적용 솔더페이스트, 파우더 크기가 보이드 형성에 큰 영향 끼쳐
솔더페이스트별 최적의 프로파일 적용도 고려해야
몇 가지 새로운 변수와 보이드에 미치는 영향을 조사하였다. 무세척 무연 솔더페이스트를 테스트해 수용성 무연 솔더페이스트와 결과를 비교하였다. 수용성 솔더페이스트는 무세척 제품보다 보이드를 발생하는 경향이 더 큰 것으로 나타났다. 수용성 솔더페이스트에 휘발성분 함량이 상대적으로 높게 함유되어 있고, 아울러 수용성 솔더페이스트 특유의 흡습성 때문이다. 솔더 파우더의 입자 크기에 대한 영향을 조사하였다; IPC 기준 Type 3, Type 4, Type 5 파우더를 사용하였다. 솔더 파우더의 산화물 함량은 파우더 크기가 줄어듦에 따라 늘어났으며, 더 많은 산화물 함량은 더 높은 보이드 비율을 생성하는 경향이 있다.
요약
솔더 조인트의 보이드는 많은 전기전자 제조업체들을 괴롭히고 있다. ‘보이드 충진’을 실현할 수 있는 훌륭한 방법들이 존재한다. 본고는 보이드와 관련해 수용성 무연 솔더페이스트, 다양한 스텐실 설계 및 리플로우 프로파일과 같은 변수를 연구해 왔던 이전 연구물에 연장선에 있다. QFN(Quad Flat No-Lead) 부품 열 패드를 테스트 시료로 사용하였다. 보이드 결과를 요약하고 보이드 감소에 대한 권장 사항을 제시하였다.
이번 연구에서는 몇 가지 새로운 변수와 보이드에 미치는 영향을 조사하였다. 무세척 무연 솔더페이스트를 테스트해 수용성 무연 솔더페이스트와 결과를 비교하였다. 수용성 솔더페이스트는 무세척 제품보다 보이드를 발생하는 경향이 더 큰 것으로 나타났다. 수용성 솔더페이스트에 휘발성분 함량이 상대적으로 높게 함유되어 있고, 아울러 수용성 솔더페이스트 특유의 흡습성 때문이다. 솔더 파우더의 입자 크기에 대한 영향을 조사하였다; IPC 기준 Type 3, Type 4, Type 5 파우더를 사용하였다. 솔더 파우더의 산화물 함량은 파우더 크기가 줄어듦에 따라 늘어났으며, 더 많은 산화물 함량은 더 높은 보이드 비율을 생성하는 경향이 있다.
서로 다른 솔더 파우더 제조업체들과 관련해서도 연구하였다. 한 제조업체의 솔더 파우더는 다른 제조업체보다 높은 보이드를 유발하기도 했다. 마지막으로, 진공 없는 증기상 리플로우와 비교해 대류 리플로우가 끼치는 영향을 조사하였다. 대류 리플로우는 일반적으로 사용되고 있으며, 해당 타입의 리플로우에 의한 보이드 생성 결과들은 많이 문서화되어 있다. 증기상 리플로우는 보이드를 감소시키는 경향이 있는 무-산소 환경에서 수행하였다. 증기상 시스템은 또한 장비가 밀봉되고 증기가 꽉 차기 때문에 진공 사용에 적합하다. 진공을 적용하면 갇힌 가스의 탈출을 촉진하는 액상 단계 도중에 보이드와 주변 대기 사이에서 차압이 생성된다. 솔더 조인트 외부의 가스 압력을 낮추면 보이드를 낮추는 데 도움이 된다.
보이드가 존재하는 솔더 조인트를 재작업하는 일은 쉽지 않은 작업이다. 일반적으로 해당 부품의 보이드를 줄일 수 있다는 희망을 품고 부품을 제거하고 재-솔더링하는 공정이 수행되고 있다. 매우 노동 집약적인 프로세스로, 주변 부품에 열적 스트레스를 줄 수 있다. 보이드가 있는 솔더 조인트의 재작업과 관련해 진공이 포함된 증기상 리플로우 시스템의 사용 가능성을 조사하였다.
대부분 보이드 완화 전략의 조합이 적용된 경우에만 보이드를 낮출 수 있다. 솔더페이스트, 스텐실 디자인, 리플로우 프로파일 및 적용 리플로우 유형 등의 조합에 관한 권장 사항을 제공한다. 본고의 목적은 독자들이 ‘보이드 충진’을 성공적으로 실현할 수 있도록 도움을 주는 것이다.
