PCB 서브스트레이트의 사인파 스윕 자극 방법
현저한 보이드 비율 감소 확인
실험 파라미터에 따라 솔더링 공정 중 PCB에 미치는 진동의 영향이 솔더링 접합부의 보이드 비율을 현저하게 개선시키는 것으로 나타났다. 연구 프로젝트에서는 보이드 비율의 최소화에 있어서 사인파 스윕 작동의 영향에 관한 긍정적인 결과를 이끌어냈다. 이 프로젝트에서 3개의 동일한 부품으로 구성된 60개의 동일한 PCB를 분석하였다. 스윕 지속 시간, 폭 및 구동의 진폭 영향과 같은 다양한 파라미터의 영향을 분석할 수 있었다. 연구 프로젝트 동안 잔존 보이드 비율을 레퍼런스 PCB의 9.09%에서 적당한 구동 파라미터를 적용하여 1.86%로 줄이는 것이 가능했다. 이는 레퍼런스 PCB의 평균 보이드 비율이 약 83% 감소한 수치이다.
전력 부품의 소형화 추세로 인해, SMT 프로세스에서 솔더 조인트의 늘어난 열 전도율에 대한 대책이 점점 더 중요해지고 있다. 그래서 전력 전자기기 내 보이드-프리 솔더 조인트의 역할이 더욱 구심점이 되기 시작했다. 솔더링 동안 대두되는 보이드는 실제 열 전송을 감소시키고, 전력 부품을 불량에 이르게 할 정도로 열적 데미지를 입힐 수 있다. 이러한 이유로, 여러 업체들은 솔더링 프로세스 동안 보이드의 형성을 최소화하기 위한 새로운 기술들을 연구해 오고 있다.
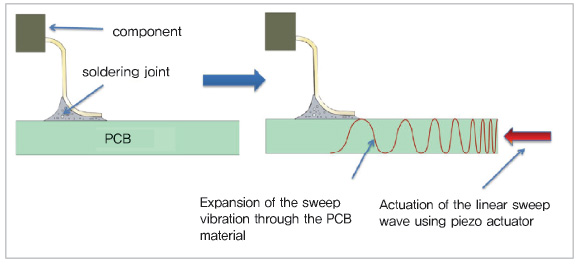
그 개선의 결과 중 하나로, 역학 사인파 구동(mechanic sinusoidal actuation)을 적용하여 부품과 PCB 사이에서 있는 액상 솔더 내의 보이드를 줄이는 기술을 소개한다. 최초 PCB에 PCB 레벨에서 10㎛ 미만의 진폭을 지닌 종파(longitudinal wave)로 자극을 주었다. 정해진 주파수 범주 내에서 PCB의 이 사인파(sinusoidal)를 작동시키는 동안, 해당 영역의 자기공진은 PCB 레이아웃과 관계없이 자극을 받는다. 낮은 주파수로 시작하는 스윕(sweep) 자극은 분자 사슬(예 : FR-4)에 손상을 끼치지 않으면서 PCB 내에 전달하는 완만하고, 균등한 진동을 보장할 수 있다. 주파수 증대는 PCB 서브스트레이트의 경화, 탄성 계수의 증가 그리고 줄어든 감쇄변수 때문에 액상 솔더의 증강된 에너지 전달을 초래한다. 그래서 저밀도 영역, 일명 보이드는 진동에 의해 솔더 조인트의 밖으로 이동하게 된다. 규정된 주파수 범주 내에서 PCB의 사인파 구동이 가해지기 때문에 주파수 범주 내 PCB의 모든 자기공진도 역시 자극을 받는다.
이것으로, 액상 솔더는 솔더 조인트 내 보이드 감소를 유도하는 상대적인 전단 운동의 진동 전파에 의해 반복적으로 자극을 받는다. 부품 쪽의 스윕 자극은 액상 솔더에 의해 대부분 흡수되어 진동 전달로 초래될 수 있는 데미지로부터 부품을 보호한다. 스윕 자극의 긍정적인 부작용은 패드 위 부품의 센터링과 패드 상 솔더의 최적화된 퍼짐 현상을 나타난다는 것이다. 보이드 최소화 프로세스는 사이클 타임의 큰 증가를 유발하지 않고 몇 초 내에 완료된다.
