다이내믹 ‘실시간’ 듀얼 헤드 디스펜싱 구조를 통한 공정 수율 향상 |
|
|
|
2024-05 자료출처 : Sunny Agarwal, ITW EAE - Camalot |
|
|
미니 XY 드라이브 시스템 채택, 수율 감소 억제
회전 보정 성능으로 생산성 증대 이뤄내
자동화된 고속 유체 디스펜싱 시스템은 높은 정확도와 반복정밀도로 기판의 복잡한 패턴을 디스펜싱하는 데 사용된다. PCB 어셈블리와 관련하여 하나의 패널 어레이로 PCB를 그룹화하는 패널화는 좋은 제조 툴이다. 대량 생산이 필요한 PCB 제조업체는 더 높은 처리량을 위해 패널화를 사용한다. 저가의 PCB 제조에서는 개별 PCB 사이의 두께와 공간에 대한 설계 제한을 해결하는 데 더 많은 비용이 필요하기 때문에 패널화가 필요하지 않을 수 있다. 이 시나리오에서 고객은 일반적으로 JEDEC tray와 같은 캐리어 트레이의 개별 PCB를 선호한다. 이러한 모든 시나리오는 동일한 기판을 개별 조각으로 배치하거나 단일 PCB 패널에 배치하여 동시에 나란히 디스펜싱하는 이중 디스펜서 밸브를 통해 처리할 수 있다. 본고는 동기식 디스펜싱 중 두 헤드의 질량 유량과 함께 점/라인 위치 정확도를 결정하는 입증된 방법을 살펴본다. 또한 직면한 문제를 다루고, 회전 보정이 기존 단일/이중 헤드 디스펜싱 시스템보다 최대 2배 더 높은 투약 생산성을 달성할 수 있는 방법에 대해 설명한다.
개요
오늘날의 독특한 어셈블리 도전과제는 복잡한 PCB 패널화에 기인하는데, 생산 현장의 설치 공간 축소 문제를 해결하고 생산 캐파 증대를 이뤄내는 동일한 PCB(Identical PCB) 구조도 여기에 포함된다. 어레이 또는 캐리어에서 일정한 간격으로 동일한 패널 내에 있는 동일한 PCB를 동시에 디스펜싱해야 한다. 이러한 모든 다품종 구조의 과제는 대세가 되었으며, 실제 생산성과 처리량에 영향을 미친다. 기존의 수동 듀얼 헤드 디스펜싱 시스템은 두 번째 헤드에 대한 회전 보정을 고려하지 않아 수율 손실을 유발한다. 두 번째 헤드의 수율 손실을 없애기 위해 미니 XY 드라이브 시스템이 장비와 통합되어 빠르고 정확한 디스펜싱을 수행해 동일한 작업 영역에서 공정 능력을 두 배로 늘린다. 다이내믹 듀얼 헤드(DDH, Dynamic dual head) 디스펜싱이란 별도의 Z축에 장착된 왼쪽 헤드에 고유한 미니 XY 드라이브 시스템을 사용하여 두 번째 부품에 정확하게 정렬 및 디스펜싱하도록 두 번째 헤드의 위치를 정밀하게 제어하는 동시에 디스펜싱하는 시스템이다. 설비의 비전 시스템은 캐리어에 개별적으로 배치된 각각의 동일한 PCB에 맞춰 기판 정렬을 수행하므로 오프셋 및 스큐(skew, 각도변화)가 변동될 가능성이 더 크다. DDH를 사용하여 두 번째 부문에 동기식 디스펜싱을 수행하는 동안 모든 운동학적 조정은 스큐 계수(Skew Factor) 및 스케일 팩터(Scale Factor)에서 계산된 값을 사용하여 수행된다. 이 기술은 타의 추종을 불허하는 정확도를 제공해 수율을 유지하면서 생산성 향상을 보장한다. DDH는 또한 모든 단계 및 반복 PCB, FPC 및 패널 설계에 있어서도 동일한 수준의 조정 및 회전 보정 성능을 제공한다. 제품에 홀수 개의 장치가 포함되어 있으면, 헤드 두 개 다 디스펜싱을 할 필요가 없으므로, 헤드 중 하나만 디스펜싱하도록 프로그래밍하여 사용하면 된다.
본고는 동기식 디스펜싱 중 두 헤드의 질량 유량과 함께 점/라인 위치 정확도를 결정하는 입증된 방법을 살펴본다. 또한 직면한 문제를 다루고, 회전 보정이 기존 단일/이중 헤드 디스펜싱 시스템보다 최대 2배 더 높은 디스펜싱 생산성을 달성할 수 있는 방법에 대해 설명한다.
