일반적인 오류들 재검토
확실한 제어와 지속적인 관리가 중요
와이어 본드 및 플립칩 범프 인터커넥트는 본드 파라미터, 리플로우 공정, 몰드 재료 세트, 서브스트레이트 패드 및 솔더 마스크가 최적화된 경우에만 신뢰성 있는 형태의 인터커넥트라고 할 수 있다. 이러한 패키지의 성공적인 어셈블리와 신뢰성은 오류 모드, 명확하고 간결한 문서화, 협력업체와 함께한 교육 및 팀워크에 대한 사려 깊은 이해를 통해 달성될 수 있다.
생산 현장의 확실한 통제는 결함 발생을 최소화하고 피할 수 있는 솔루션 중 하나이기 때문에 자주 검토해야 한다. 오류 모드를 정확히 이해하고 정정할 때, FMEA(Failure mode effects analysis) 및 제어 계획에서는 변경 사항과 ‘교훈’을 반영하여 업데이트되어야 한다. 수율 목표 및 수율 개선 계획은 생산 시작 전에 규정되어야 하며 지속적으로 검토되어야 한다. 부품 수에 따른 상위 3개의 수율 감소원(yield detractors)을 활용하는 수율 데이터 검토는 DPPM 감소 노력에 도움이 된다.
요약
휴대용 및 무선 제품의 시장 성장은 패키지의 소형화를 주도하고 있으며, 이에 따라 폼팩터가 얇은 다양한 유형의 패키지와 비용 효율적인 어셈블리 프로세스로 진화되고 있다. 종래의 구리 리드프레임을 사용하는 와이어 본딩 패키지는 오랫동안 업계에서 사용되어 왔었다. 그러나 가전제품에서의 플립칩 인터커넥트에 대한 요구가 더욱 강해지고 있다. 플립칩 패키지는 와이어 본딩 패키지와 비교하여 짧아진 시그널, 줄어든 인덕턴스, 향상된 기능 구현이 가능해 최첨단 디자인 설계에 유리하다. 플립칩 패키지는 와이어 본드 대신하는 상호 연결부로서 솔더 범프를 가지며, 일반적으로 금속 리드프레임 대신 인터포저 또는 유기 기판을 사용한다.
대량 SMT 어셈블리에 이러한 패키지를 통합시키기 위해서는 패키지 레벨의 우수한 어셈블리 프로세스 제어가 요구되며, 후속 어셈블리 작업에서 불량 발생을 최소화하기 위한 오류 모드를 확실하게 이해하고 있어야 한다. 이 문제는 무연 리플로우로의 전환에 따라 더 확대되고 있다. 높은 피크 온도의 리플로우 프로세스는 패키지와 PWB 간의 더 많은 열적 및 CTE 불일치를 초래한다.
본고에서는 패키지 어셈블리에서 볼 수 있는 전형적인 결함 및 오류 모드에 대한 일반적인 개요를 확인하고, 패키지 어셈블리 동안 발생하는 새로운 오류 모드를 이해하도록 재검토하였다. 얇은 폼 팩터 패키지 공정으로 전환한 생산라인에서 얻은 근본 원인평가와 교훈을 공유하고자 한다.
서문
와이어본드 및 플립칩 인터커넥터는 줄어든 회로 구조와 늘어난 와이어 밀도로 인해 소비재 가전기기에서의 요구를 충족시킨다. 대량 SMT 어셈블리 생산라인에서 이들 패키지에 대한 신뢰성을 구축하기 위해서는 다이어테치 에폭시, 오버 몰드/언더필 재료 그리고 주의 깊게 제어된 리플로우 프로파일과 같이 어셈블리 재료에서부터 프로세스까지 신중하게 선정해야 한다. 무연 리플로우의 좁아진 프로세스 윈도우에서 우수한 수율과 신뢰성을 확보하려면 부품 및 공정에 대한 보다 엄격한 보관과 취급 컨트롤이 필요하다.
