많은 장점의 SnCuNi 매력적
적용하기 위한 전제조건 준수가 관건
본고에서는 웨이브 솔더링에 SAC 및 SnCuNi 솔더 합금의 적용을 비교했다. SnCuNi는 비용 문제 때문에 웨이브 솔더링에서 SAC 솔더를 대체 할 수 있는 흥미로운 솔더이다. SnCuNi는 또한 웨이브 솔더링을 고려할 때 다른 장점이 있다. SnCuNi는 납땜조 재료로 사용되는 스테인리스-스틸에 대한 공격성이 낮다. 게다가, SnCuNi는 PCB 상의 홀과 패드에서 동박을 침식시키는 것이 SAC 솔더에 비해 적다. SnCuNi 솔더 조인트는 더 밝고 전통적인 SnPb 솔더 조인트와 유사하다. SAC 솔더 조인트는 종종 거칠게 보인다. 반면, SnCuNi는 SAC 솔더보다 10℃ 더 높은 융점을 가지고 있다. 융점이 높을수록 납땜 온도가 높아져 납땜 부품에 야기되는 열 스트레스가 증가하고 솔더링 프로세스에 필요한 소비전력이 높아진다.
추상
무연 웨이브 솔더링 공정에서의 적용을 고려할 때, 일반적으로 활용 가능한 2개의 무연 솔더 합금과 특성이 비교되고 있다. Sn-Ag-Cu(SAC)와 SnCuNi 무연 솔더 합금이 바로 그 솔더들이다. 본고에서는 SAC와 SnCuNi를 이용한 웨이브 솔더링을 실시하여 그 데이터를 비교하였다. 테스트한 PCB 적층판은 FR4 재질과 CEM1으로 제작하였다. PCB 표면처리는 OSP와 immersion-Sn을 적용하였다. 온도 프로파일과 플럭스는 양쪽 솔더 테스트에 동일하게 적용하였다. SAC 솔더에 적용한 납땜 온도는 260℃이었으며, SnCuNi 합금의 납땜 온도는 265℃이었다. SAC와 SnCuNi 솔더를 적용한 솔더링 머신이 실제로 약간 다르기에 양쪽 솔더 상의 테스트에서 얻은 솔더링 품질에 영향을 미칠 수도 있음을 감안하였다. 솔더링 품질은 X-선 마이크로스코프를 통해 시각적으로 검사했다. 게다가, 필렛 리프팅(fillet lifting) 현상을 발견하기 위해 솔더 조인트에서 종단면 분석을 수행하였다.
소개
웨이브 솔더링은 쓰루홀(TH, through-hole) 부품을 솔더링하는데 사용되는 대량 생산 솔더링 기술이다. 쓰루홀 및 SMD(표면 실장 장치)가 혼재된 기술의 어셈블리에서도 웨이브 솔더링 공정을 거쳐 솔더링할 수 있다. 웨이브 솔더링에 전통적으로 사용된 솔더는 Sn과 Pb 합금이었다. 납의 유해성으로 인해 Sn-Pb 솔더가 무연 솔더로 대체되었다. 전자 업계에서는 Sn-Ag-Cu(SAC) 솔더 계열을 무연 솔더로 사용해 오고 있다. 솔더의 가격은 웨이브 솔더링에서 상당히 민감한 부문이다. Ag와 같은 귀금속은 솔더의 가격을 높인다. 이점이 웨이브 솔더링에서 Ag 함량이 매우 낮은 대체 무연 솔더 혹은 Ag가 없는 솔더의 사용이 고려되는 이유이다. 본고에서는 웨이브 솔더링에서 SAC 솔더와 non-silver 솔더인 SnCuNi을 적용하여 여러 부분을 비교하였다.
솔더 특성
SAC 합금
Sn-Ag-Cu 솔더는 Ag 함량이 일반적으로 3.0~4.0w%이고, Cu 함량이 0.5~0.9w%인 솔더 계열이다. 상이한 SAC 합금은 주석 SACx1x2y로 표시될 수 있는데, 처음 2개 숫자인 x1과 x2는 Ag 함량을 나타내고, 세 번째 숫자는 Cu의 1/10 함량을 나타낸다. 예를 들어 SAC387은Ag 함량이 3.8%이고, Cu 함량이 0.7%인 SAC 합금을 의미한다. U. Kattner et al 보고서에서는 3.5wt%±0.3wt%의 Ag와 0.9wt%±0.2wt%의 Cu를 함유하는 SAC 합금의 용융 혼합물 조성을 확인했었다. SAC 합금의 융점은 약 217℃이다.
서로 다른 SAC 합금 간의 일부 차이점(예 : 강도, 인장력 및 연성(elongation performance)이 보고되었다. 한편, 2005년에 IPC협회의 SPVC(Solder Products Value Council)에서는 시차주사열량계(DSC)를 통한 융점, 습윤 밸런스 테스트 및 양쪽 어셈블리에서의 솔더 퍼짐, 금속학 분석 및 열 사이클링 테스트와 같은 합금 특성 검사를 포함한 대규모 테스트 프로그램을 수행했었다. IPC SPVC에서는 시험한 SAC 솔더 간의 큰 차이가 통계적으로 없었다고 보고했다. 솔더 조인트 및 솔더링을 고려할 때 각 SAC 합금의 차이점은 무시해도 무방한 수준이라는 의미이다.
