차세대 마이크로파 전자기기 및 안테나용 적층 기술 소개
레졸루션 진화로, 고신뢰성 패키징 제조 가능
집적 회로의 인터커넥트와 안테나 제작을 위한 3D 및 잉크젯 프린팅의 활용은 매우 흥미로운 연구 대상이다. 자동차 레이더 및 5G 무선 솔루션과 같은 특정 애플리케이션의 고객 맞춤형 제작이 가능하기 때문이다. 본 고에서는 프린팅된 비아, 램프 인터커넥트 그리고 와이어본드를 포함한 적층 제조 방법을 사용하여 MMIC와 인터페이스 하는 다양한 방법을 알아본다. 또한, 기존 제조 방법으로는 비용이 많이 들고 달성하기 어려운 우수한 대역폭과 원편광(circular polarization)이 존재하는 완전한 적층 제조 안테나의 시연도 포함하였다. 마지막으로 본 고에서는 고전력 디바이스, 냉각 기능을 포함한 패키징을 포함하고 전자기 간섭 차폐(EMI)와 유연성을 위한 색다른 재료를 사용하는 적층 제조 산업계의 미래 방향도 소개한다.
요약
본 고에서는 마이크로파 및 밀리미터파 애플리케이션용 3D 프린팅과 잉크젯 프린팅 제조기술의 집적화에 대해 논의한다. 최근 3D 및 잉크젯 프린팅 기술의 발전으로 레졸루션이 50㎛까지 내려감으로써, 밀리미터파 애플리케이션에서 작동하는 전자부품과 안테나를 제작할 수 있게 되었다. 3D 프린팅을 활용한 적층 제조의 가능성으로 인해 설계자는 특수 애플리케이션용 맞춤형 부품과 디바이스를 만들 수 있으며, 전자기기의 프로토타입 설계에 있어서 우수하고 저렴한 방법을 누릴 수 있게 되었다. 프린팅이 가능한 여러 재료를 결합하면 인덕터, 커패시터, 다이오드 및 트랜지스터와 같은 수동/능동소자의 기본 구성요인인 전도성, 유전체 및 반도체 여러가지 재료의 수직적 통합이 가능하다. 또한, 드롭-온-디멘드(drop on demand) 프린팅 방식은 포토리소그래피와 같은 기존의 미세 가공 공정에 필요한 절삭 가공 프로세스의 사용을 없앨 수 있고, 제조 비용 및 재료 낭비를 크게 줄일 수 있다.
집적 회로의 인터커넥트와 안테나 제작을 위한 3D 및 잉크젯 프린팅의 활용은 매우 흥미로운 연구 대상이다. 자동차 레이더 및 5G 무선 솔루션과 같은 특정 애플리케이션의 고객 맞춤형 제작이 가능하기 때문이다. 본 고에서는 프린팅된 비아, 램프 인터커넥트 그리고 와이어본드를 포함한 적층 제조 방법을 사용하여 모놀리식 마이크로웨이브 집적회로(MMIC)와 인터페이스 하는 다양한 방법을 알아본다. 이러한 구조를 이용해, 정합과 손실과 같은 마이크로파의 특성이 개선될 수 있는데, 이는 개별 디바이스와 일치하는 맞춤형 프린팅 인터페이스의 용이성 때문이다. 또한, 기존 제조 방법으로는 비용이 많이 들고 달성하기 어려운 우수한 대역폭과 원편광(circular polarization)이 존재하는 완전한 적층 제조 안테나의 시연도 포함하였다. 마지막으로 본 고에서는 고전력 디바이스, 냉각 기능을 포함한 패키징을 포함하고 전자기 간섭 차폐(EMI)와 유연성을 위한 색다른 재료를 사용하는 적층 제조 산업계의 미래 방향도 소개한다.
