증착성 뛰어난 플럭스 선정 먼저
솔더링 체류 시간 늘리고, 국부 예열이 ‘필수적’
열적으로 까다로운 어셈블리에서 월등한 수직 홀 충진을 이뤄내기 위해 고려해야 할 많은 요소가 있다는 데이터를 도출하였다. 이러한 요소 중 가장 눈에 띄는 것은 플럭스 선택이다. 최적화 모델링은 플럭스 증착의 증가가 수직 홀 충진을 개선할 가능성도 있음을 보여주었다. 주효과도 분석을 통해 상면 보드 온도 증가와 솔더 모듈 적용 시간의 부정적인 영향을 확인할 수 있었다. 따라서 수직 홀 충진력을 높이려면 상면 보드 온도와 솔더 모듈 시간을 최소화해야 한다. 최적화 모델링에서 결과를 찾을 수 있다. 늘어난 체류 시간과 국부적인 예열은 고열량 어셈블리 솔더링에 있어서 실행 가능한 옵션으로 여겨져야 한다.
개요
새롭고 혁신적인 제품을 만들기 위한 전자 산업계의 노력이 지속되고 있다. 경쟁력 있는 디자인 회사는 통합형 PCB 설계, 줄어든 물리적 크기 및 향상된 성능의 특성을 갖춘 어셈블리를 개발하게 되었다. 이러한 새로운 설계로 인해 전자 제품 제조업체는 많은 과제에 직면하게 되었다. 중요한 과제 중 하나는 두께가 20층을 초과하고 구리 질량 함량이 40온즈를 초과할 가능성이 있는 고열량 PCB에서 쓰루홀 부품을 처리하는 것이다. 혼합 기술의 사용, 부품 간격 감소, 무연 합금 적용과 함께한 고열량 PCB는 높은 수준의 반복성으로 까다로운 어셈블리가 가능한 고급 솔더링 장비를 선택하도록 이끌었다.
셀렉티브 솔더링 머신은 완전 자동화된 기계의 반복성과 수동 솔더링의 유연성을 결합한 기술로 매우 복잡한 PCB의 혼합 기술 부품에 쉽게 대응할 수 있다.
셀렉티브 솔더링 공정의 도입으로 PTH 처리와 관련된 많은 문제를 극복할 수 있는 귀중한 도구가 업계에 제공되었지만, 장비만으로는 고열량 PCB 솔더링 기능을 보장할 수 없다. 이러한 어려운 애플리케이션은 테크놀로지 및 공정 지식의 발달이 장비의 발전만큼 중요하다. 플럭스 적용, 예열 조합 그리고 오늘날의 셀렉티브 솔더링 기계에서 가용한 솔더링 기술과 함께한 실험적 설계를 통한 프로세스 개발을 가지고, 고열량 PCB의 탁월한 수직 홀 충진을 달성할 수 있다.
소개
구리 함량이 높은 PCB를 솔더링하는 문제는 전자 제조 산업계에서 새로운 것이 아니다. 그러나 지난 20년 동안 PCB가 더 복잡해지고 열적으로 더 까다로워지면서 이러한 문제에 직면하는 것이 점점 더 일반화되었다.
어셈블리 복잡성이 커질 때마다 충분한 수직 홀 충진을 달성하기 위한 프로세스 창이 더욱 좁아지고 유지 관리가 어려워진다. 결과적으로, 수직 홀 충진 100%을 이뤄냈던 4~8층 PCB의 안정적인 솔더링 프로세스 및 관행은 12층 이상의 PCB에 적용할 때 종종 50% 이하의 수율을 나타낸다. 이러한 과제를 해결하기 위해 전자 제조 업계의 많은 업체가 셀렉티브 솔더링으로 전환했다.