소개
자동화된 고속 유체 디스펜싱 시스템은 높은 정확도와 반복정밀도로 기판의 복잡한 패턴을 디스펜싱하는 데 사용된다. PCB 어셈블리와 관련하여 하나의 패널 어레이로 PCB를 그룹화하는 패널화는 좋은 제조 툴이다. 대량 생산이 필요한 PCB 제조업체는 더 높은 처리량을 위해 패널화를 사용한다. 저가의 PCB 제조에서는 개별 PCB 사이의 두께와 공간에 대한 설계 제한을 해결하는 데 더 많은 비용이 필요하기 때문에 패널화가 필요하지 않을 수 있다. 이 시나리오에서 고객은 일반적으로 JEDEC tray와 같은 캐리어 트레이의 개별 PCB를 선호한다. 이러한 모든 시나리오는 동일한 기판을 개별 조각으로 배치하거나 단일 PCB 패널에 배치하여 동시에 나란히 디스펜싱하는 이중 디스펜서 밸브를 통해 처리할 수 있다.
표준 유체 디스펜싱 시스템에는 XY 갠트리에 장착된 디스펜서 밸브가 포함되며, 이 밸브는 기판에서 원하는 위치에 패턴을 디스펜싱하기 위해 움직일 수 있으며 컨베이어 시스템을 통해 수평적 XY 평면에 배치된다. 디스펜서 밸브는 기판 위 부품의 방향성에 따라 3차원적인 공간에 위치할 수 있다. 갠트리 시스템은 구동 메커니즘을 통해 움직이고, 모션 제어 시스템을 통해 제어된다. 패턴을 디스펜싱하기 위해 컨트롤러는 갠트리 시스템 자체에 장착된 카메라 시스템을 통해 각 기판의 위치와 방향을 결정한다. 카메라 시스템은 디스펜싱 공정 프로그램에 미리 설정된 프로그래밍 경로를 통해 기판 상단에 있는 피디셜 마크 또는 레퍼런스 포인트의 비전 캡처를 수행한다. 캡처된 레퍼런스 포인트의 비전 이미지는 XY 좌표면에서 기판의 위치를 결정하는 데 활용된다. 높이 감지는 갠트리에 장착된 높이 감지 레이저를 통해 수행되어 기판에서 디스펜서 밸브 니들 팁 위치를 결정한다. 그런 다음 모션 컨트롤러는 XY 프로그래밍된 위치에 디스펜서 밸브를 놓은 다음 디스펜서 밸브 니들 팁은 기판에서 프로그래밍된 디스펜싱 간격만큼 내려온다. 이 시점에서 디스펜서 밸브는 사전 프로그래밍된 유체 패턴을 기판에 디스펜싱하기 시작한다.
생산 처리량을 최적화하기 위해서는 원하는 거리에 자리 잡은 듀얼 디스펜서 밸브를 사용하여 동일한 PCB를 동시에 디스펜싱한다. PCB가 싱글 프로세스 패널로 패널화되는 경우, 모든 PCB는 그림 1에 표시된 것과 동일한 방식으로 수평 XY 면에서 회전해야 한다. 제 1 및 제 2 기판 정렬은 패널 본체에 있는 글로벌 레퍼런스 포인트 또는 피디셜 마크를 통해서 찾을 수 있다. 기존의 듀얼 디스펜싱 방법은 디스펜싱 전에 밸브 1과 관련해 밸브 2를 한 번에 자동 조정하도록 패턴을 자동으로 재정렬하고 글로벌 스큐만 고려했다. 따라서, 2개의 동일한 PCB는 글로벌 스큐에 따라 동시에 디스펜싱되었다.
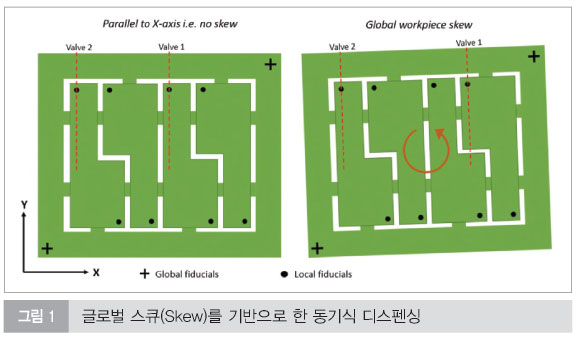
듀얼 헤드 디스펜싱의 장점
듀얼 헤드 디스펜싱은 단일 Z축에서 구동되어 각 디스펜서 밸브와 동일한 패턴을 동시에 디스펜싱한다. 대부분의 기존 기술은 X 또는 Y 방향에서 두 번째 동일한 패턴의 횡방향 이동(lateral shift)만 고려하고, 부품 간 회전은 염두에 두지 않는다. 그림 2와 같이 작동 전에 장착된 디스펜서 밸브의 X/Y축 또는 양방향으로 고정 마이크로미터 조정을 통해 횡방향 이동만이 고려된다.
