하단 단자부품(BTC) 보이드 생성에 초점
다양한 보이드 생성 인자들 실험
본 연구는 보이드에 관한 여러 가지 요인, 즉 테스트 보드 표면 마감, 보드 산화, 솔더 합금 선택, 페이스트 플럭스, 페이스트 에이징 및 부품 설계/스텐실 패턴의 영향을 조사하기 위해 시작되었다. 이들 각 요인은 전체 평균 보이드 비율에서 약간의 차이를 보였지만 모든 차이는 데이터 세트 내의 변동과 비교해 매우 작았다. 보이드 값은 다른 테스트 보드의 이들 솔더 재료에 대한 20% 미만의 일반적인 값과 비교하여 높았다. 이는 테스트 보드 디자인을 개선하여 전체 보이드 비율을 낮출 수 있음을 의미한다. 비교를 위해, 이들 테스트 보드를 사용하여 재료 및 공정 변화가 최악의 디자인에 미치는 영향을 보여주었다.
요약
솔더 조인트의 Z-축 연속성 중단이 열전달을 방해하기 때문에 보이드 현상은 열 평면(thermal plane)을 가진 부품에서 주요 관심사이다. 솔더 페이스트를 이용해 부품을 어셈블리할 때, 부품 하부에서의 제한적인 솔더 페이스트 침전물의 특성으로 인해 보이드가 발생할 경향이 짙다. 리플로우 공정 시, 리플로우 프로파일, 부품 디자인, 보드 및 스텐실 디자인 그리고 재료 계수와 같은 요소들이 솔더 조인트의 보이드 양에 많이 기여한다. 본고에서는 솔더 페이스트 합금 및 플럭스 조합뿐만 아니라 프로파일 및 보드 표면 마감재에도 중점을 두었다.
지난 10년 동안 고온 환경에서 성능을 향상시키고 열 사이클링 테스트에서 신뢰성을 높이기 위한 목적으로 몇 가지 합금이 개발되었다. 성능 개선을 위해 Sb 및 Bi와 같은 첨가제들을 일반적인 SnAgCu에 추가하여 이들 합금이 탄생되었다. 새로운 합금의 채택을 막는 주요 걸림돌 중 하나는 높아진 보이드 발생비율이었다. 이전 논문들에서는 하나 이상의 신규 합금들을 가지고 공정 및 스텐실 변형의 효과를 살펴보았다.[1]
서로 다른 페이스트 플럭스와 결합하여 자동차 업종에 제안하기 위해 솔더 페이스트의 포함 조성물 범주 내에 여러 합금을 포함하였다. 다양한 합금과 일반 보드 표면 마감재를 활용하여 신규 제품들의 보이드 결과를 비교하였다.
소개
BTC 어셈블리의 과제
BTC(Bottom Terminated Component) 하부의 보이드 현상은 극복해내야 할 전자산업계의 중대한 과제이다. 현재 일반적인 어셈블리에는 많은 QFN이 필요하며 이러한 어셈블리에는 종종 여러 유형의 BTC가 포함되고 있다. 이들 부품들은 부품의 하면에 표면 마감 처리된 평평한 단자를 가지고 있으며, 노출된 리드 또는 솔더 조인트가 없다. 일반적으로 부품의 중앙에는 주변에 부가 신호 리드가 있는 커다란 열 접지 패드가 있다. 초기 어셈블리 테스트는 시그널 리드의 연속성을 보장하겠지만, 경우에 따라 현장 불량을 예방하지는 않는다. 이 현상은 과열과 다이 크랙을 유발하는 중앙 솔더 조인트의 열악한 열전도 탓이다. 솔더 조인트의 보이드로 인해 솔더 조인트의 z-축 불연속성이 열악한 열전도의 원인이다.