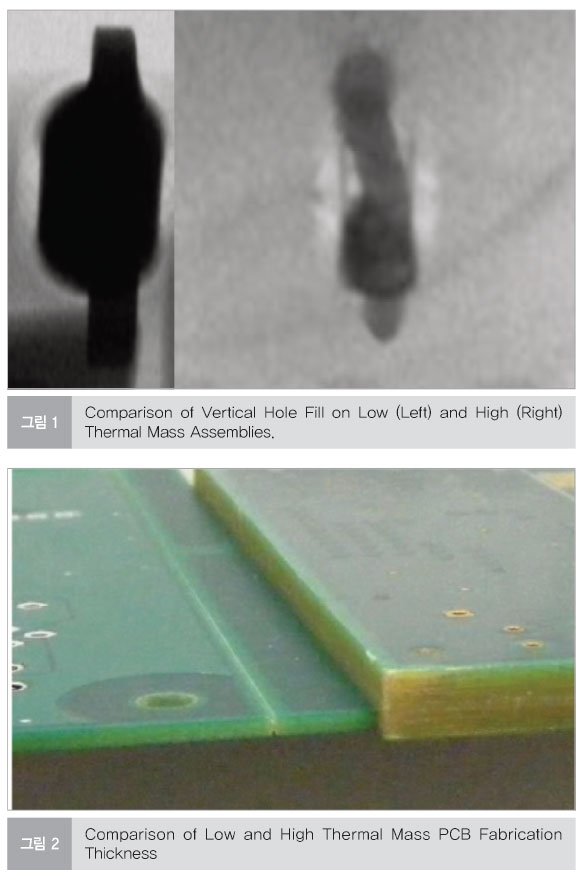
다수의 셀렉티브 솔더링 제조업체들은 전통적인 웨이브 머신보다 솔더링 프로세스의 모든 측면을 더 잘 제어할 수 있는 잠재력을 갖춘 장비를 제공하고 있다. 셀렉티브 솔더링 설비의 플럭스 전달 메커니즘에는 PTH의 각 리드에 원하는 양의 플럭스를 분사하는 기능이 있다.
이동식 갠트리 시스템의 솔더 포트와 노즐을 사용하면 솔더를 정확하게 위치하고 체류 시간(dwell time)을 맞춤화할 수 있다. 더 이상 선택적인 웨이브 팔레트가 필요하지 않은 셀렉티브 솔더는 열 질량을 크게 줄이고 더 균형 잡힌 예열을 가능하게 한다. 이러한 각 제어 기능은 잠재적으로 접근하기 어렵고 온도에 민감한 부품[1]의 선택적인 솔더링을 구현하는 데 도움을 준다. 고열량 어셈블리 솔더링에 있어서 매우 유용한 도구이다.
사용 중인 셀렉티브 솔더링 장비와 관계없이 각 기계 시스템의 특성화와 시스템 간의 상호 작용을 이해하는 것이 열적으로 까다로운 보드 프로세스를 개발할 때 중요하다. 본고에서는 고열량 어셈블리에 적용 가능한 셀렉티브 솔더링 머신의 시스템을 특성화 짓기 위한 실험 설계에 중점을 두었다. 본 실험의 결과는 이후 20층과 40온스 이상의 구리에서 열적으로 까다로운 PCB를 성공적으로 솔더링하는데 활용되었다.
열적으로 까다로운 PCB의 홀에 대한 리드 비율과 열전도율을 모방한 PCB를 실험 설계(DoE) 테스트용으로 개발하였다. 테스트 보드는 홀-리드 비율이 1.3, 1.4, 1.6인 ENIG 표면마감처리와 0~30W/mK(Watt per meter-Kelvin) 범위의 열전도율을 지녔다. 각 테스트 보드의 6개 PTH 위치는 주석 도금된 황동 핀이 있는 10개의 핀 수 헤더로 채워졌다.
