보이드 정량 측정방법
솔더 프리폼 활용
솔더 접합 내의 솔더 보이드는 SMT 어셈블리 공정에서 일반적으로 발생하는 현상이다. 그들의 기원은 잘 알려지지 않았지만, 리플로우 프로세스 동안 플럭스 잔사물을 완벽하게 배출하는 솔더 필렛의 불량에 의한 오류라고 일반적으로 인식되고 있다. 솔더 보이드의 양은 어셈블리 내부에서의 서로 다른 플럭스 조성, 솔더 합금, 보드와 부품 금속성 간의 활동에 따라 크게 다를 수 있다. 리플로우 프로파일 뿐만 아니라 스텐실 개구 디자인은 전체 보이드 수준에 큰 영향을 미칠 수 있다. 이전에 소개한 BGA 분석 소프트웨어와 대칭 Z-축 리플로우 구조를 사용한다는 가정 하에 ‘샌드위치’ 개념을 본고에서 설명한다.
솔더 보이드는 대다수의 솔더 접합에 존재하고, 보이드가 적고 총 보이드 함유량이 미세할 경우에 수용되는 것이 일반적이다. X-ray 측정이 솔더 보이드 분석에 지배적으로 사용되고 있지만, X-ray 이미지의 2D 형상과 소프트웨어 한계로 인해 grid array 부품이 아닌 경우에 상당히 주관적인 판단이 가미된다. 리플로우 동안 리드 하부 및 부품 근처 하부를 시연하기 위해 구리 ‘샌드위치’를 만드는 기발한 방법이 발전되어 왔고, 이 기술이 자세하게 논의되었다. 이 방법은 무연 솔더, 특주형 페이스트 발전 그리고 프로세스 개선을 위한 정량적인 솔더 페이스트 보이드 분석을 가능하게 한다. 본고에서는 프로파일과 페이스트 저장의 영향도 설명한다. 게다가 BBC(Bumpered Chip Carrier) 상에서 히트 스프레더(heat spreader)에 대한 솔더 보이드 관점에서의 최적화된 디자인과 재료 선택이 개선되고 있으며 이를 설명한다.
서문
솔더 접합 내의 솔더 보이드는 SMT 어셈블리 공정에서 일반적으로 발생하는 현상이다. 그들의 기원은 잘 알려지지 않았지만, 리플로우 프로세스 동안 플럭스 잔사물을 완벽하게 배출하는 솔더 필렛의 불량에 의한 오류라고 일반적으로 인식되고 있다. 솔더 보이드의 양은 어셈블리 내부에서의 서로 다른 플럭스 조성, 솔더 합금, 보드와 부품 금속성 간의 활동에 따라 크게 다를 수 있다. 리플로우 프로파일 뿐만 아니라 스텐실 개구 디자인은 전체 보이드 수준에 큰 영향을 미칠 수 있다. 게다가 솔더의 보이드 미스터리는 몇 가지를 제외한 산업계에서의 정량 측정 툴의 부족이다. BGA 보이드 분석 소프트웨어는 이러한 예외 중 하나이다. 이 소프트웨어는 솔더 구형의 경계와 보이드의 내부 경계를 결정하기 위해 그레이-레벨-픽셀 분석(gray level pixel analysis)을 이용한다. 경계가 설정되면, 이들 구조 내부에서 영역을 측정할 수 있고 전체 보이드 비율을 판단할 수 있다. 이러한 타입의 측정은 보이드가 크거나 혹은 구형의 외부 가장자리에서 발견될 때 탁월한 성능을 보인다. 그러나 보이드가 작고 구형 밀도가 더 짙은 곳의 중앙에 위치할 때 보이드가 보이지 않을 수도 있다. 주위 재료들과 자체 그레이-레벨이 비슷하기 때문이다. X-ray 파워를 강하게 하면 소형 보이드를 노출시킬 수 있겠지만, 구형의 측정 영역이 쪼그라들고, 부정확성과 폭등한 보이드 비율이 나타난다. 이 같은 문제는 칩 혹은 리드형 부품 솔더 접합 내에서 더욱 더 부각된다.