SnCuNi
Sn-Cu 솔더는 솔더의 가격 때문에 SAC 합금을 대체할 수 있는 매력적인 제품이다. SnCu의 Cu 함량은 0.7%이고 나머지는 Ag 없이 Cu로만 구성된다. SnCu 합금은 동박에 스며드는 경향이 낮다. 이는 트랙 및 패드 내의 전도성 동박의 손실이 적고 솔더 배스 내에 함유된 구리의 증가율이 낮음을 의미한다. 그러나 SnCu 솔더는 무연 웨이브 솔더링 공정에서 일반적으로 사용되는 솔더링 온도에서 유동성이 떨어진 것으로 밝혀졌다. 약한 유동성은 불충분한 쓰루홀 충진과 부품들 간의 솔더 브릿지 형성 결과를 초래하는 원인이 될 수도 있다. SnCu 합금에 니켈을 조금 첨가하면 유동성이 향상된다는 것이 밝혀졌다. 또한, 니켈 추가된 SnCu의 솔더 조인트는 냉각 속도가 느린 경우에도(높은 열량) 전통적으로 사용되는 Sn-Pb 솔더와 비슷한 밝고 매끈한 모습을 보인다. 반면, SAC 솔더와 SnCu 솔더와 같은 무연 솔더는 매우 거친 모습을 보인다.
니켈 원자는 SnCu 합금의 Cu6Sn5 금속간에 형성된다. 결정구조 내의 교류는 솔더링 도중 금속간 상(phase)의 초기 핵 형성을 촉진시킨다. 이것이 더 나은 유동성과 더 깨끗한 솔더 필렛 형성의 이유라고 생각된다. 니켈이 추가된 SnCu 혹은 SnCuNi는 Nihon Superior Co Ltd에서 특허 등록한 SN100C 브랜드로 시판되고 있다.
높은 주석 함유량의 무연 솔더는 납땜조(solder pot) 재료로 사용되는 스테인리스-스틸에 대해 보다 공격적이다. 그래서 무연 솔더링에 사용되는 납땜조는 티타늄이나 특수 표면 처리 또는 코팅된 스테인리스-스틸로 제작되고 있다. SnCuNi도 FeSn2를 형성하기 위해 철과 반응하지만, SnCuNi 합금은 SAC 합금보다 스테인리스-스틸을 덜 부식시킨다. 납땜조가 조기에 마모되지 않은 좋은 상태라면 스테인리스-스틸 재질의 납땜조는 SnCuNi 솔더 합금을 사용할 수도 있다.
SnCuNi는 SAC 합금과 비교할 때 웨이브 솔더링용 무연 솔더 중에서 비교적 새로운 솔더에 속한다. Tin Technology Ltd의 Soldertec은 무연 솔더링과 관련하여 유럽 전자 제조업체의 두 가지 설문 보고서를 발표했다. 설문은 2002년과 2003년에 실시되었다. 2004년 조사에서 나온 이와 유사한 보고서는 Tin Technology Ltd.가 참여한 European Lead-Free Soldering Network 프로젝트에 의해 공표되었다. 표 1에서는 2002년과 2003년에 SAC 및 SnCu 솔더가 널리 사용되는 웨이브 솔더링 후보 제품임을 보여주고 있다. SnCuNi는 웨이브 솔더링 합금으로 주목받기 전인 2004년 설문 조사까지 솔더 후보로 언급되지 않았다.
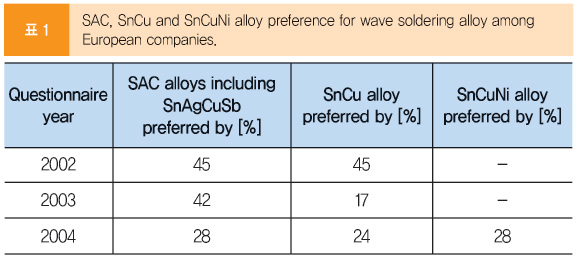
SnCuNi는 리플로우(reflow) 공정에서 솔더페이스트로 이용 가능하다. 그럼에도 불구하고 SAC 합금은 낮은 융점으로 인해 SnCuNi보다 무연 리플로우 공정에서 훨씬 더 널리 사용되고 있다. 리플로우 및 웨이브 솔더링에서 다른 솔더 합금을 사용하면 이후의 공정인 rework 혹은 repair 프로세스에서 더 많은 문제를 유발할 수도 있다. 그러나 전자 제조업체가 이 사실을 인지하고, 상황을 적절하게 제어할 수 있을 때, 2개의 합금 활용 생산라인은 훌륭한 대안이 될 수도 있다.
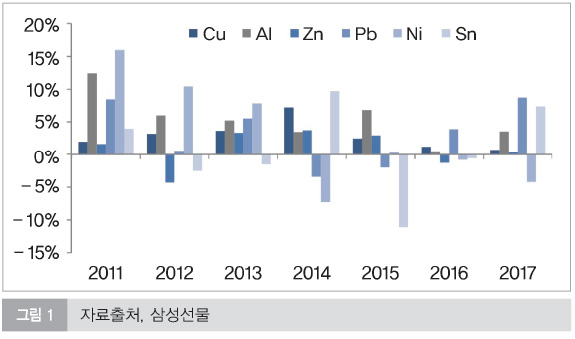
솔더 가격 : 금속 희소성, 금속 순도 및 보편적 솔더 특허
Sn은 무연 솔더에서도 기본 요소로 남아 있다. 실제로, 무연 솔더는 Sn 합금이 95% 이상을 차지하고 있으며, 공융 SnPb 솔더의 경우에도 63%가 주석으로 구성되어 있다. 무연 솔더에서 저가의 납을 값 비싼 주석으로 대체하면 솔더 가격이 높아진다. 또한 주석의 수요 증가로 인해 무연 솔더 도입 이후 주석 가격이 상승했다.
솔더 합금 가격은 금속 불순물 수준, 금속 가격 및 보편적 특허의 세 가지 요소에 따라 달라진다. 금속의 순도가 좋을수록 가격이 높아진다. 금속 가격은 금속의 희소성에 달려 있다. SAC 합금에는 솔더 합금 총 가격을 상승시키는 값 비싼 은이 포함되어 있다. 그림 1에서는 최근 금속가격의 추세를 보여주고 있다.
