PWB 표면마감재 신중하게 선택해야
사용환경의 변화에 따른 적합한 재질 고려가 우선
포터블 전자기기의 초창기 디자인 단계에서는 사용될 PWB 표면마감재을 신중하게 선택하고 결정하는 것이 중요하다. 이 결정에 영향을 주는 주요 요인은 다음과 같다: 접촉 디바이스의 타입, 재질 그리고 외형, 가용한 기술들과 가용 프로세스. 이들 모든 요인들이 고려사항에서 이야기되어야 만이 역동적이고 끊임없이 변화는 시장 내의 엔드-유저가 기대하는 신뢰성에 대한 완전한 충진 요구사항을 충족시킬 수 있다. 역사상 처음으로 결정했던 표면 마감재 선택이 오늘날 올바른 선택이 아닐 수도 있다. 그 당시 전제조건이 바뀌고 있기 때문이다.
지난 몇 년에 걸쳐 모바일 폰과 기타 포터블 컨수머 전자기기들이 큰 유행을 끌면서 서로 다른 기후의 지역에 대량으로 확산되었다. 동시에 모바일 폰은 많은 사람들의 실생활에서 특정 활동을 지원해줌으로써 이미 필수품이 되었다. 이러한 사용자 행동의 변화는 습기, 땀, 부식성 대기 그리고 기계적 낙하가 헨드헬드 단말기에 미치는 영향을 심하게 변화시키고 있다. 그 결과, 솔더 접합 신뢰성, 부식 안정성 및 내마모성 관련 요구사항은 단말기의 높은 신뢰성을 유지하기 위해서 크게 늘어나고 있다.
지난 10여 년 동안 Immersion Ni/Au는 PWB의 압도적인 전체 표면처리재이었으나, 얇고 다공성인 표면마감재 사용을 피하려는 패러다임 이동이 근래에 들어 나타나고 있다. 이러한 문제들을 만족스럽게 해결할 수 없기 때문이다. 오늘날의 휴대기기에서 OSP(Organic Solder Preservative)가 솔더 패드 상의 Immersion Ni/Au를 대체하고 있다. Key/spring contact-pad용 카본계 표면처리재가 적합한 콘셉트로 디자인되면, 가까운 미래에 Immersion Ni/Au 사용이 불필요하게 될 수 있다. 결과적으로, 덜 비싸고, 더 단순해진 공정을 지닌 더 높은 신뢰성을 제공할 것이다. 본고에서는 표면처리재 선택에 있어서 다양한 고려사항들과 연구를 통해 나타난 타당한 결과들을 논의할 것이다.
서문
ENIG(Electroless Nickel Immersion Gold)는 지난 10여 년 동안 PWB의 압도적인 표면처리 방법이었고, ENIG 공정은 전세계 거의 모든 PWB 제조업체에서 표준 공정으로 자리 잡았다. 우수한 솔더 젖음성을 제공하고, PWB의 장시간 저장이 가능하도록 산화방지 층을 제공한다는 역사적인 이유에서 시작되었다. 이러한 관점에서 본다면 ENIG는 제 기능을 우수하게 수행하지만, 신뢰성 관점에서 본 해당 표면처리재의 이용은 모바일 전자기기에서 가능한 많이 제한될 것이다.
최근에 금-취하(gold-embrittlement), 솔더 접합 사이 크랙, 침식과 접합 패드의 마모에 의해 기인되는 냉땜과 같은 특정 현상이 PWB 상의 표면마감처리재로써 선택된 ENIG와 직접적으로 연관 짓을 수 있다.
따라서 솔더링과 전기-기계적인 접촉 양쪽 모두를 대체하는 표면마감처리재는 포터블 컨수머 전자기기의 높은 신뢰성을 보증하기 위해서 평가 및 연구되기 시작했다. 본고에서는 경성 PWB용 표면 마감처리의 이슈들을 설명한다.
표면 마감처리재 옵션들
표면 마감처리재 선택에 있어서 가장 중요한 요인들은 다음과 같다:
▶ 신뢰성
▶ 유효성
▶ 비용
특정 경성 PWB용의 표면마감재를 선택하기 전에 해당 애플리케이션에 적합한 마감 특성을 보유하고 있는지를 고려하는 게 중요하다. 예를 들어, keypad 스위치 혹은 spring connector와 같은 영역에서 단순 납땜용인지 아니면 전기-기계적 접합용으로도 활용하고자 할지를 먼저 염두에 두어야 한다.
휴대전화에서 주로 사용되는 spring-loaded connector용으로써 납땜성과 전기-기계적 접합 패드 양쪽에 높은 신뢰성을 주는 단일 범용 표면 마감처리는 아직까지 존재하지 않는다.
PWB 상의 표면 마감처리재는 서로 다른 기본 요구사항을 가진 2개의 메인 그룹으로 구분될 수 있다:
솔더링용 표면 마감처리재
솔더링용 표면 마감처리재는 여러 요구사항들을 충족시켜야만 한다:
▶ 우월한 젖음성
▶ 납땜 접합 강도
▶ 파인피치 및 CSP 어셈블리를 위한 표면 평탄도
산업계에서 사용 가능한 여러 옵션들이 있는데, 그 중 일부는 다음과 같다:
▶ HASL (Hot Air Solder Leveling)
▶ Immersion Tin
▶ Ni/Au (ENIG)
▶ Immersion Silver
▶ OSP(Organic Surface Preservative)
모든 옵션들이 성능 측면에서 동일하지는 않다.
전기-기계적인 접합 패드용 표면 마감처리
접합 패드용 표면 마감처리재는 다른 요구사항들을 충족시켜야만 한다:
▶ 기계적 내구성(내마모성)
▶ 부식 안정성
▶ 접합 저항
그리고 또 다른 옵션들은 다음과 같다:
▶ Ni/Au (Electroplated)
▶ Ni/Au (ENIG)
▶ Immersion Silver
▶ Carbon
▶ 솔더 페이스트 (Sn/Sn contact)
옵션들의 요약
지난 20여 년 동안 다양한 포터블 전자기기에 실제로 사용되어 온 표면 마감처리재를 조사할 때, 왜 ENIG가 대중적이 되었고, 다른 마감처리 방식들이 여러 해 동안 거의 무시되었는지는 논리적으로 접근하지 않았다.
▶ 설명하려는 하나의 부문은 오늘날 보유하고 있는 불량 메커 니즘에 관한 지식이 최근까지 가용하지 않다는 점이다.
▶ 다른 부문은 분석 실험실 및 신뢰성 전문가들이 문제를 설 명한 후에도 불구하고 전자 산업계의 전통 변화에 대한 거 부감이다.