완성된 어셈블리에 X-ray를 투과할 때, 내부 트레이스, 비아 그리고 솔더 접합의 이미지가 중첩되는 보드의 후면에 존재한 부품들조차도 솔더 접합의 경계를 정확하게 결정하려고 하는 소프트웨어 알고리즘에 혼동을 준다. 간단히 말해서, X-ray 이미지는 2D이다. 이상적인 구조는 박스 혹은 실린더와 같이 Z-축으로 대칭이 되어야만 한다.
새로운 접근법
이상적인 보이드 정량 측정 방법이 BGA 분석 소프트웨어와 대칭 Z-축 리플로우 구조를 사용한다는 가정 하에 ‘샌드위치’ 개념이 개발되었다.
이 새로운 접근 방법은 플럭스 배출이 가장 어려운 부품 아래에서 동일한 리플로우 열 환경과 원하는 야금을 유지하면서 보이드에 맞춰 솔더 접합의 최악 조건을 시연한다. 이 아이디어는 CCGA(Ceramic Column Grid Array)에서 정량적인 방법을 통해 보이드 비율을 확인하려는 질문으로부터 시작되었다. CCGA 컬럼(column)은 10/90 Sn/Pb이고 솔더 필렛의 약 45%가 덮여졌다. 이러한 조밀한 컬럼들을 관통해서 보기 위해 충분한 전력이 사용되면 솔더 조인트의 둘레가 옅어지고, 전체 필렛의 55%가 보이지 않는다. 원형 필렛의 직경을 보기 위해 적정한 전력이 사용되면, 컬럼 하부 영역은 보이지 않는다. 그림 1에서 보는 바와 같이 컬럼 변위, 내부 트레이스 그리고 비아가 복잡하게 얽혀있다. 과도한 전력 없이 X-선이 조사될 수 있는 만큼 얇은 솔더 패드와 동일한 직경의 컬럼을 감안하여 솔더 프리폼이 선택되었다. 해당 애플리케이션에서 솔더 보이드 형성에 기여할 수 있는 변수를 최소화하기 위해 프리폼 합금은 10/90 컬럼과 동일하게 선택되었다. 몇 가지 두께는 최종 솔루션으로써 5mil 두께의 30mil 직경으로 테스트되었다.
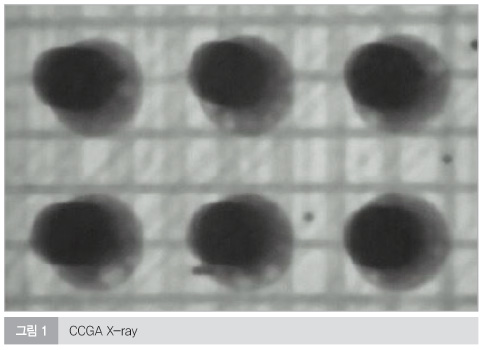
이러한 디스크를 배치하는 데에는 여러 가지 어려움이 있다. 첫 번째 문제는 신뢰할 수 있는 원본 컵 모양이었고 적층 디스크가 해결해야 할 첫 번째 문제였다. 두 번째 문제는 디스크를 실제로 배치하는 메커니즘이다. 픽앤플레이스의 비전 시스템이 일반적인 칩과 같은 모서리가 있는 부품만 인식하지 라운드형 부품을 인식하도록 프로그래밍되지 않았다. 이는 ‘볼리스틱(ballistic)’ 픽앤플레이스 전략과 관계가 있다. 이 문제를 해결하기 위해 그림 2와 같이 각각 하나의 프리폼인 원통형 포켓의 정밀한 매트릭스 트레이가 개발되었다. 다음으로 픽앤플레이스 노즐에 대한 개선이 있었다. 스톡형 초소형 노즐 OD는 프리폼과 동일하게 했다.