기존의 듀얼 디스펜싱 방법은 동일한 기판에 능동적으로 디스펜싱하는 동안 양쪽 헤드의 동적인 실시간 조정을 하지 못한다. 트레이에서 부품이 서로 비대칭이고 글로벌 스큐만 고려되는 경우, 디스펜싱 패턴이 그림 2의 오른쪽에 표시된 것처럼 잘못 정렬된다. 트레이에 있는 개별 부품의 부품 간 회전은 제쳐두고 트레이/보드의 글로벌 정렬을 정의하는 글로벌 피디셜만 캡처된다.
부품 간 회전의 경우, 카메라 비전 시스템으로 각 개별 PCB의 로컬 피디셜 또는 레퍼런스 포인트를 캡처하기 위해서는 개별로 움직일 수 있는 이동식 갠트리 시스템이 필요하다. 부품이 올려진 캐리어 포켓 트레이보다 작은 크기의 기판 또는 부적절한 툴링 사용으로 인해 부품이 국부적으로 비뚤어질 수 있다. 따라서 기존의 디스펜싱 방법으로는 개별 부품의 스큐 각도와 스케일 팩터를 각 부품에 맞게 능동적으로 보정을 할 수 없다. 스케일 팩터는 프로세스 프로그램에 입력된 위치 정렬과 다르게 피디셜 또는 레퍼런스 포인트를 찾는 갠트리 비전 시스템에 기반을 둔다. 각 디스펜서 밸브를 개별 Z축 드라이브 시스템에 장착하면 로컬 레퍼런스 포인트 또는 피디셜을 통해 부품 간 회전을 보정할 수 있다. 부품 간 회전은 각 개별 PCB의 스큐 팩터(Skew factor)와 스케일 팩터를 고려해야 한다.
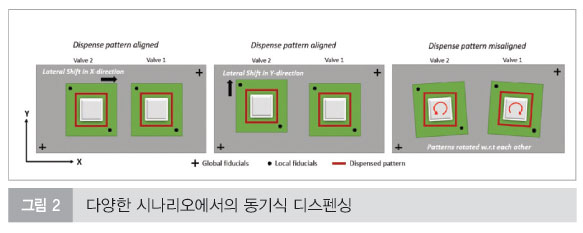
설비의 갠트리 시스템은 디스펜싱을 위해 갠트리에 부착된 첫 번째 디스펜서 밸브를 사용하여 XY 방향으로 이동하도록 한다. 두 번째 디스펜서 밸브는 디스펜싱을 위한 두 번째 디스펜서 밸브를 구동하는 자동 조정 미니 드라이브 시스템을 통해 갠트리에 연결된다. 미니 XY 구동 시스템은 두 번째 Z 축에 장착 및 구성되어 두 번째 디스펜서 밸브를 XY 방향으로 이동하여 첫 번째와 두 번째 디스펜서 밸브 사이의 간격을 조정한다. 제어부는 제 1 전자 기판 패턴 상의 첫 번째 디스펜싱 밸브와 제 2 전자 기판 패턴 상의 두 번째 디스펜싱 밸브의 토출 동작을 제어한다.