▶ 마지막 부문은 PWB 제조업체에서 표면 마감처리재의 물리 적인 가용성 부족을 이유로 다른 마감방식으로의 변경을 항상 연기시켰을 것이라는 점이다. ENIG 공정에 대한 투자 는 이미 이뤄졌고, 다른 마감재용 신규 장비를 설치하려면 더 많은 투자가 필요하다. 이 사실 또한 확실한 지연의 이유 이다.
표면 마감재의 변경에 영향을 미치는 문제의 개요는 이하의 내용에서 설명한다.
휴대전화 내 PWB 표면 마감재의 역사적인 진화
HASL + Carbon
1980년대 후반의 휴대전화 1세대 제품군에서 PWB 상의 패드용 일반적인 표면 마감처리재는 HASL이었다. HASL은 Key 패드 및 LCD 패드용 마감재로써 많은 경우 카본과 함께 사용되었다. 표면실장부품 기술은 초기 단계에 있었고, 걸-윙(gull-wing) 타입 부품들은 상대적으로 넓은 피치(1.27mm)의 리드를 가지고 있었다.
1990년대 초반 더 많은 I/O가 필요로 하는 새로운 패키지와 QFP의 요구가 나타났다. 피치는 0.6mm로 줄어들었고, 많은 솔더 브릿지가 발생했다. 균일하지 않은 HASL의 두께 때문이었다. 낮은 제조수율로 인해 HASL는 대체되어야만 했다.
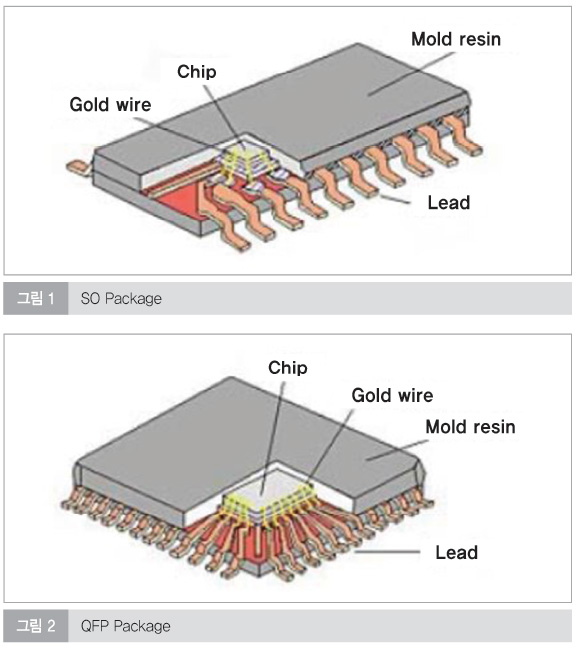
ENIG(Electroless Nickel Immersion Gold)
앞선 문제를 해결하는 유일한 방법은 평평하고 평탄성 있는 표면을 지닌 납땜 가능한 다른 표면 마감재를 발견하는 것이었다. 순동(bare copper)은 납땜성(젖음성)에 대한 산화 영향 때문에 적용할 수 없었다. 그 당시에 기술이 존재하고 있었음에도 불구하고 OSP는 논의되지 않았다.
HASL 후계자로 ENIG가 선택되었다. 그 당시의 인식은 솔더링과 key-pad 양쪽 부문에서 보편적으로 적용 가능한 표면 마감재를 발견하는 것이었다. 그래서 카본은, 기술적인 문제가 존재하지 않고, 신뢰성 측면에서도 적용 가능했음에도 불구하고, 필수재로 간주되지 않았다.
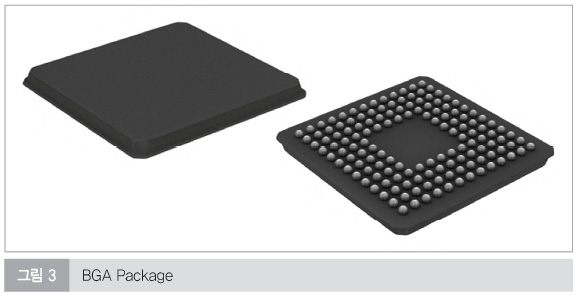
일정 기간 동안 ENIG 프로세스는 일반적으로 잘 가동되었으나 최소 공간에 더 많은 기능성이 필요해졌고, 그래서 QFP는 구식이 되기 시작했고 BGA와 CSP로 대체되었다. BGA 패키지(그림 3 참조)는 또한 몇 가지 새로운 도전과제를 제시하였다. 어전 전자산업계에서는 결코 없었던 더 작은 솔더 패드는 거대한 대량생산 증가와 함께 동시대에 나왔다. 극도의 대량생산 분위기에서 PWB를 제조하는 것은 프로세스의 특정 약점이 훨씬 더 명확하고 심각해진다는 것을 의미한다.
블랙패드
다른 브랜드의 Ni/Au 프로세스를 사용함에도 불구하고, 블랙패드라고 불리는 문제들은 여러 PWB 공급업체에서 무작위적으로 발생한다. 골드의 missing 영향은 무작위적인 단일 패드 상에서 약해지거나 혹은 비-젖음성을 보였고, 결과적으로 잘못된 상호접촉을 초래했다. 이들 대부분은 휴대전화 어셈블리 라인에서 발견되고 불량으로 처리되지만, 최악의 시나리오는 하나의 제품이 100% 전기테스트를 통과한 후 최종 시장에서 불량이 되는 경우였다. PWB가 약한 솔더접합 연결임에도 불구하고 많이 구부러지면 무작위적인 에러가 발생하고 휴대전화는 오작동한다.
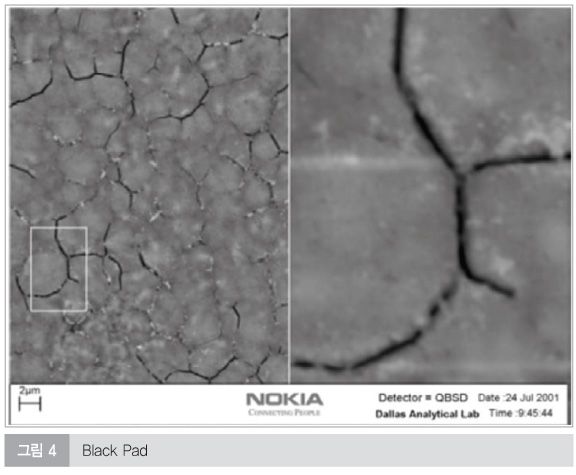
왜 블랙패드가 나타나는지에 대한 많은 이론이 존재하지만 계기가 무엇인지에 관한 실질적인 동의는 없다. 그러나 bath 제조업체들은 몇 년동안 이 영역에서 약간의 진보를 이뤘다. ENIG 프로세스는 일부 PWB 설계와 관련 있을 수도 있는 이 불량에서 여전히 자유롭지 못하다.