서문
적층 제조는 매우 빠른 프로토타입 제작 구현과 저비용 제조를 보증하기 때문에 지난 10년간 많은 관심을 받고 있다. 리드 타임이 한 달 걸리는 일반적인 부품을 단 며칠 또는 몇 시간 내에 제작할 수 있다. 매년 3D 적층 프린팅이 가능한 재료가 시장에 출시되고 있으며, 이를 통해 3D 프린팅을 새로운 애플리케이션에 활용할 수 있게 되었다. 적층 제조의 한 영역은 잉크젯 프린팅 방식으로, 이는 금속, 유전체 및 반도체 잉크를 거의 모든 표면에 빠르게 증착할 수 있으며, 넓은 영역의 디바이스를 고정밀도로 프린팅하려면 드롭-온-디`멘드(drop on demand) 방식이 유리하다. 잉크젯 프린팅은 매우 빠르고 비용이 저렴하며 밀리미터파 주파수의 애플리케이션에 활용되어 빠른 프로토타입 제작과 롤-투-롤 제조가 가능하다.[1] 또한 잉크젯 프린팅의 드롭-온-디멘드 특성은 저온(<200℃) 프로세스 가능이다. 그래서 고온 PVD 시스템을 사용하지 않고도 금속은 기판 위에 직접 증착된다. 이를 이용하면, 플렉시블 기판은 벤딩 혹은 휨 없이 쉽게 금속화된다. 적층 제조의 또 다른 영역은 3D 프린팅이다. 3D 프린터는 모델을 매우 얇은 레이어로 슬라이스하기 위해 3D 모델과 슬라이서를 활용하고, 이들 레이어를 이용하여 모델을 재생성한다. 전통적으로 3D 프린트는 압출 적층 조형(FDM, Fused Deposition Model) 방식을 활용하여 제작되었다. 이 방식은 폴리머 필라멘트(일반적으로 PLA 또는 ABS 소재)를 녹이고 압출하여 모델을 레이어별로 만든다. 그러나 모델이 광활성 수지 배스 내의 플랫폼에 모델이 제작되는 새로운 SLA(stereo lithography) 시스템은 일반적으로 매우 높은 레졸루션(10㎛)의 프린팅 레이어를 생성할 수 있다. SLA 프린팅의 또 다른 큰 이점은 수백 나노미터급의 표면 거칠기이다.[2] 이 두 가지 요소가 3D SLA 프린팅 부품을 고주파수의 밀리미터파 애플리케이션에서 활용할 수 있게 한다.
본 고에서는 3D 및 잉크젯 프린팅을 모두 사용하는 고주파 애플리케이션용 설계의 몇 가지 주제를 살펴볼 것이다. 커패시터 및 인덕터와 같은 RF 수동소자의 완전한 잉크젯 프린팅에 관한 디자인을 제시할 것이다. 이 디바이스들은 RF 시스템에 중요하며 임피던스 정합 및 DC/RF 초크를 비롯한 다양한 방식으로 사용된다. 이 디바이스들은 동일한 프로세스에서 동일한 잉크젯 프린터로 쉽게 제조될 수 있으므로, 시간과 비용을 절약할 수 있다. 다이 인터커넥트와 같은 다른 수동소자에 관해서도 설명한다. 와이어본딩을 대체하는 완전한 적층 제조 인터커넥트는 하나의 스마트 패키지에 다양한 기능을 포함하는 스마트 패키징 설계에서 혁신적인 방법이다. 다음으로, 고급 3D 프린팅 안테나를 소개한다. 기존 제조기술로 제작하기 어렵거나 불가능했던 복잡한 구조를 이 특정 안테나를 통해서 구현할 것이고, 프로토타입 생산 시간을 대폭 단축한다는 점을 보여줄 것이다. 이러한 안테나는 높은 대역폭 또는 또 다른 부품과의 집적 용이성과 유리한 기능을 제공한다. 마지막으로, 본 고에서는 향후 연구 주제를 제안할 것이다.
잉크젯 프린팅 수동소자
일반적으로 RF 시스템 내의 발룬(balun), 커패시터 및 인덕터는 신호 조정, 임피던스 정합, 커플링/초크(coupling/choking) 애플리케이션에서 사용된다. 이들 디바이스는 RF 애플리케이션에서 중요한 역할을 담당하는데, 신호 유실이 적고 품질(Q) 계수가 높아야 한다. 일반적으로 0603과 같은 표준형 표면실장패키지의 집중 부품(lumped component)은 회로 보드에 배치되고 솔더링된다. 그러나 이러한 패키지는 길고 부피가 크며 플렉시블한 기판이 구부러질 때 뜯어질 수도 있다. 잉크젯 프린팅 커패시터 및 인덕터는 LCP와 같은 플렉시블한 기판에 프린팅될 때, 굽힘을 견딜 수 있는 평면 구조, 컨포멀 및 저손실 특징을 가지고 있다. 게다가, 금속화 및 유전체 증착과 같은 일반적으로 많은 제조 단계를 거쳐야 하는 부품은 하나의 잉크젯 프린팅 프로세스로 완료될 수 있다. 드롭-온-디맨드의 적층 제조 측면에서도 낭비가 적어 대량 프린팅 시 상당한 비용을 절감할 수 있다.