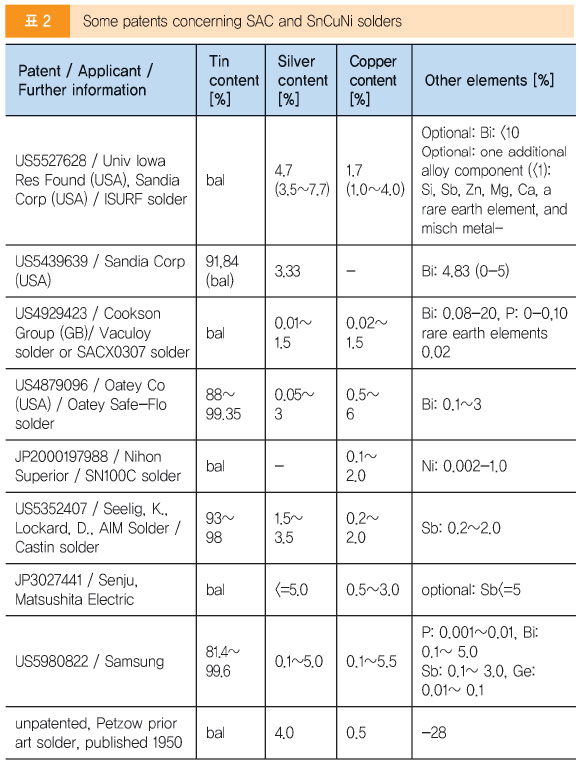
특허권자에게 지불하는 로열티는 솔더 합금 가격을 상승시킬 수도 있다. 표 2에서는 무연 솔더 합금에 관한 일부 특허를 요약하여 보여주고 있다. 표 2에서는 솔더 합금 SAC305가 일본의 Senju에 의해 특허 등록되었음을 나타내고 있다. SnCuNi 또는 SN100C 솔더는 여러 나라에 걸쳐 Nihon Superior가 특허권을 보유하고 있으며, 유럽 특허청(EP 출원) 및 세계 지적 재산권기구(WO 출원)가 발행한 해당 솔더에 대한 특허를 출원했다.
실험
SAC 및 SnCuNi 솔더를 사용한 테스트 시리즈는 제조업체가 다른 웨이브 솔더링 머신에서 솔더링되었으나, 솔더링 프로세스는 가능한 서로 비슷하게 최적화시켰다. 솔더링 프로세스 간의 차이점 중 하나는 SAC 합금에서만 질소 비활성 분위기를 조성해 적용했다는 점이다. SnCuNi를 이용한 솔더링 분위기는 일반 대기로 조성했다. 비활성 분위기는 땜납 젖음 시간을 감소시킨다. 반면 SnCuNi 솔더의 납땜 온도는 5℃ 더 높았다. SAC 솔더의 경우에는 납땜조 온도가 260℃이고 SnCuNi 솔더는 265℃이다. 납땜 접촉 시간(칩 웨이브와 1차 웨이브 포함)은 평균 약 3 초로 하였다.
테스트용 PCB은 FR4 적층과 CEM1 재질로 제작되었다. 적용된 표면 마감재는 OSP와 immersion-Sn로 처리되었다. 본 연구에서는 테스트용 PCB의 다음과 같은 스루홀 부품의 납땜 품질을 조사했다.
▶ 4핀 male row 커넥터, 표면 처리 : 무연
▶ 25핀 D-SUB 커넥터, 표면 처리 : Au
▶ 레디얼 전해 커패시터 직경/높이(d/h) 5/11mm, 표면 처리 : 무연
▶ 레디얼 전해 콘덴서 d/h 12.5/25mm, 표면 처리 : 무연
▶ 엑시얼 금속 필름 레지스터, 표면 처리 : 무연

커패시터와 함께 사용되는 커다랗고 작은 접지면이 존재했다. 접지면이 줄어든 커패시터 상에 더 작은 열량이 존재했다. PCB 설계 소프트웨어 프로그램에서는 일반적으로 큰 접지면을 기본 설정으로 제공한다. PCB 설계자는 접지면 범위를 기본 값에서 변경할 수 있는 여러 가지 방법이 있다. 그림 2와 그림 3은 본 연구에서 사용된 테스트용 PCB 바닥면(그림 2)과 상단면(그림 3)의 크고 작아진 접지면의 커패시터 지점을 보여주고 있다.
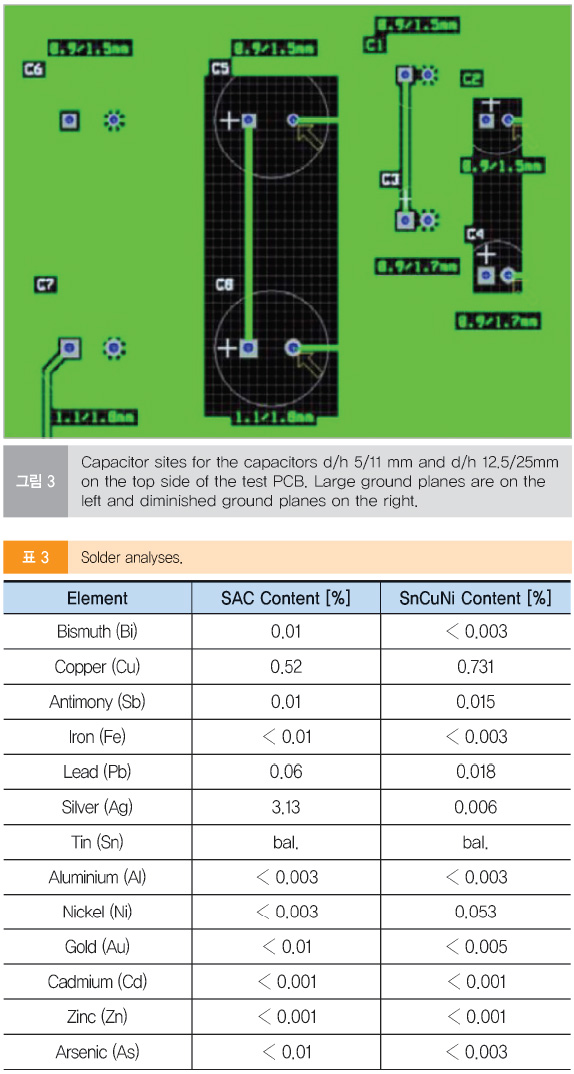
표 3에서는 SAC 및 SnCuNi 솔더 합금의 조성을 원자흡수분광법(atomic absorption spectrometry, AAS)으로 분석한 것을 보여주고 있다. SnCuNi 솔더의 니켈 함량이 매우 낮았던 점을 주목할 만하다. SnCuNi 솔더 내에서 분석된 니켈(0.053wt-%)보다 SAC 솔더 내에서 불순물로써 더 많은 납(0.06wt-%)을 가지고 있었다. 납땜조 내 니켈 함량의 주요 값은 솔더 제조업체에서 제시한 >0.1wt-%과 <0.01 %wt-%이었다.