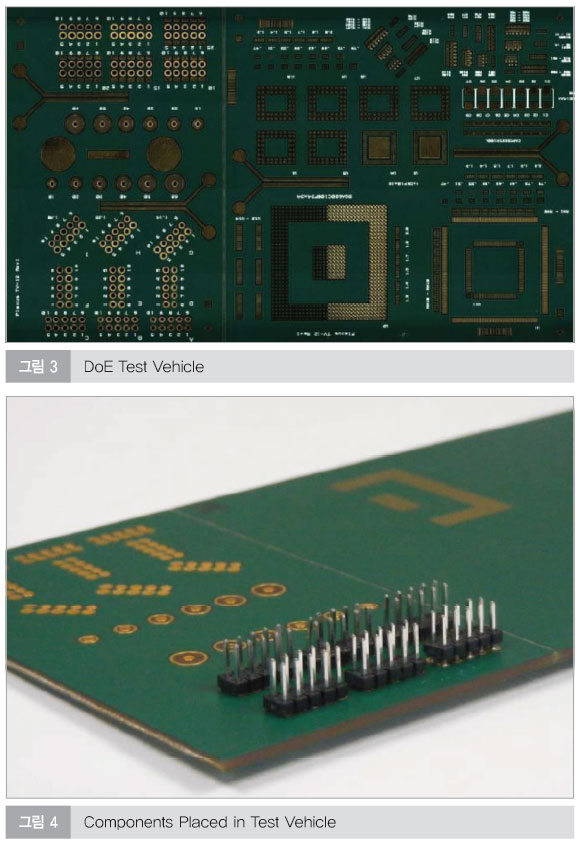
실험 설계
셀렉티브 솔더링 장비를 특성화 짓기 위해 4등분 부분 요인(a quarter factorial DoE) DoE가 개발되었다. 플럭스 유형, 플럭스 증착, 상면 보드 온도, 솔더 모듈에서 소요되는 시간, 솔더 체류 시간 및 국부적인 예열 시간 등 각 변수를 다르게 조정한 두 가지 설정을 조사했다. 플럭스 적용 패턴, 웨이브 높이, 솔더 웨이브 필오프 시간, 솔더링 방법, 솔더 포트 온도, 노즐 크기 및 솔더 합금은 고정으로 하였다. 각 실행에서는 테스트 보드에 다양한 변수를 조합하여 설정하였다. 16개의 솔더링 프로그램을 3회 반복하여 총 48회의 DoE를 실행하였다.
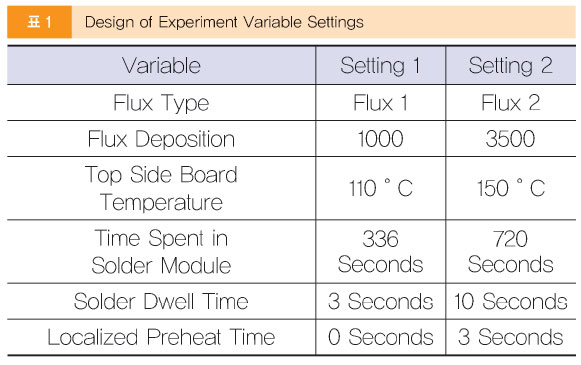
실험 실행 설계
DoE 실행에 사용된 기계에는 구동 간의 플럭스 변경 및 플럭스 라인 정화 없이도 원하는 양쪽의 플럭스를 연속적으로 뿌릴 수 있는 듀얼 플럭서 헤드가 장착되었다. 플럭스가 개별 플럭스 탱크에 로드되면 플럭스 라인이 충전되고 30분 동안 정화되었다.
플럭스 증착은 이전 실험에서 수립했던 설정을 참고하였다. 초기 실험에는 단위 시간당 플럭스 부피와 특정 설정에서의 스프레이 폭을 측정하는 것이 포함되었다. 이 데이터로부터 플럭서 이동 속도와 함께 주어진 기계 설정에 대한 스프레이 폭과 증착을 제공하는 표가 생성되었다. 각 플럭스는 고유한 플로우 특성과 플럭스-캐리어 비율을 가지므로 실험이 완료되었고 DoE에 사용된 두 플럭스에 대한 표가 작성되었다.
상면 보드의 예열 온도는 테스트 보드 상단에 부착된 알루미늄과 캡톤 테이프가 사용된 K-타입 열전대(K-type thermocouple)와 예열 사이클 동안 온도를 관찰하기 위한 데이터 기록기를 사용하여 정보를 얻었다. 데이터에 근거하여 원하는 온도가 충족될 때까지 예열 프로그램을 조정했다. 표피 효과 측정(skin-effect measurement)을 방지하고 열이 전체 두께에 스며드는지 확인하기 위해 테스트 보드는 하단 예열만 사용하여 가열되었다. 이 수행은 원하는 각 상단 보드의 원하는 온도에 맞춰 진행되었다.