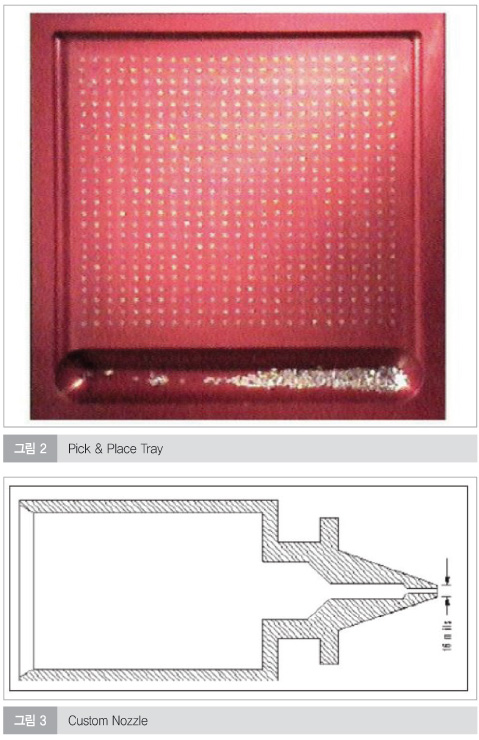
수많은 픽업 문제가 대두된다. 프리폼이 완벽하게 센터링되지 않는다면, 가끔 프리폼은 픽 이후 자체 가장자리에서 뒤집어질 것이며, 프리폼 실장 디포밍에서 충돌할 것이다. 여러 가지 개선책들이 그림 3에서와 같이 0201 칩에서 전형적으로 나타나는 노즐 팁 다운을 궁극적으로 줄이고 있다. 노즐 팁 표면적을 줄이는 것은 실장 작업에서 프리폼을 더 잘 배출하도록 도움을 준다.
CCGA 테스트 시편의 어셈블리는 애플리케이션의 형상과 패드 금속화를 유지하기 위해 ‘패드 전용’ 세라믹 시편을 적용하였다. 이 시편은 그림 4에서처럼 내부 트레이스가 없다. 솔더 페이스트는 패드보다 직경이 1mil 더 작은 원형 개구를 통해서 프린트되고 프리폼은 솔더 페이스트 전반에 놓이고 그런 후에 그림 5에서와 같이 리플로우된다. 프리폼이 셀프-센터가 될 수 있는 4mil 미만의 패드를 벗어나는지를 입증하였다. 인접한 프리폼과의 단락을 방지하려면 Z-축 배치에 주의해야 한다.
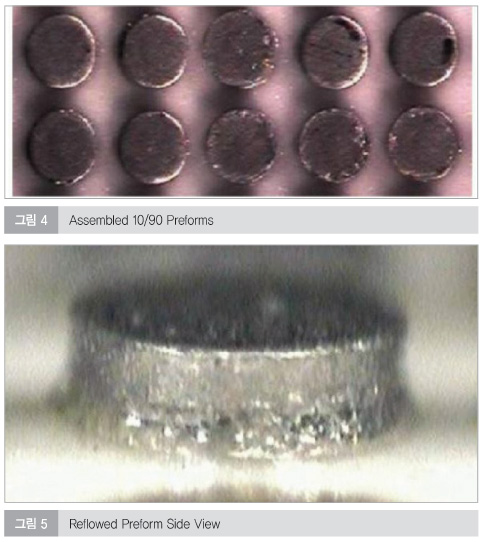
어셈블리 이후 시편 영역에 X-선을 조사하고, 그림 6과 같이 기성 BGA 분석 소프트웨어를 사용하여 정량적인 보이드 분석을 수행해 이미지화하였다. 이 소프트웨어는 구조 내부의 특정 개별 보이드가 미리 조정된 수치(즉, 5%)보다 크면, 총 보이드 비율과 pass/fail 상황 둘 다 제공한다. 이 기술은 맞춤형 63/37 Sn/Pb 계열의 솔더 페이스트 또는 유사한 용융점을 갖는 다른 합금에서 매우 잘 작동하지만 무연(Sn/Ag/Cu, Mp 219℃) 제품으로 테스트 한 결과, 프리폼들이 녹아서 시험 중 하부에 있는 솔더 페이스트에 부분적으로 결합하는 현상이 나타나기도 했다. 이는 동일한 형태의 OFHC 구리 프리폼으로 전환함으로써 해결되었다. 일반적인 페이스트 보이드 벤치마크를 위해 전용 패드 테스트 영역(그림 7 참조)이 Benchmarker II 테스트 보드에 포함되었다. 이를 통해 Entek OSP(Organic Solder Protectant) 및 ENIG (Electroless Nickel Immersion Gold)와 같은 표준 PCB 표면에서 솔더 페이스트를 테스트하였다. 아주 단순하게 우리는 원통형 구조의 구리 샌드위치(그림 8 참조)를 만들어서 표준 BGA 분석 소프트웨어로 매우 정량적인 보이드 분석을 가능하게 했다.