솔더 볼 계면 균열
블랙패드 문제와 관련하여 ‘계면열화’라고 불리는 새로운 불량 유형이 나타났다. 결함이 있는 BGA 혹은 CSP 부품의 미세 단면에서는 솔더 젖음이 좋았음에도 불구하고 Cu 패드와 솔더 볼 간 계면에서 크랙이 나타났다(그림 5 참조).
그 이유가 무엇일까요? 많은 조사 이후, 3가지가 결합된 것으로 밝혀졌다:
▶ 니켈과 Sn 사이의 부서지기 쉬운 IMC(Inter Metallic Compound)를 간과된 문제.
▶ 사용자가 이전 보다 더 많이 땅에 제품을 떨어뜨리기 시작 한다는 사실.
▶ 기존 패키지 타입과 비교해 BGA 패키지 타입의 솔더 조인 트 응력 경감.
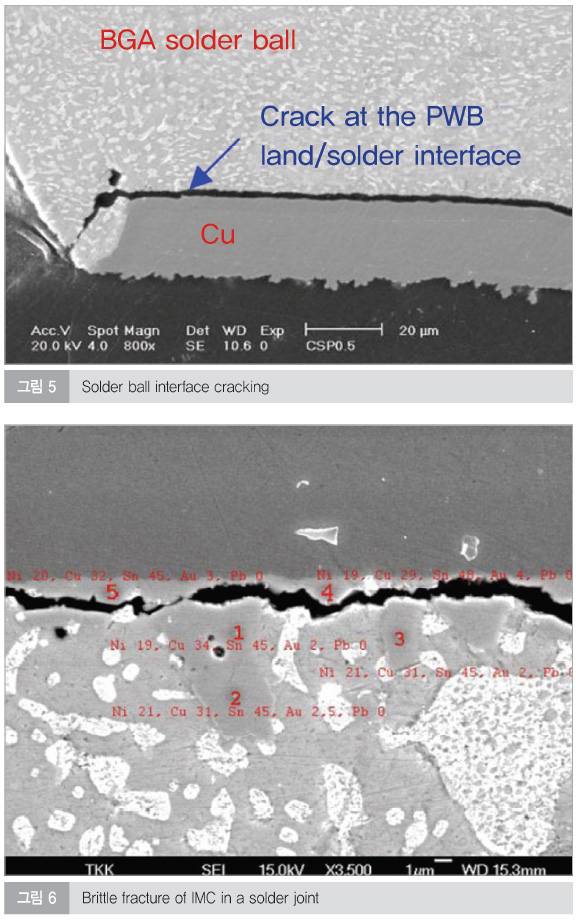
IMC 문제
솔더링 프로세스 동안 깨지기 쉬운 니켈-주석 IMC가 형성되었다. 제품이 기계적인 충격에 노출되면, 특히 BGA 타입 부품의 솔더 조인트 내에서 IMC 파손을 유발할 수 있다(그림 6 참조). 이 현상은 ‘금-취화(gold-embrittlement)’로 잘 알려져 있고, ENIG가 도입된 이래로 분명하게 존재해 왔다.
패키지 응력
QFP는 일정 수준의 기계적인 응력을 견디기 위해 솔더 조인트에서 적절하게 응력 경감 역할을 하는 걸-윙(gull-wing) 타입 리드를 가지고 있다. 볼이 있는 딱딱한 BGA 패키지(그림 7 참조)는 휴대전화가 떨어지는 동안 PCB가 구부러질 때 응력을 많이 경감시켜주지 못한다. 따라서 IMC 내에서 균열이 시작하는 허용치를 쉽게 초과한다.
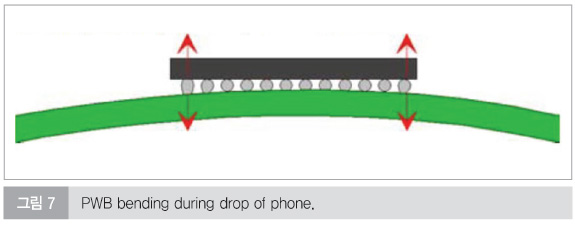
수천 개의 실제 제품과 가속계, 스트레인 게이지, 이벤트 감지기 그리고 고속 카메라가 장착된 비디오 레코더를 부착하여 특별히 설계된 테스트 보드의 제어된 낙하 테스트를 수행함으로써 응력과 실패 메커니즘을 훨씬 더 잘 이해할 수 있다. 낙하 테스트 도중 PWB의 구부러짐이 1~2미터 낙하에서 나타나는 pure G-forces보다 더 큰 문제였음을 알 수 있었다. 수치화된 모델이 생성되어 왔고, 일부 낙하 시뮬레이션은 디자인 프로세스 전에 먼저 수행될 수 있다.
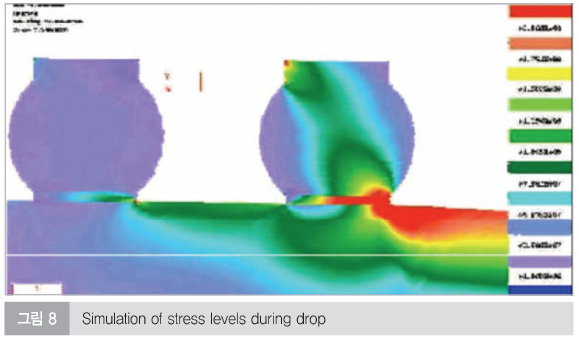
사용자 프로파일 변화
1980년대 후반 제 1세대 휴대전화가 시장에서 가용해지기 시작할 때 그들은 매우 비쌌다. 그래서 사용자들은 자신의 휴대전화를 매우 조심스럽게 다뤘다. 1990년대 후반 휴대전화 시장 볼륨이 폭발적으로 커졌고 하드웨어의 단가가 하락하였다. 동시간대에 서비스 제공업체들은 최종 사용자들에게 휴대전화를 때때로 기부하기도 했다. 새로운 미디어에 사람들을 익숙하게 하고, 통화시간에서 비즈니즈를 창출하도록 실제 비용의 일부만을 받는 방식을 적용했다. 대부분의 사람들에게 좋았으나 부정적인 영향을 미치기도 했다. 휴대전화가 실제로는 존대를 받아야만 하는 매우 정교하고 복잡한 전자기기라는 점을 사용자들이 잊게 되었기 때문이다. 낮은 생산단가 때문에, 휴대전화는 갑자기 보호가 필요 없는 제품으로 취급되었고, 이전보다 매우 높아진 응력에 노출되는 결과를 초래했다. 1~1.5미터 높이에서의 휴대전화 낙하가 최근에는 쉽지 않아서 신뢰성 문제들을 해결하기 위해 즉각적인 조치가 필요했다. BGA를 언더필하는 것은 납땜 균열과 관련된 문제들을 지연시키나 문제의 근본적인 원인을 제거하지는 못한다. 이 문제를 해결하는 유일한 방법은 니켈/금 도금 상에서의 솔더링을 피하는 것뿐이다.