서문
전자 제조업체에게 있어서 솔더 조인트 내의 보이드는 아직 해결되지 않은 문제이다. QFN(Quad Flat No-Lead) 유형과 같은 하부 단자형 디바이스 혹은 ‘no-lead’형 디바이스가 일반화되고 있다. 이러한 유형의 디바이스는 낮은 스탠드오프 높이와 패드에 도포되는 비교적 대량의 솔더페이스트로 인해 보이드에 취약하다. QFN 열 패드 솔더 조인트는 특히 보이드에 취약하며, 보이드 연구에 훌륭한 테스트 시료가 된다.
본고는 이전의 보이드 연구에 대한 연속성 상에 있다.[1] 이전 연구에서 보이드에 영향을 미치는 다양한 파라미터들을 요약하였다. 2개의 수용성 무연 솔더페이스트를 비교해 보았다. 이들 솔더페이스트에서 확연하게 다른 보이드 수준이 나타났다. QFN 열 패드의 스텐실 디자인을 다양하게 하였고, 보이드 수준의 차이를 관찰하였다. 2개의 서로 다른 대류 리플로우 프로파일인 RTS(ramp-to-spike)와 고온 RTS(RTS-HT, higher temperature ramp-to-spike)를 사용하였다. 보이드의 차이를 확인할 수 있었으며, 이러한 차이는 사용된 솔더페이스트에 따라 달라졌다. 가장 큰 보이드의 크기 또한 변수와 관련하여 분석하였다. 이러한 모든 변수에 대한 보이드 수준은 통계 분석 기법을 활용하여 비교 및 대조하였다.
보이드 축소 방법을 알아보는 본 조사에는 훨씬 확장된 변수 세트를 포함하였다. 이들 변수가 보이드에 끼치는 영향과 관련해 테스트하였고, 적용된 변수들은 다음과 같다.
▶ 수용성 무연 솔더페이스트 : A, B, E
▶ 무세척 무연 솔더페이스트 : C, D
▶ 솔더 파우더 크기 : IPC 기준 Type 3 / 4 / 5
▶ 솔더 파우더 제조업체 : I 및 G
▶ 스텐실 디자인 : 십자 방격 (U9), 45도 회전한 십자 방격 (U10), 5-도트 (U11), 대각선 줄무늬 (U12)
▶ 회로기판 표면마감 : ENIG, OSP
▶ 대류 리플로우 프로파일 : RTS, RTS-HT, RTS(2회), RSS(ramp soak spike), RTS-N2(질소)
▶ 증기상 리플로우의 진공 유무 : VP, VP-V1, VP-V2, VP-V3
▶ 현존 보이드의 재작업 방법으로써 진공 증기상 리플로우 활용
대부분의 경우에, 이들 변수는 실험의 매트릭스 유형 설계가 아닌 선형 방식으로 변경시켰다. 예를 들어, 보이드 관련 솔더 파우더 크기의 영향을 연구하기 위해, 하나의 솔더페이스트 플럭스에 3개의 솔더 파우더 크기 모두를 적용하였다. 반면 다른 모든 변수는 일정하게 유지하였다. 3개의 솔더 파우더 모두에 관한 보이드 결과를 서로 비교했다.
보이드 데이터의 분석은 통계 분석 기술을 사용하여 수행하였다. 박스 및 휘스커 플롯을 사용하여 데이터 밀집도를 표시하였다. Tukey-Kramer HSD(honest significant difference) 테스트를 사용하여 데이터 세트가 크게 다른지를 확인했다. 각 변수 세트에 대한 결론을 도출하였으며, 이 결론을 토대로 ‘보이드 충진’을 돕기 위한 일련의 권장 사항을 작성하였다.
방법론
재료
본 실험에 사용된 회로 보드는 그림 1과 같다. 이 회로기판은 FR4 재료, 에칭 구리 패드 및 ENIG 표면 마감재로 제작되었다. ENIG와 비교하기 위해 OSP 처리된 제품을 실험에 수행하기도 했다.
QFN 열 패드(U9, U10, U11, U12)를 보이드 측정을 위해 사용하였다. 적용된 QFN은 0.5mm 피치, 10mm 몸체 크기 그리고 주석 마감처리된 더미 부품으로, 68개의 주변 리드가 존재한 디바이스이다(그림 2 참조).