미니 드라이브 시스템에는, 갠트리 및 마운팅 블록에 고정되어 리니어 베어링을 따라 이동하게 하고 두 번째 디스펜싱 밸브에 연결된 리니어 베어링이 포함되어 있다. 자동 조정 메커니즘은 리니어 베어링을 따라 마운팅 블록을 이동시키도록 구성된 제 1 리니어 구동 모터 조립체를 포함한다. 상기 제 1 리니어 구동 모터 조립체는 기계적으로 결합된 모터에 의해 구동되는 볼 스크류 구동 리니어 액츄에이터가 포함되어 있다. 상기 자동 조정 유닛은, 상기 마운팅 블록에 고정되는 제 1 브라켓과, 상기 제 1 브라켓은 상기 리니어 베어링의 방향에 수직한 방향으로 연장되고, 상기 제 2 디스펜서 밸브에 고정되며, 상기 제 1 브라켓을 따라 구동하도록 구성되는 제 2 브라켓을 더 포함한다. 자동 조정 메커니즘은 또한 제 1 브라켓을 따라 제 2 브라켓을 이동시키도록 구성된 제 2 리니어 구동 모터 조립체를 포함한다. 제 2 리니어 구동 모터 조립체는 기계적으로 결합된 모터에 의해 구동되는 볼 스크류 구동 리니어 액추에이터가 포함되어 있다. 제 1 디스펜싱 유닛과 제 2 디스펜싱 유닛 각각에 대하여, 자동 조정 조립체는 또한 제 1 디스펜싱 유닛으로 디스펜싱 동작을 수행할 때 디스펜싱 유닛을 지지하고 하강하도록 구성되는 Z 구동 메커니즘이 포함되어 있다.
여러 개의 독립적인 디스펜싱 시스템이 때때로 디스펜싱 작업의 생산량을 증가시키는 데 사용된다. 이 솔루션은 복수의 설비 구축에 따른 비용이 많이 들며, 추가적인 제조 공간 확보가 필요하며, 경우에 따라 많은 현장 작업자가 뒷받침되어야 한다. 일반적으로 제조 현장 공간은 제한적이다. 따라서 제조 현장에서 각 제조 시스템의 ‘설치 공간’을 줄이고 운영 및 유지 보수가 필요한 개별 기계의 수를 줄이는 것이 바람직하다.
일부 업종의 경우, 여러 개의 동일한 회로 패턴이 공통 기판에 제작된다. 일반적인 예로 휴대전화용 회로 패턴을 꼽을 수 있는데, 4개 이상의 동일 패턴이 단일 기판 상에 놓여지고 있다. 이러한 경우, 회로 패턴들의 다수의 인스턴스들 사이에는 종종 고정되고 균일한 오프셋이 존재하며, 이들은 공통 기판 상에 배치되고 완료 후 타공(perforation)을 따라 서로 분리될 수 있다. 또한, 생산량 증대를 위해 다수의 디스펜싱 유닛 또는 펌프를 구비한 디스펜싱 시스템이 활용되고 있다. 이러한 시스템에서, 복수의 디스펜싱 펌프들 사이의 오프셋 거리가 여러 개의 회로 거리 사이의 오프셋 거리와 실질적으로 동일하게 조정될 수 있으며, 오프셋 조정의 정확도가 그에 따른 디스펜싱 패턴의 정확도 요건들 내에 있는 경우, 복수의 디스펜싱 펌프들은 단일 X, Y, Z 갠트리에 의해 동시에 위치하여, 동시에 동작할 수 있다.
본 연구의 주요 목적은 우수한 도트 및 라인 디스펜싱 품질과 함께 고정된 오른쪽 디스펜싱 밸브의 위치 정확도를 미니 XY 드라이브 시스템에 장착된 왼쪽 디스펜서 밸브와 일치시키기 위한 자세한 연구를 수행하는 것이다. 본 연구에는 공압 제트 펌프가 설치된 고속 디스펜싱 시스템의 사용이 포함되며, 이는 현재 디스펜싱 품질에 영향을 주지 않고 반복 가능한 방식으로 재료를 디스펜싱할 수 있다.
본 연구는 공압식 제트 펌프에 대한 실험을 수행하는 지점에서 시작된다. 노즐 히터는 유체 온도를 주변 온도 조건과 동일하게 유지하는 데 사용되었다. 본 연구는 디스펜싱 품질에 미치는 영향을 최소화하면서 미니 XY 드라이브 시스템의 견고성을 확인하기 위해 도트 및 라인의 위치 정확도를 결정하는 실험 실행을 수행하는 것으로 마무리된다. 실험에는 글래스 지그 플레이트를 사용하여 도트 및 라인 위치 정확도 테스트를 수행하는 것이 포함된다.
도트 위치 정확도
도트 위치 정확도는 도트의 어레이 디스펜싱을 통한 각 개별 도트의 입력된 위치와 실제 도트 위치 간의 차이로 측정된다. 위치 정확도는 또한 도트가 니들 끝에서 기판까지 수직(즉, 아래쪽)으로 정밀하게 쏘이게 되는지 여부(즉, 아래쪽)를 정의한다. 현장 작업자의 관점에서 볼 때, 디스펜싱은 우수한 위치 정확도로 좋은 모양의 원형과 같은 특정한 도팅 형성 및 특성이 가능해야 한다. 글래스 지그 상의 디스펜싱된 도트 측정은 XY 방향의 이동을 측정하기 위해 백라이트를 이용한 광학 측정기로 수행되었다. 각 헤드는 각 방향 당 84개의 도트를 디스펜싱했다.