그림 4에서는 SAC 및 SnCuNi 공정에서 측정된 온도 프로파일을 보여주고 있다. PCB가 솔더 웨이브에 들어가기 직전의 예열 온도는 SAC 솔더보다 SnCuNi 솔더가 약간 높았다. 결과적으로 솔더 웨이브로 접촉하는 도중의 PCB 상부 온도는 SnCuNi 솔더를 적용하였을 때 더 높다. 납땜조 온도가 SAC 솔더에 비해 SnCuNi 솔더가 5℃ 정도 높기 때문이다.
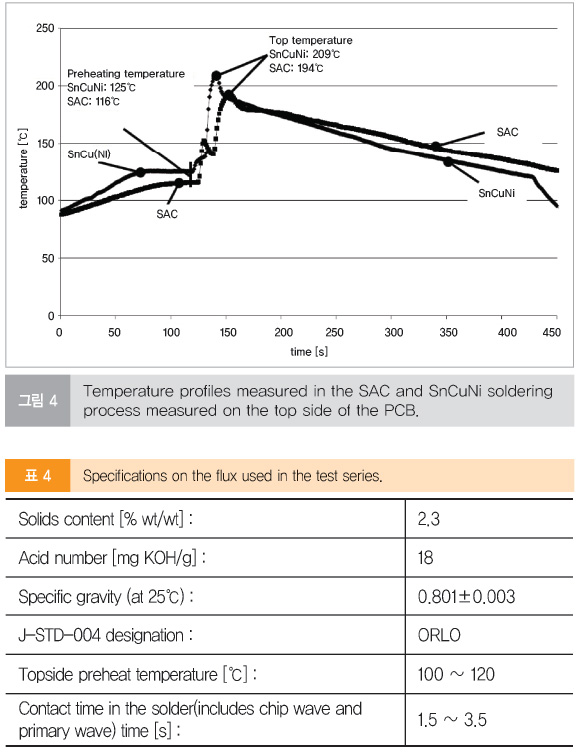
테스트 시리즈에 사용된 플럭스는 알코올 기반의 no-clean 플럭스였다. 플럭스 스펙은 표 4에 나열되어 있다. 또한 사용된 플럭스는 IPC-TM-650, 2.3.25에 따른 아이노그래픽 청결 테스트(Ionograph cleanliness test)를 수행했다. J-STD-001에 따라 허용 가능한 최대값이 3.1μg NaCl/㎠일 때, Ionograph 테스트에서는 1.08μg NaCl/㎠의 평균값을 나타냈다. 측정된 표면절연저항치(surface insulation resistance, SIR)는 솔더링 후 2.2 × 1011Ω이고 고온고습시험(damp heat) 이후 7.9 × 1010Ω이고, IEC 68-2-30에 따라 주기적인 환경시험이다. 고온고습시험에서 보드 상의 이온성 잔사물의 절연저항이 현저하게 감소하지 않았다.
결과
솔더 외관
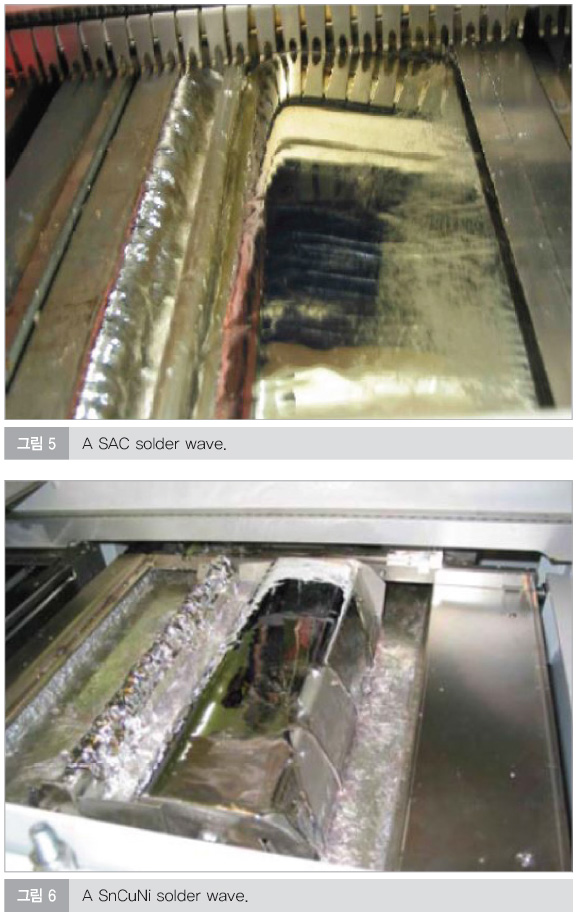
그림 5에서는 용융된 SAC 솔더를, 그림 6에서는 용융된 SnCuNi 솔더를 보여주고 있다. 솔더 표면 상에 얇은 산화층이 존재했음(그림 6)에도 불구하고, SAC 합금이 노랗게 보이는 점을 주목할 만하다. SnCuNi 땜납은 일반적으로 은 회색이다. SAC 합금의 노란색은 외관에 비해 실제 솔더링에서 어떠한 의미를 가지고 있지 않다는 것은 잘 알려지지 않았다. SAC 합금 산화물의 노란색은 Sn-Pb 솔더 표면에서 때때로 보이는 자주색과 비슷했다.