서문
본 연구 프로젝트의 목표는 현재 최신의 방법들이 겪고 있는 단점을 극복하여 납땜 조인트 내부 보이드 감소 기술을 조사하는 것이다. 이를 위해 피에조 액추에이터의 로우-레벨 신호 측정에 일반적으로 사용되는 개념을 콘셉트로 채택하였다. 이 프로세스에서, 정의된 사인파 스윕 구동과 상대적으로 낮은 레벨의 자극 진폭은 공진 주파수 감지를 위해 피에도 액추에이터의 주파수 범위를 자극하기 위해 사용되었다.
이 기술은 변환기의 피에조-전기 특징을 특성화짓기 위해 사용되었다. 프로젝트에서는 미리 규정된 주파수 범위에서 PCB의 구동에 사용되고 있는 전송 원리에서 아이디어를 얻었다. 이를 통해서, 이 주파수 범위 내에서 PCB의 모든 자기공진은 PCB 레이아웃 혹은 자체 재질 특성과 상관없이 자극을 받는다. PCB의 사인파 구동은 주파수 범위 내에서 중첩되는 횡파와 종파의 전파를 유발하고, 밀도가 낮은 매체(여기서는 액상 솔더 내의 가스 함유물)에 운동 에너지를 전달한다.
거의 0Hz의 주파수로 시작하는 스윕 구동은 한편으로는, 피에조 액추에이터 및 시스템 부품에 미치는 영향이 적고, 다른 한편으로는, FR-4 서브스트레이트에서 폴리머 체인의 균일한 전파를 가능하게 한다. 모든 플라스틱의 특징과 마찬가지로, 주파수가 증가하면 PCB 서브스트레이트의 탄성 계수가 증가한다. 폴리머 체인은 증가하고 변화하는 응력에 적응할 시간이 없다. 그래서 프로세스에서 그들은 탄성 계수의 증가를 유발하는 강성을 가지게 된다. 이 상태에서, 액상 솔더의 PCB를 통해서 진동을 전달하는 것이 이상적이다. PCB에서 유도된 에너지는 부분적으로 흡수하고, 부분적으로 운동 에너지로 변환한다.
타당성 연구의 맥락으로, 솔더 조인트의 보이드 비율에 대한 사인파 스윕 구동의 영향을 테스트하였다. 이를 위해 FR-4 PCB를 특수 설계된 시험 장비에 배치하였고 인라인 리플로우 솔더링 시스템에 적용되는 온도 프로파일에 상응하는 적절한 히터로 가열하였다. 사인파 스윕 구동은 피에조 스택을 통해 PCB 서브스트레이트에 직접 전달하였다. PCB 레벨에서 세로 방향 구동은 FR-4 서브스트레이트의 압축을 초래한다. 자극의 최소 진폭 때문에(불과 수 μm), FR-4 PCB의 서브스트레이트는 재질의 복원력을 이끌어 내는 선형 점탄성 범위에 머물러 있다. 횡단 파(sweep actuation의 부작용)에 의해 야기되는 PCB의 표면 상 움직임은 레이저 진동계를 사용하여 PCB 상의 정해진 지점에서 측정하였다. 측정 지점의 위치는 PCB 표면 상의 모든 관련 영역을 평가할 수 있도록 선택하였다. 이를 위해 PCB 상의 각 주파수 스윕에 대한 하나의 측정 포인트를 분석하였다. PCB 서브스트레이트의 탄성 계수의 반응 신호를 분석할 수 있도록 하기 위해, 구동 중에 발생된 반작용 힘은 로드셀로 검측하였다.
결과들
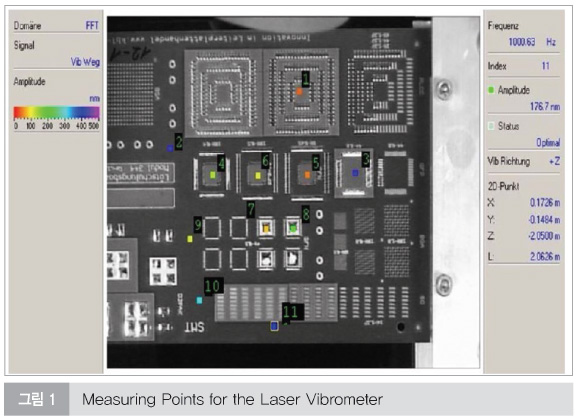
측정 지점 4, 5 및 6은 부품 상단에 있으며(그림 1 참조) 부품 하부의 솔더의 진동 거동에 관한 결론을 내릴 수 있었다. 기판 표면 상의 진동 거동 분석을 위해 PCB는 모든 측정 지점에 스윕으로 구동되었다.