스텐실 디자인은 각 QFN 열 패드 위치에 따라 다르게 하였다(그림 3 참조). 각각의 경우에 솔더페이스트 커버리지는 열 패드 면적의 약 65%였다.
보이드와 관련하여 스텐실 디자인의 영향은 이전 연구에서 논의하였다.[1] 이전 논문의 데이터는 참고용으로 본고에 요약되어 있다.
사용된 솔더페이스트는 표 1과 같이 다양하게 적용했다. 주석 (Sn) / 은 (Ag) 3.0 % / 구리 (Cu) 0.5 % (SAC305) 합금을 항상 사용하였다.
대류 리플로우 프로파일
본 실험에서는 여러 가지 리플로우 프로파일을 사용하였다. 첫 번째 논문[1]에 사용된 리플로우 프로파일은 여기에 참고용으로 표시하였다(그림 4 참조). 이들 프로파일은 모두 선형 램프 유형이었다. 하나는 RTS이고 다른 하나는 피크 온도가 높고 리플로우 시간이 더 긴 RTS-HT이었다.
RSS 프로파일은 150 ~ 180℃의 소크 시간을 추가하여 생성하였다(그림 5 참조).
각 프로파일의 파라미터는 표 2에 요약되어 있다. 질소 분위기 상에서 수행한 하나의 실험을 제외하고 모두 대기 상 리플로우를 적용하였다.
증기상 리플로우
최첨단 기술이 내포되어 있는 증기상 솔더링 시스템은 낮은 피크 온도(최대 230℃ 무연) 및 zero ΔT와 함께 무-산소 분위기에서 온도 구배(勾配) 제어(temperature gradient control) 기능을 제공한다. 증기상 리플로우 시스템은 응축 공정을 거쳐서 솔더 조인트로 열을 전달하는 회로 기판 표면 상에 응축된 가열 유체(PFPE, perfluoropolyether(과불소 폴리에테르))를 사용한다. 액체에서 수증기 / 증기로의 잠재열 전이는 상태의 변화를 초래하지만 온도 변화는 없다. 증기상 솔더 시스템에서 특정 회로에 도달할 수 있는 절대 최대 온도는 물리적 상수인 유체의 비점에 의해 결정된다. 따라서, 회로 기판의 온도 구배는 대류 리플로우 시스템에 비해 매우 작으며, 피크 온도는 사용된 솔더 합금의 리플로우 온도에 매우 근접하게 유지될 수 있다.
증기상 시스템은 공정 안정성과 반복성이 표준 대류 시스템을 능가한다. 외부 열원을 사용하는 오늘날의 증기상 솔더링 시스템은 확실한 열 프로파일링 기능과 함께 유연한 온도 구배 제어 기능을 갖추고 있다. 모든 예열 및 프로파일링은 단일 밀폐 공정 챔버에서 수행된다. 온도 구배 제어는 장비 설계를 간단하게 하고, 무-산소 환경에서 공정을 훨씬 단순하게 만든다(그림 6 참조).
공정에서 완전하게 산소를 제거한다는 것은 솔더 조인트로 불로우 다운되는 가열 공기의 후속 문제를 걱정할 필요 없이 플럭스 화학 물질을 이상적인 환경에서 동작시키는 게 가능하다는 점을 의미한다. 표준 대류 리플로우(그림 7 참조)에서 가열된 공기의 산소는 솔더를 지속적으로 산화시키고, 플럭스 매체는 제 위치에서 솔더링하기 위해 산화물을 제거해야 한다.
이론적으로 금속 산화물은 보이드 형성 수준에 관여한다. 리플로우 대기 상에서 산소를 제거하면 보이드가 감소될 수 있다. 무-산소 환경에서 플럭스 활성화 및 효율이 개선된다. 궁극적으로 플럭스 잔류물 및 활성 레벨을 최소화하기 위해 페이스트 조성물을 재가공해야 할 필요성이 있다고 본다. 본 실험에 사용된 증기상 장비는 그림 8과 같다. 사용된 모델에는 진공 기능이 내포되어 있다.
이 장비에는 무(無) 진공, prevac(사전 진공) 1, prevac(사전 진공) 2 그리고 메인 진공의 네 가지 진공 옵션이 있다. 이러한 옵션은 개별적으로 또는 서로 조합하여 사용할 수 있다. Prevac 1 단계에서는 솔더페이스트에서 공기를 제거하기 위해 가열하기 전에 솔더페이스트 침전물을 진공 상태로 만든다. Prevac 2 단계에서는 솔더가 녹기 전에 램프업 가열 동안 솔더페이스트에서 진공을 끌어낸다. 메인 진공 단계에서는 포집된 가스를 제거하기 위해 용융 솔더 침전물에서 진공을 끌어낸다. 메인 진공 사이클은 약 5초씩 연속적인 2번의 단계의 경우에 75kPa(750mbar) 압력으로 낮췄다(그림 9 참조).