선택적 ENIG + OSP
2000년대 산업계에서는 IMC 문제를 해결하기 위해 선택적 ENIG + OSP 공정을 도입하였다. 이는 key-pad 그리고 다른 전기기계적인 접촉 영역에만 금 도금이 적용되는 것을 의미한다. 그림 9에서 보여주는 것과 같은 선택적 프로세스는 이미 까다로운 ENIG 프로세스에 복잡성, 문제점 그리고 비용이 추가된다는 것을 나타냈다.
광범위한 테스트 이후 앞서 언급한 여러 솔더링용 표면마감방식 중에서 한 후보인 OSP가 솔더 성능, 비용 및 솔더 접합부 강도에 대한 요구사항을 부응하기 선택되었다. PWB 제조업체에서 선택적 ENIG + OSP 프로세스의 가용성이 초기에는 존재하지 않았지만, 글로벌 거대 PWB 고객사들은 놀라울 정도로 짧은 시간 내에 공급업체들을 깨울 수 있었다: 요구가 시작된 지 1년 후, 모든 PWB 관계 공급업체들이 적절한 대량생산과 품질의 프로세스를 관리할 수 있었다. ENIG 상의 솔더링에서 OSP으로의 변화는 BGA 부품의 솔더 접합부 균열에 의해 유발되는 불량률을 크게 감소시켰다.
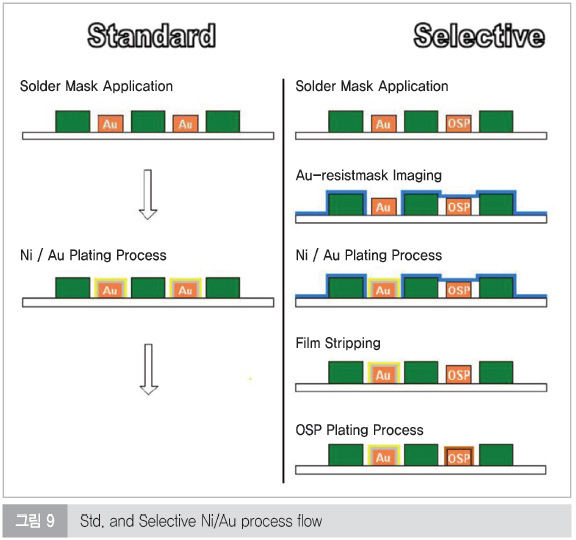
ENIG 특성 개선
지금까지 ENIG가 전기기계적 접촉부에만 사용되기 때문에, 이 표면이 충분한 접촉부 신뢰성을 보장하는 최상의 상태인지를 평가하는 것이 중요하다. 오늘날 상태는 다음과 같다:
1. 선택적 Ni/Au 프로세스가 복잡하고 비용이 높다.
2. Ni/Au 품질은 대부분의 사람들이 기대한 것만큼 우수하지 않다.
- 매우 얇은(40~60 나노미터) Au 표면마감은 Ni-부식에 이 르게 할 수 있는 마모 문제가 나타난다.
- 때때로 Au 표면의 다공성 특성은 마모가 없음에도 불구하 고 Ni-부식 문제가 나타난다.
특히, 전통적인 ENIG의 부식 안정성은 제품이 높은 습도, 염분, 대기 오염 혹은 땀이 존재하는 환경 하에서 작동할 때 부적합한 것으로 최근에 평가되었다. 이 결과, Ni 프로세스는 Ni 표면이 약간 더 우월해지기 시작했고, 상부의 침식 Au는 다공성이 덜해지기 시작했다는 효과가 있다는 것으로 받아들여지고 있다(주요 P 함유).
최종 결과는 만약 얇은 Au 표면이 스크래치 혹은 마모에 의해 피해를 입지 않는다면, 수정된 높은 P ENIG의 부식 안정성이 더 높은 수준으로 개선된다는 것이다. 개선에도 불구하고 침식 골드 프로세스는 전기도금 골드의 경우와 같이 전체 기공 없는 표면을 제공할 수 없었다.
이는 점점 더 분명해지기 시작했다. 미래의 얇은 ENIG가 노동 혹은 스포츠 활동 중에 사용되는 게임 디바이스 및 휴대전화와 같은 극한의 제품군에서 요구되는 더 높아진 내마모성에 부응할 수 없을 것이다. 따라서 ENIG를 보다 안정적으로 것으로 대체하는 게 중요하다.
접합부 마감재의 재검토
다음의 후보군들이 연구되었다:
- Ni/Au (전기도금)
- Ni/Au (어셈블리용 P3의 전기도금)
- Carbon (스크린프린트)
경성 PWB 상의 금 전기도금
니켈/금을 이용한 PWB의 전기도금(하드-골드, 0.8미크론보다 두꺼운)은 낮은 접합 저항, 우수한 내구성 그리고 부식 특성 때문에 기술적으로 가장 매력적인 접합 표면재이지만 이 공정의 매우 높은 비용 때문에 대부분 실격처리 되었다. 사용에 있어서 실제적인 다른 저해요소는 부스 바(bus bar)를 이용한 도금 프로세스 동안에 모든 패드의 단락(short-circuiting)이 필요하다는 점이다. 도금 이후, 부스 바는 긴 ‘dead traces(EMC와 ESD 특성에 악영향을 주는)’가 나타나게 오픈되어야만 한다. 관련된 모든 패드가 PWB의 주위에만 배치되는 드문 경우도 있지만, 부스바는 그 후 라우터 프로세스 도중에 효율적이고 쉽게 제거될 수 있다.
P3의 금 전기도금
픽앤플레이스 패드(P3)는 Cu 혹은 니켈-은 재질로 된 금속 호일의 작은 부분이다. P3는 Ni 및 Au의 고체 레이어로 전기도금되었다. P3 부품들은 원하는 모양, 크기 및 두께로 쉽게 디자인될 수 있고, 편리한 어셈블리가 가능하도록 레지스터 혹은 커패시터처럼 취급될 수 있다. P3을 사용하면, PWB 상 원하는 어디든지 고품질의 금 접합부 납땜이 되도록 배치 및 리플로우가 가능하다. 그 다음 PWB는 OSP 혹은 Immersion Silver 등과 같이 솔더 가능한 하나만의 표면마감재가 필요하다.
비용 측면에서 P3의 수가 10 조각 미만으로 제한된 경우, OSP 상의 P3을 활용한 솔루션은 선택적 ENIG + OSP에 비해 매력적이다. Key-pad 용도만은 P3가 실현 가능한 솔루션이 아니다. 따라서 다른 표면 마감재가 여전히 필요하다. Key-pad 용의 가장 확실한 선택으로 카본이 고려되었다.