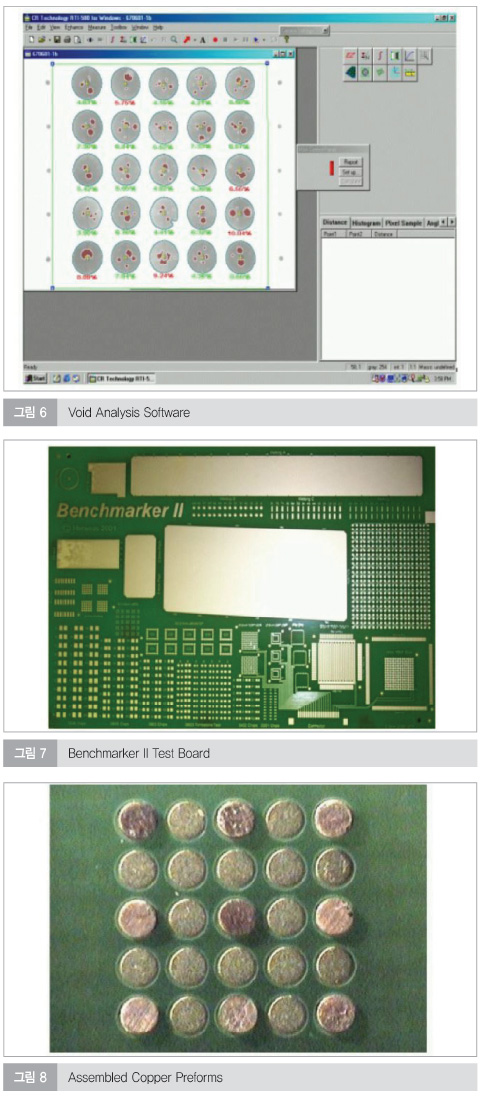
유통기간 영향
주요 커패시터 제조업체에서 발간한 여러 평가서에 따르면, 0201 MLCC 시장 볼륨은 2010년에 1,000억~2,000억 유닛 사이인 것으로 예상된다. 0201 MLCC 제조업체의 실제 제조 볼륨을 조사했을 때, 이 보다 더 많은 1,050억~2,050억 유닛으로 나타났다.
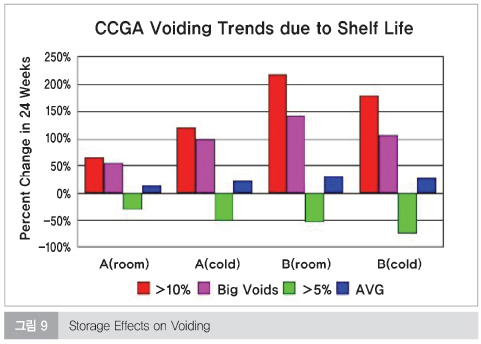
이 데이터를 통해 2개의 재료의 경향이 다르며 그들 간의 보이드 거동이 상당히 차이가 있었다. 저온 저장시 재료 A에 대한 에이징의 효과는 재료 B와 반대 방향으로 가속화되었다. 2개 두 재료 모두 무기질(분말 + 첨가제)의 정확하게 동일한 소스와 사양을 가지고 있다.
프로파일 영향
리플로우 프로파일의 영향이 중요하게 여지질 수 있으나, 그 크기는 여기저기에서 상당히 다르다. 다음의 예는 그림 10에서 설명된 것처럼, 4개의 프로파일을 가진 구리 프리폼을 사용하여 Entek 패시베이션 구리를 통해 테스트한 무세척 재질의 63/37 Sn/Pb 2개 제품을 포함하고 있다. 프로파일 매트릭스는 주어진 조성의 프로파일 민감성을 노출하기 위해 설계되었다. 이 경우 보이드(voiding)와 관련이 있다. 램프 스타일 예열로 구성된 2개의 프로파일과 소크 예열로 구성된 2개가 있다. 액상 상태에서 60초 동안 225℃의 피크를 유지하는 2개의 프로파일과 90초의 확장된 액상 동안 240℃의 피크를 유지하는 더 뜨거운 2개의 프로파일이 있다. X-선 데이터는 비교를 용이하게 하기 위해 단일 ‘포인트 스케일’로 압축되어 왔다. 이들 포인트들(100이 최고)는 다음과 같이 요약될 수 있다:
Points = (≤4% - ≥6%)
“총 보이딩(voiding)이 4% 미만 구조의 %에서 총 보이딩 6% 이상 구조의 %를 뺀 것.”