메인 진공을 사용할 때 프로파일에 추가되는 총 시간은 약 15초이다. 이러한 진공 사이클의 여러 조합을 이번 테스트에 사용하였으며, 각 조합은 코드별로 재명명하였다. 코드와 진공 조합은 다음과 같다. VP = 진공 없는 증기상 리플로우, VP-V1 = 메인 진공만, VP-V2 = 사전 진공 1 + 메인 진공, VP-V3 = 사전 진공 1 및 사전 진공 2 + 메인 진공.
증기상 리플로우 프로파일은 그림 10에 표시하였다. 적용된 프로파일은 램프-소크-스파이크(RSS, ramp-soak-spike) 유형이었다.
130℃ ~ 145℃의 소크 시간은 약 80초로 하였다. 리플로우 시간(> 221℃)은 약 70초이다. 피크 온도는 230℃이다. 이 프로파일은 일반적인 증기상 프로파일이며 RSS 대류 프로파일과는 다르다.
실험 절차 및 통계 분석
각 변수에 있어서 대부분의 경우 20개의 회로 보드로 실행했지만, 경우에 따라서는 30개의 보드로 실시했다. 회로 보드 당 4개를 측정하여 각 QFN 열 패드에 대한 보이드 면적을 분석하였다. 각 실험 변수에 대한 총 측정 수는 80개 또는 일부의 경우 120개이었다. 통계적으로 의미 있는 데이터를 생성하기 위해 수행하였다.
Tukey Kramer HSD(Tukey Kramer honest significant difference) 테스트는 데이터를 비교하고 대조하기 위해 데이터 세트로 수행하였다. Tukey Kramer HSD 분석은 여러 데이터 세트가 상당히 다른지 아니면 통계적으로 비슷한지를 결정한다. 이 테스트는 평균을 비교하는 데 사용되는 Student`s t-test와 비슷하다. Tukey Kramer HSD 테스트의 결과는 데이터 세트, 여러 데이터 계산 및 보고서를 보여주고 있다(그림 11 참조).
Tukey Kramer HSD 분석의 상단에는 데이터 세트를 나타내는 산점도(scatter plot)와 원을 표시하였다. 원이 겹쳐진다면 데이터 세트가 크게 다르지 않다는 의미이고, 원이 겹치지 않으면 데이터 세트는 아주 다르다는 뜻이다. Tukey Kramer HSD 분석의 중심 부분에는 다양한 데이터 계산이 포함되어 있다. 이 테스트의 신뢰 수준은 95%이므로 데이터 세트가 통계적으로 유사하거나 아니면 다른지를 95% 확신할 수 있다. Tukey Kramer HSD 분석의 맨 아래 부분에는 연관된 문자 코드들을 보여주고 있다. 문자 코드는 맨 위에서 가장 높은 평균 순서로 데이터 세트에 지정하였다. 문자 코드가 비슷하면 데이터 세트가 크게 다르지 않지만, 다르다면 데이터 세트가 크게 차이난다는 의미이다. 경우에 따라 데이터 세트에 여러 문자 코드를 지정하였다. 이는 데이터 세트가 여러 다른 데이터 세트와 통계적으로 유사함을 나타냈다. 예를 들어, 그림 11에서 ‘Paste B WS SAC T3’은 문자 코드가 A이고 ‘Paste A WS SAC T3’은 문자 코드가 B이다. 이는 2개의 솔더페이스트가 상당히 다른 보이드가 생성되었음을 의미한다. 이 예를 통해서 Paste B는 Paste A보다 높은 보이드를 생성했음을 알 수 있었다.
결과 및 논의
보이드 조사 결과는 하부에서 변수별로 세분화하여 설명했다. 각 비교 결과는 하부의 각 섹션에서 설명한다.
솔더페이스트가 보이드에 미치는 영향
솔더페이스트 플럭스는 보이드 형성에 큰 영향을 끼친다. 일부 솔더페이스트는 낮은 수준의 보이드를 생성하는 경향이 있었고, 다른 솔더페이스트는 보이드 비중이 높은 경향이 있었다. RTS 프로파일, SAC305 Type 3 솔더 파우더 그리고 솔더페이스트에 의한 보이드 형성은 그림 12에서 보여주고 있다.