본고에서는 얇은 폼 팩터 패키지의 제조에서 볼 수 있는 전형적인 결함 및 오류 모드, 근본 원인 이해, 시정 조치를 요약할 것이고, 대량 생산 협력업체 작업에서 얻은 교훈들을 정리할 것이다.
어셈블리 프로세스 플로우 개요
와이어 본드 및 플립칩 어셈블리는 고유한 프로세스 플로우와 최적의 생산량을 제공하도록 설정된 재료들을 가지고 있다. 와이어 본드 어셈블리 작업은 프론트-엔드-라인(FOL)과 백-엔드-라인(BOL)으로 구분된다. FOL에는 다이 부착, 와이어 본드 및 3번째 광학 검사까지이고, EOL은 그림 1에서 보는 바와 같이, 몰드, 경화, 레이저 마크, 플레이트 및 싱귤레이션 프로세스를 포함한다.
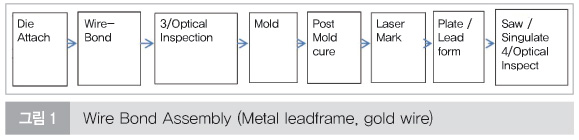
플립칩 어셈블리 작업은 프론트-엔드-라인(FOL)과 백-엔드-라인(BOL)으로 구분된다. FOL에는 다이 실장, 리플로우 및 3차 광학 검사가 포함되고, EOL에는 그림 2와 같은 몰드, 경화, 레이저 마크 및 싱귤레이션 프로세스가 포함된다.
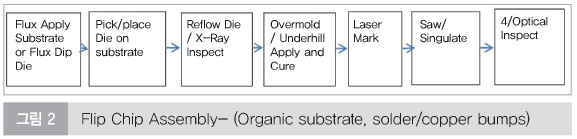
어셈블리가 끝난 후에, 패키지는 Test, Tape-and-Reel을 거쳐 출하를 위해 포장된다.
결함 및 오류 모드 평가
패키지 제조 프로세스에는 최종 제품을 제조하는데 사용되는 다양한 재료와 프로세스가 있다. 재료와 프로세스가 적절히 제어되지 않으면 많은 결함이 발생할 수 있다. 초기 엔지니어링 단계에서 사용된 주요 결함 예방 툴 중 하나는 설계 및 프로세스의 위험군을 예측하고 결함을 최소화하도록 제어 장치를 배치하는 DFMEA(설계 오류 모드 및 효과 분석)과 PFMEA(프로세스 오류 모드 및 효과 분석)이다.
얇은 폼팩터 패키지로의 이동하기 위해서는 취급 제어, 수분 내성 분류(moisture sensitivity classifications), 재료 유효기간 및 프로세스 윈도우 강화에 보다 중점을 두어야 한다.
와이어 본드 패키지
와이어 본드 패키지는 leaded 및 leadless(QFN) 버전으로 제공된다. 그림 3과 그림 4에서 와이어 본드 패키지를 보여주고 있다.