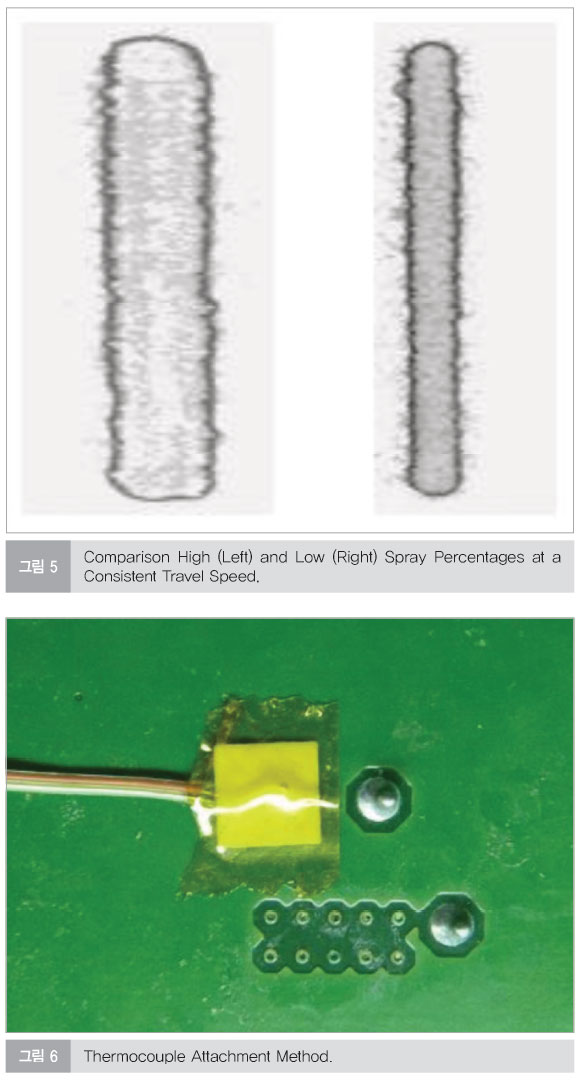
솔더링 프로세스 동안 PCB 온도를 유지하기 위해 상단 솔더 모듈 히터를 사용하여 솔더링 모듈에 대한 정확한 시간을 맞추는 솔더링 프로그램에 솔더링 지연(delay) 항목을 추가하였다. 지연 길이는 원하는 솔더 모듈 시간에서 총 솔더링 시간을 빼서 계산하였다. 솔더링 전 남아 있는 시간에 PCB 온도에 맞춰 히터를 유지하고 확장된 솔더링 프로그램을 시뮬레이션할 수 있었다.
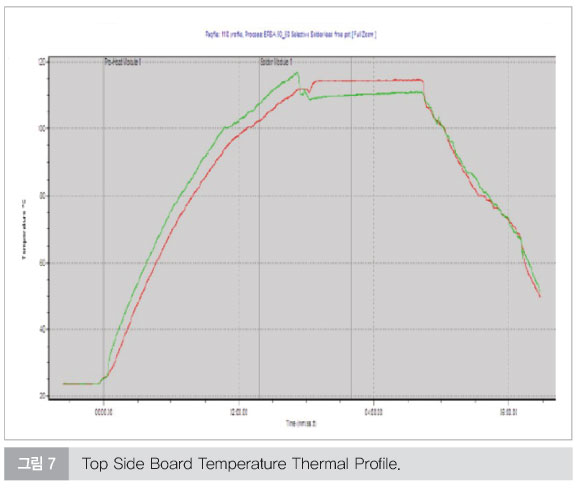
솔더 노즐을 납땜할 리드 바로 아래 위치로 이동하여 국부적인 예열을 완료했다. 안정적인 솔더 플로우로 노즐은 솔더의 메니스커스(meniscus)가 리드와 접촉하지 않고 리드의 바닥에 최대한 가깝게 들어 올려졌다. 습식 노즐에 드로스 형성을 방지하기 위해 사용된 질소에 의해 열이 전달된 이후 솔더 노즐이 일반 솔더링 위치로 올라갔다.