SAC 합금으로 납땜된 솔더 조인트는 종종 거칠게 보인다. SnCuNi 솔더가 더 밝게 보인다. 테스트 보드를 통해서 SAC 솔더 조인트는 종종 입자가 거칠고(그림 7 참조) SnCuNi 솔더 조인트가 더 밝았음을 알 수 있었다(그림 8 참조).
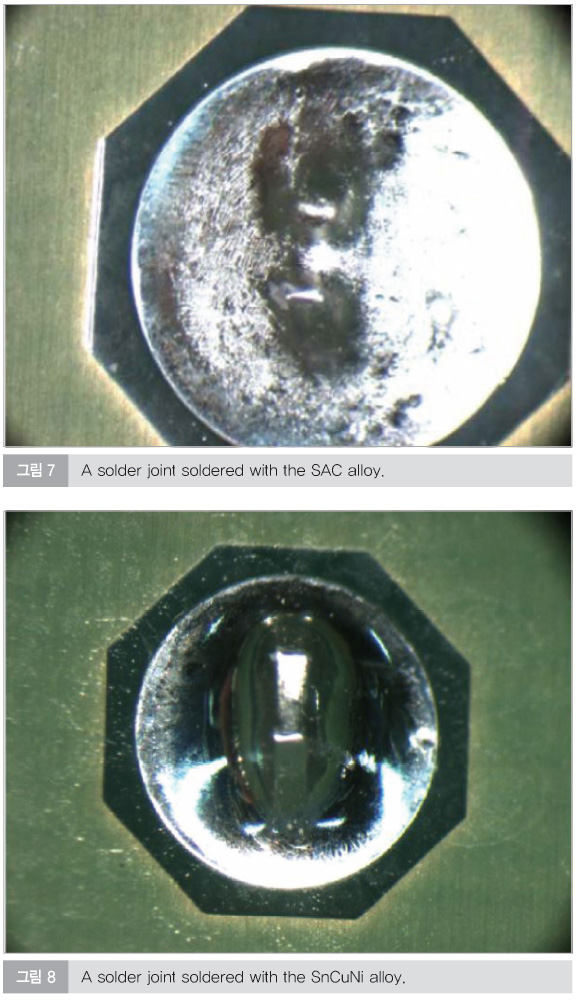
솔더 볼링
그림 9에서는 SAC 솔더로 납땜된 PCB에서만 솔더볼이 검출되었음을 보여주고 있다. SnCuNi 솔더로 납땜된 보드에서는 어떠한 솔더 볼도 발견되지 않았다. SAC 솔더를 사용한 솔더 볼링은 SAC와 SnCuNi 솔더 간의 특성 차이로 인해 발생할 수도 있다. 한편, SAC 솔더에서는 질소 비활성 분위기가 적용되었다. SnCuNi 솔더에서는 질소 분위기가 사용되지 않았다. 질소 비활성 분위기는 솔더볼의 양을 증가시킨다. SAC 솔더의 크고 많은 양의 솔더 볼은 질소 납땜 분위기로 인해 발생할 수도 있다.
OSP 표면 처리된 PCB보다 immersion-Sn 표면 처리가 된 PCB에서 더 많은 솔더 볼이 존재했다. 그러나 immersion-Sn 및 OSP 표면 처리가 된 PCB는 서로 다른 PCB 제조업체에 의해 제조되었다. PCB 상에 사용된 솔더 마스크는 달랐다. 솔더링 마감재는 동박 표면 위에 처리되었다. 솔더 볼이 놓이는 PCB 적층판에 솔더 마스크를 놓았다. Immersion-Sn PCB에 사용된 솔더 마스크가 솔더에 더 매력적이고, OSP로 표면 처리된 PCB 보다 immersion-Sn PCB 상에 더 많은 솔더 볼이 존재했던 이유일 가능성이 크다.
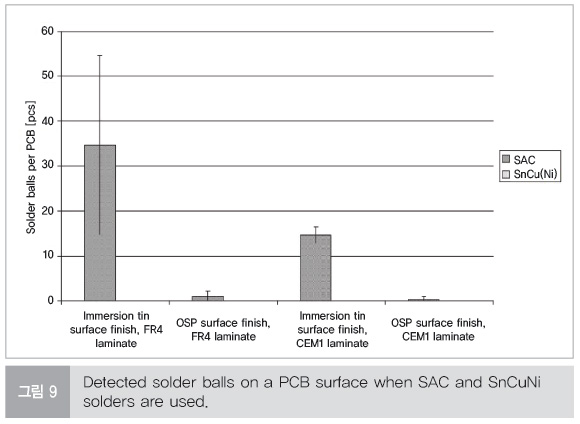
솔더 브릿지
그림 10에서는 부품들 간의 솔더 브릿지를 보여주고 있다. 솔더 브릿지는 SAC 솔더에서만 감지되었다. SAC 솔더에서 감지된 솔더 브릿지는 SAC 및 SnCuNi 솔더 간의 특성 차이로 인해 발생할 수도 있다. 반면에 솔더 브릿지는 PCB 컨베이어 속도에 비해 솔더 유량속도에 크게 의존한다. PCB 컨베이어 속도에 비해 유량 속도는 SAC 공정에서보다 SnCuNi 공정에서 더욱 최적화될 가능성이 있다.
FR4 적층판 사용 시 OSP 표면처리 된 PCB보다 immersion Sn 표면처리 PCB에서 더 많은 솔더 브리지가 감지되었다. 더 많은 양의 솔더 브리지 현상은 솔더 볼링의 발생과 동일한 이유일 가능성이 크다: 솔더 마스크가 서로 다르고 솔더 브릿지 양이 표면 마감 특성에 따른 솔더 마스크 특성이 다르기 때문이다. CEM1 적층판의 경우, 솔더 브릿지에서 immersion-Sn과 OSP 표면처리 간의 어떠한 차이가 발견되지 않았다.