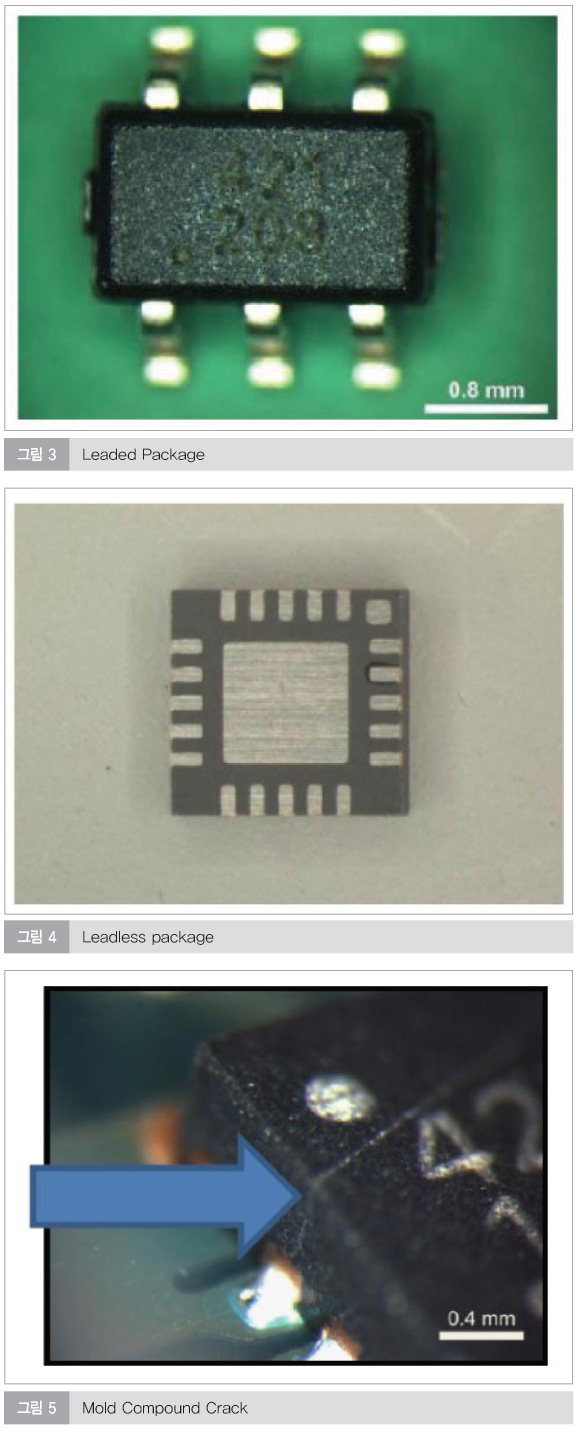
두 패키지 모두 와이어 본딩된 구리 리드프레임을 사용하여 제작된다. 외부 터미네이션 도금은 RoHS 요구 사항을 충족시키기 위해 100% 무광택 주석 또는 NiPdAu를 사용하였다. 전형적인 오류 모드로는 박리, 도금 크랙, 버(burr), 오염, 와이어 본드 패드의 부식 그리고 몰드 화합물의 크랙이 나타났다.
얇은 폼팩터 패키지로의 이동은 취급 컨트롤, 재료 유효기간 그리고 보다 엄격한 프로세스 윈도우 수립에 더 중점을 두어야 한다. 그림 5에서 볼 수 있듯이 1mm 두께 패키지에서 0.7mm 및 0.5mm 두께 패키지로 이동함에 따라 몰드 화합물 크랙의 높은 발생률이 나타날 수 있다.
Depaneling 및 싱귤레이션을 위한 자동화 설비로 전환하고 매뉴얼 취급을 줄음으로써 패키지 파손의 확률을 낮출 수 있었다. 쏘잉(sawing)과 블레이드 마모에 대한 새로운 프로세스 윈도우를 정의하기 위해 검사 및 취급에 대한 트레이닝이 뒤따르도록 설계된 실험을 수행했다.
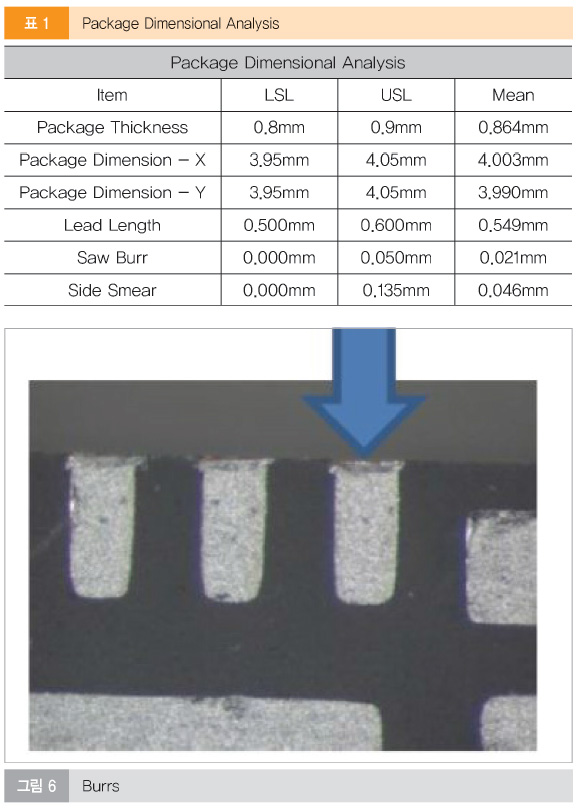
패키지 상의 버(burr), 스크래치, 툴링 자국은 솔더 젖음성 문제로 인해 어셈블리 수율에 영향을 줄 수 있다. 버(Burr)는 표 1과 그림 6에서와 같이 0.05mm 이내에서 측정하고 제어해야 한다.