경성 PWB 상의 카본
카본은 PWB 산업계에서 30년 이상 폭 넓게 사용되고 있으나 최근 10년간은 잊혀져 있었다. 1970년대 및 1980년대의 경성 보드가 고부가가치로 이용되면서부터, 카본은 1990년대에는 ENIG로 인해 거의 경쟁에서 밀려났다. 리모컨, 계산기, 워키토키 및 다른 종류의 전기장난감의 키보드와 같은 애플리케이션에서만 경성 보드 상에서 이 표면마감재가 현재까지 꾸준히 사용되어 왔다. 이 외에도, 폴리머 은 및 카본을 활용한 폴리에스터 플렉스 기반의 멤브레인 터치 스위치 키보드가 여전히 넓게 사용되고 있다.
하이엔드 및 휴대전화 시장에서만 카본을 대부분 경시했었다. 경성 PWB 상의 옵션사항으로만 인지했었다. 카본 표면이 제공하는 여러 이점들을 고려했을 때, 상당히 이례적인 모습이다:
- 단순하고 저렴한 프로세스(그림 10 참조).
- O2, SO2, NOx, Cl- 그리고 기타 가스에 대한 높은 내식성.
- 대부분의 솔벤트, 커피, 맥주, 콜라 등과 같은 액체로 인한 영향이 거의 없다.
- 우수한 내마모성(두께 및 ‘자가 윤활’ 표면)
- ENIG 프로세스에 비해 보다 친환경적인 프로세스.
몇 가지 단점이 존재하지만 인지하고 있는 것이 중요하다:
- 순금속 표면 대비 높은 접촉저항. 일반적으로 4~10Ω.
- 카본층의 플레이스먼트 공차는 일반적으로 ±150㎛이다.
- 카본 페이스트는 본질적으로 흡습성을 가지고 있기 때문에 적절한 방법을 통해 최상의 재질이 되도록 경화시키는 방법 의 사용이 중요하다. 경화 프로파일에 부적절한 재료 혹은 가열이 사용된다면, 저항성은 습기에 민감해질 것이다.
제조 프로세스
카본은 스크린-프린터를 활용한 추가 프로세스로 적용할 수 있다(그림 10 참조). ENIG 프로세스에 공정 단계 및 화학적 프로세스가 훨씬 적게 포함되어 비교적 단순한 프로세스이다.
카본의 적외선 경화 방식은 이전에 연구되었고, 저항 안정성의 현저한 향상을 보여주었고, 시트 저항의 감소를 가져왔다.
적외선 경화가 최적화된 프로파일과 자동 인라인 설비를 통해 수행된다면, 전체 3개의 공정단계의 총 프로세스 시간은 15분 미만으로 낮출 수 있으므로 대량 생산에 매우 적합하다.
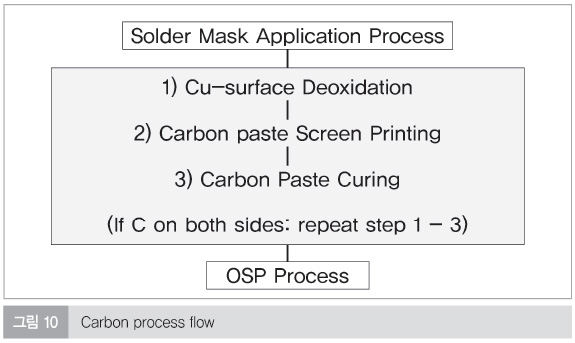
접촉 저항
접촉 저항은 PWB에서 전기 기계적인 접촉과 동박 간의 저항으로 정의된다.
이 저항은 다음의 합계이다:
1. 카본 계면 저항에 대한 스프링-접촉
2. 카본 두께 벌크 저항
3. 동박 계면 저항에 대한 카본
제어되고 안정적인 접촉저항 레벨은 성공적인 카본 테크놀로지를 위한 간단한 요구사항이다. 적당한 재료와 프로세스를 사용했을 때 5Ω의 접촉저항 레벨은 쉽게 이룰 수 있다. >10Ω의 접촉저항은 수용되지 않아야만 한다. 제조공정 상에서 문제들이 대두되기 때문이다. 일반적으로 높은 접촉저항은 카본 스크린-프린팅 프로세스 이전에 동박 표면의 부적절한 탈산화반응을 나타낼 것이다.
카본 제조 프로세스가 적합한 방법으로 이행되어 오고 있는지를 판단하는 매우 간단한 방법은 온습도(Damp heat) 테스트에 샘플들을 노출시키는 것이다. 2일 후 85℃, 85%R.H의 접촉저항이 10Ω을 초과하는 중요하고 영구적인 접촉저항을 제공한다면, 그 후 프로세스는 제어 불능상태가 될 것이다.
카본 시트 저항률
카본에 관한 그림을 완성하기 위해서는 폴리머 카본 레지스터에 기반을 둔 약간의 신규 임베디드 레지스터 기술이 필요하다. 원칙적으로 이들 레지스터 재료는 표면 마감재용 카본과 유사하다. 차이점은 시트 저항률이 100ohm/square, 1Kohm/sq, 10Kohm/sq와 같이 각 10년에 맞도록 조정된다는 것이다.
‘접촉-카본’용 시트 저항률은 가능한 낮아야만 한다: 전형적으로 15ohm/square이고 최대 25ohm/sq이다.
이상적인 조합
잠재적으로 다음의 조합은 비용/신뢰성 측면에서 미래에 가장 매력적이고 유연한 솔루션이 될 수 있다.
- 솔더 패드용 OSP
- 솔더 패드용 잠재적으로 Imm. Ag
- 접촉 저항에서 중요한 전기 기계적 접촉용 납땜 커넥터 혹은 P3
- 키패드 및 다른 낮은 저항에서 중요한 전기 기계적 접촉 패 드용 카본
이 조합에서의 과제 중 하나는 오늘날 존재하는 휴대용 단말기 부문에서 카본 테크놀로지를 검증하는 테스트이다. 하부에서는 테스트 실행 후 도출된 일부 결과들을 설명할 것이다.
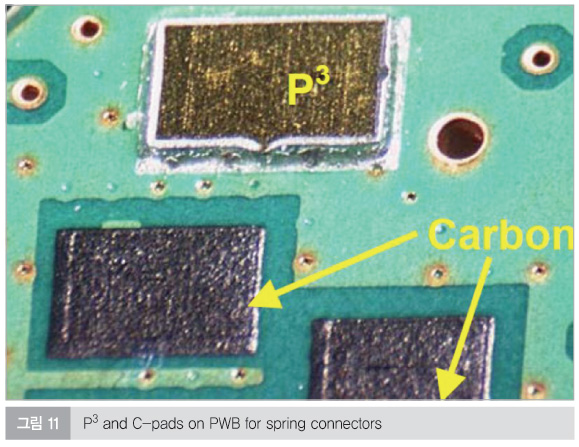
카본의 신뢰성 테스트
지난 10여 년 동안 전자산업계에서 카본이 철저하게 배제되어 왔기 때문에, 대부분의 PWB 제조업체들이 과거에 보유하고 있는 프로세스 기술들을 재검토해야만 한다는 점이 사실이다. 스크린프린킹 설비들이 컴퓨터 제어 파라미터 설정과 카메라 정렬 시스템이 필요로 하는 반복정밀도 및 정확도에 관한 오늘날의 요구사항에 매번 부합한 것은 아니다.