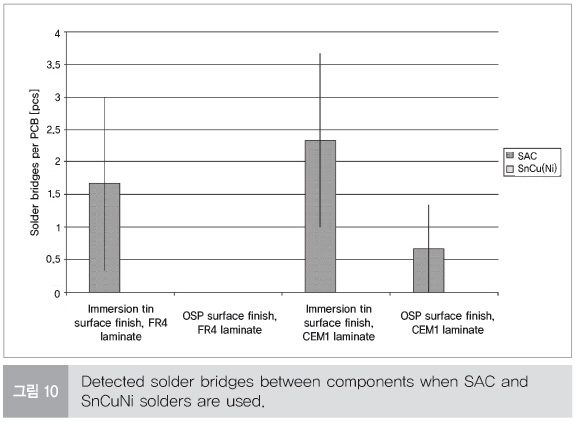
쓰루홀 충진
충분하지 못한 쓰루홀 충진 현상은 무연 웨이브 솔더링에서 나타나는 전형적인 문제이다. 더 긴 솔더 접촉 시간 및/또는 더 높은 솔더 온도를 적용하면 더 우수한 쓰루홀 충진을 이룰 수 있다. 그림 11, 그림 12, 그림 13, 그림 14에서는 SAC와 SnCuNi 솔더가 사용되었을 때 4핀 male row 커넥터, 25핀 D-SUB 커넥터, 전해 콘덴서 직경/높이(d/h) 5/11mm 및 전해 콘덴서 d/h 12.5/25mm 상의 쓰루홀 충진을 보여주고 있다. 적용된 표면 마감재는 OSP와 immersion-Sn이었다. 커패시터와 함께 사용되는 커다랗고 감소된 접지면이 있다. 줄어든 접지면으로 커패시터 상에 더 적은 열량이 존재했다.
그림 11~그림 14에서는 SAC 솔더가 SnCuNi 솔더보다 우수한 쓰루홀 충진이 있었음을 보여주고 있다.
▶ OSP 표면 처리된 PCB의 4핀 male row 커넥터(그림 11)
▶ OSP 표면 처리된 PCB의 25핀 D-SUB 커넥터(그림 12)
▶ OSP 표면 처리된 PCB의 줄어든 접지면의 전해 커패시터 5/11mm(d/h)(그림 13)
다른 시험된 경우에 SAC와 SnCuNi 솔더 간에 차이가 없었다(그림 11~그림 14). 또한, 그림 11~그림 14에서는 immersion-Sn PCB 마감이 OSP 표면 마감보다 우수한 쓰루홀 충진을 제공하고 있음을 보여주고 있다.
▶ SnCuNi 솔더가 사용되었을 때의 4핀 male row 커넥터(그 림 11)
▶ SnCuNi 솔더가 사용되었을 때의 25핀 D-SUB 커넥터(그 림 13)
▶ 전해 콘덴서 5/11mm(d/h) (그림 12)
▶ SnCuNi 솔더가 사용되었을 때 줄어든 접지면의 전해 커패 시터 12.5/25mm(d/h)(그림 14)
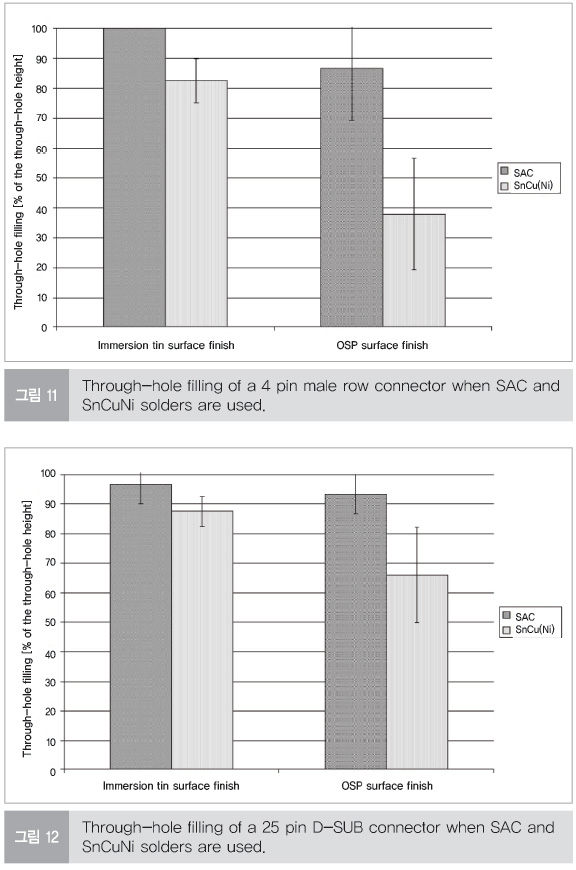
다른 시험에서는 immersion-Sn과 OSP 표면 마감 간에 차이가 없었다(그림 11~그림 14).
그림 13과 그림 14는 전해 콘덴서 5/11mm(d/h)와 12.5/25mm(d/h) 양쪽에서 대형 접지면일 때보다 줄어든 접지면일 경우 현저하게 우수한 쓰루홀 충진이 이뤄졌다는 점은 주목할 만한 하다. 적용되는 전기 부하와 같은 기술적 요소가 허용될 때, 줄어든 접지면이 무연 솔더링에 사용되어야만 한다.