Leaded 패키지의 경우, 폼의 ‘무릎’ 부분에서 리드가 형성되는 동안에 도금 크랙이 발생할 수 있다.
더 미세해진 SMT의 피치와 좁은 리드 폭으로 기술이 진화함에 따라, 보다 엄격한 포밍 프로세스 제어가 필요해지고 있다. 크랙, 불충분 또는 미싱(missing) 도금은 솔더 성능과 신뢰성 문제를 유발할 수 있다. 그림 7과 그림 8은 NiPdAu 도금의 lead를 보여주고 있다.
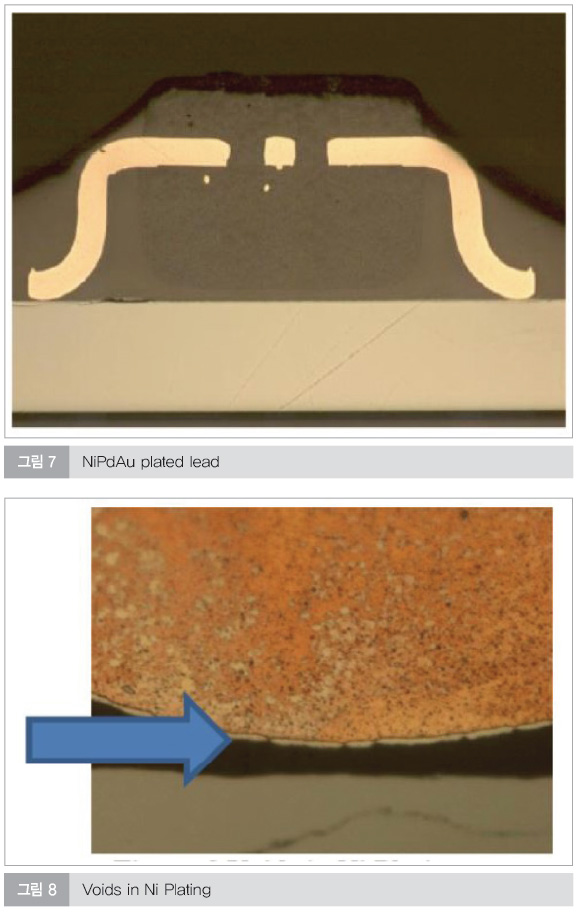
와이어 본딩 프로세스는 패키지 어셈블리 수율을 결정하는 핵심 공정이다. 와이어 본딩을 위한 적절한 최적화와 프로세스 윈도우 개선은 패드 상의 비-점착성, 리프트(lift) 혹은 와이어 본드 파손을 최소화하는데 필수적이다. 적절한 본드 패드 청결은 또한 신뢰성 있는 와이어 본드에 기여한다. 그림 9에서는 끊어진 와이어 본드를 보여주고 있으며, 그림 10에서는 리프트된 와이어 본드를 나타내고 있다.