시장조사를 통해 많은 PWB 제공업체에게 접촉저항의 Kelvin 분석을 위해 특별히 설계된 약간의 테스트 보드 제조가 가능한지 문의했다:
- 카본 프로세싱에서 최상의 클래스인가?
- 저습도 요구사항을 충족한 카본 페이스트가 접촉/시트 저항 에서 안정적인가?
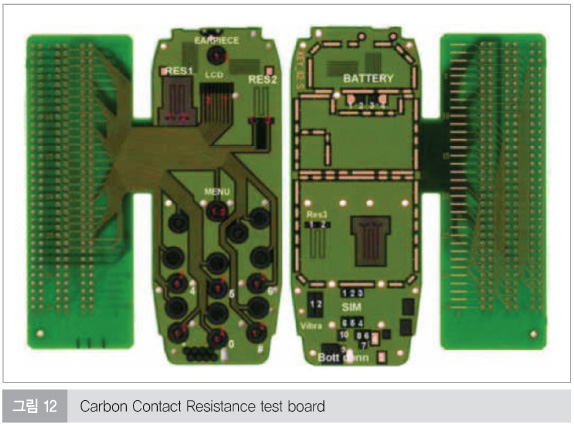
테스트 계획
테스트 보드 및 카본으로 수정된 테스트 전화기가 많은 환경 및 실제 사용자 환경 테스트에 노출시켰다. 이 테스트에서 가장 중요한 점을 논의했다. 대부분의 경우 ENIG 테스트 보드는 2개의 표면 마감재의 신뢰성과 비교하기 위해 참조문헌들을 사용하였다.
베어 보드 테스트 :
- 염수 분무 시험(2주간)
- SO2 가스 부식 테스트(48시간)
조합된 휴대전화 레벨의 마모 및 부식 테스트 :
- 내습성 사이클 테스트 25℃ <-> 55℃, 98% R.H. (EC 60068-2-30 Variant 1, 6일에서 6주로 확대)
- 2,500,000번 키패드 스트로크의 수명 + 내습성(표 1 참조). 오류를 유발하기 위해 특별히 설계된 ‘비표준’ 테스트이다. 다양한 테스트 샘플의 신뢰성 레벨 차이를 도출할 수 있 었다. 몇 년 동안의 실제 사용을 시연했다. 저항 측정이 각 각의 5,000번 키스트로크를 자동으로 측정되는 이 테스트 를 5주에 걸쳐 수행하였다.
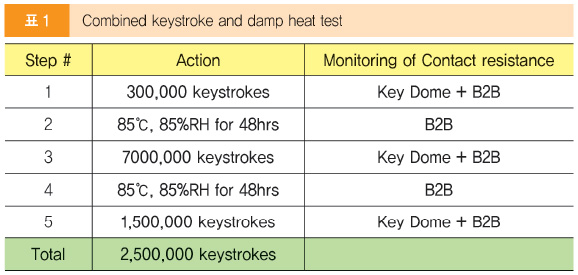
테스트 결과
베어 보드 염수 분무 테스트
염수 분무 테스트 2주 후, 테스트 보드를 시각 검사하였다. High-P ENIG 샘플들은 너무 많이 부식되어서(그림 13 참조) 예정된 핵심 기능 테스트를 취소했다.
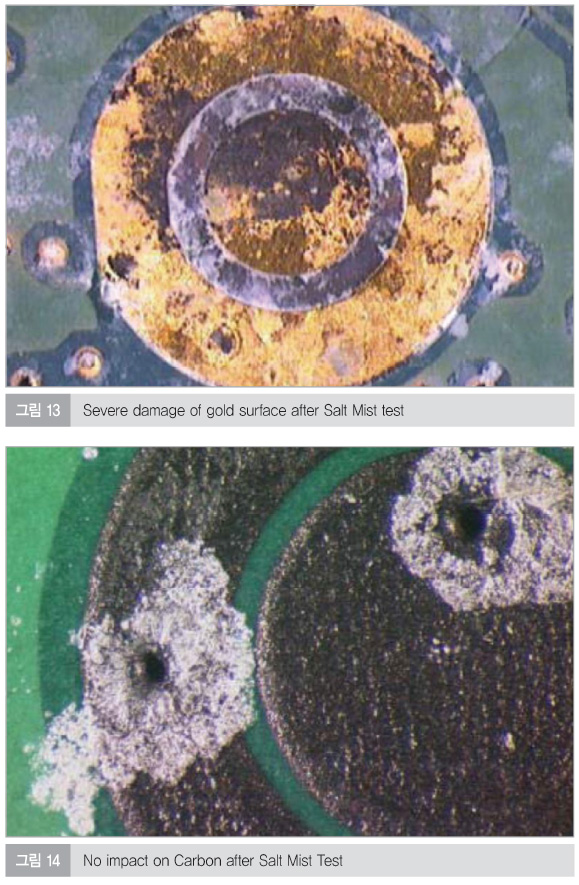
카본 샘플들은 전부 부식되지 않았으나 표면상의 자연적인 염분 오염이 있었다. 이소프로필 알콜로 염분을 제거한 이후, 카본 표면은 다시 새 것처럼 보였다. 접촉저항이 측정되었고, 여전히 안전한 10ohm 미만이었다. Dome 시트의 어셈블리도 일반적인 주요 기능을 보여주었다.
베어 보드 SO2 가스 부식 가스 테스트
ENIG와 카본 샘플 모두 테스트를 통과했다. ENIG 샘플들이 수정된 High-P ENIG로 도금된 점이 언급되어야만 한다. 표준 ENIG 표면은 해당 테스트에 노출되었을 경우, 이전 테스트에서 높은 부식률을 보여주었다. High-P ENIG이 시행되는 이유이다.
내습성 사이클 테스트
카본에 대항하는 스프링 접촉의 접촉저항은 노출 동안 6주에 걸쳐 지속적으로 관찰되었다. 스프링 접촉의 표면 마감은 금 전기도금이었다.
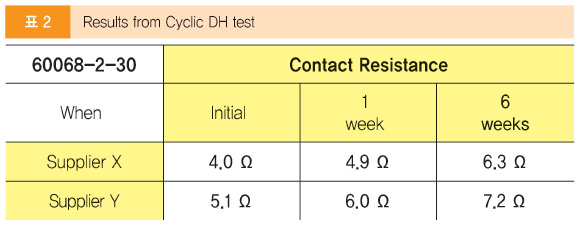
테스트 막바지에 접촉저항 레벨은 안전하게 10ohm 미만이었고, 드리프트 역시 전적으로 수용할만한 수준이었다.