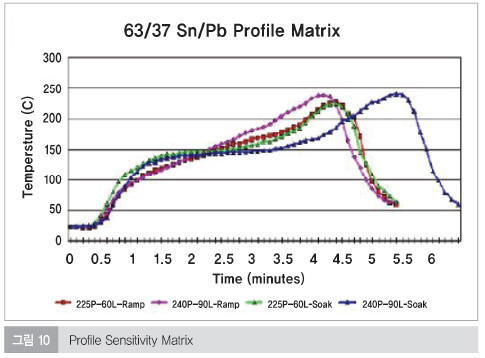
그림 11의 결과는 재료 1이 보이드 형성 테스트 프로파일에 둔감하고 전체 보이드 생성에 있어서 재료 2보다 훨씬 우수하다는 점을 확연하게 보여주고 있다. 2개의 재료는 동일한 수지 시스템과 농도를 공유하고 있다; 두 물질의 주요 차이점은 재료 1이 재료 2보다 현저하게 높은 농도의 활성제로 혼합되었다는 것이다. 재료 2 내의 단일 솔벤트 vs 재료 1 내의 솔벤트 혼합이 또 다른 차이이다. 재료 1은 보이드 측정을 위한 적절한 정량적인 툴을 감안하여 낮은 보이드 비율 생성 능력을 보여주는 새롭게 설계된 무세척 제품이다.
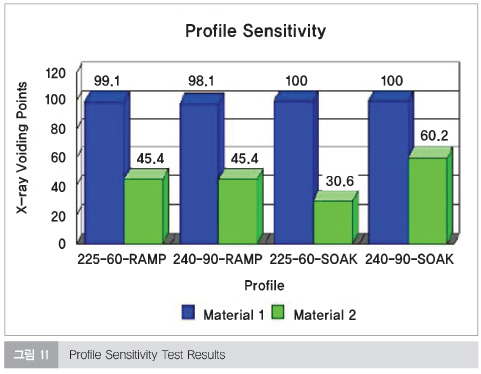
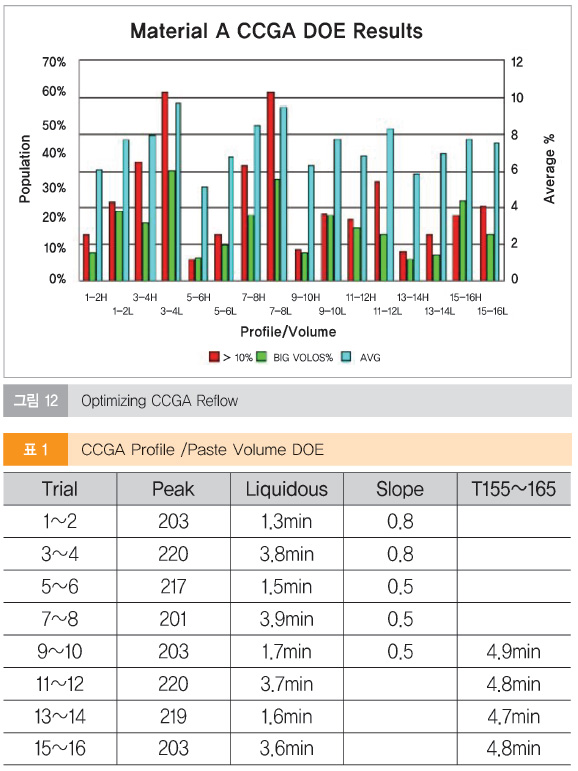
프로파일 민감도의 다음 예는 CCGA 보이드 개선을 위한 DOE(Department of Energy)를 포함시켰다(표 1 참조). 8개의 서로 다른 프로파일과 2개의 솔더 페이스트 체적을 생성하였다. 표 1에는 프로파일의 주요 차이점이 요약되어 있다. 그림 12는 엄격한 프로파일 민감도를 나타내는 DOE 결과에서의 커다란 차이를 보여주고 있지만, 더 높은 피크 온도의 이들 재료(셀 5~6H 및 13~14H))와 늘어난 솔더 체적에 대한 솔루션을 나타내고 있다.