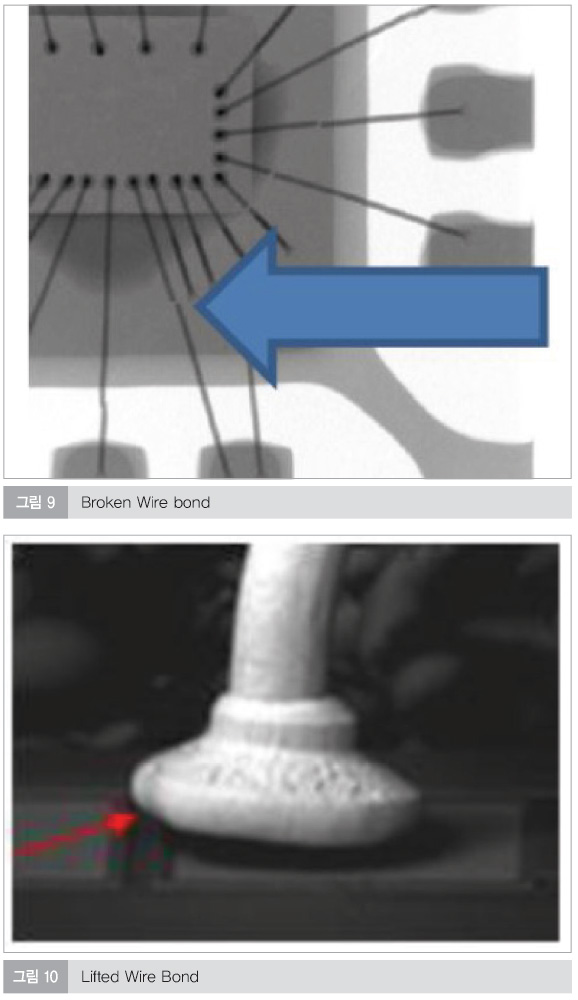
플립칩 패키지
플립칩 패키지 어셈블리 수율은 적절한 범프 정렬, 리플로우 및 몰딩 프로세스에 크게 의존한다. 라미네이트 기판 재료, 표면 처리 그리고 CTE는 패키지의 신뢰성에 중요한 역할을 담당한다. 그림 11 및 그림 12에서 보는 바와 같이, 성공적인 패키지의 어셈블리를 위해서는 패키지-다이 인터페이스와 범프-서브스트레이트 인터페이스에서 적절한 범프 정렬과 금속간 형성이 필요하다.
라미네이트 패드 형상 및 솔더 마스크 윈도우 최적화는 적당한 조인트 형성에 중요하다. 라미네이트의 유리전이온도와 자체 CTE(열팽창 계수) 그리고 휨 특성은 범프 신뢰성에 영향을 줄 수 있다. 또한, 리플로우 프로파일은 서브스트레이트의 박리를 야기하지 않고 적절한 솔더 리플로우 작업이 이뤄지도록 최적화되어야 한다.
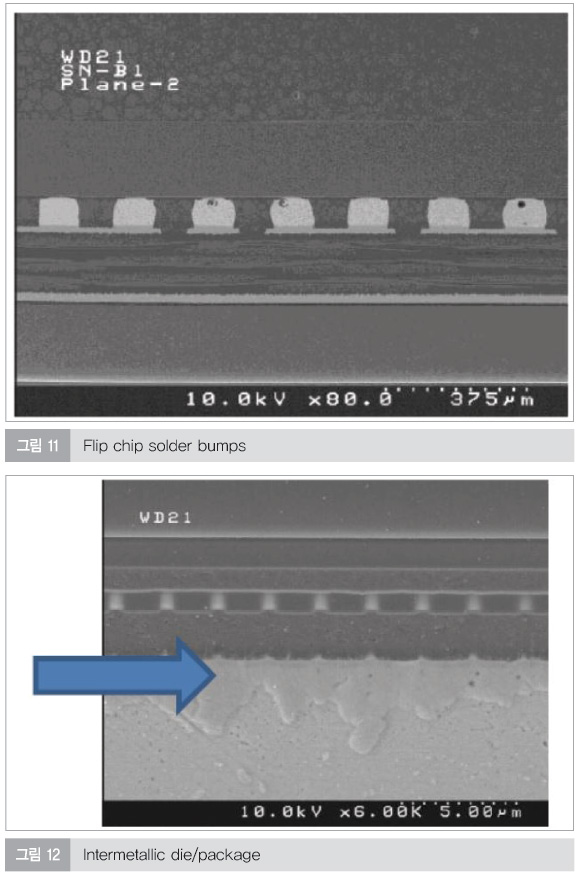
구리 스터드는 미세 피치 플립칩 패키지에 사용되는 범프 인터커넥트의 또 다른 형태이다.
