카메라 기반 센터링 시스템 알아보기
조명, 카메라, SW 요소들도 중요
정확한 부품 실장은 모든 픽앤플레이스 머신의 기본 요구 사항이다. 정확한 실장을 향한 첫 번째 단계는 정확한 센터링 또는 실장 헤드에서의 부품 위치 측정이다. IC, 커넥터 및 이형 부품에 가장 널리 사용되는 센터링 방법 중 하나는 해당 포인트를 기준으로 부품 위치를 측정하는 카메라 기반 시스템이다. 카메라 기반 센터링 시스템에는 조명, 카메라 및 소프트웨어라는 세 가지 주요 요소가 포함된다. 이들 각각의 요소는 부품의 정확한 측정을 획득해야 하고, 궁극적으로 PCB 상에 정확한 부품 실장에 중요하다. 오래된 격언대로, ‘시스템은 가장 약한 하나의 연결고리에 달려 있다’는 말이 적합하다.
정확한 부품 실장은 모든 픽앤플레이스 머신의 기본 요구 사항이다. 정확한 실장을 향한 첫 번째 단계는 정확한 센터링 또는 실장 헤드에서의 부품 위치 측정이다. IC, 커넥터 및 이형 부품에 가장 널리 사용되는 센터링 방법 중 하나는 해당 포인트를 기준으로 부품 위치를 측정하는 카메라 기반 시스템이다. 카메라 기반 센터링 시스템에는 조명, 카메라 및 소프트웨어라는 세 가지 주요 요소가 포함된다.
이들 각각의 요소는 부품의 정확한 측정을 획득해야 하고, 궁극적으로 PCB 상에 정확한 부품 실장에 중요하다. 오래된 격언대로, ‘시스템은 가장 약한 하나의 연결고리에 달려 있다’는 말이 적합하다.
조명
올바른 조명은 정확한 부품 실장을 향한 첫 걸음이다. 오늘날의 SMT 시스템이 광범위한 부품들을 실장하기 위해서는 우수한 조명이 있어야만 한다. 20년 전 QFP는 그야말로 낯선 모양이었지만 오늘날에는 QFP, BGA, LGA, CSP, 다이, 플립칩, 커넥터 그리고 피처, 반사도 및 모양이 매우 다양한 디바이스가 존재해 있다. 카메라와 소프트웨어는 조명이 약하게 비춰진 부품을 완전히 보정할 수 없다. 이해하기 쉽게 비유해 보자면, 열악한 조명으로 촬영된 일반 사진을 생각해 보면 된다. 포토 프로세싱 소프트웨어를 통해 밝기 또는 대비를 향상시킬 수 있다. 그러나 좋은 조명을 사용했을 때처럼 선명한 최종 사진을 얻지 못한다. 조명은 방향과 색상의 두 가지 하위 범주로 나눌 수 있다. 대상체에 적용되는 조명의 설계는 이형 부품을 센터링하는 능력과 모든 부품의 정도에 큰 영향을 끼친다.
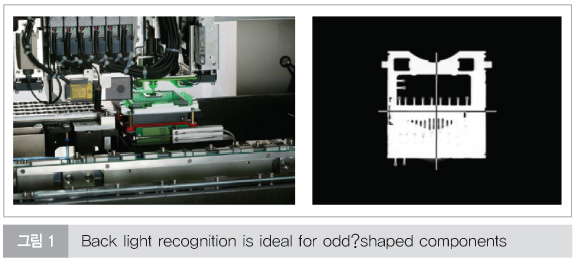
방향
SMT 부품은 리드, 볼 혹은 구체, 랜드 혹은 플랫 패드 그리고 모서리 혹은 외곽선과 같은 피쳐 또는 요소의 유형에 따라 4개의 기본 그룹으로 분리된다. 서로 다른 4개의 요소 유형의 모양과 위치가 이상적인 조명 방향을 결정한다. 카메라 기반 센터링은 부품 위치를 계산할 때 중요한 피쳐를 결정하기 위해 대조하는 방식이 적용되고 있다. 이상적으로, 카메라는 가능한 ‘보이지 않는’ 다른 모든 피쳐과 요소들의 부분을 센터링에 적용할 수 있도록 ‘보아야’한다. 카메라 방식에 있어서, 이는 센터링 요소와 다른 모든 피쳐 간의 가장 큰 대조를 의미한다.