수용성 솔더페이스트 A는 다른 수용성 솔더페이스트 B와 E보다 보이드가 적었다. 솔더페이스트 B와 E의 보이드 형성 수준은 평균치와 비슷했지만 페이스트 E의 형성 범위는 페이스트 B보다 훨씬 좁았다. 무세척 솔더페이스트 C와 D 모두는 모든 수용성 솔더페이스트보다 훨씬 적었다. 그림 13의 Tukey Kramer HSD 분석에서는 이러한 데이터 세트의 통계적 비교를 보여주고 있다.
솔더페이스트 A, D 그리고 C의 보이드는 솔더페이스트 B 및 E 둘 다에 비해 상당히 적었다. 솔더페이스트 A, D 및 C의 보이드 수준은 서로 비슷했다. 솔더페이스트 B와 E의 보이드는 서로 유사했다.
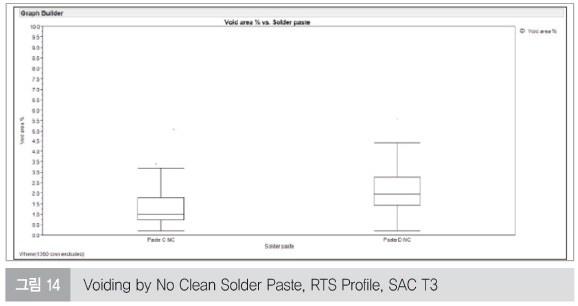
무세척 솔더페이스트의 보이드 수준은 수용성 솔더페이스트보다 훨씬 적었다. 이들 무세척 솔더페이스트의 차이를 나타내기 위해 보이드 영역 y 축을 0~10% 단위로 변경하여 표시했다(그림 14 참조).
Tukey Kramer 분석에 따르면, 솔더페이스트 D의 보이드 수준은 솔더페이스트 C보다 훨씬 높았다(그림 15 참조).
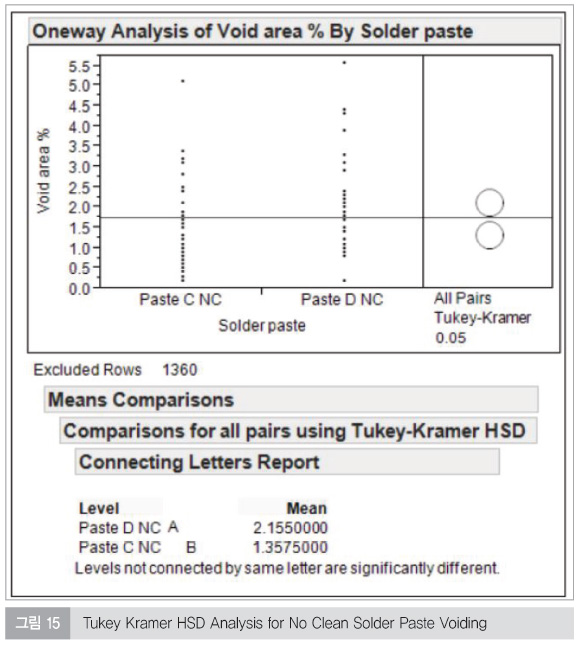
솔더 파우더 크기와 제조업체가 보이드에 미치는 영향
솔더페이스트 B는 IPC 기준 Type 3, 4 및 5의 세 가지 솔더 파우더 크기를 적용하여 제조되었다. RTS 프로파일을 거친 3개의 솔더페이스트의 보이드 수준을 그림 16에서 보여주고 있다.
솔더 파우더 크기가 줄어듦에 따라 보이드 수준이 낮아졌다(T3 > T4 > T5). 그림 17의 Tukey Kramer 분석에서는 이러한 보이드 결과가 크게 다르다는 것을 보여주고 있다.
이것은 예상과는 다른 결과였다. 솔더 파우더의 총 산화물 수준은 솔더 파우더의 해당 질량에 있어서 파우더 크기가 작아짐에 따라 늘어난다. 파우더 크기가 감소함에 따라 표면적이 증가하기 때문이다. 금속 산화물이 보이드 형성에 기여하는 것으로 생각되므로 이론적으로 Type 4 및 Type 5 솔더 파우더는 Type 3 솔더 파우더보다 높은 보이드를 생성해야 한다. 이러한 현상을 설명하기 위해서는 추가 조사가 필요하다.