마모와 부식 테스트 결합
2개의 스프링-로드 보드-투-보드(B2B) 커넥터용 전체 키보드(21개 키)와 접촉패드(24개 조각) 모두 포함된 수많은 휴대전화 UI-보드의 휴대전화 레벨에서 테스트가 실행되었다. 스프링 커넥터들은 금 전기도금 표면마감 처리되었다. 테스트는 다른 카본 제조 프로세스 설정과 다수의 다른 카본 페이스트로 진행되었다.
테스트에서는 일부 PWB 제공업체가 노키아의 요구사항을 통과하기 위한 더 많은 경험과 더 우수한 카본 프로세스 설정이 필요하다는 점을 밝혀냈다. 최상의 제공업체들은 우리의 요구사항을 충족시켰고, 이 엄격한 테스트를 통과할 수 있는 카본 활용 PWB를 제작하는데 전혀 문제가 없었다.
그림 15에서는 1쌍의 보드-투-보드 커넥터 스프링에 관한 유효한 접촉저항을 보여주고 있다. 카본 제조 프로세스가 불량일 경우(라벨 : Supplier E), 접촉저항은 내습 도중에 크게 증가했고, 정확한 방법으로 제조했을 때는 매우 안정적인 모습을 보였다(라벨 : Supplier A).
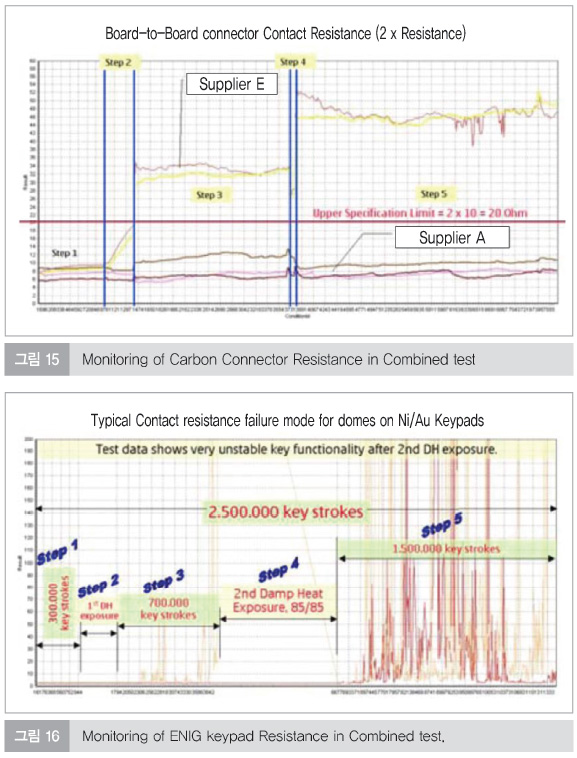
그림 16(High-P ENIG)와 그림 18(카본)은 다음과 같은 체인의 전체 저항을 관찰한 모습이다;
스프링 커넥터 1 - 카본 접촉패드 - Cu 트레이스 - 카본 키 외부 링 - metal dome - 카본 키 센터 패드 - Cu 트레이스 - 카본 접촉 패드 - 스프링 커넥터 2. 테스트에서 이 체인에 대한 Pass/Fail 기준을 200 ohm으로 설정했다.
ENIG의 경우(그림 16 참조), 저항은 DH 노출 이후 약 200,000번의 키 스트로크가 행해진 step #3에서 불규칙적으로 약간 증가하기 시작했다. 400,000번의 키 스트로크 이후 처음으로 핵심 기능이 불량을 나타냈다.
step #5(2차 DH 노출 직후)에서는 핵심 기능은 매우 불안정해지기 시작했다. 이에 대한 근본적인 원인은 테스트 샘플들의 시각검사 이후에 분명해졌다. 그림 17에서는 metal dome이 금 도금 표면에서 벗겨지고 있으며, 노출된 Ni의 심각한 부식이 시작되었음을 보여주고 있다.
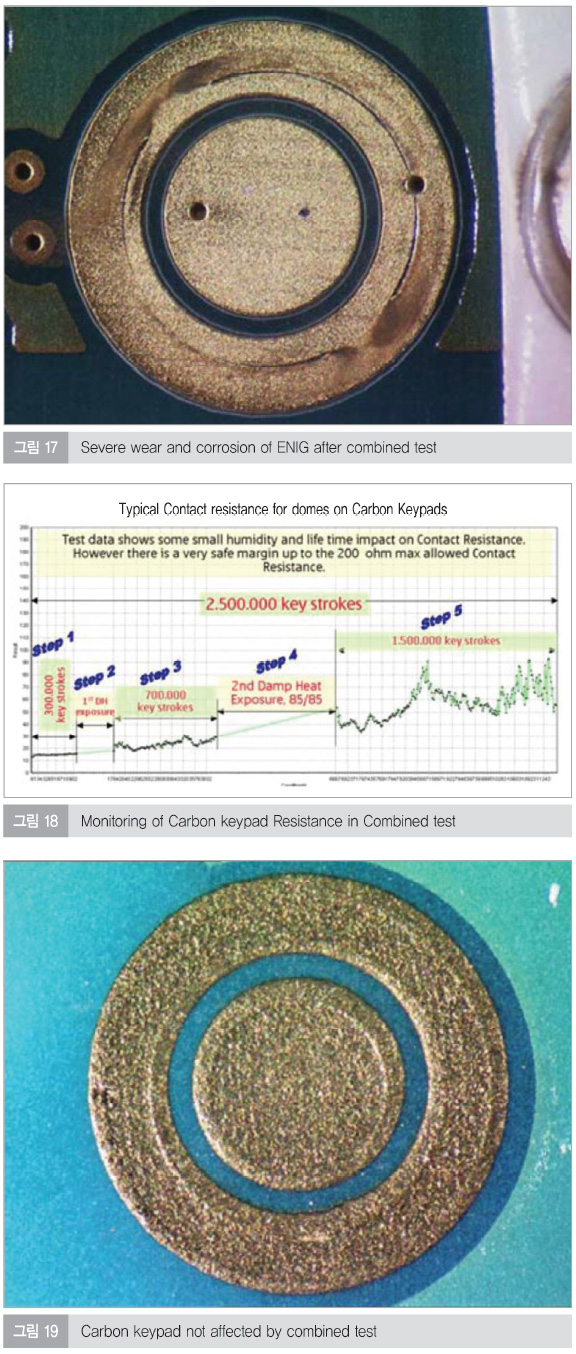
그림 18에서 보는 바와 같이 카본의 경우, 저항은 13ohm에서 약 80ohm으로 증가하였다(그림 18 참조). 이 변화는 전체적으로 수용 가능하고 최대 200ohm 요구사항의 미만이다. 전체 2,500,000번의 키 스트로크 중에 어떠한 단일 키-불량도 검출되지 않았다.