솔더 조인트가 숨겨져 어셈블리의 X-선 스캔이 필요하기 때문에 BTC 검사가 어려울 수도 있다. X-선 이미지는 부품의 2차원 view를 제공하고 보다 명암 대비로 저밀도 영역을 지정한다(그림 1 참조). 그런 다음 소프트웨어를 활용하여 보이드를 나타내는 영역의 %, 가장 큰 보이드의 크기와 총 보이드 수량을 정량화한다. 브릿지가 감지될 수도 있고, 다양한 외형들이 간혹 부품 평탄도의 차이를 보여줄 수 있기 때문에 솔더 조인트 주변의 이미지를 보는 것이 중요하다.
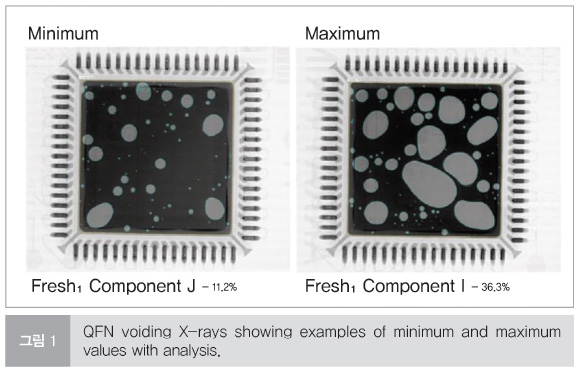
보이드 최소화를 위해 어셈블리 프로세스를 최적화하는 것이 어셈블리의 여러 측면에서 보다 유리하다. 공정의 한 부분을 변경하거나 솔더 재료를 간단히 전환하여 보이드 최소화를 이뤄내기가 쉽지 않다. 보이드가 불량의 원인이라고 판명되었을 때, 다양한 어셈블리 시나리오가 검토되어 왔다. 유발 인자들이 다양한데, 보통 디자인, 프로세스 그리고 재료의 3가지 유형으로 분류하고 있다. 그림 2는 성능을 최적화하기 위해 고려해야 할 변수의 예를 보여주고 있다.
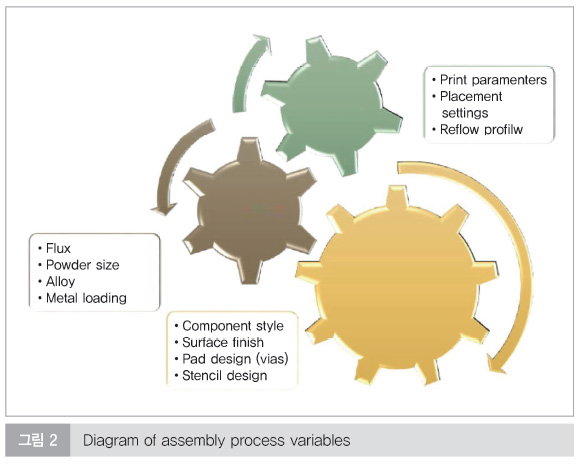
보이드 형성에 기여하는 2가지 주요 메커니즘은 ‘빈약한 젖음’과 ‘휘발성물질 갇힘’이다. 먼저, 솔더가 젖게 되지 않는 영역은 솔더 조인트 형성에서 불연속성을 유발할 것이고, 보이드 생성 가능성을 높일 것이다. 빈약한 젖음은 종종 부품 및 패드 표면의 열화에 의해 발생한다. 표면 마감 처리는 동박 패드가 공기와 접촉하여 산화되는 것을 방지한다. 또한 표면 마감 처리에도 불구하고 플럭스 혹은 야금이 결합해야만 하기 때문에 솔더 조인트 형성에 있어서 장벽 역할을 하기도 한다. 이러한 방식으로 표면 마감재는 보이드에 미치는 영향이 크게 달라질 수 있다. 솔더 페이스트 플럭스는 산화물을 제거하고 젖음성을 증진시킨다.