표시된 방향 유형은 스마트폰 제조 보드와 유사하며, 일반적으로 그림 3과 같이 0° 또는 180° 방향의 패턴이 있다. 높이 감지는 글래스 지그 상단 표면으로부터 정확한 디스펜싱 높이를 보장하기 위해 글래스 상에서 수행된다. 각 패턴은 시계 방향 또는 시계 반대 방향으로 2° 회전하여 왼쪽 헤드 디스펜싱 정확도가 실제 동기 모드 하의 디스펜싱에서 오른쪽 헤드와 동일하다는 것을 증명하였다.

공정 능력 지수(Cpk)는 공정이 목표값에 얼마나 가까운지 그리고 공정이 평균 성능을 중심으로 얼마나 일관성이 있는지를 측정한다.
작업자는 최소한의 변동으로 수행할 수 있지만 목표에서 벗어나 여러 스펙 한계치 중 하나를 향해 이동할 수 있으며, 이는 낮은 Cpk를 나타내는 반면 Cp는 높음을 의미한다. 양쪽의 이동의 경우, Cp의 값이 크고, Cpk의 값이 낮으면 공정에서 센터링 문제가 있다는 것을 나타낸다. 공정이 가능한지 여부를 결정하기 위한 업계의 지침에 따라 일반적으로 허용되는 최소값은 1.33이다. 공정 능력은 ±3 시그마 공정에서 ±50 미크론 사양 한계에 대해 결정된다.
표 1은 왼쪽 헤드의 공정 능력이 0° 및 180° 기판 방향 모두에서 오른쪽 헤드와 동일한 것으로 확인되었음을 보여주고 있다. 또한 Cpk 값은 동기 모드에서는 실시간 다이렉트 디스펜싱에서 두 헤드에 허용되는 업계 표준보다 훨씬 높았다.
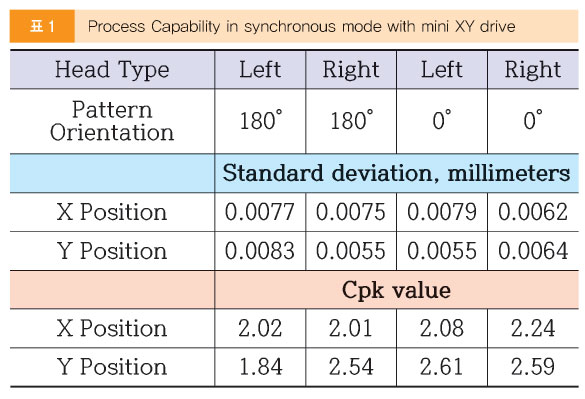
라인 위치 정확도는 프로그래밍된 라인의 위치와 실제 디스펜싱된 라인 사이의 이동으로 측정된다. 라인은 일정하고 올바른 간격으로 쌓인 일련의 점으로 구성되며 직선 및 부채꼴 모양이 아닌 라인을 형성하도록 적절하게 정렬되었다. 점들이 서로 닿으면 경계는 점들이 겹치고 포개진 형태의 울퉁불퉁한 모양이지만, 점은 더 압축되고 유체이므로 레벨링이되어 직선을 형성한다. 디스펜스 밸브가 기판에 가까울수록 라인 품질이 좋아진다.
실험 테스트는 그림 4에 표시된 글래스 정확도 플레이트에서 수행되었다. 그림 4의 (a) 패턴은 시계 반대 방향으로 1.5° 각도로 기울어지고 (b) 패턴은 시계 방향으로 1.5° 기울어졌다. (c) 패턴은 전혀 비뚤어지지 않았다. 양쪽 극단의 패턴 피치는 44mm였다. 피디셜 얼라인먼트는 칩의 가장자리 주위에 선을 디스펜싱하기 전에 수행되었다. 머신 비전 시스템은 비전 알고리즘을 통해 칩 가장자리를 파악하고, 프로그래밍된 위치 오프셋에서 칩 가장자리를 따라 라인 패턴을 디스펜싱한다. 위치 오프셋은 선택한 칩 가장자리의 중심으로부터 칩 가장자리에 수직인 방향으로 떨어진 오프셋 거리로 정의하였다. 파란색으로 강조 표시된 라인은 디스펜싱 높이 2mm에서 0.75mm의 위치 오프셋으로 디스펜싱된 것이다. 패턴은 미니 XY 드라이브 시스템 설정을 통해 동기 모드에서 듀얼 헤드로 디스펜싱해서 형성하였다.