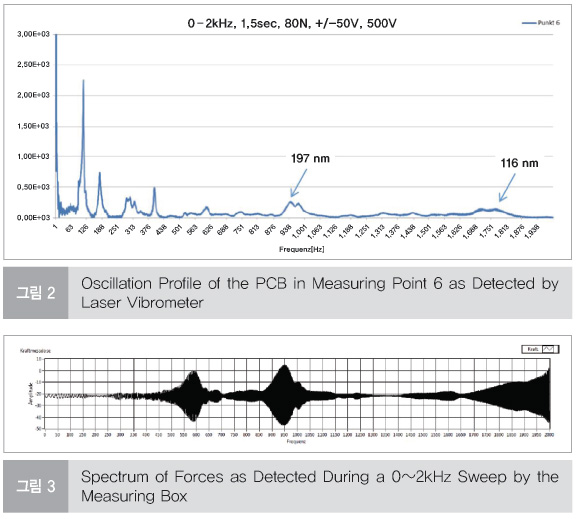
그림 2와 그림 3에서는 측정 박스의 신호와 관련하여 레이저 진동계에 의해 감지된 측정 포인트 6의 PCB 진동을 보여주고 있다. 600Hz 이하의 주파수 범위에서 레이저 진동계 신호의 높은 진폭은 PCB의 이동을 초래했다. 측정 박스의 해당 신호는 600Hz의 주파수에 달하는 현저한 힘의 상승을 나타내지 않았다. 이 주파수 범위에서 PCB에 연결된 구동 에너지는 PCB의 탄성 변형으로 거의 완벽하게 전환되었다. 그림 2에서는 약 600Hz에서의 첫 번째 공진이 시험 장비의 구성에 의해 발생하고 PCB 거동에 영향을 미치지 않는다는 것을 보여주고 있다(측정 지점 6에서 600Hz에서 상당한 진폭 상승이 없었음). 870Hz 이상의 높은 주파수에 도달할 때, PCB는 탄성 계수 증가로 인해 강화되었다. 탄성 계수의 변화는 솔더에 더 나은 에너지 전달을 유발한다. 약 940Hz에서 197nm까지 진폭이 증가하고 1700Hz에서 1800Hz까지의 주파수 범위에서 119nm까지 추가 상승이 분명하게 나타났다(그림 2 비교). 고주파수 범위 내에서 PCB의 강화가 이뤄지는 동안 나타난 감지 진폭은 PCB 이동뿐만 아니라 PCB 상에 놓인 솔더 및 부품의 이동이었다.
보이드의 형성과 그 치수에 있어서 파라미터 변화의 영향을 분석할 수 있도록 동일한 부품으로 구성된 3개의 동일한 PCB를 각 세트 파라미터에 사용하였다. 테스트 결과를 분석하는 동안 9개 솔더 조인트의 보이드 비율의 중간 값을 책정하였다. 이러한 테스트의 경우, PCB는 낮은 기계적 장력을 이용하여 테스트 장비에 고정하였다. PCB 하부의 적외선 가열은 리플로우 솔더링 시스템의 온도 프로파일에 상응하는 온도 프로파일로 설정하였다. 용융 온도에 도달한 후에, 사인파 스윕(sinusoidal sweep)을 미리 예정된 시간 동안 구동하였다. 이후 솔더링된 PCB의 X-선 분석을 수행하여 솔더링 영역의 크기와 솔더링 조인트에서 가장 큰 보이드의 크기와 관련하여 보이드 비율을 확인했다.
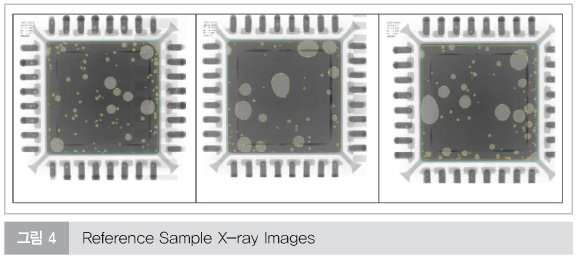
그림 4는 진동의 영향 없이 납땜된 레퍼런스 샘플의 3개 부품의 X-선 이미지를 보여주고 있다. 다량의 가스 함유물(보이드)을 명백하게 관찰할 수 있다. 다른 양의 크고 작은 보이드가 관찰되었기 때문에 보이드의 퍼짐은 중요한 경향을 보이지 않는다. 이후 분석에서는 솔더링된 영역 대비 보이드 크기의 백분율뿐만 아니라 각 부품의 보이드 비율(%)을 구하였다. 레퍼런스 PCB의 평균 보이드 비율은 9.09%이고 보이드의 평균 크기는 납땜 영역의 2.00%이었다.