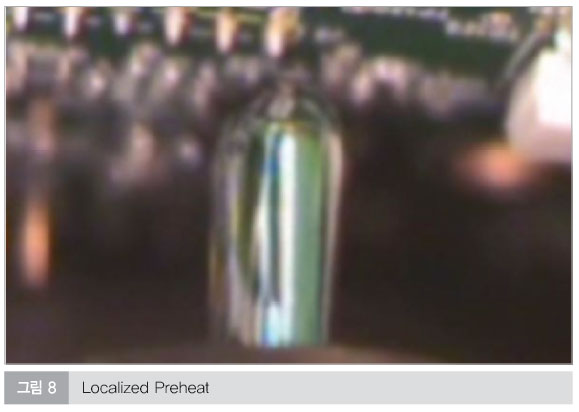
모든 솔더링은 포인트 납땜 방식으로 완료되었다. 포인트 납땜 시 노즐은 리드로부터 정확한 납땜 거리로 움직인다. 그런 다음 웨이브 높이는 납땜을 위해 올바른 높이로 켜진다. 일정 시간 동안 체류한 후 노즐 내부에서 웨이브 높이가 낮아지고 노즐은 납땜을 위해 다음 위치로 이동한다.
DoE의 48개 실행은 모두 24시간 이내에 무작위로 완료되었다. 각 프로그램 변경 후 모든 기계 온도가 정상화되는 데 최소 15분이 소요되었다. DoE 실행 단계에서 관찰되거나 기록된 이상 현상은 없었다.
DoE 모든 실행을 완료된 후 3D X-Ray로 테스트 보드를 검사하였다. PTH 위치당 총 5개의 슬라이스를 가했고, 25% 증분으로 X-ray를 촬영하고 수직 홀 충진상태를 검사하였다. 그런 다음 데이터를 수동으로 편집하고 분석을 위해 스프레드시트로 작성했다.
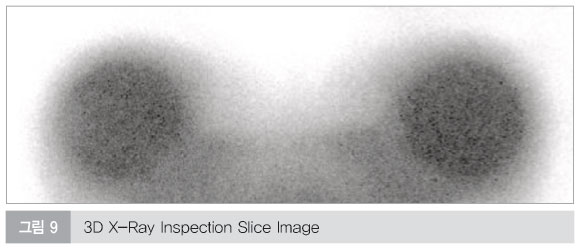
분석
DoE 데이터 분석에 사용된 주요 도구는 주효과도(Main Effects Plots), 표준화된 효과의 파레토 차트(Pareto Charts of Standardized Effects) 그리고 교호작용도(Interaction Plots)였다. 이들 차트는 각각의 홀-리드 비율과 열 연결성 조합에 관해서 작성되었지만, 본고에서는 수집된 높은 열 질량 위치 데이터에만 중점을 둘 것이다. 이렇게 하면 홀-리드 비율이 1.6 및 1.4이고 열 연결성이 30W/mk인 스루홀 위치로 데이터 설정이 제한된다.
홀-리드 1.6의 비율에서, 수직 홀 충진 평균은 약 40%~60% 범위였다. 플럭스 선정 결과에 따라 수직 홀 충진 부문에서 급격한 개선이 관찰되었다. 플럭스 2를 사용하면 플럭스 1에 비해 평균 홀 충진이 크게 향상되었다.
또한 플럭스 증착이 증가하면 눈에 띄는 평균 수직 홀 충진 증가가 나타났다. 국부적인 예열과 늘어난 솔더 체류 시간의 적용은 수직 홀 충진 부문에서 약간의 증가만을 보였다. 상면 보드 온도와 솔더 모듈 시간을 늘렸을 때는 수직 홀 충진에서 부정적인 영향이 관찰되었다.