금속공학 영향
무연 솔더페이스트는 Sn/Pb 제품보다 보이드 발생 레벨이 높다는 것은 상당히 잘 알려져 있다. 그림 13에서 보는 바와 같이, 무세척 무연 솔더페이스트와 납 함유 솔더 페이스트 간의 보이드 결과는 극명한 대조를 보여주고 있다. 그림 14는 최악의 무연 및 최상의 납 함유 재료의 데이터 분포를 보여주고 있다. 이들 모든 데이터는 Entek OSP 보드 및 구리 프리폼에서 생성되었다.
다음 예에서는 솔더페이스트 고유의 보이드화 경향과 솔더링 가능한 표면의 부가적인 효과 간의 관계를 더욱 강조하고 있다. 재료 A(CCGA용 특수 페이스트)는 Al2O3 기판 상에 원형 침전물로서 10mil 스텐실을 통해 인쇄하였다. 5mil 두께 구리 프리폼 여러 개가 스페이서 역할을 위해 인쇄된 침전 주위에 놓였고, 두 번째 기판을 습식 페이스트 위에 놓은 다음 리플로우시켰다. 리플로우 후에 솔더는 10mil~15mil 두께로 디스크를 형성하였다. 그림 15에서 보여준 X-Ray 이미지에서는 매우 적은 보이드만 볼 수 있었고, 실제로 대부분의 기판에서는 보이드 프리를 보였다. 빨간색 화살표는 30mil 직경의 10/90 10mil 두께 프리폼을 가리키고 있다. 이 테스트는 이 시스템에 솔더 가능한 표면이 존재하지 않기 때문에 페이스트만의 보이드 특성을 나타내고 있다. 보이드는 0%~1.76% 내에서 형성하였다. 이 제품과 관련된 그 다음의 관찰은 그림 16에서와 같이 동일한 많은 양의 재료가 단순히 프린트되고 쿠폰 금속화로 리플로우 될 때 보이드가 증가했다.
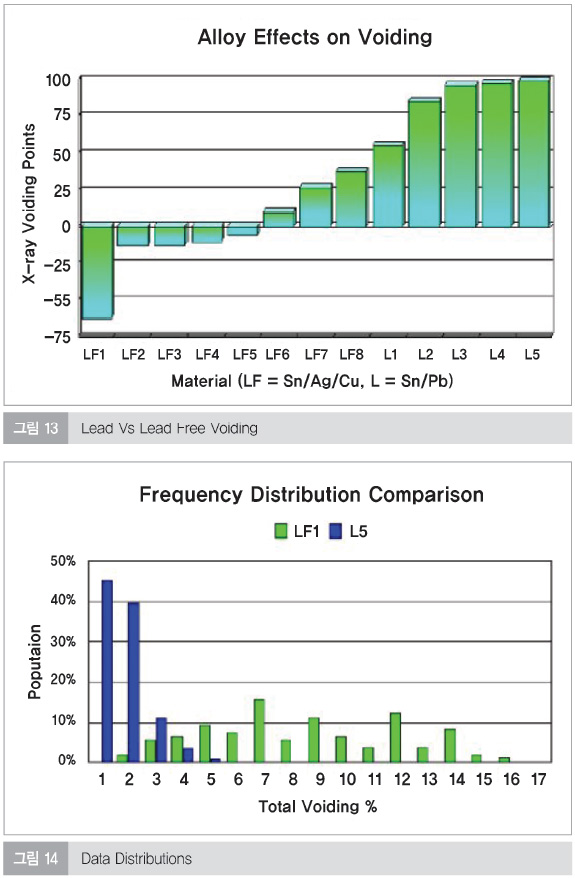
보이드는 0.14%~4.13% 범위에서 나타났다. 최종 관찰은 솔더페이스트가 5mil 두께의 10/90 프리폼으로 ‘캡핑’되었을 때 전체 보이드가 2.62%~8.21%로 눈에 띄게 증가했다.
처음에는 캡핑 프로세스가 리플로우 동안의 플럭스 유출 방지에 의한 보이드 증가의 원인이라고 생각되었지만 그림 17의 ‘기판 샌드위치’ 실험에서는 이러한 이론을 반박할 수 있었다. 아마도 솔더 프리폼 캡의 추가적인 솔더링 가능한 표면이 대부분의 추가적인 보이드의 원인이었다. 이 이론이 사실이라면 보이드의 80%~90%는 접합할 표면과의 상호 작용 때문이며 솔더페이스트 원료 문제는 아니다.