때로는 ‘축상 조명(on axis lighting)’이라고 불리는 바닥 조명은 카메라 근처에 광원이 있음을 의미하며 일반적으로 리드 부품에 이상적이다. 리드가 조명을 잘 반사하기 때문이다. 반면 플라스틱 패키지는 일반적으로 잘 반사하지 않을 것이다. 바닥으로부터 조명이 나온다면, 부품의 바닥의 특정 다른 피처들이 비춰질 수도 있을 것이다. 그러나 QFP, TSOP 등과 같은 부품들에게는 일반적으로 문제가 되지 않는다. 몰딩이 검은색이고 빛 반사가 적기 때문이다. 흰색 몸체 커넥터들은 바닥 조명구조에서 약간의 문제가 나타날 수 있으나 소프트웨어를 통해 이를 해소할 수 있다. 일부 회사들은 리디드 디바이스를 위해 백라이트를 사용하고 있으나 이는 이상적이지 않다. 몸체를 포함한 전체 부품들이 동일하게 ‘어두운’ 색상이고 배경이 밝기 때문이다. 바닥 조명을 가지고서는 가장 중요한 부분인 오직 리드만 다른 밝기가 된다.
BGA에는 흔히 트레이스, 패드 또는 바닥 조명을 사용할 경우에 빛이 반사하는 미싱 볼이 자주 있다. 일부 CSP 및 플립칩은 반사되는 바닥면을 지니고 있다. 중요 요소와 배경 요소 간의 대비가 좋지 않은 반사되는 바닥면을 지니고 있다. 이것이 바닥 조명이 볼 구조의 특정 부품에 이상적이지 않는 이유이다. 측면 조명(볼의 평면에 거의 수평으로 들어오는 조명)이 이들 부품에 더 적합하다. 측면으로부터 볼 부품을 비추면, 볼이 미싱되었거나 혹은 존재해 있을 때 더욱 선명하게 보인다. 측면에서 불빛이 들어올 때, 카메라에 빛을 반사하는 어떠한 볼도 존재하지 않고, 미싱 볼과 존재 볼 간의 차이는 훨씬 더 뚜렷하다. 미싱 볼의 바닥 조명은 반사를 만들어 낼 수 있다. 이는 볼이 진정으로 미싱되었는지 아닌지를 결정해야 하는 소프트웨어에 더 큰 도전과제를 안겨준다. 측면 조명은 바닥 조명만큼 부품 바닥에 원하지 않는 피처를 비추지 않으므로, 소프트웨어가 실수로 센터링에 이들 피처들을 포함할 가능성을 줄여준다.
리드가 없거나 볼 구조 이형부품의 아웃라인과 센터 인식은 최종 과제이다. 이들 모양들이 상당히 불규칙적이고 반짝이거나 흐릿해질 수 있기 때문에, 최상의 상황은 부품의 실루엣을 만드는 것이다. 이는 부품의 상부로부터 빛이 들어오고 카메라쪽으로 향하게 하는 백라이팅을 의미하는데, 이 구조가 가장 좋다. 백라이트는 부품의 모양이나 반사율에 관계없이 고-대조비의 실루엣을 만든다.
컬러
빛의 방향이 중요하지만, 빛의 컬러도 중요하다. 조명 방향과 달리, 서로 다른 컬러 조명이 필요한 센터링 요소의 외형이나 위치가 아니다. 부품의 몸체 또는 센터링 요소 주변 에어리어가 일반적이다. 색깔이 있는 배경에 글씨가 쓰이고 빨간 필터로만 볼 수 있는 ‘비밀 메시지’ 장난감과 같이, 컬러 조명의 목표는 카메라를 혼동 시켜 부품 위치를 ‘읽기’ 어렵게 만드는 항목을 걸러내는 것이다.