MIM(Metal insulator metal) 커패시터
MIM(Metal insulator metal) 커패시터는 가장 기본적인 싱글 레이어 소자이다. 이 커패시터는 유전체로 분리된 두 개의 금속 전극으로, 둘 다 잉크젯 프린팅 방식으로 제작할 수 있다. 금속 전도 레이어의 경우에는 은 나노입자(silver nano particle, SNP)가 프린팅되고, 유전체 절연 레이어의 경우에는 얇은 필름(>0.5㎛)에 PVP(polyvinylpyrrolidone)가 프린팅되거나 두꺼운 필름(>3㎛)에 에폭시 기반 네거티브 포토레지스트가 프린팅된다. 이를 통해 더 두껍거나 더 얇은 유전체를 프린팅하거나 전극 영역을 변경하는 등 커패시턴스 값을 다양하게 제어할 수 있으므로 최종 애플리케이션에 따라 설계 사양을 완벽하게 제어할 수 있다. 폴리이미드 기판에 제작된 플렉시블한 MIM 커패시터는 >1GHz[3]의 자기공명주파수(self-resonance frequency, SRF)를 나타내지만, 그림 1에서와 같이 1.6㎛ ~ 1.8㎛ 두께의 PVP 유전체 및 SNP 금속 전극으로 제작된 MIM 커패시터는 SRF 1.2GHz, 최대 Q 계수 25, 면적당 커패시턴스 33pF/㎟[4]를 가지고 있었다.
발룬 및 인덕터
인덕터와 발룬은 유사한 나선형 구조이다. 발룬은 일반적으로 신호 조정 애플리케이션에서 평형 신호를 불평형 신호로 변환하거나 그 반대로 변경하는 역할을 한다. 그림 2의 (a)와 (b) 각각에서 표시된 것처럼, 발룬 기반 변압기는 5-레이어 구조 내에 3개의 권선을 통합하고 있다.[5] 발룬 변압기는 복잡한 구조를 보여주고 있으며, 적층 잉크젯 프린팅을 사용하여 제작될 수 있다. 상당한 인덕턴스 값을 얻기 위해 긴 전도성 트레이스가 필요하므로 인덕터는 유사한 권선 구조로 되어 있다. 1.5턴(turn) 인덕터는 전도성 금속으로 SNP 잉크를 사용하였고, 유전체 레이어 분리막으로 네거티브 포토레지스트 잉크 기반 에폭시로 제작되었으며, 1GHz에서 21의 Q 계수를 나타냈다.[6] 양쪽 애플리케이션은 본질적으로 다층 구조이지만, 이들 시연에서는 고주파에서 동작할 수 있는 잉크젯 프린팅 다층 RF 부품의 용이성과 프로세스 단계를 줄일 수 있는 잉크젯 프린팅을 활용함으로써 달성할 수 있는 집적의 레벨을 보여주고 있다.
인터커넥트
인터커넥트는 기능성 전자 시스템에서 모든 마이크로전자 디바이스의 실제 구현에 필요한 필수 패키징 요소이다. 특히, 1차 인터커넥트는 마이크로전자 칩 또는 다이와 패키징 기판과의 연결을 책임지고 있다. 최신 무선기기 시스템에서, 패키징 기판은 전통적으로 패키징된 기성 부품에 금속성 리드프레임, 신호 팬아웃 및 재분배를 위해 라미네이트 기반 인터포저 형태를 취하거나 혹은 기본 호스트 기판에 다른 패키지 부품으로 직접 집적된 부품이 존재한 PCB 형태를 보인다. 이러한 패키징 구조에서는 신호 패드 위치, 열 경로 관리 및 인터커넥트된 디바이스 아래의 신호 라우팅을 포함한 여러 설계 요인에 따라 전통적으로 와이어본딩 혹은 플립칩 기술로 1차 인터커넥터가 이뤄진다. 와이어 및 리본 본딩 기술이 칩과 기판을 상호 연결하기 위한 빠르고 저렴하며 성숙한 방법이지만, 늘어나는 기생 인덕턴스와 기계적 안정성이 실제 환경에서 고려되어야 할 중요한 문제이다.[7] 무선용 부품, 패키지 및 시스템의 발전에 맞춰 적층 제조기술이 최근 성장함에 따라 1차 인터커넥트는 온전한 프린팅 3D RF 인터커넥트 전환을 실현하기 위한 잉크젯과 3D 프린팅 제조 방법의 통합을 조사하는데 주요 후보이다.