두 번째 메커니즘인 휘발성물질 갇힘 현상은 부품과 보드 사이의 넓은 해당 영역과 낮은 스탠드오프를 유발하기 때문에 BTC의 고유한 도전과제가 된다. 휘발성 화합물을 포함한 보드와 솔더의 재료들은 리플로우 동안 배출한다. 이들 가스는 BTC에서 형성된 좁은 공간에 제약을 받지 않기 때문에 다른 부품 주위에서 자유롭게 빠져 나온다. 리플로우에서 액상에 도달하고 솔더 합금이 용융되어 솔더 조인트를 형성하면, 갇혀있던 잔류 가스는 기포를 형성한다. 이들 대부분의 기포들은 액상 솔더의 표면 장력에 의해 빠져 나가지만 합금이 고체화되기 전에 빠져 나가지 못한 기포들이 솔더 조인트에 보이드로 남는다.
보이드에 초점을 두는 동안, BTC 어셈블리에서 가장 중요한 인자인 ‘스탠드오프 높이’를 놓치기 쉽다. 부품 제조업체는 솔더 조인트에 의해 형성되는 일정량의 스탠드오프를 권장하고 있다. 부품 제조업체에서는 허용 가능한 최소 스탠드오프를 약 50미크론으로 보고 있다. 이는 일반적으로 크로스-섹션과 같은 파괴분석과 분석용 SEM 이미지를 통해 측정된다. 일부 X-선 설비에서는 높이와 평탄도를 검출할 수 있는 지형분석(topographical analysis) 알고리즘이 적용되어 이제는 가용하기도 하다. 솔더 조인트가 권장한 최소 두께보다 낮다면, 보드와 부품 간의 CTE 불일치의 경우에 간극을 메우기에 솔더가 충분하지 않을 것이다. 이는 보이드로 막연하게 연결만 된 상태로, 추가적인 기능성 불량을 유발할 수 있다.
충분한 스탠드오프 높이를 지닌 솔더 조인트는 보이드 비중 50%까지 가속 수명 테스트(ALT, accelerated life testing)를 통해서 가용한 성능을 보여주었다.[2] 이는 부품이 최적으로 작동하는데 필요한 열 부하를 고려한 것이 아니라 BTC와 관련된 솔더 조인트의 강력한 특성을 보여주기 위한 것이다. 본고에서는 그림 2의 일부 인자들(표면 마감재, 솔더 페이스트 재료 선택 및 부품/스텐실 디자인)이 미치는 영향을 살펴보았다.
실험 설계
실험용 테스트 보드에는 QFN 부품만 포함하도록 설계하였다. 2종의 부품은 동일한 외형 치수를 가지고 있으나, 주요 차이점은 중앙 써멀 패드의 크기였다. 그림 3은 2개의 디자인을 보여주고 있다. 9개의 부품 위치 중 가능한 5개만을 선정하였고, 그 이후에 스텐실 디자인에 노출시켰다. Design A보드에는 더 작은 중앙 써멀 패드가 있으나 스텐실 디자인에 윈도우 페인(window pane)이 많았다. Design B보드에는 4분면 디자인 구조로, 더 많은 양의 솔더 페이스트를 침전시킨다.