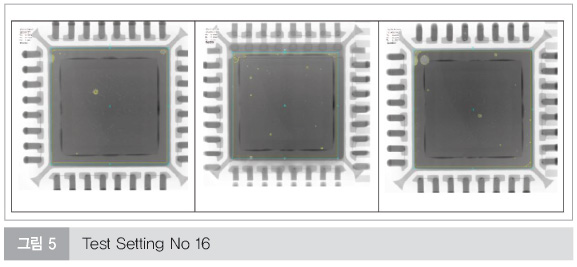
그림 5의 X-선 이미지를 분석한 결과 솔더링된 영역의 평균 보이드 비율이 현저하게 개선된 것을 볼 수 있었다. 평균 보이드 비율이 1.83%이었으며, 이는 사인파 구동 없이 솔더링된 레퍼런스 PCB의 9.09%과 비교하면 평균 보이드 비율은 80% 이상 감소하였다. 잔존하는 보이드는 더 작은 지름을 가지고 있었으며 QFN 부품의 넓은 납땜 영역에 균등하게 퍼져있는 모습을 확인했다. 사인파가 동된 부품의 경우, 대부분의 가스 함유물(보이드)는 부품 하부의 납땜 영역의 바깥쪽에 위치해 있었다.
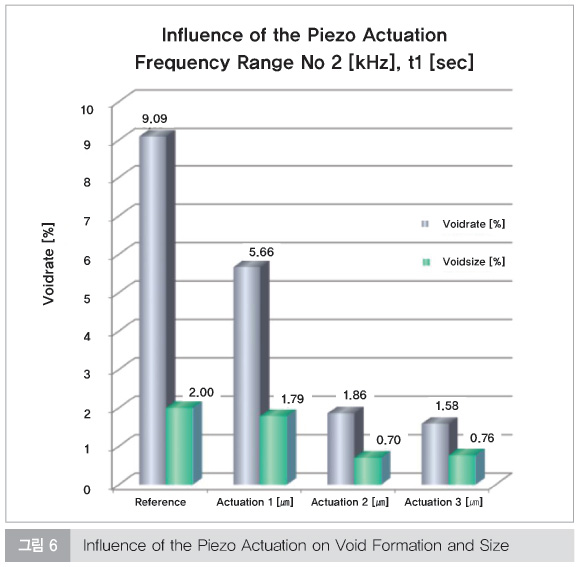
그림 6에서는 보이드 크기와 보이드 형성에 있어서 구동 진폭이 미치는 영향을 보여주고 있다. 사인파 구동 진폭이 커지면 보이드 비율이 현저하게 감소한다. Actuation 1에서는 9.09%(레퍼런스)에서 5.66%로 보이드 비율이 줄어들었다. 구동 진폭의 추가 상승시킨 영역(Actuation 2)에서는 1.86%로 더욱 낮췄다. Actuation 3의 진폭 세트는 최종적으로 1.58% 미만의 보이드 비율을 최종적으로 구현하였다. 82.6%인 레퍼런스 테스트와 비교하면, 이 수치는 평균 보이드 비율의 감소를 의미한다. 대형 보이드의 평균 백분율 또한 진폭의 상승에 따라 감소하였다. 레퍼런스 테스트에서 2.0%의 대형 보이드를 보여준 반면, 그 양은 Actuation 2에서 0.7%로 감소하였다.