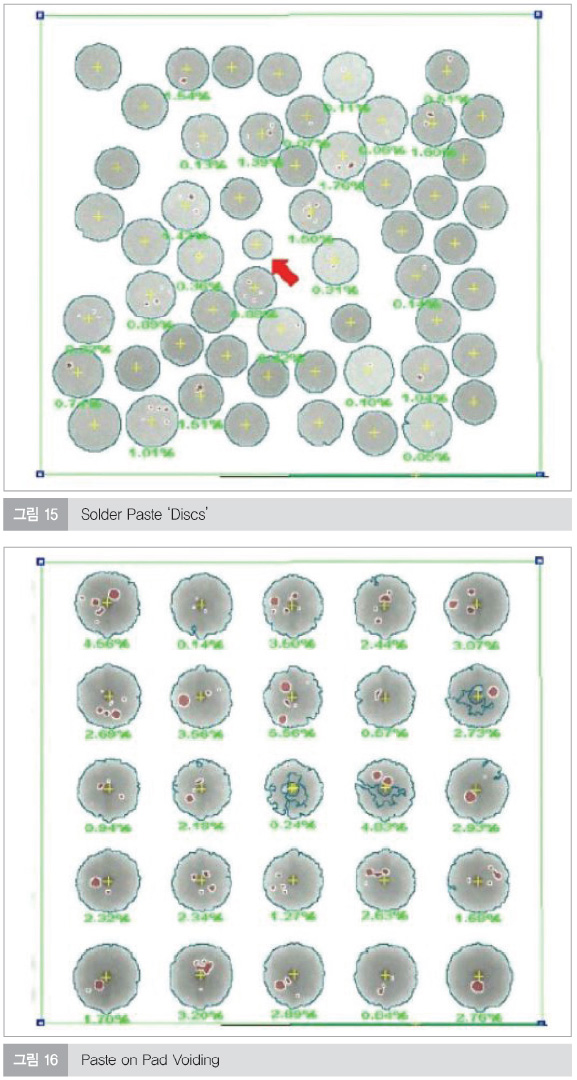
디자인 영향
그림 18에 도시된 BCC(Bumped Chip Carrier)와 같은 부품은 일반적으로 대형 평면 중앙 히트 스프레더 아래의 보이드(voiding) 문제가 있다. 큰 보이드는 균일하고 빠른 열전달을 막아서 부품 조기 고장, 성능 저하 또는 둘 다를 초래할 수 있다. 문제는 앞서 설명한 무연 솔더페이스트의 첨가제가 보이드되어 악화된다.
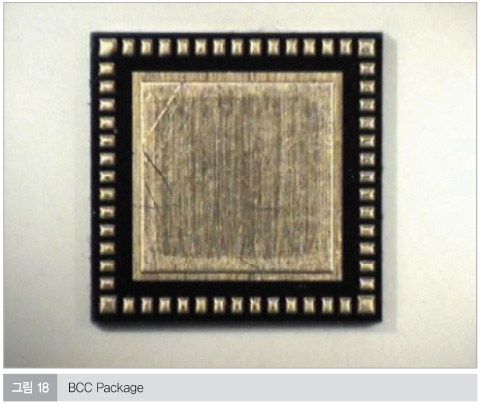
27개 디자인 요소, 4개의 페이스트 실험은 최적의 디자인/페이스트 조합을 찾기 위해 구성되었다. 에어 리플로우 결과와 유사한 질소 리플로우를 이용해 실험을 반복했다. BCC와 PCB 모두 ENIG 처리하였다. 일반적으로 인쇄 적성(適性) 라인 해상도 테스트에 사용되는 Benchmarker II 테스트 보드의 중앙 커다란 사다리꼴 섹션(그림 7 참조)이 일반적인 솔더 패드로 사용되었습니다.
그림 19에서 볼 수 있듯이 단순한 사각형에서부터 복잡한 모양까지 다양한 디자인 아이디어를 포함시켰다. 디바이스는 전체 27개 디자인 어레이에 단순하게 픽앤플레이스되었고, 리플로우되었다. 중앙 히트 스프레서 영역에 대한 페이스트 평균 범위는 25%~100%이었다.