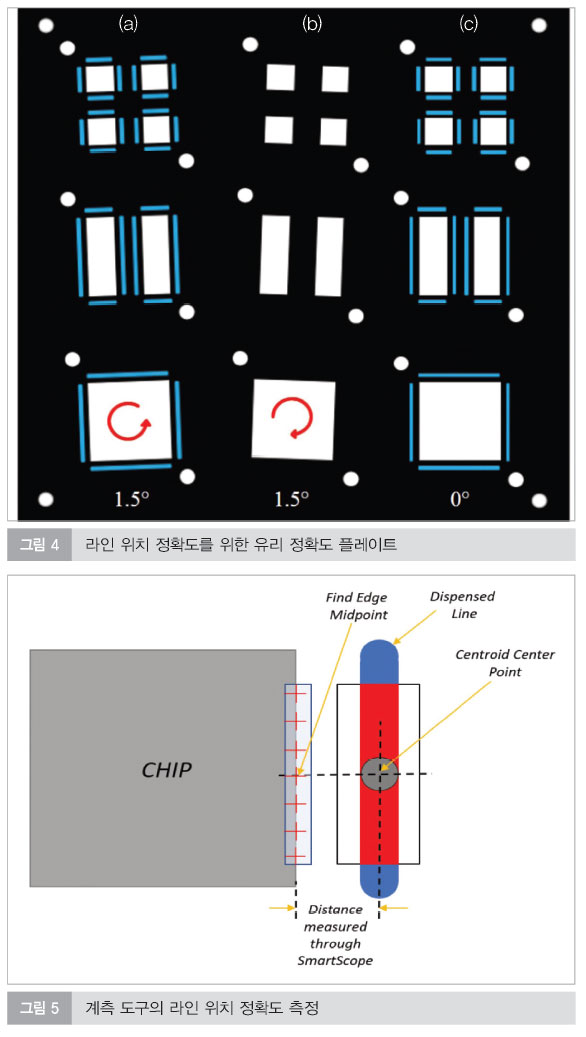
그림 5에서 보여주는 SmartScope라는 계측 도구는 디스펜싱된 라인(빨간색/파란색으로 강조 표시)에서 프로그래밍된 중심의 중심점과 프로그래밍된 칩 가장자리의 중간점 사이의 거리를 측정하도록 프로그래밍되었다. 그림 5는 계측 시스템의 다이어그램이다. 측정 한계 허용 오차는 둘레 0.75mm 위치 오프셋에서 ±50미크론이다.
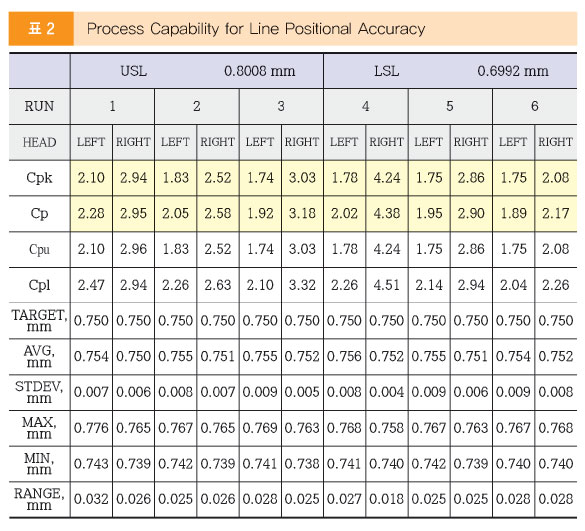
표 2에서는 대부분의 디스펜싱 작업에서 왼쪽 헤드의 표준 편차가 오른쪽 헤드의 표준 편차에 매우 근접하다는 것을 보여주고 있다.
공정 능력은 동기 모드에서 실시간 다이렉트 디스펜싱을 수행한 두 헤드 모두 업계 표준인 1.33 값보다 높았다. 오른쪽 헤드는 오른쪽 Z축에 고정된 메커니즘으로 인해 왼쪽 헤드보다 약간 높은 공정 능력을 가졌으며, 왼쪽 헤드는 왼쪽 Z축의 이동식 미니 XY 드라이브 시스템에 장착되었다. 6개 디스펜싱 모두에 대한 공정 능력 차트는 그림 6에 나와 있다.