서로 다른 부품 유형에 어떠한 색깔이 적합한 역할을 하는지와 관련해 규정된 표준이 없다. 최상의 색상 조명을 결정하기 위해서는 여러 번의 시행착오를 겪어야만 한다. 최상의 색상은 단순하다. SMT 부품의 일반적인 색상으로 더 잘 읽을 수 있게 하면 된다. 볼 부품의 경우, 적용되는 패키징 방법이 다양하기 때문에 보통 가장 큰 문제가 된다. 많은 BGA의 경우에는, 트레이스 또는 밑면에 가시적인 비아 홀을 가지고 있다. 측면 조명은 이것의 대부분을 걸러내는 반면, 골드 트레이스 또는 비아 홀에 파란색 조명을 적용하면 볼과 원치 않은 요소 간의 대비를 더욱 향상할 수 있다. 실루엣 이미지의 경우, 녹색이 더욱 이상적인 컬러이다. 멀티 컬러 조명을 사용하면 다양한 부품 센터링에 대한 향상된 유연성을 경험할 수 있다.
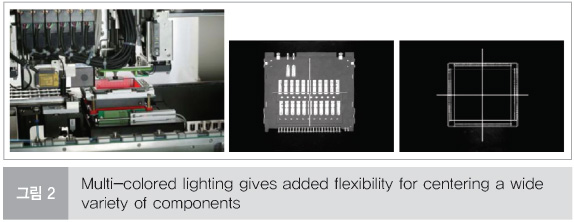
카메라
부품이 잘 비춰지면, 다음 단계는 카메라가 노즐 상의 부품 이미지를 캡처하는 것이다. 부품 센터링에 사용되는 카메라는 다양한 종류가 존재하고 있으며, 대부분이 ‘상품 가용성(off-the shelf)’을 가지고 있는 제품이다. 아날로그 및 디지털 카메라 그리고 여러 가지 통신 타입(CameraLink, USB, Firewire(IEEE1394) 및 GigE)이 있다. 이들 차이점은 비용과 속도 이유로 디자이너에게 중요하지만 최종 사용자가 고려해야 할 주요 문제는 해상도이다. 일반적인 경험으로는 카메라가 요구된 정확도에 10배의 해상도를 가져야만 한다. 카메라는 부품의 위치를 정확하게 측정하기 위해 충분히 자세하게 사진을 찍어야만 한다.
해당 공간 내에서 더 많은 선이나 픽셀이 더 세밀한 이미지를 생성하지만 오늘날 일반 디지털 카메라 시장에서 보편화된 픽셀 수만 고려하는 것으로는 충분하지 않다. FOV(field of vie)는 카메라가 볼 수 있는 영역이다. 높은 픽셀 수를 지닌 카메라이지만, 넓은 FOV가 자세한 이미지를 충분히 생성하지 못할 수도 있다. 얼마나 많은 메가 픽셀 수를 지니고 있는가에 비해 mm 당 픽셀 수가 더욱 중요한 카메라 해상도 측정요소이다.
낮은 해상도의 카메라를 사용하는 것은 마킹되지 않은 줄자만으로 방의 길이를 정확하게 측정하려고 노력하는 것과 유사하다. 방이 정확한 줄자 내의 정수가 아니라면, 그 길이에 대한 일부 야드를 추정하는 것이 필요하다. 반대로, 1mm까지 표시가 있는 줄자를 사용하면 보다 정확한 길이를 결정할 수 있다. 부품 센터링에서도 동일하게 적용된다. 더 높은 해상도(mm 당 더 많은 픽셀)는 더 미세한 측정 마킹과 같다. ‘마킹’이 미세할수록 카메라가 부품 위치를 보다 정확하게 측정할 수 있다.
장비 디자이너의 도전과제는 FOV가 작으면 최대 부품 사이즈도 작기 때문에, 해상도와 FOV 간의 최적의 절충안을 선택하는 것이다. 한편, 해상도(mm 당 픽셀 수)가 낮으면 센터링 정확도가 떨어진다. SMT 부품은 다양한 치수, 요소 크기 및 피치로 제공되기 때문에 최대한 전체 부품에 대응하기 위해 때때로 2개의 다른 카메라를 사용하는 방법도 필요하다.