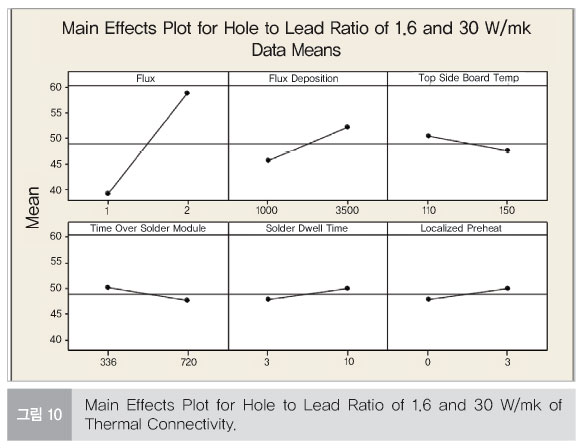
홀-리드 1.4 비율에서, 수직 홀 충진 평균은 약 65%~95% 범위였다. 홀-리드 1.6 비율에서와 마찬가지로 수직 홀 충진 부문에서 가장 눈에 띄는 개선은 플럭스 2를 사용한 플럭스 선정의 결과로, 가장 원하는 결과를 생성하는 것을 새삼 확인하였다. 플럭스 증착, 상면 보드 온도, 솔더 모듈 적용 시간 및 솔더 체류 시간에 대한 결과에서는 홀-리드 1.6 비율과 유사한 수치가 나왔다. 그러나 국부적인 예열은 평균 수직 홀 충진에 무시해도 되는 수준의 영향을 미치는 것으로 기록되었다.
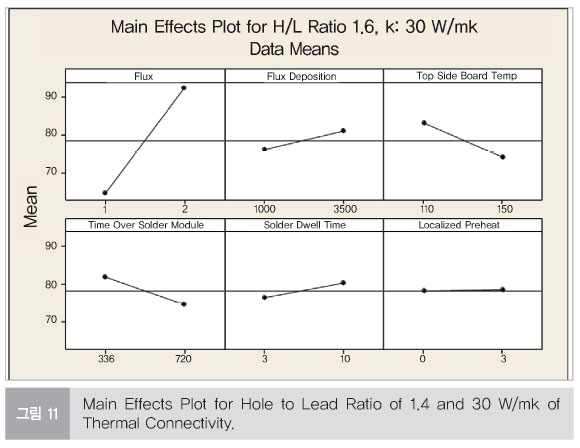
홀-리드 1.6 비율에서 여러 교호 작용이 관찰되었다. 상면 보드의 온도는 솔더 모듈의 시간과 국부적인 예열 사이의 교호 작용을 보여준다. 솔더 모듈에 가해전 시간과 솔더 체류 시간은 물론 솔더 체류 시간과 국부적인 예열도 상호 작용했다.
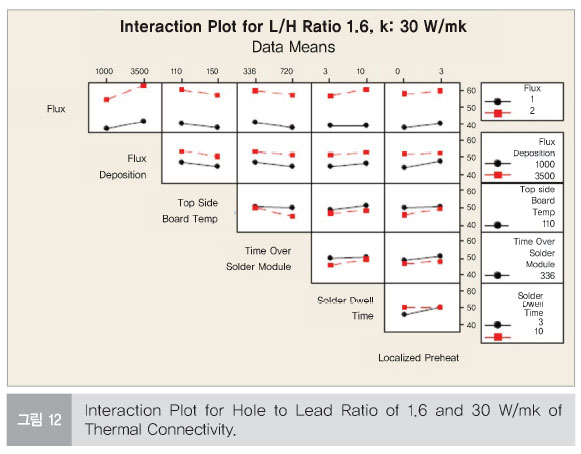
1.4의 홀-리드 비율에서 관찰된 대부분의 교호 작용은 플럭스 증착과 관련이 있었다. 플럭스 증착은 솔더 모듈의 시간, 솔더 체류 시간 및 국부적인 예열과 상호 작용하는 것으로 나타났다. 솔더 체류 시간과 국부적인 예열은 1.4의 홀-리드 비율에 대한 유일한 상호 작용을 보여주었다.