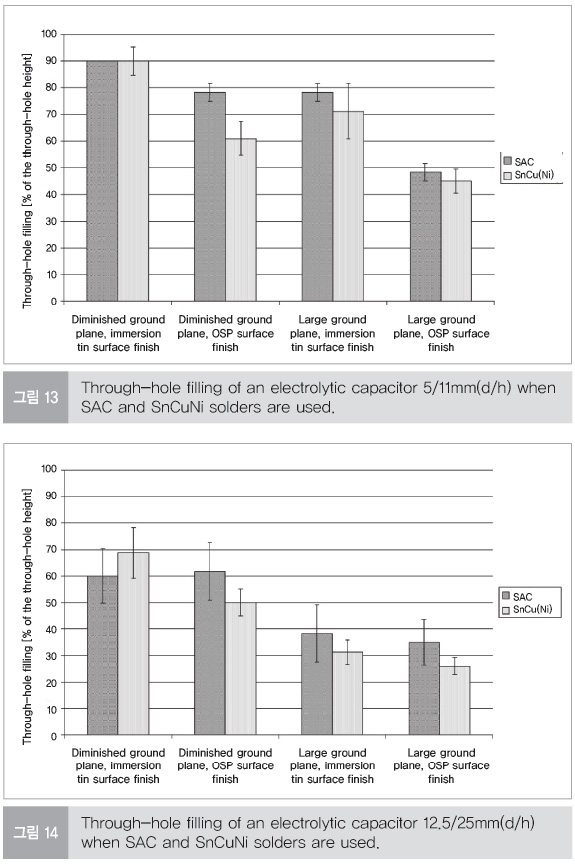
필렛 리프팅
그림 10에서는 부품들 간의 솔더 브릿지를 보여주고 있다. 솔더 무연 솔더는 동박 패드로부터 솔더 필렛이 이동하는 필렛 리프팅 현상이 발생하기 쉽다(그림 15). 또한 무연 솔더 접합부에서 패드 리프팅(그림 16)이 발생할 수도 있다. 전자 어셈블리에서 필렛 리프팅 현상을 평가하기 위해 횡단면 분석을 수행하였다. 횡단면 분석은 4핀 male row 커넥터 및 쓰루홀 레지스터를 대상으로 실시했다. 표 5에서는 검사된 솔더 조인트와 발견된 필렛/패드 리프팅 현상을 보여주고 있다.
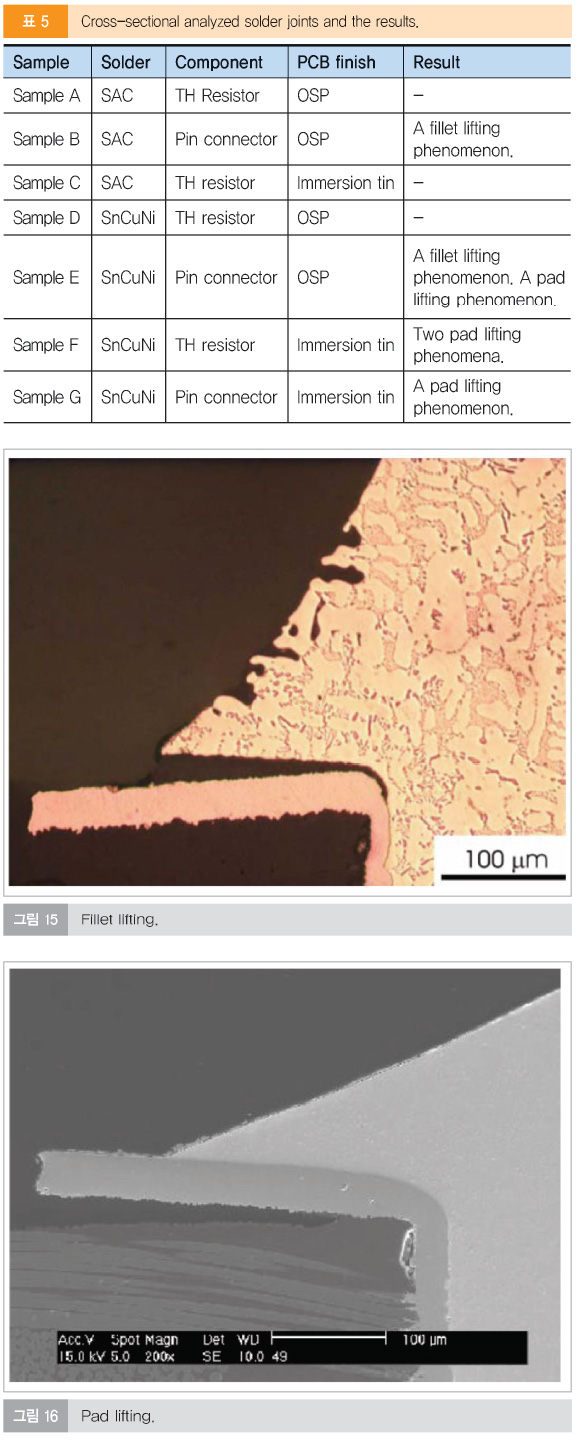
필렛 리프팅 현상은 SAC 및 SnCuNi 솔더 조인트 모두에서 발견되었다. 패드 리프트 현상은 SnCuNi 솔더로 납땜된 솔더 조인트에서만 발견되었다. SnCuNi가 SAC 솔더에 비해 패드 리프팅 가능성이 더 큰지 혹은 더 많은 양의 패드 리프팅 현상이 샘플의 작은 사이즈와 무작위인 차이인지 아니면 또 다른 불특정한 요인으로 인해 발생하는지에 대한 여부는 분명하지 않다. 이전 자료에서는 SnCuNi가 패드 리프팅 현상에 대해 더 큰 가능성을 가질 것이라는 점이 언급되지 않았다.