범프 정렬에 적합한 패드는 구리 스터드에 있어서 더욱 중요하다. 솔더 범프가 지닌 셀프-센터링 성능을 가지고 있지 않기 때문이다. 서브스트레이트와 다이 간의 CTE 불일치는 구리 범프 신뢰성에 상당한 영향을 줄 수 있다. 그림 13에서는 구리 인터커넥트를 활용한 수용 가능한 조인트를 보여주고 있으며, 그림 14에서는 구리 범프 인터커넥트 내의 크랙을 보여주고 있다.
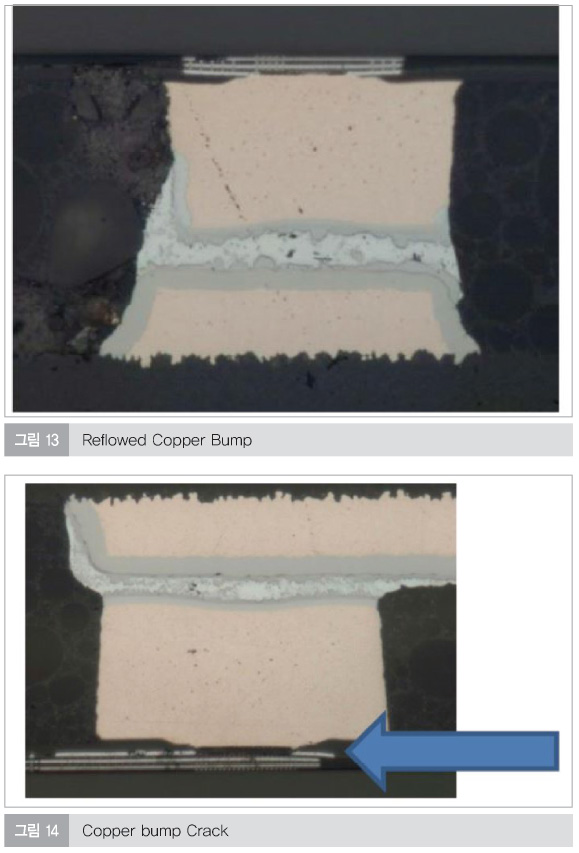
솔더 조인트 프로파일, 정렬, 보이드의 유무를 이해하고 솔더 조인트의 입자 구조를 측정하기 위해 리플로우 후에 X-sectioning 작업을 수행하였다. 범프에서 서브스트레이트 인터페이스 내부에 갇혀 있는 보이드는 어셈블리 문제를 야기할 수 있다. 일반적으로 허용되는 보이드의 기준은 범프 직경의 30% 미만이다.
저 보이드 솔더 페이스트로 교체하면 보이드 문제를 최소화하는데 도움이 될 수 있다. 솔더 페이스트로 범프를 대체하는 방법은 보이드 문제가 적게 발생하는 솔더 볼 드롭 프로세스(solder ball drop process)을 적용할 수 있다.