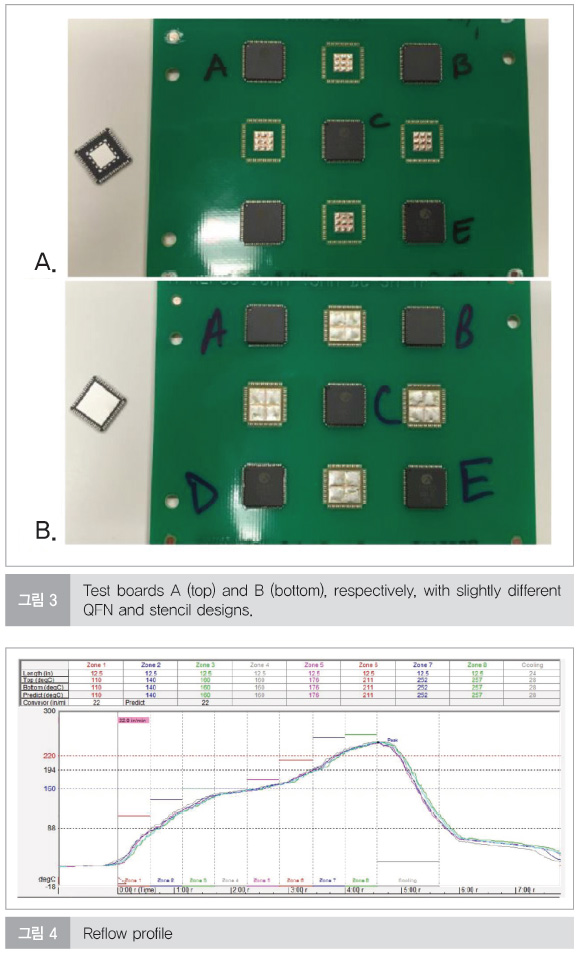
이들 보드 디자인은 동일한 보드 제조업체에 4가지 표면 마감처리(immersion silver(Ag), immersion tin(Sn), 기존의 OSP(organic solderability preservative), ENIG(electro-less nickel immersion gold))한 제품으로 주문 제작하였다. 여러 번의 리플로우 이후 산화의 영향을 테스트하기 위해 프린팅 및 부품 실장 전에 2번의 리플로우를 가해서 산화시켰다. 그림 4의 프로파일을 적용하였다.
본 연구를 위해서 3개의 합금을 테스트하였다. ‘SAC305’, 자동차 업종에 맞춰 개선한 2개의 SnAgCu 합금계열인 Auto Alloy 1 ‘90.95Sn3.8Ag0.7Cu3Bi1.4Sb0.15Ni’와 니켈이 없는 Auto Alloy 2 ‘90.95Sn3.8Ag0.7Cu3Bi1.4Sb’의 제품을 사용하였다. 3개의 합금 모두 동일한 ROL0 무세척 할로겐-프리 플럭스 테스트 보드(페이스트 A)을 사용하여 솔더 페이스트 형태로 테스트하였다.
Auto Alloy 1의 페이스트 A는 또한 페이스트 에이징(paste aging)의 영향을 평가하기 위해 1년 동안 냉장 보관하였는데, 그 시작과 끝 시점에서 테스트하였다. 보이드 성능에 대한 플럭스 시료의 잠재적 영향을 조사하기 위해 Auto Alloy 1 합금 기반의 2개의 서로 다른 페이스트로 테스트했다(ROL1 무세척 솔더 페이스트와 보이드 감소용으로 설계된 ROL0 솔더 페이스트). 243℃의 피크 온도와 약 60초의 액상 유지 리플로우 프로파일을 모든 보드에 동일하게 사용하였다. 그림 4의 프로파일을 적용하였다.
결과 및 논의
X-선 분석을 통해 모든 부품의 전체 보이드 비율과 최대 보이드 비율을 측정하였다. 범주별로 모든 포인트의 분산을 보여주는 일반적인 변동성 차트를 활용하여 분석 결과를 표시하였다. 종종 다이아몬드 플롯과 같은 평균 및 분포의 표현을 추가하였다. Quantile 바와 그룹 평균도 평균과 비교하는데 도움이 되었다.