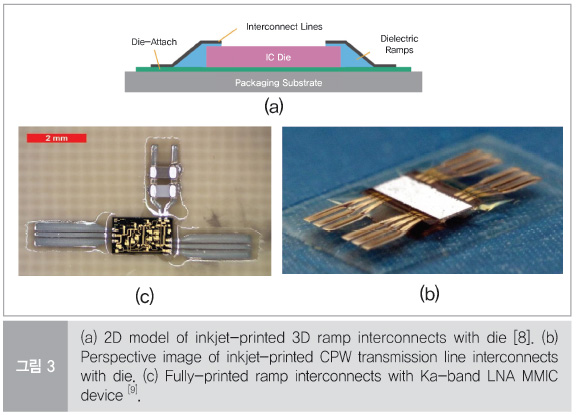
인터커넥션 프로세스에 있어서 적층 제조기술을 사용하면 낮은 기생 인덕턴스, 높은 기계적 신뢰성 및 향상된 시스템 레벨 재구성 가능 등 기존 와이어본딩 솔루션의 몇 가지를 개선할 수 있다. 낮은 기생 인덕턴스는 와이어본드 루프 길이의 감소를 통해 이뤄지며, 프린팅된 인터커넥트는 컨포멀 로우-프로파일 방식으로 실현된다. 기계적 신뢰성은 열초음파 본딩 프로세스의 제거와 프린팅 기술의 컨포멀 특성을 통해 개선될 가능성이 있다. 마지막으로, 인터커넥션 관련 프린팅 기술은 안테나 및 수동소자와 같이 서로 다른 시스템-레벨 부품을 제조하는 데 현재 사용되고 있는 방식과 같다. 패키징, 신속한 시스템 프로토타입 제작 그리고 제품 개발을 위한 단일 툴 솔루션으로 사용할 수 있다. 그림 3의 (a)는 폴리머 및 금속 기반 잉크를 잉크젯 프린팅에 활용한 완전 프린팅 램프 인터커넥션 방법의 2D 모델을 보여주고 있다.[8] 첫째, 패턴이 규정된 다이 어테치로 폴리머 잉크를 사용하여 다이를 기판에 부착한다. 다음으로, 폴리머 잉크가 프린트되어 호스트 기판에서 다이의 상단 표면으로의 3D 램프 전송을 패턴화한다. 마지막으로, 은 나노입자 기반 잉크를 인쇄하여 다이의 패드까지 RF 인터커넥트를 패턴화한다. 그림 3의 (b)에서는 잉크젯 프린팅을 통해 제조된 동일평면도파관(Coplanar Waveguide, CPW)의 1차 인터커넥트 이미지를 보여주며, 다이의 상단 표면에 직접적으로 50Ω의 전송 라인을 패턴화할 수 있음을 강조하고 있다. 이러한 램프는 그림 3의 (c)[9]에 표시된 것처럼 Ka-대역 초고주파집적회로(Ka-band monolithic microwave integrated circuit, MMIC) 저잡음 증폭기(LNA) 장치와 같은 능동 무선 부품과 직접 통합될 수 있다.