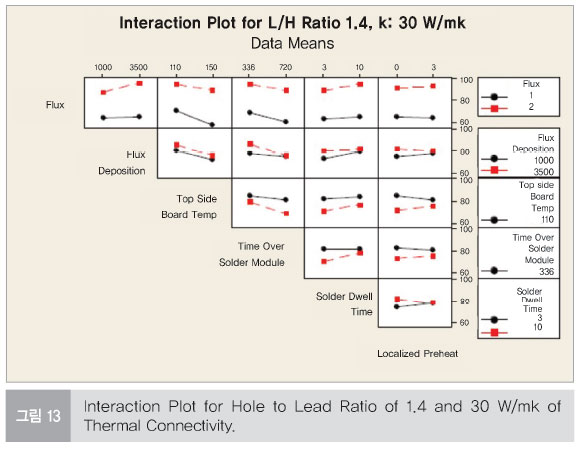
95% 신뢰도(알파 레벨 .05)에서 1.6의 홀-리드 비율에는 두 가지 요인이 있었으며 이는 수직 홀 충진의 통계적 유의성 효과(statistical significance effects)를 보여주었다. 수직 홀 충진에 있어서 가장 중요한 효과는 플럭스 선정이었는데, 이는 1.6의 홀-리드 비율 주효과도에서 관찰한 내용을 확인 시켜주었다. 통계적으로 중요한 또 다른 요인은 플럭스 증착이었는데, 이는 이전 관찰과도 일치했다. 통계적으로 유의미한 교호 작용은 나타나지 않았다.
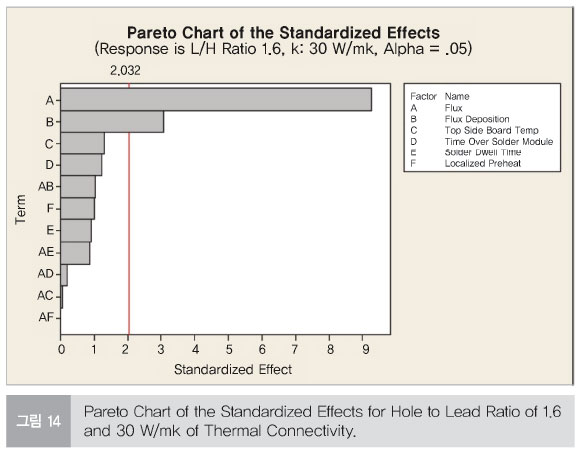
1.4의 홀-리드 비율에 대한 표준화 효과의 파레토 차트에서는 95% 신뢰도(알파 레벨 .05)로 계산되었으며 세 가지 요인이 통계적 유의성을 갖는 것으로 나타났다. 플럭스 선정은 다시 한번 수직 홀 충진에 영향을 미치는 가장 중요한 요소였다. 상면 보드 온도와 솔더 모듈 사용 시간도 통계적 유의성을 보여주었다. 이번에도 통계적으로 유의미한 상호작용은 나타나지 않았다.
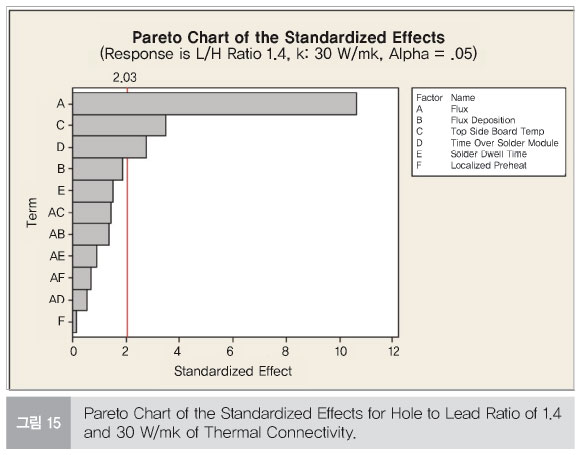
1.6개의 홀-리드 비율에 대한 최적화 모델이 100% 수직 홀 충진을 목표로 두고 생성되었지만 68.5%만 달성할 수 있었다. 목표가 달성되지 않았지만, PTH가 열 방열판 역할을 하는 열 또는 도체 층에 연결된 경우 IPC-A-610E에 따라 68.5%의 홀 충진이 잠재적으로 허용될 수 있다.[2] 최적화된 모델에는 높은 플럭스 증착을 보인 플럭스 2를 사용했다.
이 모델은 최소화된 상면 보드 온도 시간과 솔더 모듈 적용 시간을 보여준다. 이 결과는 이전 데이터와 일치했다. 또한 두 가지 모두 통계적으로 유의하지 않은 것으로 여겨졌지만, 솔더 체류 시간을 최대로 늘렸고, 국부적으로 예열하였다.