라인 품질은 도트 위치 정확도와 원형도 측면에서의 도트 특성에 따라 달라진다. 라인 너비는 부채꼴 모양이 아닌 직선을 형성하기 위해 올바른 간격으로 디스펜싱된 일련의 점으로 정의된다. 시각 검사는 현미경을 이용해 디스펜싱 사이클 동안 위성 방울(satellite)이 형성되었는지를 확인하는 인간 기반 광학 라인 품질 검사와 관련이 있다. 시각 검사는 또한 라인이 잘못 정렬되었는지 여부를 확인하는 것과 라인이 가장자리에 잘 걸쳐져 있는지 학인하는 데 도움이 된다. 그림 7의 라인 품질은 듀얼 헤드 동기 모드에서 2개의 헤드 모두다 양호한 디스펜싱 품질을 가지고 있음을 보여준다.
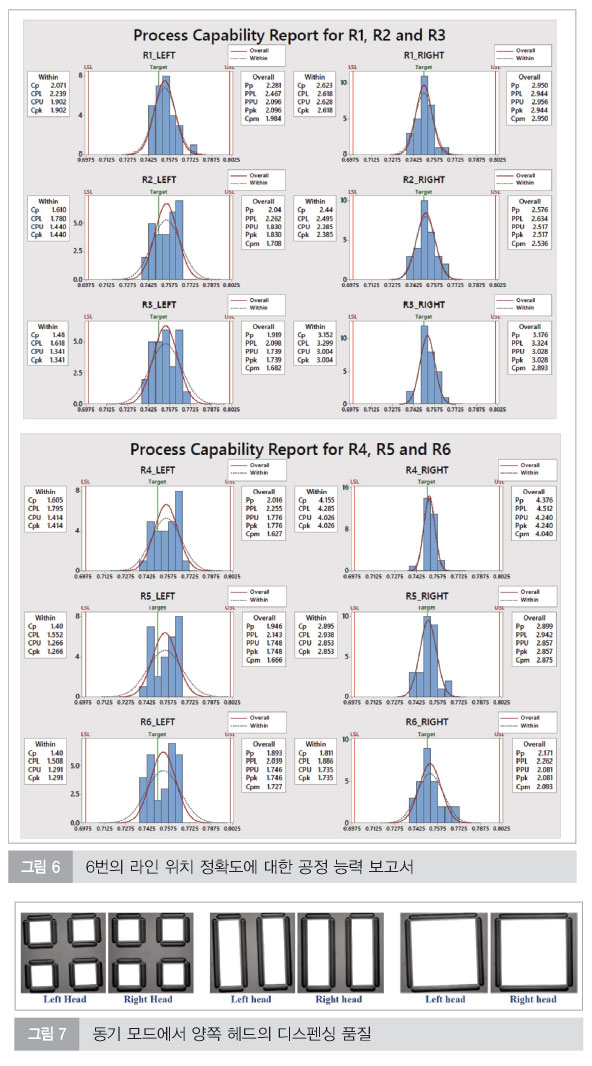
생산 환경에서의 처리량 증가는 주로 전자 디바이스 제조업체가 고객의 요구를 충족하기 위해 설정한 시간당 단위(UPH)를 충족하는 것이 중요한 요인이다. UPH는 최종 제품의 시간당 생산되는 단위 수로 산업 생산 공정을 측정하는 데 사용된다. 처리량에 기여하는 주요 요인 중 일부는 향상된 비전 캡처 및 이미징 시스템, 컨베이어 메커니즘, 강력한 소프트웨어 제어 아키텍처 그리고 일관된 디스펜싱 결과를 제공하기 위해 보다 정확하고 빠른 플랫폼에 장착된 레이저 높이 센싱이 있다.
사이클 시간 계산에는 보드 전송, 보드 클램프, 캡처 보드 피디셜, 높이 센싱, 니들 세척, 디스펜스, 보드 언클램프 및 다운스트림 이송에 대한 시간 간격이 포함된다. 총 공정 시간은 46.75% 단축되었으며, 이는 미니 XY 드라이브 시스템을 사용하여 단일 헤드를 듀얼 헤드로 전환하는 과정에서 공정 시간을 절반으로 단축하는 데 매우 근접한 수준이다. 사이클 시간 및 UPH 계산에는 16개의 제품이 들어 있는 하나의 캐리어에 대한 디스펜싱 작업이 포함된다. 표시된 UPH 및 사이클 시간 백분율은 제조업체의 대부분 시설에서 생산 환경을 시뮬레이션하기 위해 공정 프로그램에 라인 및 도트 명령을 포함하는 프로그래밍 테스트를 실행하여 계산되었다.