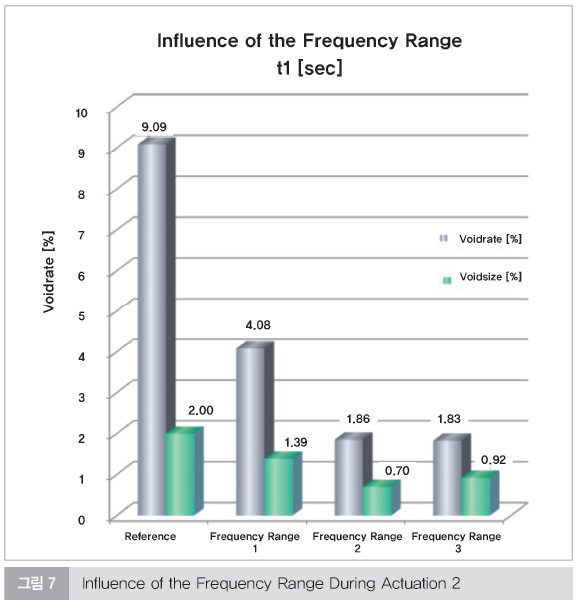
그림 7에서는 Actuation 2 동안 보이드 감소에 있어서 주파수 범위의 영향을 보여주고 있다. 선정한 주파수 범위와 비교하여 보이드 감소는 비선형 발달을 나타냈다. 평균 보이드 비율은 주파수 범위 1에서 9.09%이었던 것이 4.08%로 줄어들었다. 1.86%의 잔존 보이드가 구현된 주파수 범위 2에서 보이드 비율의 더 큰 감소가 나타났다. 주파수 범위를 더욱 늘리더라도 평균 보이드 비율이 두드러지게 개선되지 않았다. 주파수 범위 3에서는 1.83%의 보이드를 보였는데, 이는 주파수 범위 2와 비교하면 0.03%의 감소에 불과했다.
그림 8에서는 주파수 범위 2에서의 보이드 감소와 스윕 지속 시간에 대한 상관관계를 보여주고 있다. 이를 통해서, 평균 보이드 비율의 감소에 있어서 스윕 폭이 미치는 영향이 분명함을 알 수 있었다. 스윕 지속 시간 t1의 경우 1.86%이었다. 연구 프로젝트의 맥락에서 스윕 폭이 보이드 감소에 긍정적 영향을 미치는 것으로 나타났다. 한편 평균 보이드 비율은 t1의 1.86%에서 t2의 2.36%까지 스윕 지속 시간이 늘어남에 따라 증가했다.
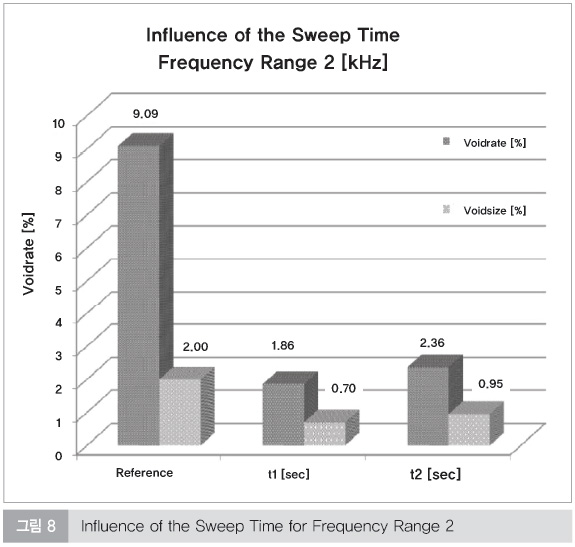
요약
실험 파라미터에 따라 솔더링 공정 중 PCB에 미치는 진동의 영향이 솔더링 접합부의 보이드 비율을 현저하게 개선시키는 것으로 나타났다. 연구 프로젝트에서는 보이드 비율의 최소화에 있어서 사인파 스윕 작동의 영향에 관한 긍정적인 결과를 이끌어냈다. 이 프로젝트에서 3개의 동일한 부품으로 구성된 60개의 동일한 PCB를 분석하였다. 스윕 지속 시간, 폭 및 구동의 진폭 영향과 같은 다양한 파라미터의 영향을 분석할 수 있었다. 연구 프로젝트 동안 잔존 보이드 비율을 레퍼런스 PCB의 9.09%에서 적당한 구동 파라미터를 적용하여 1.86%로 줄이는 것이 가능했다. 이는 레퍼런스 PCB의 평균 보이드 비율이 약 83% 감소한 수치이다. 연구 프로젝트 동안 더욱 가치 있는 발견은 다음과 같다:
▶ 스윕 지속 시간이 짧으면 솔더링 된 영역에 작은 보이드가 형성된다.
▶ 스윕 지속 시간이 길면 부품 가장자리에 모이는 큰 보이드 가 거의 형성되지 않았다.
▶ 스윕 폭이 넓을수록 솔더링 조인트의 보이드 비율이 감소 한다.
▶ 액추에이터의 진폭이 증가하면 보이드 감소에 긍정적인 영 향을 미친다.