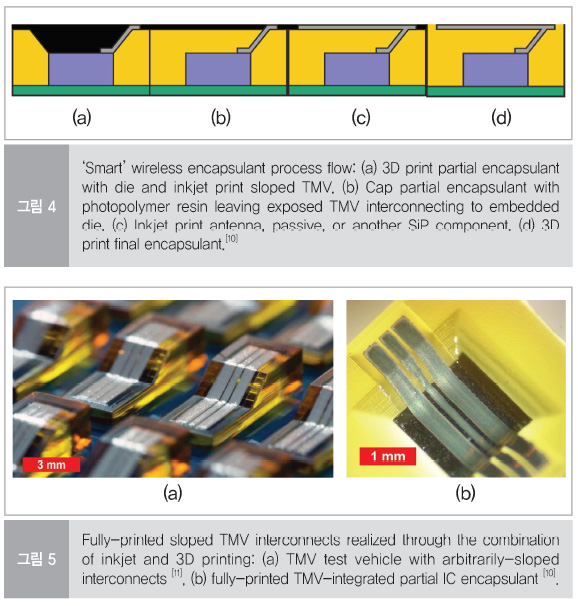
잉크젯 프린팅 프로세스가 1차 인터커넥션용 다양한 솔루션을 제공하지만, 3D 프린팅 기술의 통합은 3D SiP(system-in-package) 마이크로전자 패키징 구조의 개선을 위한 추가 설계 플레인을 도입시키기에 충분하다. 패키지의 기능적 다양성을 구축하기 위해서 패키지 내 안테나, 수동소자, 센서 등과 같은 부품들과 열 관리용 미세 유체 아키텍처를 포함하도록 확장되기 시작했다. 이러한 재구성 가능한 애플리케이션별 시스템 패키지 또는 ‘스마트’ 패키지는 그림 4[10]에 제시된 프로세스 플로우에 설명된 대로 잉크젯 및 3D 프린팅 기술의 통합을 통해 실현된다. 이 프로세스의 하이라이트는 IC 봉지재의 취급으로, 일반적으로 외부환경으로부터 디바이스를 보호하기 위해 에폭시 몰딩 컴파운드(EMC)가 부착되고 인터커넥트된 다이에 전사 성형되는 전통적인 마이크로전자 패키징 절차의 마지막 단계에서 수행된다. 적층 프린팅 기술을 사용하여 봉지재 부품에 기능이 추가되는 쓰루-몰드 비아(TMV) 구조를 구현할 수 있다. TMV 구조에서는 봉지재 내에 내장된 멀티 플레인으로 IC 다이를 인터커넥션 할 수 있다. 이러한 TMV는 잉크젯과 3D 프린팅 방법의 통합을 통해 제작된다. 그림 5의 (a)에서는 밀리미터파용 디바이스 패키징을 위한 3D/잉크젯 프린팅된 경사진 CPW TMV 인터커넥트의 투시 이미지를 보여주고 있다.[11] 다양한 램프 경사에 관한 연구 노력이 최대 경사 65° 및 길이당 손실 0.6dB/mm 미만의 CPW TMV를 달성하는 데 이바지했다. 그림 5의 (b)에서는 잉크젯과 3D 프린팅의 조합을 통해 실현된 CPW TMV-집적 부분 IC 봉지재의 개념 검증 시연을 보여주며, 이는 그림 5[10]에 표시된 회로도에 해당한다. 완전히 프린팅된 TMV는 다양한 새로운 무선 애플리케이션을 위한 애플리케이션별 기능성을 갖춘 고도로 재구성 가능한 ‘스마트’ 패키지 개발의 기본 구성요소가 되었다.
적층 제조 안테나
3D 프린팅은 3D 호환 재료로 제작된 2D 평면 구조와 달리 진정한 자유형 3D 구조를 생성할 수 있는 기능을 제공한다. 안테나 제작에 있어서 3D 프린팅 방법의 장점은 기존의 절삭 기술(subtractive techniques)을 사용해서는 제작할 수 없었던 복잡한 모양과 구조를 생성할 수 있다는 것이다. 3D 프린팅을 활용하여 쉽게 생성할 수 있는 복합하고 첨단화된 모양은 안테나가 고대역폭 또는 시스템 집적의 용이성과 같은 고성능 기능을 가질 수 있게 한다.
2개의 안테나에 관해 설명한다. 하나는 보로노이 테셀레이션 수학 기법(Voronoi tessellation mathematical models)을 기반으로 하는 3D 프린팅 보로노이 디스콘 테셀레이션 안테나(Voronoi discone tessellation antenna)로, >100%의 중심 주파수 대역폭을 보여주고 있다. 또 다른 하나는 집적된 발룬으로 밀리미터파 주파수에서 작동하는 완전히 적층 제조된 로그 나선형 안테나이다. 두 안테나 모두 고유의 수지를 사용하여 시판되는 3D 프린터를 사용하여 프린팅되었다.