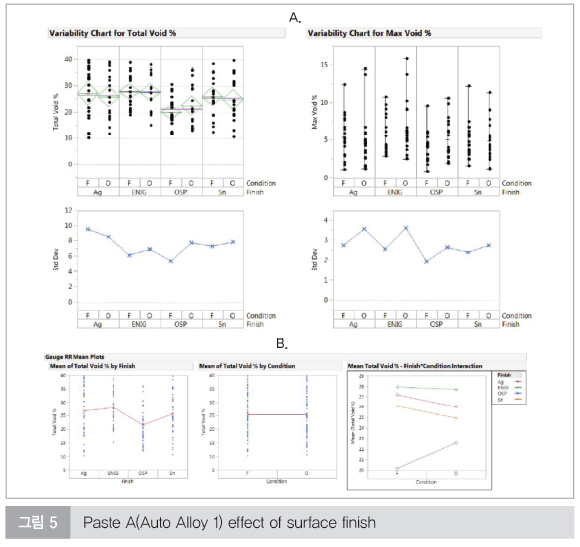
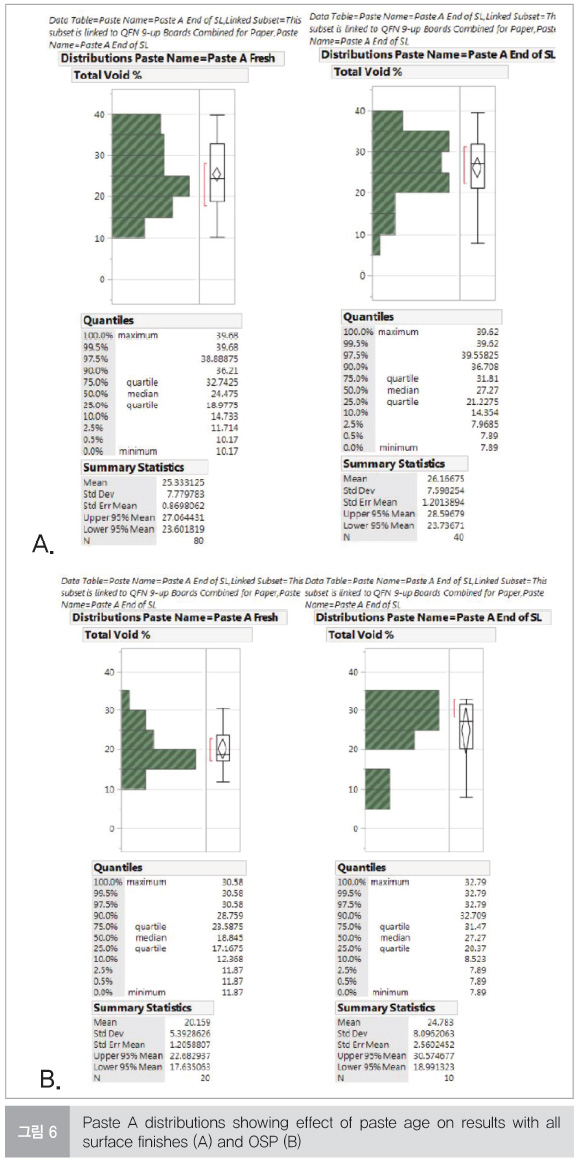
먼저, 보드의 표면 마감처리에 대한 효과를 고려하였다. 새로운 합금 조건과 산화 조건을 포함한 모든 표면 마감재에 관한 Auto Alloy 1 페이스트 A의 결과를 그림 5에 나타냈다. 모든 보이드 비율에서는 10% 미만의 표준 편차를 보였고, 새로운 조건(F)와 산화 조건(O) 간의 아주 작은 차이가 존재했음을 확인했다. 표면 마감재 간의 차이는 작았으며, 전체 데이터 세트의 평균의 차이가 5% 미만이었다. 최대 보이드 %에 대한 결과에서는 하나의 큰 보이드가 존재하는 특이치를 관찰하였다. 가장 높은 데이터 포인트는 하나의 표면 마감재에서 특출하게 나타나지 않았다. 이는 부품 마감 혹은 청결과 같은 다른 특성의 변화도 영향을 줄 수 있음을 의미한다.