솔더페이스트 B를 제조하기 위해 서로 다른 두 제조업체(I 및 G)에서는 SAC305 Type 3 솔더 파우더를 사용하였다. RTS 프로파일을 사용하였으며, 보이드 결과는 그림 18과 같다.
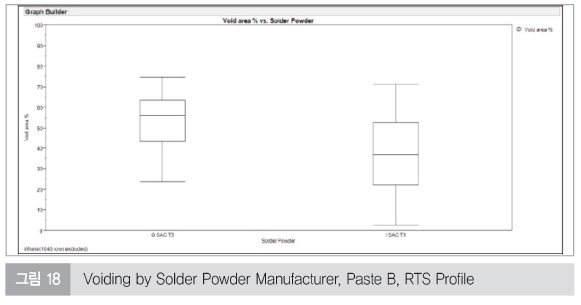
솔더 파우더 제조업체 I 제품의 보이드는 제조업체 G보다 적었지만, 보이드 생성 범위는 더 넓었다. 이러한 결과는 Tukey Kramer 분석에 의해 나타내는 바와 같이 통계적으로 의미가 있다(그림 19 참조).
제조업체마다 솔더 파우더 제조에 약간 다른 공정을 적용할 수도 있다. 결과적으로 약간 다른 파우더 모양과 파우더 크기 분포를 가지고 있으며, 잠재적으로 다른 산화물 수준이 생겨서 보이드에 영향을 끼친다.
스텐실 디자인 보이드에 미치는 영향
시험된 4개의 스텐실 디자인에서는 약간 차이나는 보이드를 보여주고 있다. 이전 연구의 결과[1]가 그림 20에 요약되어 있다.
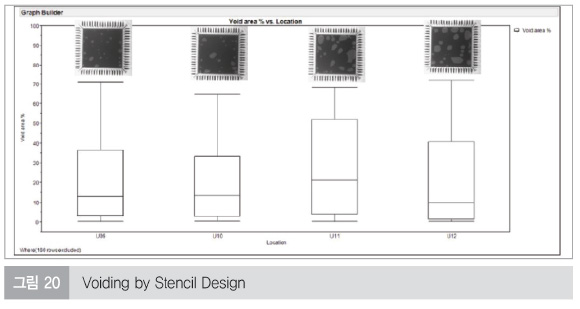
5-도트 스텐실 패턴(U11)이 다른 디자인보다 더 높은 중앙 보이드 현상을 보였다. Tukey Kramer 분석에서 이 결과를 검증하였다(그림 21 참조).
5-도트 패턴(U11)에서의 보이드 현상은 사용된 다른 스텐실 디자인보다 훨씬 높게 나타났다. 다른 스텐실 디자인은 통계적으로 모두 유사한 보이드 수준을 보였다.
표면마감재가 보이드에 미치는 영향
OSP 표면마감재를 평가한 하나의 실험을 제외하고 ENIG 표면마감재를 기본으로 선택하였다. 표면처리된 보드에 Type 3 솔더 파우더의 SAC305와 함께 및 RTS 프로파일을 적용하여 솔더페이스트 B를 실험하였다. 보이드 수준은 그림 22에 나타냈다.
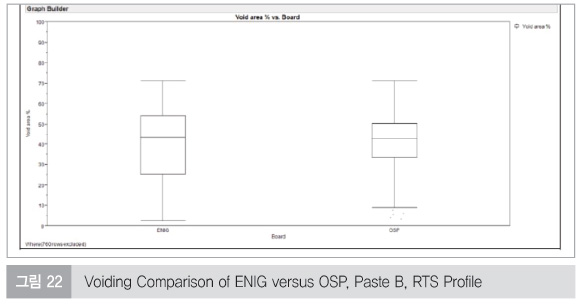
이 경우 ENIG와 OSP 표면마감재의 보이드 수준에서는 거의 차이가 없었다. Tukey Kramer 분석에서 이러한 데이터 세트가 크게 다르지 않은지를 확인하였다(그림 23 참조).