결론
본고에서는 웨이브 솔더링에 SAC 및 SnCuNi 솔더 합금의 적용을 비교했다. SnCuNi는 비용 문제 때문에 웨이브 솔더링에서 SAC 솔더를 대체 할 수 있는 흥미로운 솔더이다. SnCuNi는 또한 웨이브 솔더링을 고려할 때 다른 장점이 있다. SnCuNi는 납땜조 재료로 사용되는 스테인리스-스틸에 대한 공격성이 낮다. 게다가, SnCuNi는 PCB 상의 홀과 패드에서 동박을 침식시키는 것이 SAC 솔더에 비해 적다. SnCuNi 솔더 조인트는 더 밝고 전통적인 SnPb 솔더 조인트와 유사하다. SAC 솔더 조인트는 종종 거칠게 보인다. 반면, SnCuNi는 SAC 솔더보다 10℃ 더 높은 융점을 가지고 있다. 융점이 높을수록 납땜 온도가 높아져 납땜 부품에 야기되는 열 스트레스가 증가하고 솔더링 프로세스에 필요한 소비전력이 높아진다. SnCuNi는 리플로우 공정에서 솔더 페이스트로 이용 가능하지만, SAC 합금이 무연 리플로우 공정에서 훨씬 더 널리 사용된다. 리플로우 및 웨이브 솔더링에서 다른 솔더 합금을 사용하면 이후 rework 혹은 repair 공정에서 문제가 발생할 수도 있다. 여러 개의 솔더 합금이 동일한 PCB에 부품을 납땜하는데 사용되기 때문이다. 전자 제조업체가 이 사실을 인지하고 있을 때, 생산라인의 이중 합금 적용이 좋은 대안이 될 수도 있다.
본고에서는 웨이브 솔더링 머신에 SAC 솔더와 SnCuNi 솔더를 이용하여 테스트 시리즈를 납땜하였다. 사용된 웨이브 솔더링 머신은 두 솔더 모두 다르지만 예열과 솔더 접촉 시간과 같은 솔더링 프로세스 설정을 최대한 비슷하게 유지되도록 노력했다. 어쨌든, 다른 솔더링 머신으로 인해 솔더 웨이브 구조가 달라서 솔더링 품질에 영향을 줄 수도 있다. 또한 SAC 공정에는 비활성 솔더링 분위기에서 진행했고, SnCuNi 솔더링 공정에서는 일반 대기 분위기에서 실시했다. 비활성 솔더링 분위기는 솔더링 습윤성을 향상시킨다. 반면 SnCuNi 솔더링 공정의 납땜조 설정 온도는 SAC 솔더링 공정보다 5℃ 높았다. 솔더 온도를 높이면 비활성 솔더링과 비슷하게 젖음 시간이 단축된다. 양쪽 웨이브 솔더링 머신에는 스프레이 플렉서와 복사 및 대류로 가열되는 예열 유닛이 있었다. 사용된 플럭스는 두 공정 모두 동일했다.
솔더링 품질은 X-선 현미경을 통해 시각적으로 검사하였다. 횡단면 분석은 필렛 리프팅 현상을 발견하기 위해 실시되었다. SnCuNi 솔더보다 SAC 솔더에서 더 많은 솔더 볼과 솔더 브리지가 검출되었다. SAC 및 SnCuNi 합금의 서로 다른 솔더 특성에 의해 차이가 발생할 수도 있다. 한편, SAC 솔더링 공정에 사용되는 비활성 질소는 솔더 볼의 양을 증가시키는 것으로 알려져 있다. SnCuNi 납땜 공정에서 비활성 질소를 사용하지 않았다. SAC 합금에서의 더 커진 솔더볼 양은 비활성 솔더링 분위기의 사용으로 인해 발생할 수도 있다. 솔더 브리징은 PCB 컨베이어 속도 대비 솔더 유동율이 크게 작용하였다. PCB 컨베이어 속도 대비 솔더 유동율은 SnCuNi 합금보다 SAC 합금이 더 적합하며, 이는 SAC 합금으로 납땜된 PCB 상의 솔더 브릿지를 유발했을 가능성이 있다.
4개의 다른 부품의 쓰루홀 충진을 검사했다. 검사에 사용된 부품은 4핀 male row 커넥터, 25핀 D-SUB 커넥터, 5/11mm(d/h) 및 12.5/5mm(d/h) 크기의 전해 커패시터 2개였다. 이들 모두는 웨이브 솔더링에 사용되는 전형적인 부품들이다. 전해 커패시터의 경우 PCB 상에 가벼운 열 질량을 지닌 크고 작은 두 개의 접지면 유형이 있다. 여러 번의 실험을 통해 SnCuNi의 쓰루홀 충진이 SAC의 쓰루홀 충진보다 나쁘다는 점을 알 수 있었다.
줄어든 접지면의 커패시터 상의 쓰루홀 충진은 대형 접지면보다 더 좋았다. 접지면의 크기는 무연 웨이브 솔더링에서 중요한 요소이다. 줄어든 접지면은 적용되는 전기 부하와 같은 다른 요소가 허용될 때 항상 사용되어야 한다.
OSP 표면 처리보다 immersion-Sn 표면 처리가 된 PCB에서 더 좋은 쓰루홀 충진이 이뤄졌다. 반면에 OSP 표면 처리보다 immersion-Sn 표면 처리된 PCB에서 더 많은 솔더 브릿지 및 솔더 볼링이 감지되었다. 그러나 솔더링 및 브리징의 차이점은 솔더링 마감의 차이점보다 솔더 마스크의 차이로 인한 것임을 알아야 한다. Immersion-Sn 표면 처리된 PCB의 솔더 마스크는 OSP 표면 처리 PCB의 솔더 마스크보다 더 매력적이었다.
SAC 및 SnCuNi 솔더 합금으로 납땜한 솔더 조인트에서 필렛 리프팅 현상이 발견되었다. 또한 SnCuNi 솔더 조인트에서 몇 가지 패드 리프팅 현상이 발견되었다. SnCuNi 솔더 조인트에서 패드 리프트 현상이 많이 발생하는 이유는 알려져 있지 않다.
본 연구를 통해, SnCuNi가 비용 효율적인 무연 웨이브 납땜 공정에서 SAC 합금의 적절한 대안이 될 수 있음을 알 수 있었다. SnCuNi의 쓰루홀 충진은 SAC 솔더와 유사한 공정 설정일 때 SAC보다 다소 열악한 것으로 검출되며, 더 긴 솔더 dwell time 및/또는 더 높은 솔더링 온도를 사용하면 도움을 받을 수 있다. 이 경우 높아진 열 스트레스에 대한 부품의 내구성이 보장되어야 한다.