그림 8의 파란색 막대는 미니 XY 드라이브 시스템을 사용하여 단일 헤드에서 듀얼 헤드로 전환하는 동안 높이 감지와 피디셜 기준 기능 스캔에서 24.00% 감소했음을 보여주고 있다. 노란색 막대로 표시된 디스펜싱 시간은 49.18% 감소하여 상당한 절감 효과를 보였으며, 듀얼 헤드 다이내믹 디스펜싱으로 전환하여 디스펜싱 시간이 거의 절반으로 줄었다.
보드 로드, 니들 세척, 보드 언로드 및 보드 전송 시간은 공정에 영향을 미치지 않기 때문에 줄어들지 않았다. 원하는 높은 작동 속도는 3축 갠트리 모션과 부품 간 기계적 마찰에 의해 제한되는 짧은 시간 간격에서만 달성될 수 있다. UPH는 단일 헤드에서 동적 ‘다이내믹’ 듀얼 헤드 디스펜싱으로 전환하는 동안 87.79% 증가한 녹색 막대로 표시되었다.
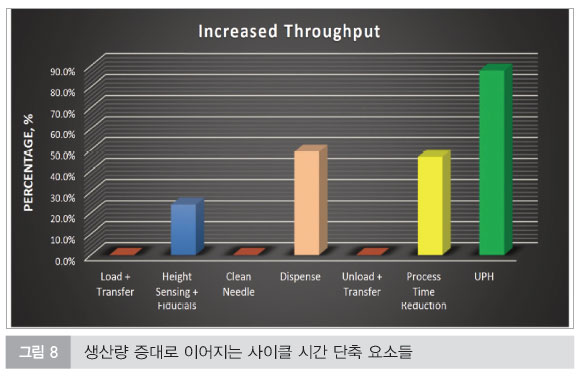
요약
미니 XY 드라이브 시스템을 사용한 듀얼 다이내믹 디스펜싱은 대량 제조 공정에 새로운 차원의 견고함을 가져왔다. 또한 멀티플 디스펜싱 펌프 간의 오프셋 거리는 여러 회로 거리 사이의 오프셋 거리와 동일하게 XY 방향으로 동적으로 조정되어 디스펜싱 시스템과 동일한 수준의 정확도를 달성한다. 이러한 방식으로 미니 XY 드라이브 시스템에 장착된 왼쪽 헤드에서 발생하는 결함 수 증가 없이 멀티플 디스펜싱 펌프는 생산성 증대에 활용될 수 있다.
±3 시그마 공정에서 점과 라인 위치 정확도 모두 Cpk 수치가 1.33보다 크면, 미니 XY 드라이브 메커니즘이 오른쪽 헤드에 근접하게 구성된 왼쪽 헤드의 정확도에 부정적인 영향을 미치지 않음을 나타낸다. 미니 XY 드라이브 시스템이 있는 듀얼 헤드의 ‘실시간 디스펜싱’ 등장으로 인해 서로 인접한 비뚤어진 동일한 기판으로 더 높은 수준의 공정 제어를 제공하여 생산 실행 중에 우수한 제품 신뢰성을 제공한다. 또한 설비가 차지하는 제고 공간이 줄어들어 생산성이 두 배 효과를 제공한다.
REFERENCE
[1]. Reid, Scott A. et al. Illinois Tool Works Inc. U.S. Patent No. 9,374,905 filed Sep. 30, 2013 and issued July 21, 2016.
[2]. Reid, Scott A. et al. Illinois Tool Works Inc. U.S. Patent No. 9,775,250 filed May 26, 2016 and issued Sep. 26, 2017.
[3]. Agarwal, S., (2016) “Improved maintenance and reliability for large volume underfill processes”, Institute of Printed Circuits APEX EXPO, Las Vegas, NV. https://n2a.goexposoftware.com/events/ipc16
[4]. Agarwal, S., “Low Volume Dispensing with High Speed Dispensers,” Master’s Thesis, State University of New York at Binghamton, December 2012.
[5]. Giusti, Christopher L. Nordson Corporation. U.S. Patent No. 9,707,584 filed July 9, 2014 and issued July 18, 2017. |
[저작권자(c)SG미디어. 무단전재-재배포금지] |
|
|
|
|