X-단면 분석은 범프 주변의 적절한 몰드 컴파운드의 분포와 보이드 최소화를 보장하기 위해 패키지 몰딩 프로세스를 평가하는데도 도움이 된다. 적은 핀 수의 패키지는 일반적으로 전체 몰딩되어 패키지 레벨의 신뢰성 테스트를 견딜 수 있다. 핀 수가 많은 패키지는 리플로우 이후 언더필과 경화가 필요하다. 경화 공정 도중 언더필에 솔더 압출(solder extrusion)이 존재하지 않도록 하기 위해 언더필된 패키지의 주의 깊은 평가가 필요하다. X-단면 및 SEM/EDX 분석에서 볼 수 있는 다른 오류 모드는 솔더 범프로부터의 UBM(under bump metallurgy) 분리, 패시베이션 크랙(passivation cracking), 범프 부식, 패드 분리 등이 있다.
근본 원인 분석
이전에 논의된 플립칩 및 와이어 본드 패키지에서의 다양한 결함은 생산라인 기록, 제어, 교육 및 문서화라는 철저한 후속조치가 필요하다고 말하고 있다. 외관 및 기능 결함의 전형적인 원인은 최적화되지 않은 공정, 취급 상 피해, ESD 제어, 작업자 교체, 교육 부재, 재료 관리 등이다. 결함 중 일부는 품질검사 프로세스에서 노출되지 않으며 나중에 설비 및 프로세스로 생산라인을 완벽하게 구축하여 가동할 때 노출되기도 한다. 이러한 결함을 최소화하기 위해 품질 승인 이전에 세부적인 패키지 구조 분석이 실시되어야만 한다. 분석들 통해 결함을 격리하고 수정 조치를 취하여 생산 가동 전에 프로세스 윈도우 최적화를 수립할 수 있다.
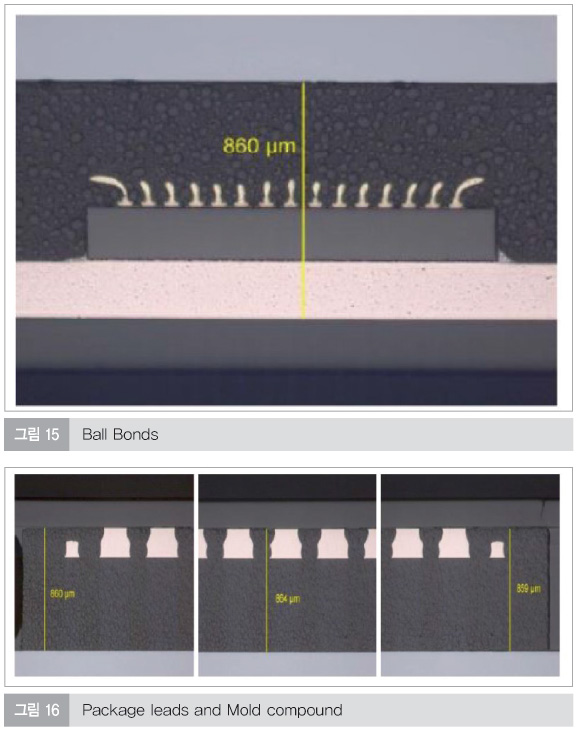
와이어 본딩 패키지의 경우, 다이 장착, 볼 본드, 웨지 본드 및 패키지 몰딩은 X-section을 사용하여 평가된다. 그림 15는 패키지 와이어 본드를, 그림 16은 패키지 몰드 화합물을 보여주고 있다.
와이어 본드의 신뢰성은 어셈블리 프로세스에서의 패키지 작업과 후속 고객 애플리케이션의 성공에 중요한 요소이다.
적절한 금속간 형성과 >25gms의 전단 값 그리고 최소한의 보이드가 와이어본드 이후에 예상된다. 그림 17은 금-알루미늄 와이어 본드의 금속간 형성을 보여주고 있다. 그림 18은 lead에 생성된 웨지 본드를 보여주고 있다. 리프트된 웨지 본드는 본드 파라미터 레시피 최적화와 청결한 본드 표면 유지를 통해 예방할 수 있다.