이 결과는 예상치 못했다. OSP는 다른 표면마감재보다 높은 보이드를 생성한다고 사료된다. OSP는 리플로우 조건에서 가스를 배출할 수 있는 비교적 두꺼운 유기층으로 구성된다. OSP는 또한 보이드를 유발할 수 있는 솔더의 습식 제한 확산을 어렵게 한다. 솔더페이스트 B는 ENIG 표면마감에서 우수한 습윤을 보였지만 OSP 표면에서 적당한 습윤을 보이는 것으로 알려져 있으나, 이는 보이드 결과에 영향을 끼치지 않는 것으로 보인다. 표면마감재가 보이드에 미치는 영향을 확인하려면 추가 조사가 필요하다.
대류 리플로우 프로파일이 보이드에 끼치는 영향
Type 3 솔더 파우더가 포함된 SAC305의 솔더페이스트 B를 모든 대류 리플로우 프로파일에서 실행하였다. 질소 분위기(RTS-N2)를 사용한 마지막 변동을 제외하고 모든 경우 대류 상에서 리플로우를 수행하였다. 테스트 된 프로파일 변동은 다음과 같다. ▶ RSS(ramp-soak-spike), ▶ RTS(ramp-to-spike), ▶ RTS-2(양면 리플로우, RPS-HT 고온을 시연하기 위한 2번의 RTS 프로파일 수행) 그리고 및 질소 분위기의 RTS-N2(순도 99%). 이들 실험의 결과는 그림 24에 나타냈다.
RSS 프로파일은 RTS 프로파일보다 약간 많은 보이드를 생성했지만 RTS-2 및 RTS-HT 프로파일과는 유사한 수준의 보이드를 생성했다. 질소 분위기를 사용한 RTS-N2 프로파일은 매우 낮은 보이드를 생성했다. 이 결과는 통계적으로 매우 의미가 있다(그림 25 참조).
RTS 프로파일과 비교하여 RSS 프로파일을 사용할 때 솔더페이스트 B의 보이드 수준이 현저히 증가했다. 양면 리플로우를 시연하기 위해 RTS 프로파일을 두 번째로 실행하였어도 보이드가 많이 늘어나지 않았다. 질소 분위기의 사용은 솔더페이스트 B에 큰 이득을 주었으며, 보이드가 현저하게 줄어드는 효과를 보였다.
증기상 리플로우가 보이드에 미치는 영향
여러 Type 3 솔더 파우더의 SAC305(A, B 및 C)를 증기상 리플로우로 수행하였다. 진공 옵션(VP-V1, VP-V2, VP-V3)을 사용하거나 혹은 사용하지 않고 증기상 리플로우를 실행했다. 이들 결과는 비교하기 쉽게 표시된 RTS 대류 보이드와 함께 그림 26에 표시하였다.
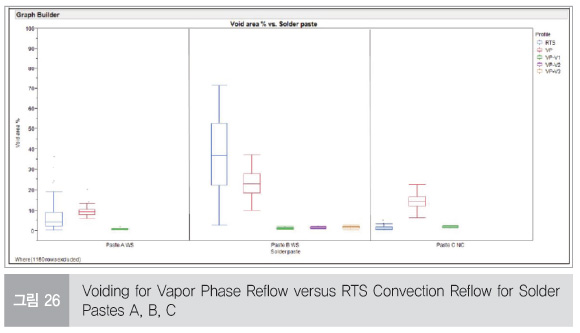
Tukey Kramer HSD 분석에서는 보이드 수준에서 몇 가지 중요한 차이를 보여주고 있다(그림 27 참조).
솔더페이스트 A는 RTS 대류 리플로우에 비해 진공이 없는 증기상 리플로우에서 더 높은 보이드를 보였다. 진공 옵션 V1은 솔더페이스트 A의 보이드를 크게 감소시켰다. 솔더페이스트 B는 진공 없이 증기상에서 수행되었을 때의 보이드 수준에 비해 RTS 대류 리플로우에서 매우 높은 보이드를 나타냈다. 세 가지 진공 옵션 V1, V2 또는 V3 중 하나를 추가하면 솔더페이스트 B의 보이드가 크게 줄어들었다. 솔더페이스트 C는 진공이 없는 증기상에서 높은 보이드를 나타냈다. 진공 옵션 V1을 추가하면 보이드가 RTS 대류 리플로우에서 볼 수 있는 것과 유사한 수준으로 감소했다.
리플로우 도중에 진공을 적용하면 보이드에 극적인 영향을 미치기 때문에 솔더페이스트의 기본적인 보이드 경향 및 기타 요인을 극복할 수 있다. 진공을 추가한 대류 리플로우는 진공 증기 상과 비슷한 결과를 나타내고 있다고 가정할 수 있다. 이 가정을 확인하려면 테스트를 수행해야 한다.