테스트 샘플들의 시각검사에서 놀랄만한 경험을 하였다: 카본 표면은 전체적으로 손상되지 않았고, 부식의 흔적도 없었다(그림 19 참조). 특별한 조명 설정만으로도, 카본과 접촉된 dome의 검출이 가능했다.
수명의 극한 테스트
좋은 결과에 힘입어, 마모와 부식이 조합된 테스트는 샘플들을 36번 반복하였고, 그래서 전체 충격은 5,000,000번의 키 스트로크와 4번의 DH 사이클로 하였다. 저항치는 여전히 100ohm 미만이었고, 카본 표면은 여전히 전체적으로 손상이 없었으며, 부식 흔적이 없었다.
부식 및 수명의 극한 테스트
다음의 조합 테스트가 카본 + OSP로 앞서 언급된 UI-보드의 18개 샘플들에서 수행되었다.
1. 1주간 염분 분사에 PWB 노출
2. 이소프로필 알콜로 염분 오염물 제거
3. 레드-프리 리플로우 솔더링 프로파일 노출
4. 돔-시트 및 휴대전화 매커닉의 어셈블리
5. 2,500,000번의 키 스트로크의 마모 및 부식 결합 테스트에 노출
모든 샘플들은 어셈블리 이후에 완벽하게 동작하였고, 불량 없이 step #1, 2# 그리고 #3(1,000,000번의 키 스트로크와 1번의 DH 사이클)을 통과하였다. Step #4 이후, 18개의 샘플 중 3개는 2번째 DH 노출 후에 약간의 돌발적인 키 불량이 즉각 나타났다. Step #5 이후, 불량 샘플들은 다시 잘 작동했다.
테스트의 말미에서 결과는 18샘플 중 17개는 정상적으로 키가 작동했다.
결론
특히, 모바일 전자기기 장비의 경우, PWB 상의 적당한 표면마감재의 선택은 더 많은 주의를 기울여야만 한다. 솔더 조인트와 전기기계적인 접촉 포인트 양쪽 모두에서 높은 신뢰성을 줄 수 있는 하나의 범용 표면마감재가 존재하지 않기 때문이다.
솔더링용 마감재
ENIG 상의 솔더링은 일반적으로 권장하지 않으며, BGA 부품 타입에서는 금지되어야만 한다. PWB 솔더 패드의 ENIG에서 OSP로의 대체는 솔더 조인트 인터페이스 크랙에 의해 기인하는 불량의 현저한 감소가 증명된 수백만개의 휴대전화 제조 및 현상 피드백으로부터 입증되었다.
OSP는 Sn/Pb 솔더를 사용할 때 원래 도입되었으나 무연솔더에서도 우수한 솔더 조인트의 완전한 충진 요구사항을 충족할 수 있었다. Immersion Ag는 여전히 향후 OSP를 보완하는 대체재질로 간주되고 있다.
접촉 패드용 마감재
전기도금 gold(0.8㎛보다 두꺼운)는 신뢰할만한 선택이지만 경성 PWB 산업계에서 설계 및 프로세스에 항상 호환 및 가용할 수 없다. 불행하게도 비싼 프로세스이고 낮은 생산단가의 대량 제품군의 범주에서는 비껴나 있다.
연성 PWB 산업계에서 전기도금 gold는 어느 정도 표준 프로세스이지만 이들 FPCB는 일반적으로 비싸고, 대부분 하이엔드 제품군에 대개 들어간다.
Gold로 전기도금된 픽앤플레이스 패드는 더 싸지고, 매우 낮고 신뢰할만한 접촉저항이 필요한 약간의 접촉 포인트가 존재한 경우에 PWB 상 gold 도금의 대체 재질로 매력적이다. 이 경우의 PWB는 단지 OSP만 필요하다.
카본은 최대 10ohm 접촉 저항이 수용될 수 있는 키패드와 대부분의 스프링 구조 접촉 패드 상의 ENIG에 월등한 신뢰성을 제공한다. 카본은 매우 높은 내부식 성과 우수한 내마모 성을 지닌 오늘날 가장 저렴하게 가용할 수 있는 접촉 표면마감재이다.
ESD와 cosmetic 영역용 마감재
ENIG가 신뢰성에 너무 많은 영향을 미치지 않는 유일한 측면은 ESD와 cosmetic 영역이다. ENIG는 새롭고 주의를 기울여 처리했을 때 우수해 보인다. 고급스러운 인상을 주지만 혹독한 환경에서 사용한 이후 설비를 분해해 본다면, 이 꿈의 그림은 빠르게 사라진다. 이러한 종류의 환경은 모바일 단말기의 매일 사용에 대해서 오늘날 꽤 일반적이다.
요약
포터블 전자기기의 초창기 디자인 단계에서는 사용될 PWB 표면마감재을 신중하게 선택하고 결정하는 것이 중요하다. 이 결정에 영향을 주는 주요 요인은 다음과 같다: 접촉 디바이스의 타입, 재질 그리고 외형, 가용한 기술들과 가용 프로세스. 이들 모든 요인들이 고려사항에서 이야기되어야 만이 역동적이고 끊임없이 변화는 시장 내의 엔드-유저가 기대하는 신뢰성에 대한 완전한 충진 요구사항을 충족시킬 수 있다. 역사상 처음으로 결정했던 표면 마감재 선택이 오늘날 올바른 선택이 아닐 수도 있다. 그 당시 전제조건이 바뀔 수도 있다:
▶ 하드웨어 관련:
- 새로운 패키지 타입.
- 새로운 솔더 합금.
- 새로운 전기기계적 커넥터 접합 재질.
- 새로운 기계적인 디자인
-지지 역학의 견고성.
▶ 엔드유저 프로파일 관련:
- 온습도 대기상태, 비, 액체류에 노출.
- 진동, 낙하, 수많은 키스트로크에 노출.
- 하루에 사용자가 직접 사용하는 시간: 5분, 1시간, 8시간, 24 시간.
▶ 기술 발전 및 전문 지식 수준 :
- 새로운 표면 마감재의 존재.
- 옛 표면 마감재의 재질 특성의 개선.
- 제조 프로세스 및 장비의 개선.
- 불량모드 메커니즘에 관한 지식 증가.
단독 혹은 혼합될 수 있는 이러한 모든 조건들은 차세대 새로운 제품이 평소처럼 동일한 PWB 표면 마감재를 가지고 있는지를 재검토할 필요가 있음을 분명하게 하고 있다. 끊임없이 변화하는 시장에서 전통적인 설계 방법을 의존할 수 없다.