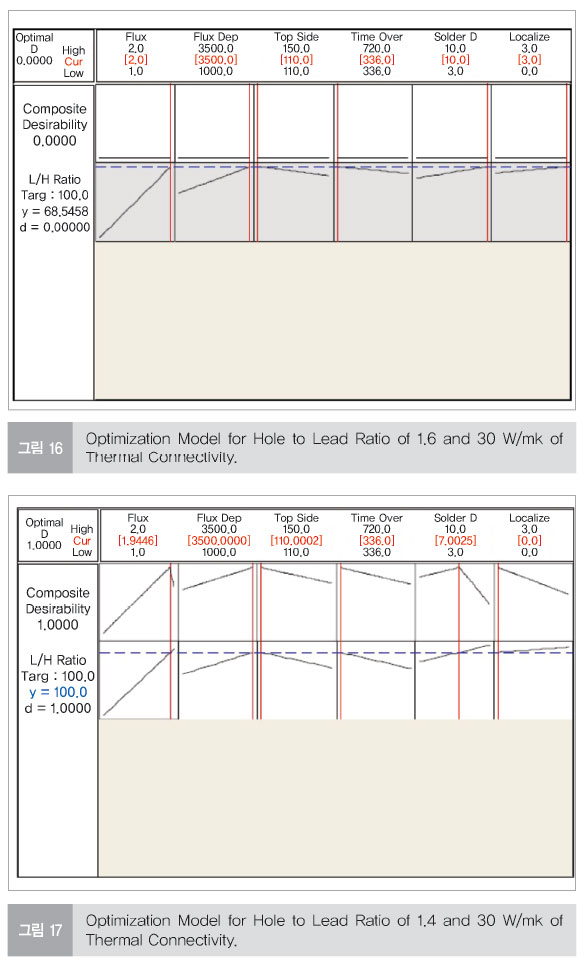
1.4의 홀-리드 비율에 대한 최적화 모델은 100% 수직 홀 충진을 목표로 두었고, 목표를 달성할 수 있었다. 이 모델은 1.6의 홀-리드 비율 모델과 일관된 결과를 보여주었다. 국부적인 예열이 사용되지 않은 동안 솔더 체류 시간은 두 가지 변수 설정 사이에서 최적화되었다. 최적화 모델에서는 또한 국부적인 예열과 최대화된 솔더 체류 시간이 수직 홀 충진에 사용된다면 100%를 초과할 수 있음을 나타냈다.
결론
열적으로 까다로운 어셈블리에서 월등한 수직 홀 충진을 이뤄내기 위해 고려해야 할 많은 요소가 있다는 데이터를 도출하였다. 이러한 요소 중 가장 눈에 띄는 것은 플럭스 선택이다. 최적화 모델링은 플럭스 증착의 증가가 수직 홀 충진을 개선할 가능성도 있음을 보여주었다.
주효과도 분석을 통해 상면 보드 온도 증가와 솔더 모듈 적용 시간의 부정적인 영향을 확인할 수 있었다. 따라서 수직 홀 충진력을 높이려면 상면 보드 온도와 솔더 모듈 시간을 최소화해야 한다. 최적화 모델링에서 결과를 찾을 수 있다.
표준화된 효과에 관한 파레토 차트를 통해 늘어난 솔더 체류 시간과 국부적인 예열의 효과는 통계적으로 유의미하지 않은 것으로 확인했다. 그러나 최적화 모델에서는 이러한 요소가 여전히 최상의 수직 홀 충진을 달성하는 데 중요한 역할을 한다는 것을 보여주었다. 이로 인해 늘어난 체류 시간과 국부적인 예열은 고열량 어셈블리 솔더링에 있어서 실행 가능한 옵션으로 여겨져야 한다.
REFERENCES
[1] Niemeier J. and Seliger, G., “Simulation of the soldering process” annals of the CIRP, 47/1:27-30, (1998)
[2] IPC “IPC A-610E, Acceptability of Electronic Assemblies” (2010)
|