기존의 보이드를 재작업하기 위해 진공 상태의 증기상 리플로우로 수행하였다. Type 3 솔더 파우더의 SAC305인 솔더페이스트 B를 대류 RTS 프로파일로 먼저 리플로우하고 보이드를 측정하였다. 동일한 회로 기판을 진공 상태의 증기상 시스템에서 다시 리플로우하고 보이드를 측정하였다(그림 28 참조).
진공 상태의 증기상 시스템을 사용하여 보이드를 재작업할 때, 기존 보이드가 크게 줄어든 것으로 나타났다. Tukey Kramer 분석에서는 이 결과가 의미 있음을 보여주고 있다(그림 29 참조).
이 결과는 진공 증기상 시스템이 보이드 감소를 위한 재작업 방법으로 사용될 수 있음을 보여주고 있다. 보이드가 존재한 납땜 부품의 재작업이 어렵고, 자주 실패하고, 회로 기판에 열적 손상을 초래할 수 있기에 매우 흥미로운 결과라고 할 수 있다. 진공 증기상 재작업 공정이 솔더 조인트 품질 및 강도에 영향을 미치지 않도록 하기 위해 추가적인 연구가 수행될 필요가 있다.
"보이드 충진"을 위한 권장 사항들
본고에서 제시된 데이터를 바탕으로 몇 가지 권장 사항들을 설명할 수 있다.
▶ 공정에서 보이드 발생이 적은 솔더페이스트를 선택해야 한다.
▶ 더 작은 솔더 파우더(IPC 기준 Type 4 또는 Type 5)의 솔더페이스트를 사용하면 보이드를 줄일 수도 있다.
▶ 솔더페이스트를 프린트하는 스텐실을 보이드 최소화에 맞춰 디자인해야 한다. 가스 배출 경로를 사용하면 보이드 수준 에 영향을 줄 수 있다.
▶ 리플로우 프로파일을 사용하여 솔더페이스트의 보이드를 최소화해야 한다. 리플로우 프로파일은 각 솔더페이스트에 맞게 조정해야 한다.
▶ 보이드를 감소시킬 수 있으므로 질소 분위기의 대류 리플로 우 적용을 고려해야 한다.
▶ 보이드 감소를 위해 진공이 있는 리플로우 시스템을 사용해 야 한다. 진공은 솔더페이스트 또는 기타 요인과 관계없이 보이드를 크게 줄여준다.
▶ 진공 상태의 증기상 리플로우를 사용하여 보이드가 존재한 납땜 부품의 재작업을 수행할 수 있다.
결론
솔더 조인트의 보이드는 많은 요인에 의해 영향을 받는다. 솔더페이스트는 보이드에 큰 영향을 미친다. 일반적으로, 무세척 무연 솔더페이스트는 수용성 무연 솔더페이스트보다 보이드 비율이 낮다. 솔더 파우더 크기가 보이드에 영향을 끼치는 것으로 나타났다. 솔더 파우더 크기가 작아지면, 보이드가 줄어드는 경향이 있다. 서로 다른 솔더 파우더 제조업체의 공정 차이도 보이드에 영향을 미친다. 스텐실 디자인은 공극에 영향을 주지만 다른 요인과 비교하면, 영향력이 높지 않다. ENIG 및 OSP 표면마감재는 이번 평가에 사용된 솔더페이스트의 보이드 수준에 거의 영향을 미치지 않았다. 리플로우 프로파일은 보이드에 큰 영향을 끼치며, 리플로우 프로파일은 각 솔더페이스트에서 보이드를 최소화하도록 조정되어야 한다. Air 대류 리플로우와 비교해 질소 증기상 리플로우 및 대류 리플로우는 보이드를 줄여준다. 진공 상태에서 증기상 리플로우를 사용하면 보이드 수준이 매우 낮았다. 또한 진공을 이용한 증기상 리플로우는 납땜 부품에 존재하는 보이드의 재작업 및 감축이 가능해 사용될 수 있음을 보여주었다.
보이드에 영향을 미치는 요인 중 일부만 이번 연구에서 연구되었다. 수행해야 할 훨씬 더 많은 테스트가 남아 있다. 일반적으로 많이 사용되고 있는 하부 단자 부품 관련 보이드도 아직 해결해야 할 문제이다. 저자는 독자들이 ‘보이드 충진’에 도움을 주기 위해 보이드에 영향을 미치는 요소들을 지속적으로 연구할 것이다.