그림 5의 (a) 데이터를 요약한 그림 5의 (b)에서는 OSP 마감이 가장 낮은 평균 보이드 비율을 보이고 있음을 명확하게 나타내고 있다. 또한 2번의 리플로우 사이클을 거쳐 이미 산화된 보드와 신규 보드 간의 차이가 거의 적었음을 확인하였다.
테스트 보드를 1년 동안 냉장 보관된 솔더 페이스트로 어셈블리하였다. 그림 6에 표시된 분포는 약간 달랐다. 보관 수명이 다한 페이스트는 평균과 변형이 약간 높았지만, 이 데이터 세트에서 가장 낮은 보이드의 부품도 일부 있었다. 여기에서의 변형은 두 개의 QFN 보이드 데이터 세트 사이에서 보이는 변형과 유사하게 보였다.
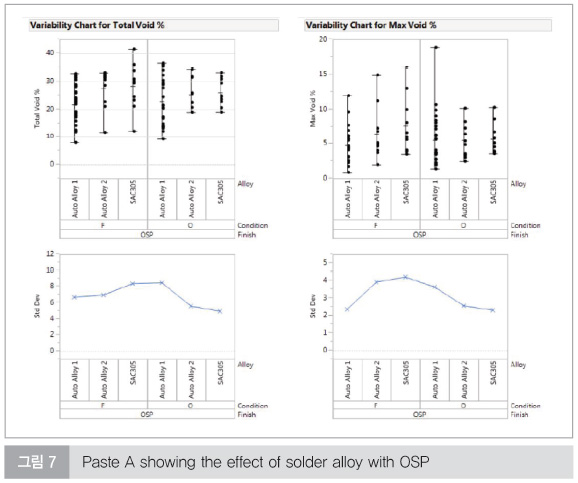
다음으로, 솔더 합금의 효과를 고려해 보았다. 3개의 페이스트는 모두 동일한 금속 비중으로 페이스트 A 플럭스 시료와 Type 4 파우더를 함유하고 있다. 그림 7에서는 또한 새로운 보드와 산화된 보드의 차이가 거의 없고 평균의 차이도 거의 없음을 보여주고 있다. Auto Alloy 1의 데이터 세트에는 추가 보드가 어셈블리되었기 때문에 더 많은 데이터 포인트가 있음을 유념해야 한다.
보이드에 있어서 상이한 플럭스의 영향을 조사하기 위해, 동일한 점도를 유지하도록 각기 다른 금속 비중에 3개의 다른 플럭스 시료들을 Auto Alloy 1과 Type 4 파우더로 혼합하였다. 그림 8의 평균 결과에서는 실험 ROL0 페이스트 C(오렌지색 상단 그래프로 표시)의 경우, 보이드 경향이 약간 낮았고, ROL1 페이스트 B의 경우에 약간 더 많은 변화를 보였다. 보드 표면 마감처리와 관련된 추세는 다른 페이스트 플럭스로 해석되는 것처럼 보인다.
