용된 스틸의 두께에 의해 결정된다. 레이저 용접 프로세스는 그림 2에서 보여주고 있다.
마이크로-머시닝 프로세스는 에칭 프로세스와 비슷한 덜어 내는 프로세스이지만 어떠한 화학재도 사용하지 않는다. 마이크로-머시닝 프로세스는 한 번에 매우 적은 양의 재료를 없애기 위해 매우 특수한 CNC 밀링 머신을 이용한다. 마이크로-머시닝 프로세스는 그림 3에서 보여주고 있다.
스텝 스텐실을 생성하는 이들 3가지 프로세스는 스텝 영역 내에서 서로 다른 결을 나타낸다. 각 프로세스에서 제작된 스텝 스텐실의 결은 그림 4에서 보여주고 있다.
스텝 스텐실 디자인은 다양한 두께의 스텝 다운 포켓으로 제작된다. 기본적인 스텐실 두께는 4.0mil(101.6 미크론)이고, 스텝 다운 포켓은 3.5mil(88.9 미크론), 3.0mil(76.2미크론), 2.5mil(63.5미크론) 그리고 2.0mil(50.8미크론) 두께였다. 각 스텝 영역은 정사각형 1인치(25.4mm)이고, 스텝 디자인은 그림 5에서 나타내고 있다.
각 스텝 포켓의 두께는 FARO 암 디바이스를 이용해 측정하였다. 각 스텝 테크놀로지에 대한 측정을 비교 및 대조하였다.
개구 패턴은 03015(metric), 01005, 0.3mm BGA, 0.4mm BGA 그리고 0.5mm 피치 QFN 부품에 맞춰 제작하였다. 각 부품에 대한 개구는 스텝 엣지에서부터의 다양한 거리(10mil, 20mil, 30mil, 40mil 및 50 mil)에서 절단하였다. 각 스텝 스텐실 테크놀로지의 스텝 엣지에 솔더 페이스트가 얼마나 근접하게 프린트될 수 있는가를 알아내는 것이 목적이었다. 더불어 비교를 위해 개구를 각 스텝 영역의 중앙 부분에서 절단하였다. 개구 레이아웃은 그림 6에서 보여주고 있다.
각 스텐실은 2세트의 스텝과 개구로 제작하였다. 한 세트의 스텝과 개구는 FPN 코팅처리하였다(그림 7 참조).
FPN 코팅의 효과를 알아보기 위해 솔더 페이스트의 프린팅에서 코팅되지 않은 스텐실 부분과 비교하였다. 대중적인 비세척, SAC305 Type4 솔더 페이스트를 각 스텝 스텐실에 10번의 프린트를 실시하였다. 사용된 회로보드는 베어 동박판 재질의 0.062″(1.57mm) 두께였다. 표 1의 프린터 파라미터에 따라 실시하였다.
솔더 페이스트 체적은 SPI를 이용하여 측정했다. 솔더 페이스트 체적 데이터는 정량적인 분석 소프트웨어를 이용하여 분석하였고 그 결과를 하부에 설명하고 있다.
각 테크놀로지의 각각의 스텝 영역을 측정하였다. 측정 데이터와 결부된 문제로 인해 3.5mil 스텝 영역은 포함시키지 않았다. 두께 측정 데이터는 표 2에서 보여주고 있다.
일반적으로, 화학 에칭 프로세스는 공칭 값 보다 더 깊은 스텝 다운을 만들었다. 그리고 용접 및 머시닝 프로세스는 목표된 깊이에 근접한 스텝들을 만든다. 스텝 깊이의 표준편차는 스텝 영역 내 평탄도 혹은 조도의 표시이다. 화학 에칭 프로세스는 원래 표면보다 더 거친 표면을 생성하였다(그림 4 참조). 용접 프로세스는 스텝 영역 내로 스텐실 블랭크를 고정하는 것이 포함되는데, 용접될 때 블랭크는 완전히 평평하게 놓이지 않을 수도 있다. 머시닝 프로세스는 컷팅 툴로 재료를 제거하기 때문에 표면 상에 줄무늬를 남긴다. 결과적으로, 표준 편차는 각 테크놀로지별로 매우 비슷했다.
3.0mil, 2,5mil 그리고 2.0mil 두께의 에칭 스텝에 관한 솔더 페이스트 체적 박스 플롯들은 그림 8, 그림 9 및 그림 10에서 차례대로 보여주고 있다. 이들은 스텝 엣지로부터의 거리, 개구 사이즈 그리고 나노 코팅별로 보여주고 있다.
일반적으로, 9.8 × 35.4mil 크기의 더 커진 개구부는 더 높은 인쇄 솔더 페이스트 체적을 제공한다. 작아진 개구 사이즈는 솔더 페이스트 체적에 약간의 차이를 보였다. Tukey의 HSD(Honest Significant Difference) 테스트에서는 대부분의 이러한 변동이 통계적으로 유사하다는 점을 보여주고 있다. 이는 스텝 엣지에서부터 10mil~50mil 범위의 인쇄된 솔더 페이스트 체적에 매우 적은 차이가 존재함을 의미한다. 한 가지 예외가 존재하였다(그림 11 참조).