소프트웨어
소프트웨어는 이미지를 분석하고 센터링 프로세스의 마지막 단계에서 부품 위치를 결정하는데 사용된다. 소프트웨어는 이미지의 어떤 기능을 센터링에 사용할지, 정확한 위치를 결정한 다음 부품의 센터를 계산할 수 있어야만 한다. 위치 계산은 각 센터링 요소를 정확하게 위치시키는 에지 기반 알고리즘에 의해 일반적으로 수행된다. 경우에 따라 알고리즘은 카메라가 캡처한 특징들 중에서 중요하지 않는 부문을 무시하는 시스템의 성능을 향상시키기 위해 패턴 매칭을 적용한다. 2개 이상의 픽셀로 효과적으로 분할하는 ‘서브-픽셀 어큐러시(Sub-pixel accuracy)’ 방법은 카메라의 유효 해상도를 향상시키는 데에도 사용된다. 비전 프로세싱에 활용되는 대부분의 소프트웨어는 독점적이며 자주 영업 비밀로 간주된다.
대화형이고, 유연한 사용자 인터페이스 소프트웨어는 가장 복잡한 요소 패턴을 쉽게 규정할 수 있는 기능을 작업자에게 제공한다. 대부분의 리디드 디바이스와 심플한 BGA는 동일하게 규정하기 쉬운 매우 단순한 패턴으로 배열된 요소를 가지고 있지만, 더 많은 부품 디자이너들은 매우 복합하고 종종 랜덤한 디자인을 사용하고 있다. 특히 BGA의 경우가 그렇다. 그러나 리디드 부품에도 존재하는데, 특히 커넥터가 그렇다. 해당 커넥터는 불규칙한 위치에 다양한 너비 및 폭의 리드를 가지고 있다. 이들 부품들은 작업자가 간단한 좌표 입력으로 규정하기가 어려울 수 있다. 첨단 비전 시스템은 작업자에게 볼이나 리드 패턴을 자동으로 ‘습득’할 수 있게 한다. 이 방식은 수동 데이터 입력보다 빠르고 더욱 정확하다.
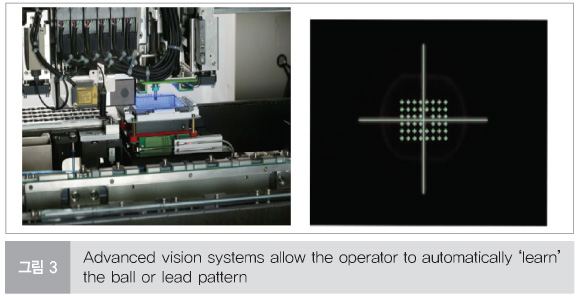
마지막으로 비전 시스템은 표준 조명으로는 잘 읽을 수 없거나 사용자 지정 조명 패턴으로 더 잘 읽히는 부품을 처리하기 위해 조명 방향, 색 및 강도를 프로그래밍 할 수 있어야 한다. 이러한 경우, 소프트웨어가 정확한 센터링 결과를 보고하면서 사용자에게 자세한 제어 비전 파라미터를 제공하는 것이 중요하다.
결론
SMT 시장에서 사용되는 다양한 카메라 기반 센터링 시스템이 있다. 이러한 시스템을 평가할 때 단일 피터가 아닌 전체 패키지를 고려하는 것이 중요하다. 조명이 다양한 부품을 처리하는가? 카메라가 작업에 충분한 해상도를 가지고 있는가? 소프트웨어를 통해 운영자는 복잡하거나 불규칙한 부품을 쉽게 정의할 수 있는가? 대부분의 경우 이를 평가하는 가장 좋은 방법은 사용 가능한 가장 일반적인 부품을 테스트 한 다음 실장 정확도를 확인하는 것이다. 훌륭하고 완전한 ‘비전 시스템’이 이를 처리할 수 있다.