보로노이 안테나 패턴은 3D 프린팅 구조의 기능을 잘 보여준다. 보로노이 테셀레이션은 평면을 다각형으로 세분화하여 각 다각형의 테두리 크기와 수를 사용자가 생성한 시드 점(seed point) 사이의 중간 거리를 찾고, 인접 지점 사이의 중간 지점을 찾아 결정하는 방식으로 생성된다.[12] 그래서 테셀레이션 구조는 그림 6의 (a)와 같이 디스콘 표면에 설계되고, 바닥으로부터 성장한다.
3D 구조를 프린팅한 후, 전도성 구리를 안테나 표면에 무전해 도금했다. 이것은 아크릴 표면을 PdCl2 용액으로 아크릴 표면처리 방법을 활용하여 실행한 후에 황산구리와 주석산나트륨 칼륨(sodium potassium tartrate tetrahydrate) 4수화물로 만든 수제 구리 무전해 도금 조에 담근다. 그런 다음 표면은 구리로 완전히 덮었다. 방사 패턴과 S11 측정은 각각 전방위적인 이득(gain)과 광대역 정합을 보여주는 그림 7에서 볼 수 있다.
나선형 안테나는 주로 원형 편파를 지닌 고 대역폭 안테나이다. 나선형 안테나의 두 개의 균형 잡힌 암은 좋은 원형 편파를 제공한다. 즉, 안테나를 모든 방향에서 조사하여 정렬 불량 문제를 제거할 수 있다. 나선형 안테나의 한 가지 단점은 보드 레벨 회로 또는 측정 장비와 인터페이스 할 수 있도록 신호를 불균형 신호로 변화하는 발룬이 필요한 자체 밸런스 구조이다. 일반적으로 발룬은 나선형 중앙의 끝부분에 솔더링되지만 고주파수에서와 같이 문제가 되고, 허용 오차가 매우 적기 때문에 솔더링은 바람직하지 않은 영향을 미칠 수 있다.
그림 8과 같이 적층 제작 기술의 안테나를 설계 및 제작하였다. 안테나 구조의 베이스는 시판되는 감광성 수지를 사용하여 3D 프린팅이 되었고, 안테나는 생산된 은 나노입자 잉크를 사용하여 금속화되었다. 이 안테나의 주요 특징은 마이크로 스트립을 동일 평면 스트립라인으로 전환하는데 사용하는 집적화된 발룬의 자체 포함이다. 이러한 구조를 포함하면 발룬이 마이크로 스트립라인으로 원활하게 전환할 수 있게 함으로, IC와 같은 다른 회로 부품과의 집적할 수 있다. 그림 8에서는 CAD 모델뿐만 아니라 측정 장비의 상단에 있는 제작된 디바이스를 볼 수 있다. 나선형이 프린팅된 구조는 속이 비어 있어 표준 밀링 공정에서 제조하기가 특히 어렵지만, 3D 프린터에서는 사소한 문제에 속한다. 측정된 S11 파라미터는 그림 9의 (a)에, 이득 측정값은 그림 9의 (b)에 표시되어 있다.
구리 쓰루홀 충진
대량 생산현장에서 구리를 적용한 쓰루홀 충진은 2005년에 시작되었다. X-도금 또는 브릿지 도금의 도입이 그 시작이었다. ‘브리징’ 기술은 인클루젼을 피하면서 쓰루홀을 완벽하게 구리도 충진시키기 위해 개발되었다. 이러한 완전한 충진 쓰루홀은 고주파 보드 PCB 설계에 있어서 열 전도성 및 신호무결성과 같은 많은 이점을 제공한다.
쓰루홀 충진은 페이스트로 메우거나 혹은 전해 구리 도금 공정으로 채움으로써 구현될 수 있다.
대형 홀(직경 > 500μm)의 경우, 열 전도성 페이스트를 이용한 플러깅 공법이 주로 사용되는 프로세스이다. 소형 홀(직경 < 500μm 및 가능한 종횡비 (AR > 0.5 및 < 5.0)의 경우, 브리지 도금 기술을 사용하는 구리 충전으로, 페이스트 플러깅에 비해 많은 이점이 있다. 우선 브리지 도금 기술은 페이스트 플러깅에 비해 제조 스텝이 더 적다(그림 6 참조). 생산 비용 측면에서 매우 유리하다.