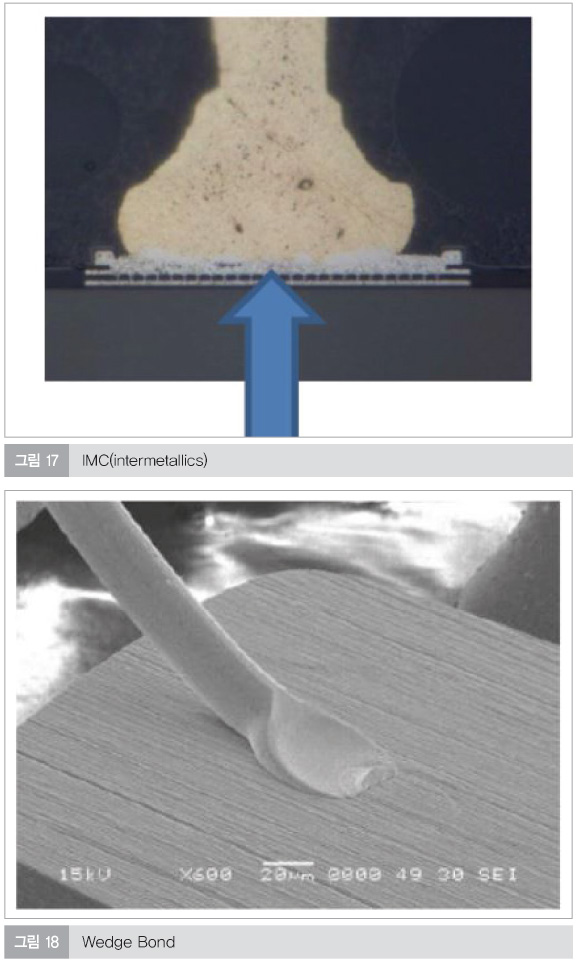
X- 단면 분석은 또한 플립칩 패키지에 있어서 다이 두께, 라미네이트, 비아, 범프 높이, 보이드, 금속간 화합물 등의 패키지를 이해하기 위해 수행되었다. 그림 19는 플립칩 패키지의 X-섹션을 보여주고 있다.
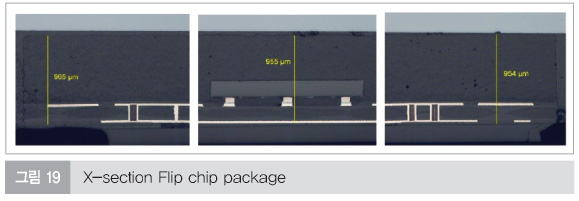
생산 현장의 확실한 통제는 결함 발생을 최소화하고 피할 수 있는 솔루션 중 하나이기 때문에 자주 검토해야 한다. 오류 모드를 정확히 이해하고 정정할 때, FMEA(Failure mode effects analysis) 및 제어 계획에서는 변경 사항과 ‘교훈’을 반영하여 업데이트되어야 한다. 수율 목표 및 수율 개선 계획은 생산 시작 전에 규정되어야 하며 지속적으로 검토되어야 한다. 부품 수에 따른 상위 3개의 수율 감소원(yield detractors)을 활용하는 수율 데이터 검토는 DPPM 감소 노력에 도움이 된다. 제조라인 검사, 교육 검토 및 재교육은 지속적인 개선에 도움이 되는 하나의 수단이기도 하다. 각 주요 프로세스에 대한 Cp/Cpk와 출시 이후 10~15개의 생산 로트를 모니터링하는 것은 지속적인 프로세스 개선과 최적화에 집중할 수 있는 효과적인 솔루션이 될 수 있다.
결론
와이어 본드 및 플립칩 범프 인터커넥트는 본드 파라미터, 리플로우 공정, 몰드 재료 세트, 서브스트레이트 패드 및 솔더 마스크가 최적화된 경우에만 신뢰성 있는 형태의 인터커넥트라고 할 수 있다. 이러한 패키지의 성공적인 어셈블리와 신뢰성은 오류 모드, 명확하고 간결한 문서화, 협력업체와 함께한 교육 및 팀워크에 대한 사려 깊은 이해를 통해 달성될 수 있다.