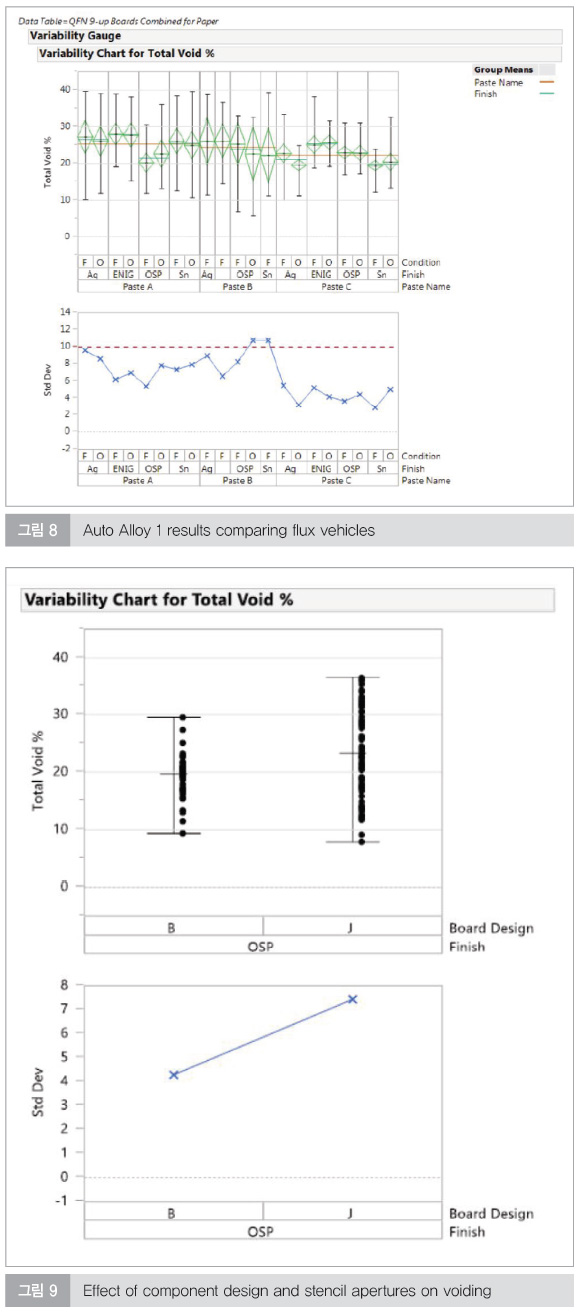
마지막으로, 그림 9와 같이 부품 설계의 영향을 고려하였다. J형 부품용 스텐실 설계는 솔더 조인트의 솔더 체적이 줄어든다. 이러한 솔더 체적의 부족은 보이드 비율을 높이고, 부품 하부의 기하학적 갭을 채우기에 충분한 솔더 체적이 없기 때문에 불충분한 스탠드오프 높이에 기여하는 것으로 나타났다.
결론
본 연구는 보이드에 관한 여러 가지 요인, 즉 테스트 보드 표면 마감, 보드 산화, 솔더 합금 선택, 페이스트 플럭스, 페이스트 에이징 및 부품 설계/스텐실 패턴의 영향을 조사하기 위해 시작되었다. 이들 각 요인은 전체 평균 보이드 비율에서 약간의 차이를 보였지만 모든 차이는 데이터 세트 내의 변동과 비교해 매우 작았다. 보이드 값은 다른 테스트 보드의 이들 솔더 재료에 대한 20% 미만의 일반적인 값과 비교하여 높았다. 이는 테스트 보드 디자인을 개선하여 전체 보이드 비율을 낮출 수 있음을 의미한다. 비교를 위해, 이들 테스트 보드를 사용하여 재료 및 공정 변화가 최악의 디자인에 미치는 영향을 보여주었다.
어떠한 표면 마감처리 혹은 어떠한 합금이 가장 성능이 좋을지에 대한 가설은 세우지 않았다. OSP 마감은 신선 또는 산화 여부와 관계없이 낮은 보이드 결과를 일관되게 보여주었고, 일반적으로 최고의 산화 억제제로 간주되는 ENIG는 높은 보이드 결과를 나타냈다. 보드 표면 마감처리의 추세는 표면 마감처리 만의 특성보다 적용된 상태에 기인할 수도 있다.
솔더 재료 비교는 개량된 플럭스가 전체 보이드 비율에서 약간의 개선을 보였지만, 합금은 더 적은 효과를 나타냈다. 보관 수명이 지난 노화된 솔더 페이스트는 평균 보이드 비율이 약간 더 높았지만 정상적인 변화로 여기는 범위 내였다. 이는 플럭스 시료에 따라 변경될 수 있지만 페이스트 노화가 보이드 발생에 거의 영향을 미치지 않는다는 확신을 높게 만들기에 충분했다.