인쇄된 솔더 페이스트 체적은 50mil 거리에 비해 10mil 및 20mil 거리에서 더 높았다. 스퀴지가 스텝 포켓에 일치하지 않았고, 표면으로부터 페이스트가 깨끗하게 떨어지지 않았음을 의미한다. 동일한 Tukey HSD 분석에서는 이 스텝의 코팅되지 않은 버전과 개구 사이즈에서 마찬가지로 나타났다.
인쇄 이후 스텝 벽 근처에 남아 있는 솔더 페이스트 잔사를 쉽게 볼 수 있다. 이는 더 높게 인쇄된 페이스트 체적에 상응하는 것으로 보인다.
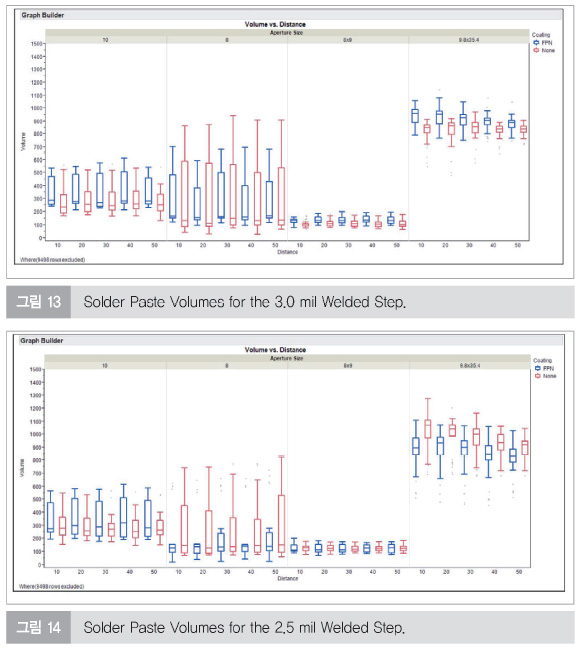
그림 13, 그림 14 그리고 그림 15에서는 3.0mil, 2.5mil 그리고 2.0mil 두께의 용접 스텝에 대한 솔더 페이스트 체적 박스 플롯을 보여주고 있다. 이들은 스텝 엣지로부터의 거리, 개구 사이즈 그리고 나노 코팅별로 보여주고 있다.
인쇄된 솔더 페이스트 체적은 용접 스텝 두께와 관계없이 스텝 엣지로부터 10mil~50mil 떨어진 범위에서 크게 변하지 않았다. 이는 에칭 스텝에서 보여준 결과와 매우 비슷한 것이었다. 그림 16의 Tukey HSD 테스트에서는 약간 흥미로운 결과를 보여주고 있다.
이 경우, 10mil 거리에서 인쇄된 솔더 페이스트 체적은 40mil 및 50mil 거리일 때 보다 매우 높았다. 인쇄된 솔더 페이스트 체적은 이후의 50mil 거리보다 20mil 거리에서 상당히 높았다.
다시 한 번 말하자면, 이는 스퀴지가 인쇄 도중 스텐실의 표면에서 모든 솔더 페이스트를 제거하기 위해 스텝 내로 내려가는 것이 일치하지 않음을 의미한다. 3.0mil 용접 스텝 그리고 동일한 개구 사이즈의 FPN 코팅 버전에서도 마찬가지였다.
그림 17, 그림 18 그리고 그림 19에서는 3.0mil, 2.5mil 그리고 2.0mil 두께의 머시닝 스텝에 대한 솔더 페이스트 체적 박스 플롯을 보여주고 있다. 스텝 엣지로부터의 거리, 개구 사이즈 그리고 나노 코팅별로 보여주고 있다.
인쇄된 솔더 페이스트 체적은 머시닝 스텝 두께에 관계없이 스텝 엣지로부터 10mil~50mil 떨어진 범위에서 크게 변하지 않았다. 에칭 및 용접 스텝에서 보였던 결과가 매우 비슷했다. Tukey HSD 테스트에서는 결과에 몇 가지 중요한 차이를 보였다(그림 20 참조).
스텝 생성에 사용되는 테크놀로지와 관계없이, QFN 개구에 있어서 솔더 페이스트 체적은 스텝 엣지로부터 30mil~50mil 떨어진 것보다 10mil~20mil 거리에서 더 높은 경향이 나타났다. 이러한 증가된 솔더 페이스트 체적은 실험된 QFN 부품 디자인에 맞춘 개구 디자인으로 쇼트를 유발할 수 있다. 스텝 엣지에서부터 30mil 크기의 이 개구를 놓는 것이 가능할 것이고, 수용 가능한 솔더 페이스트 체적을 얻을 것이다. 더 작아진 8mil, 8 × 9mil 그리고 10mil 개구는 스텝 엣지로부터 10mil~50mil 떨어진 거리에서 통계적으로 비슷한 솔더 페이스트 체적을 제공하였다. 비록 향후 연구가 필요하지만, 데이터에서는 소형 개구 부품이 스텝 엣지로부터 10mil까지 근접하게 놓일 수 있으며 수용할만한 인쇄 체적을 여전히 얻을 수 있음을 보여주고 있다.
FPN 코팅은 측정된 모든 개구에 걸쳐 약간 늘어난 체적을 보여주었다. 이들 소형 개구들이 인쇄될 때, FPN 코팅처리된 제품 적용을 권장한다. 이러한 스텝 스텐실 테크놀로지 간의 차이점을 확인하기 위해 추가 조사작업이 분명하다.