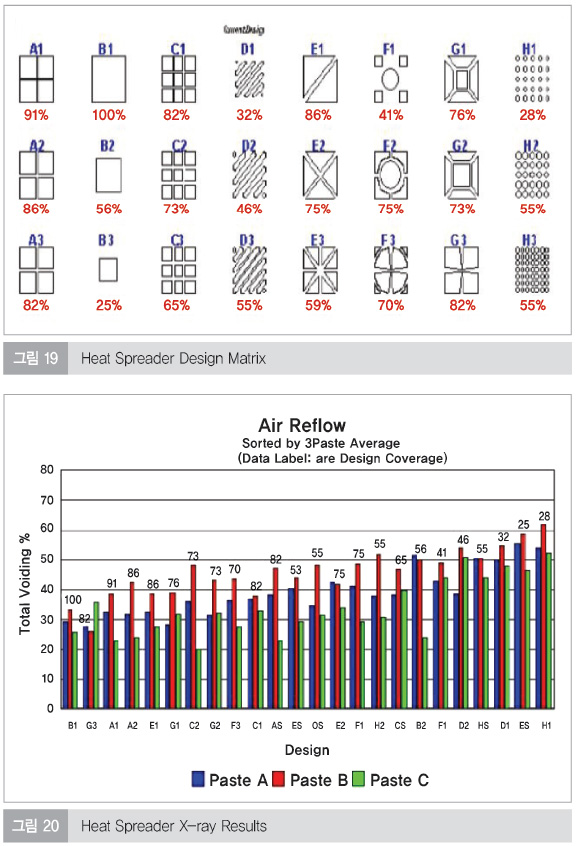
디바이스는 X-Ray 검사를 실시했고, 다이어테치 비율 소프트웨어 애플릿을 사용하여 총 보이드 비율 뿐만 아니라 최대 보이드 크기를 정량화했다. 그림 20에서 볼 수 있듯이 초기 데이터 정렬은 페이스트 범위와 총 보이드 간의 상관관계가 존재할 수 있음을 나타내고 있다. 이 데이터는 또한 대부분의 파트에 대한 재료들 간의 성능 차이를 보여주고 있다. 회귀 분석 플롯(그림 21 참조)은 최고의 결과를 산출하는 가장 단순한 설계(B1)로 보이드가 줄어들고 범위가 단순해지는 추세를 더욱 뒷받침하고 있다. 게다가 페이스트 C를 사용한 프로파일 작업은 보이드 제거 목표(<20 %)를 충족시킨다. 이 프로젝트는 전체 보이드의 약 70%에서 시작되었다.
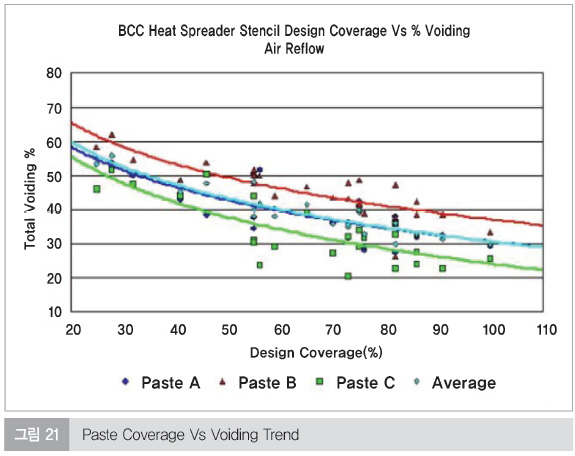
결론
많은 질문에 대한 모든 해답을 도출하지는 못했지만, 솔더 보이드를 피하기 위한 몇 가지 추세를 알 수 있었다.
▶ 보이드 형성은 단일 소스가 아닌 다양한 시스템 변수의 결 과이다.
▶ 각 페이스트는 리플로우 프로파일과 민감도와 관련해 독특 한 보이드 거동을 가지고 있다.
▶ 페이스트 제조시기와 보관 조건은 보이드의 수준에 영향을 줄 수 있다.
▶ 무세척 무연 페이스트는 납 함유 제품에 비해 더 많은 차이 를 보인다.
▶ 패드 및 부품 야금은 총 보이드 비율에 확실하게 영향을 끼 친다.
▶ 히트 스프레더가 있는 디바이스와 같은 대면적 솔더링은 보 이드 제거에 문제가 될 수 있지만 페이스트 범위를 최대화 하여 최소화할 수 있다.